Grinding wheels for grinders: types and tips for use

The grinder is a popular power tool and is widely used in repair, construction and finishing work. Thanks to the ability to install a variety of attachments, the tool acts as an irreplaceable assistant when sanding wood, stone, metal and concrete surfaces.

Appointment
Sanding hard substrates would not be possible without the use of special interchangeable discs available on the market in a wide variety of sizes, shapes and textures. They are used to polish workpieces in the furniture industry, restore antiques, grind the walls of wooden log cabins, rough logs and remove paint and varnish residues from any surfaces.
In addition, grinding wheels are widely used in the repair of wooden floors and natural parquet., as well as in the manufacture of lining, floorboards, window frames, doors and boxes for them. Discs are often used for roughing, cleaning and polishing various parts, removing rust stains from metal and concrete surfaces, as well as for precise fitting of tongue-and-groove joints, and for other elements requiring a tight fit.
In addition to grinders, grinding wheels are used in combination with electric drills and orbital eccentric grinders.
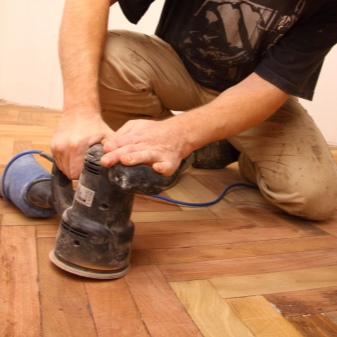
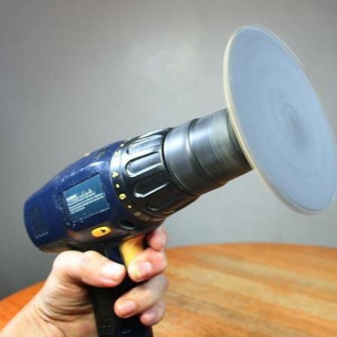
Varieties
The classification of grinding wheels occurs according to several criteria, the determining of which is the specialization of the models. On this basis, there are three categories of products, such as:
- universal models capable of processing any surface;
- discs designed for grinding and polishing wood products;
- circles for working on concrete, natural stone and metal.



The first type includes 4 types of ground wheels, which can be equally effectively used on any surfaces.
- Rough circle is intended for removing layers of old paint or varnish from all substrates. It is a disc covered with metal bristles. For the manufacture of bristles, a strong elastic wire is used that is resistant to deformation and is able to quickly and effectively break and remove the old coating. The location of the bristles relative to the plane of the disc, as well as their length and stiffness, may vary, since they depend on the size and specialization of the model.


- Cordbrush (twisted roller cutter) is a wire attachment and is used in cases where coarse grinding and removal of primary irregularities is required. This variety is completely universal and can be used both for removing paint and varnish from wooden surfaces, and for removing rust from metal and concrete substrates.


- End circle designed for aligning the ends of the workpieces when performing bevel cuts. The surface treatment technique with its help remotely resembles the work of a file.
- Velcro discs used for processing stone, metal and concrete surfaces. They are a set of five circles that are fixed to the working base by means of an adhesive backing. The main disk, in its configuration, resembles a plate, with an adhesive applied to it - Velcro. It is on it that removable disks are installed. Models are produced with a diameter of 125 mm and more.They have different degrees of grain, which greatly facilitates the selection of the desired disc and allows you to purchase it for a specific material. The set usually includes sanding, polishing and felt models. The presence in one set of wheels of different purpose and structure allows you to grind and polish any surfaces to a mirror shine.


The next category of grinding wheels has a narrow specialization. It is intended for processing wooden surfaces and is represented by an emery petal model. The flap wheel is used for primary grinding and final polishing of wood products. It is a flat nozzle with trapezoidal sandpaper petals located on it. The petals overlap each other and visually resemble fish scales. Thanks to this structure, the attachments are highly wear-resistant, which is why one disc is enough for polishing 10 m² of wooden surface.
Flap wheels are produced with different grains, which allows grinding wood species of different hardness and structure. The models are produced in a wide variety of standard sizes, with diameters from 115 to 230 millimeters.

