Monolithic strip foundation: construction features
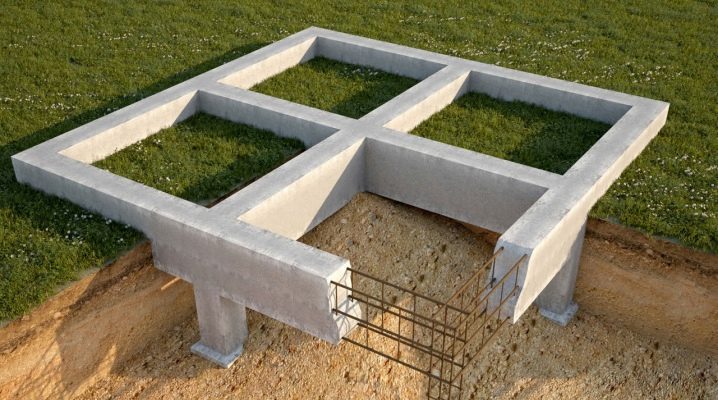
The monolithic strip foundation is an inseparable system of steel reinforcement and concrete. A foundation of this type is laid along the perimeter under all the walls and partitions of the building. With the correct calculation and erection, the monolith is strong, reliable and stable, it is suitable for buildings and structures of the most diverse sizes and purposes.
The organization of a monolithic strip foundation is most expedient with a low occurrence of groundwater, otherwise it is necessary to arrange a drainage system.
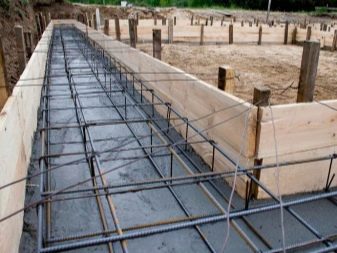
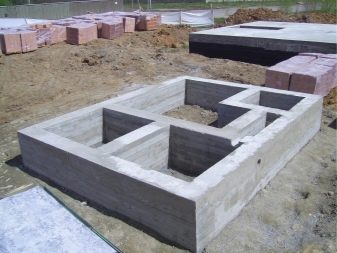
Peculiarities
The foundation structure absorbs all loads from the building and distributes the load to the foundation soil, which protects the walls from deformation due to ground movements. The main design feature of the strip foundation is the rule - the height should be at least twice the width. Provided that concrete is reinforced, it can carry significant loads, more than pile, columnar and grillage foundations. A monolithic strip foundation is used for the construction of various objects. With its help, it is possible to erect both low-rise buildings for various purposes (individual residential houses, summer cottages, baths, outbuildings), and auxiliary buildings (greenhouses, outbuildings, fences).
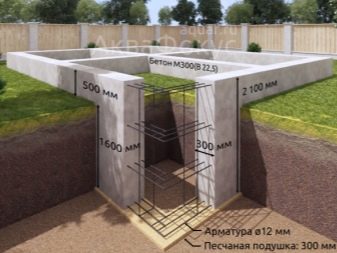
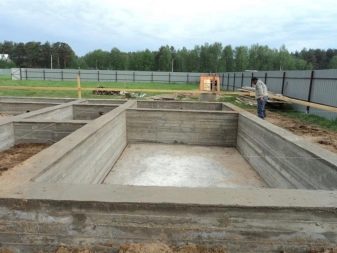
In the design and construction of a monolithic tape, several regulations must be taken into account. When calculating, they are guided by the data according to the region of construction according to SNiP 23-01-99 "Construction climatology", SNiP 2.02.01-83 "Foundations of buildings and structures". At the stage of selection of materials and installation of formwork, GOST R 52085-2003 “Formwork. General technical conditions ", GOST 5781 82" Fittings ".
