Tips for choosing grinders for working with concrete

A concrete grinder or angle grinder (angle grinder) is a great tool for cutting grooves in walls or sanding and polishing the surface of a concrete floor. However, not every model is suitable for solving such problems, therefore it is worth figuring out how to choose the right unit for processing.
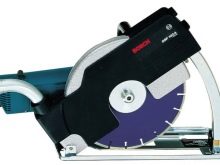


Models
To begin with, it should be said that angle grinder is a very versatile tool. It can handle many different materials, and individual models usually do not have a clear specialization - to "change the profile" you just need to buy a special disc for a specific material and use only it. Accordingly, there are probably no units exclusively for cutting reinforced concrete, but it should still be understood that some models may not be able to handle such a durable material.
To begin with, it is worth deciding on the type of food. Network grinders are the most common, they are considered the most versatile and convenient for home use, but you are unlikely to be doing concrete grinding at home. If you do not do this even in a workshop, but work at a construction site, where there may be problems with the power supply, it is better to turn your attention to battery or even gasoline solutions.
The latter are distinguished by increased power, their service life depends only on the available reserves of gasoline, however, modern professionals often prefer battery models, since in recent years they have become more powerful and durable, and there is less fuss with them.


Although you will choose a disc later and separately, you should decide in advance on its maximum allowable size, since you cannot put a large disc in a small grinder. For precise cutting and grinding work, a small version with a 125 mm disc may work, but to cut large concrete blocks, you may need a more serious tool - up to 230 mm. Unfortunately, aggregates of different classes are far from always interchangeable, therefore professionals often have to buy two devices at once with an eye on different disk sizes.
The power of the grinder should be considered exclusively in conjunction with the diameter of the disc used, because it is clear that the larger the latter, the less the engine power affects the torque. It should be noted that units with a power below 1 kW, regardless of the size of the disc, are considered domestic, in principle, they are not particularly suited for processing concrete, and even long-term.
LBMs with a power range of 1.3-2.7 kW are considered a construction tool, and you should pay attention to them.


As for the speed of rotation, it is usually of fundamental importance for increasing the speed of the task - the faster the circle spins, the better. At the same time, replacing the circle with a lighter one can increase the rotation speed, and with a heavier one, accordingly, decrease it. In a professional tool, the option to adjust the rotation speed is often found, and if you plan to process different materials with the purchased tool, then it is better not to ignore this opportunity, because some fragile structures easily crumble from excessive pressure.
Weight, by the way, should be chosen according to a rather confusing scheme. It is clear that an increase in the severity of the tool does not contribute to the duration of the work, therefore it is generally accepted that an aggregate weighing 1-2 kg can be used daily for up to four hours, and structures weighing 3-4 kg already assume work only 2-3 hours a day. However, if the work is really hard, then they choose not light, but, on the contrary, heavy models weighing up to 9 kg, which weigh a lot, but have the highest power, therefore they are able to cope with the task extremely quickly. In the case of concrete processing, the last option seems to be the most appropriate.


Even the number of pens matters, but here the question is not about the material to be processed, but about the way it is processed. So, for cutting various materials, even one handle is usually enough, since the angle grinder during such operations has a fairly stable position, but grinding is desirable only with a two-handed tool. Finally, when choosing a portable battery or gasoline grinder, pay attention to the degree of its autonomy.
The battery capacity is usually from 2 to 4 A / h, the higher it is, the longer the unit will work, delivering maximum power, which is usually required for concrete processing.
A similar relationship is observed when choosing the volume of the tank, which is usually 0.7-1.5 liters, but if you have the opportunity to carry a can of gasoline with you, this problem is usually solved entirely.