The third category of grinder abrasives is represented by models designed for the processing of particularly hard materials, including concrete, metal, marble and granite. This category is quite numerous and is represented by a large number of different models, the most popular of which will be discussed below.
- Double segment disc intended for rough grinding of natural stone, brick and concrete. The nozzle effectively removes various surface defects and cuts off thick layers of concrete screed.


- Dolphin model has a more gentle effect on the work surface than the previous tool and allows for a more delicate sanding. The product is characterized by light weight, high performance and long service life.
- Grinding wheel "Square" used to perform rough processing of the base, necessary for the subsequent application of a polymer coating on it. The sanded surface becomes rather rough and acquires high adhesive properties.

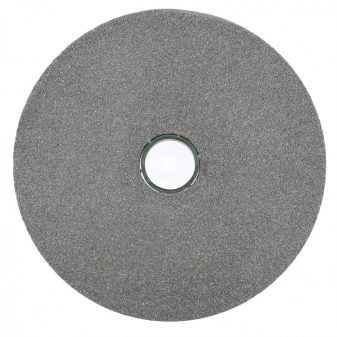
- Boomerang model it is lightweight and versatile. It is capable of processing concrete and masonry substrates, and its grinding quality can be compared to double-row diamond cutters.
- Disc "Turtle" used for the treatment of marble and granite surfaces. The tool makes stone bases absolutely smooth and gives them a mirror-like shine. This model is available in different grain sizes, which allows you to perform both rough primary grinding of the stone and fine polishing.
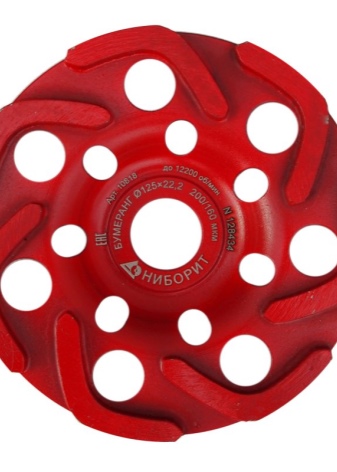

- Circle "Turbo" characterized by high wear resistance and is used for grinding reinforced concrete and metal substrates. Moreover, the tool is capable of chamfering and edging marble slabs, which is why it is used by master masons to create compositions from natural stone.


- Typhoon model presented in the form of a diamond grinding bowl-shaped structure, characterized by high performance and long service life. The product is used for rough primary processing of natural stone and for removing old decorative coatings from concrete walls.
In their shape, grinding wheels can be flat or cup. The first are fine abrasive emery or polishing discs and are used for polishing wood and other soft surfaces. Cup models are used for grinding serious surfaces and require a high power grinder. If such a model is installed on a low-power angle grinder, then the motor of the power tool will not withstand the increased load and will burn out.In addition to polishing especially hard materials, the cup bits are capable of efficiently processing hard-to-reach places where a flat disc cannot get close.


Grinding and polishing of metal pipes is done in a slightly different way. For this, a roller (drum) type nozzle is used, which effectively cleans the pipe surface from rust and paint residues. Moreover, the roller perfectly aligns the seams from welding, and when replacing the sanding strip with felt, it turns into a polishing tool.
In addition to felt, other non-abrasive materials are often used for metal polishing, such as foam rubber, sponge pads and cloth.
Fiber discs, which effectively remove oxidation residues, as well as grinding abrasive wheels, do an excellent job with welding scale. The latter have a thickness of 5 mm, are equipped with a recess on the inner side, and, in addition to leveling the weld seam, can be used for sharpening cutting tools.