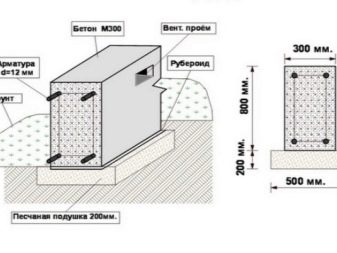
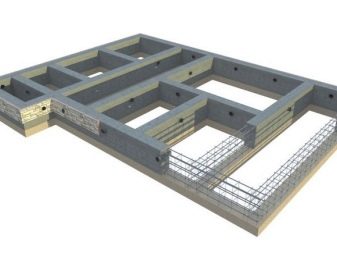
This type of foundation has many advantages.
- Strength. Provided that the calculation is correct, the monolith will withstand the loads from the building in any conditions.
- Durability. The service life of a monolithic strip foundation is from 150 years. This duration is achieved due to the integrity of the structure and the absence of seams. Compared to "tapes" made of bricks, concrete blocks, whose service life is 30–70 years, the choice of a monolith for durable buildings is more expedient.
- Possibility of constructing a basement and basement.
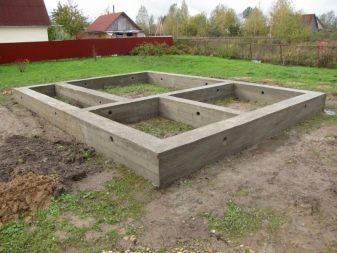
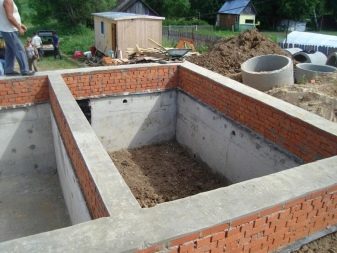
- The possibility of building a building of any configuration, because a monolithic strip foundation is poured on the spot directly into the formwork, the shape and size of the foundation can be of any kind. There is no binding to the factory size of the blocks.
- The possibility of self-laying. The technological process of installation and pouring is quite simple, so there is no need to attract specialized construction equipment or hire highly qualified specialists. You can lay a monolithic "tape" with your own hands.
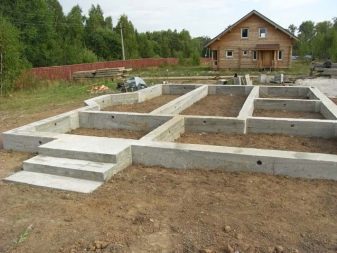
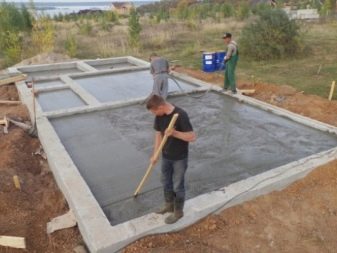
The monolith also has disadvantages, among which, first of all, it is worth highlighting the high cost of the foundation, which consists of the cost of materials (concrete, fillers, steel reinforcement, backfill materials, waterproofing), the cost of work (earthworks, a bundle of reinforcement, installation of formwork) ...
When self-laying, you will need a team of 4–5 people, a concrete mixer, and an apparatus for vibrating concrete.
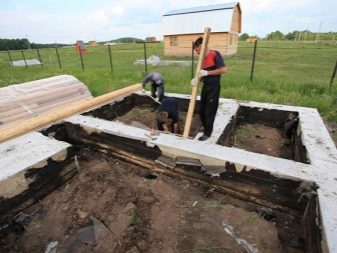
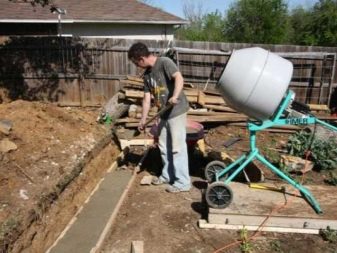
Device
Reinforced concrete strip foundations can be of two types.