LBM can be equipped with a number of "bonuses", which are simply not available in cheap trim levels. This is, for example, a case that is convenient for transportation, a soft start system to reduce the load on the engine when turned on, or a lock of the start button so as not to tire your finger with constant pressing. We have already mentioned the speed control above, and there is also the option to stabilize the speed, which works automatically and is very useful when working with heterogeneous materials such as reinforced concrete. Working with concrete is always very dusty, and the special protection against dust for the gearbox and the shaft, in combination with the branch pipe for the construction vacuum cleaner, will make tasks more comfortable for both equipment and humans.
Finally, the choice of a grinder is almost always an attempt to "guess the quality", unless you clearly know which model you came for. For an inexperienced consumer, a good solution would be to target famous brands that have shown themselves well before - such as Sturm and Makita, Metabo and DeWalt. Some experts also trust certain domestic brands, although outside of Russia they are not known to anyone.




Disk
Above, we decided that when processing concrete, the model of the grinder is not so important as the correctly selected disc. Diamond wheels for concrete are called so, however, they are divided into several types, and not all of them are equally practical.
So, segmented circles are considered not quite the best choice, since their segmented edges suggest an increased risk of breakage when working with the same reinforced concrete, whose structure is heterogeneous, but they are chosen for a relatively low cost.
At the other pole are the wave-cased turbo-diamond discs - they are more expensive than any others.


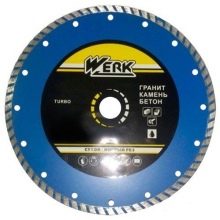
But on the other hand, they are designed for the maximum load, and therefore they will cope even with reinforced concrete of any strength. There are also just turbo diamond discs without a wave body - they, accordingly, occupy an intermediate position.
Among other things, the discs also differ in the way the soldering is attached - for example, it can be fastened with solder containing silver or be laser welded. The first option is suitable for wet cutting, the second is focused primarily on dry cutting and is appreciated for its increased productivity. Finally, it is worth checking the elementary conformity of the disc to the grinder. It must match the angle grinder not only in its diameter, but also in the diameter of the hole for fastening.At the same time, the maximum rotation speed permissible for a particular disc should be even higher than the grinder itself is capable of producing - this ensures that the disc does not burst during operation.


How the work is done
Each type of concrete has its own characteristics, therefore work always begins with an accurate determination of its characteristics. As a rule, experienced craftsmen choose special discs for plain and reinforced concrete, for fresh and old. Even blotches in the form of basalt or quartz can tell you which disc is best if you have the experience to understand such clues.
If possible, the concrete should be cut wet. A thin layer of water allows the cut-off wheel and tool to cool down, which extends the service life of the latter and ensures continuous operation. If there is no water nearby or there is not enough water, the cutting is performed dry, but in this case it is impossible to rush - the work is usually performed in several stages, allowing the unit to cool down a little after each of the approaches. To make sure that the tool and the disc successfully cope with the task, the first cut is completely limited to a depth of 1 cm, after which the grinder and the disc are carefully examined for possible mechanical damage.
Work continues only if none are found.

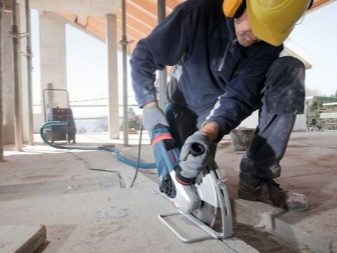
The sawing procedure itself is quite simple. Even with wet cutting, care should be taken to protect the respiratory system in case something goes wrong. After that, you should clearly outline the line of the future cut, and the supports on both sides, made of wooden bars, at the same time will help not to go deeper into the thickness of the material than it should be for the first cut. The first cut, as already mentioned, is usually made to a depth of no more than a centimeter. When cutting wet, spray water on the blade as carefully as possible, there should not be too much water, otherwise, if it gets into the engine of the angle grinder, it can cause damage to the electrical unit.
When the first notch is made and the cutting disc has cooled down a little, the wooden stands are removed - now you can navigate without them, along the existing notch. When cutting to a considerable depth, it is advisable to divide the work into several stages.



Even without knowing the exact structure of a particular concrete product, you can be sure that when you go deeper into the thickness by more than 10 centimeters, the probability of finding metal reinforcement there almost reaches 100%, so choose the appropriate disc.
How to work with a grinder correctly is described in the next video.
The comment was sent successfully.