Selection recommendations
Before you start buying grinder grinding wheels, there are several important points to note.
- It is imperative to check the correspondence of the rim and grinder bore diameters.
In order not to be mistaken in the choice, you need to rewrite the technical characteristics of the angle grinder and compare them with the sizes of the purchased attachments.
- When choosing the maximum outer diameter of the disc, it is necessary to take into account the power of the electric motor of the grinder. The more powerful the motor, the more the overall circle it can rotate. Low-powered models are not able to cope with large discs, which is why the latter are constantly stuck in the material being processed, causing the engine to overheat.

- As mentioned above, grinding wheels are divided into universal and highly specialized. A common mistake of consumers is the choice of universal models, the purchase of which seems to be more profitable. In fact, this is not the case. As practice shows, for each specific material it is better to buy "your" special disc, which will significantly increase the processing efficiency and save the motor from possible overload. Universal models can only be selected for rough rough grinding, while for finishing work it is better to purchase a specialized model.
- Pay attention to the thickness of the nozzle. The thicker the circle, the longer it can be used.
- The grit size of abrasive models is also an important criterion. The higher it is, the smoother the finished surface will be.
- When choosing a circle with Velcro, it is better to opt for a perforated model. Such a disc will not overheat at high speeds and will not ignite.
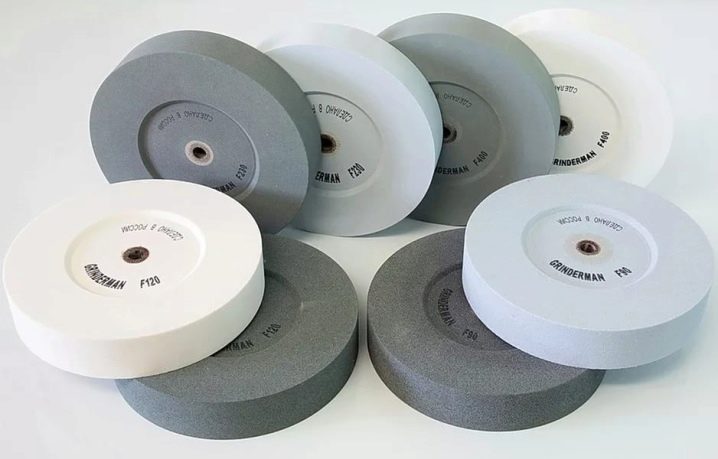
Subtleties of use
Before starting to work with the tool, it is necessary to make sure that the blade is correctly seated and securely fastened. When the device is connected to the network, the sound of a running engine should be uniform, without extraneous noise and vibration. Otherwise, switch off the unit and reinstall the grinding disc.
In the process of grinding and polishing, it is necessary to monitor the condition of the wheel, if the slightest defects are found, work should be stopped immediately.
This is due to the high speed of rotation of the wheel, reaching 13,000 rpm in some models, and a breakage of the disc at such speeds can lead to injury.


When using overhead wheels made of sandpaper, it is necessary to monitor the degree of its abrasion, otherwise the main wheel may be damaged. To avoid such situations, use discs as thick as possible. When working, it is worth using personal protective equipment. These include special goggles, canvas gloves, a respirator or gauze bandage, and long-sleeved work clothes. It will be useful to equip the workplace with a dust removal system and a chip sucker.In addition, when working with concrete structures, as well as when removing weld scale from metal surfaces, the operator should not be in the area where the fragments are flying.

In the process of grinding and polishing, it is recommended to use special grinding pastes or solutions saturated with fine abrasive particles.
The primary processing of the metal is performed with low-abrasive wheels, and the final polishing is performed using felt or fabric nozzles. As for the grit class, coarse-grained nozzles marked 40-60 units are used to remove the paint and varnish layer and rough processing of the planed surfaces. For removing the top layer from old wooden surfaces, for adjusting edges and joints, as well as for sanding the cut line - the best option would be a sanding attachment with an average grain size of 60-80 units. And, finally, when performing fine finishing sanding, as well as when preparing substrates for applying paints and varnishes, fine-grained nozzles of 100-120 units are used.
You will learn how to install a grinding wheel on a grinder from the following video.
The comment was sent successfully.