Grinder attachments for grinding wood: varieties and tips for choosing

The grinder belongs to the universal equipment in demand in the construction market. For angle grinding and polishing of wood, replaceable discs are attached to the tool axis. Grinding and polishing wheels are available in many varieties and are classified according to the type of abrasive surface.
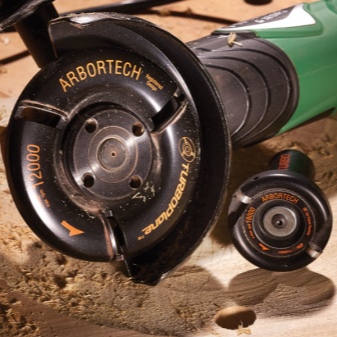

What it is?
A grinder or angle grinder is a tool often used in construction and during repair work. If the house needs minor repairs, there is no point in buying powerful and expensive construction equipment. But such a car will be useful and relatively inexpensive to purchase. The versatility of a modern tool is its main advantage: with the help of angle grinders, they saw and cut, grind and level surfaces. The principle of operation of the grinder is simple: operations are performed by rotating nozzles.
Discs are divided into three types - sharpening, cutting or grinding (roughing). Operations are different in purpose and complexity, sometimes one machine has to process materials of different hardness, as a rule, it is stone and steel joints, as well as wood. Refurbished and processed wood parts, windows, floors and furniture are sanded.



The attachment for a grinder for grinding wood is a replaceable wheel, similar to that for a circular saw. The roughing cutter for primary grinding is made of durable metal, has teeth and is selected according to the diameter for each angle grinder. The size of the teeth is determined by the thickness of the wood layer. The shape of the tooth is also important. Variables are suitable for all types of wood, and trapezoidal ones are used only for soft varieties. It is also possible to roughly process the material with discs with straight teeth.
Sawing wood before processing is necessary with other, sawing cutters. They are monolithic, made of high-strength sheet steel. Some varieties are sprayed on the teeth.
Expensive types of wood are cut both lengthwise and across with special discs marked "thin +". Precision cutting is essential in furniture making and serious woodworking.


Varieties
Grinding is the basic purpose of angle grinders. In the case of working with wood, this is a complex process that requires care and skill from the master. Natural wood of different structure is brought to a perfect look with high-quality and reliable discs. Conventional diamond cutters will not work here. There are special grinding wheels for the woodworking industry.
High-speed cleaning and grinding takes place in two stages: coarse and fine.

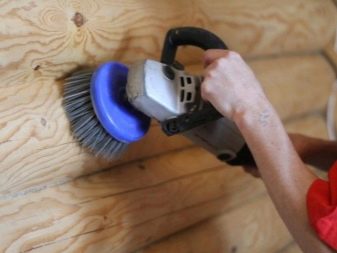
There are several types of angle grinder grinding wheels. First of all, the initial cleaning of the surfaces is carried out. This job is done by several discs that differ in shape and size.
- Roughing. They are designed to remove old paint and varnish from wood. Usually, residues of the previous coating that cannot be cleaned manually are removed from windows, sills and floor surfaces. A steel wire bristle is attached to the disc for rough processing. The elastic pile is placed either along the entire perimeter of the circle, that is, along, or at an angle segmentally as in a conventional brush. It depends on the purpose of the nozzle.
- Cord brushes with wire or spikes. They allow you to level and smooth the surface of any material.With a wire brush, it is easy to remove a layer of varnish or old paint, rust from the metal. If the boards on the floor are of different heights, they can be compared with each other with a spike circle. They differ in shape and speed of rotation.
- End pieces. They work in layers, like files, with sides and edges, corners and oblique cuts. The attachments are designed for sanding edges or smoothing bevels.



When roughing with a sander, the wood layer remains intact, only the decorative coating is removed. This property of the grinder is indispensable for the restoration of products. After removing the previous color scheme, you can apply another to the fresh and smooth panel. At the same time, the furniture will change its appearance and will look new. Brushing or artificial aging of the material is performed with a brush. To do this, the soft fibers are removed, and rings and texture appear on the natural wood. The stain emphasizes the relief transitions.
At the next stage of processing, the surface is smooth. Here, experts advise using polishing wheels. They are spongy, made of felt and coarse fabric, with replaceable sandpaper. The fabric and felt are secured for work with Velcro. Attachments are sold in sets of five for easy changing. Sandpaper is selected with a medium or fine grain. The brand is usually indicated on the packaging.
Even old paint can be removed with coarse paper, medium grain is suitable for cleaning small damages and removing a small layer. Fine-grained material gives the surface absolute smoothness.


