All about tongue-and-groove moisture-resistant slabs
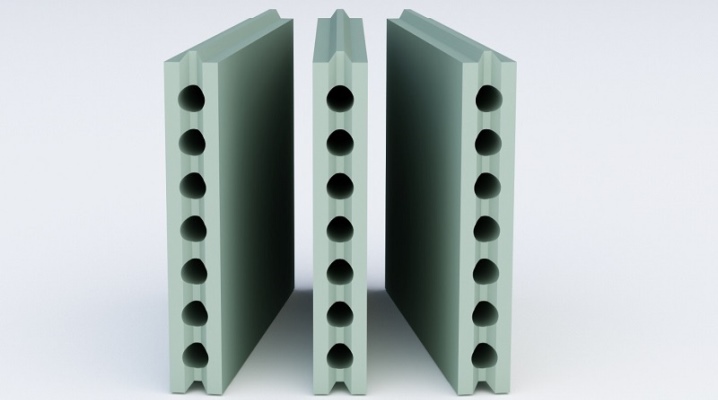
When making redevelopment in an apartment or house, you have to install additional partitions. And here a huge problem arises with the choice of material that meets the technical requirements of the new walls. It must have a bearing capacity, be strong, reliable and withstand excessive loads.
Another important selection criterion is ease of installation. Quite often, home repairs are done on their own, so it is important for inexperienced builders that the material is malleable and easy to install. The tongue-and-groove plates meet all the criteria presented.
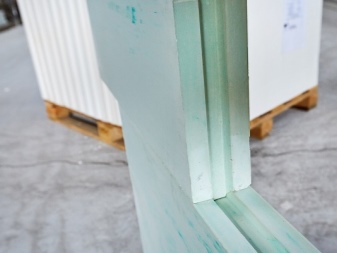
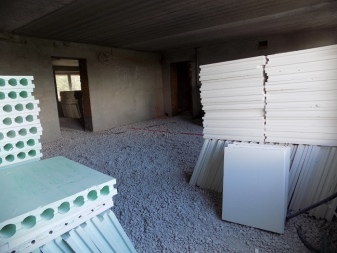
What it is?
Tongue slabs or, as they are called abbreviatedly, GWP is a wall material used in the installation of load-bearing partitions indoors. A distinctive feature of these plates is the presence of protruding and falling parts, which serve as reliable elements for fixing the partition plates.
In construction, special attention is paid to tongue-and-groove slabs, since this material has a number of significant advantages:
- quick installation;
- the minimum amount of consumable glue for fixing the plates;
- the surface of the GWP does not require the application of plaster;
- environmental friendliness;
- fire resistance;
- high level of thermal insulation;
- excellent sound insulation.
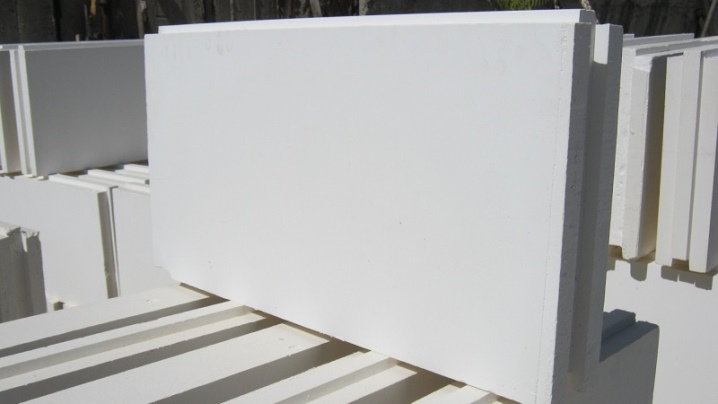
But despite the advantages presented, the GWP material has some disadvantages:
- a high level of hygroscopicity limits the use of GWP in rooms with high humidity;
- partitions installed by GWP have restrictions on the weight of the attached equipment;
- with building settlement and even minimal seismicity, there is a likelihood of cracks and deformation of blocks.
However, modern manufacturers, realizing that partitions are necessary in rooms with a high level of humidity, have developed waterproof tongue-and-groove blocks.
Their moisture-resistant characteristics guarantee the strength and reliability of the partition structure in baths and saunas.
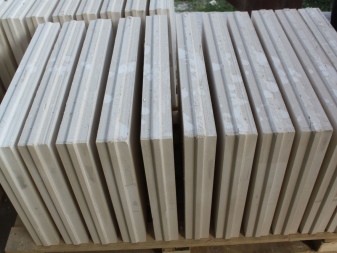
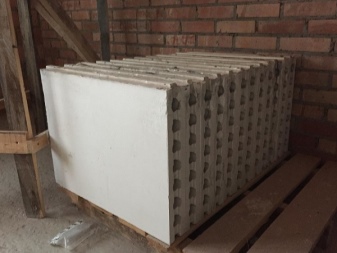
Types and sizes
According to the interstate requirements of the standard, each tongue-and-groove plate must have clear dimensions:
- 667 × 500 mm;
- 660x500 mm;
- 900 × 300 mm.
The thickness of the blocks ranges from 80 to 100 mm. The most common dimensions are 667x500x80 mm. As for the density, this indicator depends entirely on the materials used in the manufacture. Thus, it turns out that the density level for gypsum blocks is 1050-1300 kg / m³, and for silicate blocks the minimum value is 1870 kg / m³.
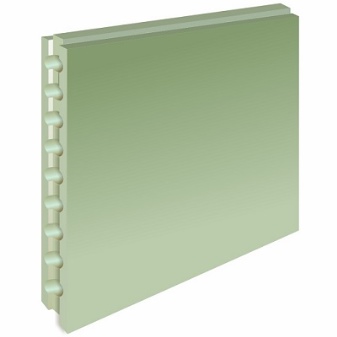
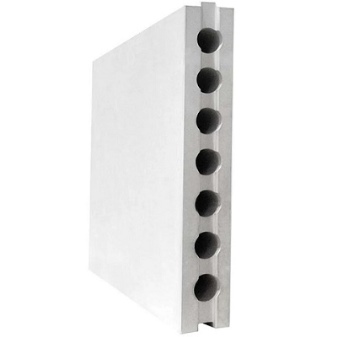
With the stated requirements of the state standard, tongue-and-groove plates differ in several parameters. And first of all it is the composition.
- Gypsum boards are molded. They contain gypsum and a plasticizer. According to the technical specifications, the level of thermal insulation of gypsum blocks is very high. An 8 cm slab is equivalent to a wall covered with a 4 cm thick layer of concrete.
- Silicate slabs are made from quartz sand, lime and water. Their technical characteristics are similar in almost all respects to gypsum blocks.
To date, the blocks manufactured by PGP are divided according to the type of fasteners. The groove / tongue can be rectangular or trapezoidal. There is no difference between the strength of the mountings. The question of the choice assumes the convenience of installation for the master himself.
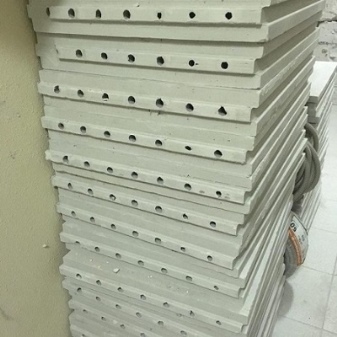
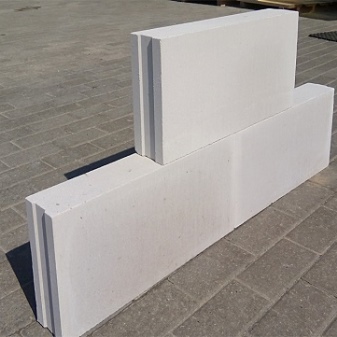
On the construction market, you can find several types of tongue-and-groove slabs.
- Standard. They are used in rooms with low humidity levels. But at the same time, the height of the walls of the room should not be more than 4.2 m.
- Hydrophobized. A more understandable name is moisture resistant. These boards contain special water-repellent additives. You can determine that these are hydrophobized slabs by their greenish tint.
- Shungite. These plates are supposed to be used in rooms where a lot of devices with electromagnetic radiation are installed. These slabs contain coal, which is why they have a black color.