The design of the nozzle is also important. Finishing or finishing circles are divided into flap, solid and mobile. The use of a petal wheel allows you to achieve an absolutely smooth surface. Several layers of emery, overlapping like fish scales, are placed on the disc as an abrasive. This arrangement of the abrasive material reduces wear. Such a modern nozzle as a cup circle brings the product to an ideal state. The bowl does little texturing, easily penetrates the joints. A pile made of synthetic material or corrugated wire is attached to it.
A nylon wood brush is made up of a large number of fine fibers. It is used for finishing polishing. The bowl-shaped attachment allows the technician to sand the most difficult-to-reach areas on the part. The brush removes burrs and small dirt, sands the varnish. End brushes are made of polymer abrasive, cylindrical ones are made of brass and steel wire.
On the construction market, modern grinding varieties of wheels with abrasives of three components are sold: aluminum oxide, nylon and polymeric materials.



Selection Tips
The attachments are acquired taking into account a strictly defined speed during rotation, the correspondence between the machine and the discs for it must be absolute. Several standard sizes of wheels are produced - from 115 to 230 mm. Shaft diameter - 22.2 mm. The smaller disc is easy to install on a larger grinder using special adapters. The nozzle is secured with a nut connection, a stud with a standard M14 thread.
In order to choose the right disk, experts recommend paying attention to several parameters.
- Thickness. It is believed that tighter circles last longer.
- Main diameter. The larger it is, the faster the grinding occurs. Larger circles are more reliable and last longer. Craftsmen prefer universal wheels with a diameter of 125 mm. In this case, it is easy to hold the machine with one hand for precise operations. The maximum size of 230 mm is rarely used when working with wood. Natural wood is not uniform, so it is better to resort to a gradual and gentle sanding. For repairs, discs of 150 mm are also suitable, sometimes even 180 mm.
- Segment type. Coarse abrasives are purchased for primary processing, soft abrasives for finishing parts.Usually, in everyday life, for processing large surfaces, both hard grinding and polishing wheels are needed.


How to use?
The grinder has a simple technical device. It is equipped with an electric motor connected to a bevel gear. It provides rotation of the shaft at a high speed of up to 1000 rpm (when working with wood, this speed is optimal). Powerful models require a three-phase power source; for domestic use, a standard power source with a voltage of 220 V is suitable. You have to work with the tool with a single point of support, holding the grinder on the weight. A skew can lead to a jerk, for this novice master needs to acquire serious skills to work.
Correctly working with the machine will allow compliance with safety measures, namely:
- carelessness in this matter is unacceptable;
- in order to exclude injuries when using angle grinders, the protective casing is not removed from the disk;
- do not work with wood using a strong feed;
- before starting operations, be sure to wear glasses and thick gloves; arms are protected with long sleeves, clothes should not be light, as sparks can fall on the body;
- it is important to take breaks during work so that your hands do not get tired and the machine does not slip.


It is convenient to work with a tool that has a support handle. The safest are those grinders that are equipped with a chain from a chainsaw. If the clipper suddenly jams, the disc continues to rotate, minimizing the risk of injury. It is also important to move the machine smoothly over the floor surface, free of vibration. Before starting work, you should once again make sure that the wheel is securely and accurately fixed on the axis.
It is better to start mastering the tool with cutters with small teeth. The smaller the teeth, the easier and safer the operations. In the process of work, any disc wears out, the diameter of the circle changes, a replacement is needed. Discs are changed when switching from one type of processing to another during the grinding process.
It also happens that the disc is cracked or the casing is broken. It is imperative to remove and replace such a disk, further work is dangerous.


It is worth adhering to the following step-by-step instructions:
- disconnect the tool from the mains, stop the rotation of the shaft by pressing the blocking button, only after that it is allowed to unscrew the disc and remove it;
- unscrew the retaining nut - the stopper is removed with a wrench, if the nut is tightened too tightly on the disk, you will need a gas wrench, which is heated and cooled before use, and the rest of the disk is cut out with a hacksaw;
- remove the unusable disk;
- put on a new one and secure it with a lock nut, firmly fix the thread on a precisely installed disc, then you can continue to work.


See the next video for more details.
The comment was sent successfully.