Also, tongue-and-groove blocks are produced in the form of hollow and solid structures. Hollow core slabs are used to create partitions in a home environment. Solid blocks - for wall mounting in industrial and public buildings.
By the way, it is possible to create double structures from hollow and solid slabs. In the distance between them, it will be possible to hide insulation, electrical wiring and other communications.
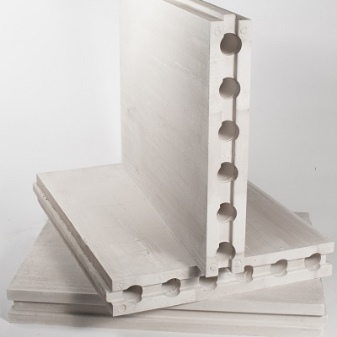
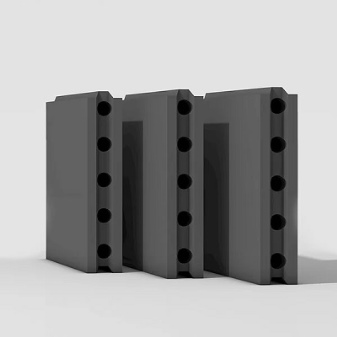
Manufacturers and their products
Today, tongue-and-groove gypsum blocks are the most demanded material. It is used not only for the creation and reconstruction of public buildings, but also when carrying out house repairs with the idea of redevelopment. In the construction market, you can find tongue-and-groove plates of both domestic and foreign manufacturers.
For example, Knauf. It produces a GWP material called Knauf-Plaster. This world-famous manufacturer is ready to offer its customers standard and hydrophobized solid blocks.
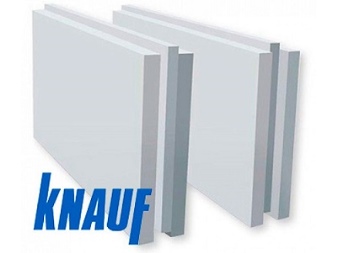
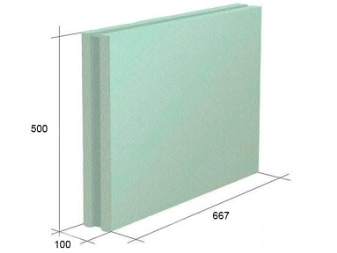
A fairly large and well-known company "Volma" is engaged in the production of solid and hollow GWP blockswith normal and moisture resistant characteristics. You can meet its products on the Russian market and in the countries of the customs union. Many builders give their preference to Volma slabs, as they are distinguished by their increased strength and ease of installation.
The Peshelansky Gypsum Plant is widely known in the construction industry. He is engaged in the manufacture of GWP blocks from gypsum mined in his own mine. The finished products of the plant are supplied to almost all regions of the Russian Federation, as well as to the markets of neighboring countries. "Peshelansky Gypsum Plant" offers its customers not only ordinary and hydrophobic boards - the manufacturer produces shungite tongue-and-groove panels that absorb electromagnetic radiation.

Use and installation
Today, solid and hollow GWP blocks are widely used in the construction industry. Their distinguishing feature lies in the ease of installation. Of course, it is convenient to invite a bricklayer specialist who will raise the partitions in a short period of time, or you can do the installation of the slabs yourself. The main thing is to know the general requirements for working with GWP plates:
- installation of plates must be carried out before the start of finishing work;
- the room temperature should be more than 5 degrees Celsius;
- Before placing the slabs, they must be primed.
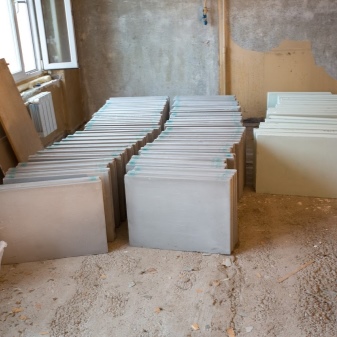
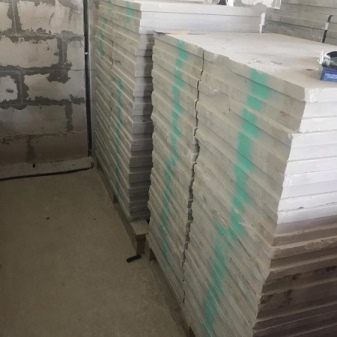
To start the installation process, you need to prepare some tools and materials:
- GWP plates;
- glue mixture;
- primer;
- brackets for fixing the partition to the ceiling and floor;
- self-tapping screws;
- putty knife;
- level;
- container for mixing the adhesive;
- hacksaw;
- drill;
- screwdriver.
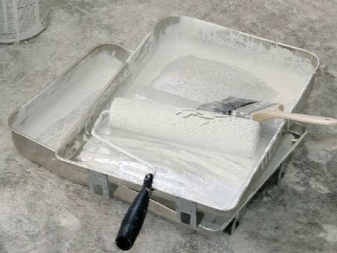
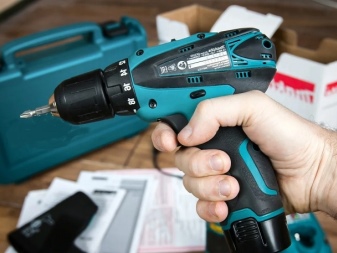
Now you can proceed to the preparatory step for installing the partition. First of all, the marking of the dividing wall is made on the floor. To do this, the floor covering must be cleaned of dust, treated with a primer. The boundaries of the septum are applied with a pencil or marker. A strong thread must be pulled to a height of 30 cm from the side, which will indicate the installation boundaries of the first row of plates.
Next, the solution is prepared. The adhesive mixture is presented in dry form.Accordingly, it must be diluted with water in the proportion indicated on the package. A gypsum-based mixture sets much faster. Therefore, it is necessary to knead it in small quantities. A small amount of glue is applied to the base of the slab and the adjacent part of the wall. The slab is installed on the mortar with the ridge upwards and is firmly pressed against the floor covering and the wall. The horizontality is checked by the level. An adhesive is applied to the end side of the block, designed to fix the next block.
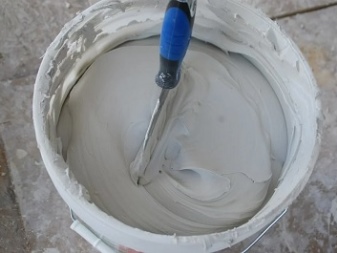
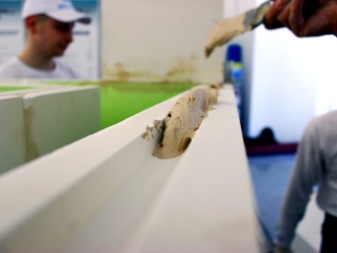
After installing the first row of plates, you can proceed to the second. The installation process in this case is slightly similar to brickwork, where the dressing of the joints is used. Accordingly, the second row is made with an offset of the joint of the masonry slabs. To strengthen the partition, it is necessary to fix metal corners or brackets at the joints of the slabs with the wall and floor. The fasteners are mounted using self-tapping screws.
The entire partition is laid out in a similar way. It is necessary to know the intricacies of sealing the gaps between the assembled wall and the ceiling. It is clear that there is a gap between them.
The easiest way to fill the gap is to use polyurethane foam or starter filler. Knowing the rules of work, you can proceed to the independent installation of GWP plates.
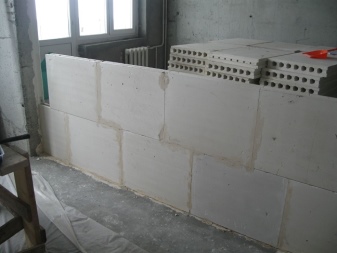
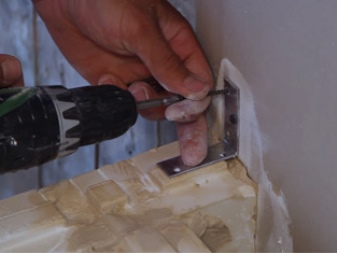
In the next video, you will see the installation of walls and partitions from tongue-and-groove slabs with your own hands.
The comment was sent successfully.