- Shallow options can be used on calm, non-rocky soils with good load-bearing capacity for small buildings (frame buildings, wooden houses).In this case, it is enough to bury the tape 10–15 cm into the hard soil layer, which is under the fertile soft layer. It should be noted that the total height of the foundation, according to the standards, must be at least 60 cm.
- Monolithic strip foundations deep-seated arranged under heavy houses. As a rule, they are lowered below the level of freezing of the soil by 10-15 cm according to climatic standards. It is important that the sole rests against a solid layer of soil with a high bearing capacity. In this regard, there may be a need for additional deepening of the foundation to the required support.
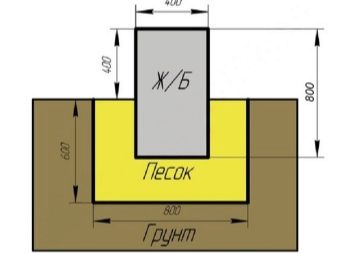
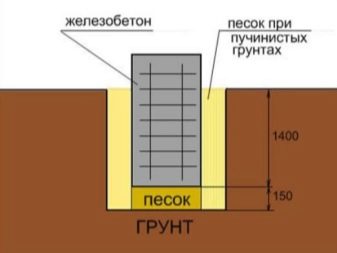
The technology for the production of strip foundations varies. Such foundations are as follows:
- prefabricated - consist of reinforced concrete blocks and prefabricated pillows. Prefabricated foundations are erected very quickly; construction equipment will be required for installation work;
- monolithic - such structures are made immediately at the construction site. Reinforcement is laid in the formwork and concrete is poured. A monolithic reinforced foundation does not require the involvement of construction equipment, because it can be done independently, even without specialized skills.
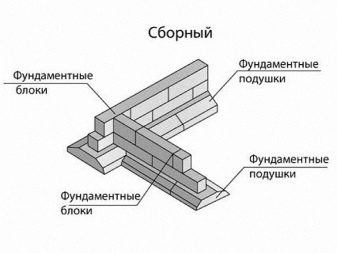
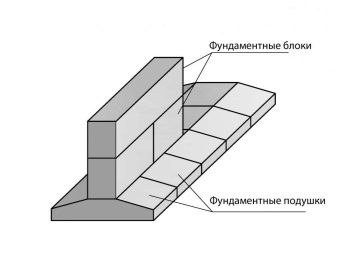
The main material of the concrete structure is Portland cement. His brand is selected according to the project. For the construction of individual residential low-rise buildings, Portland cement of the M400 brand is usually taken. And also fillers (crushed stone and sand) and water are part of the concrete pour. The structure can be rubble concrete, in this case rubble stones are used as a filler.
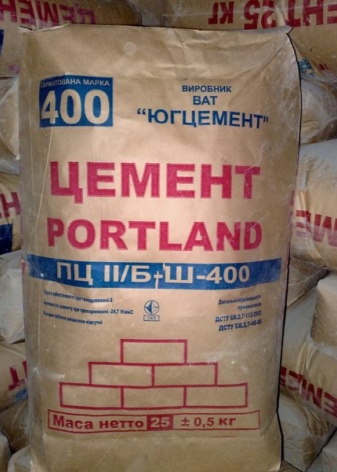
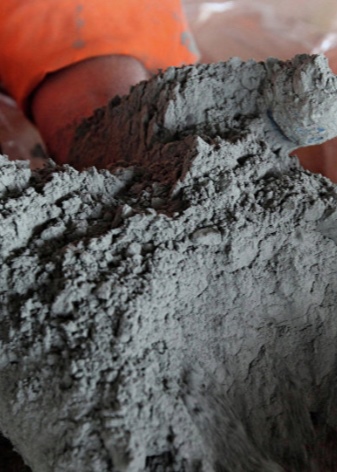
Reinforced concrete has the best strength characteristics for the foundation. It is a concrete fill, reinforced with a steel frame. Reinforcement mesh consists of longitudinal and transverse rods connected by knitting wire. Formwork is an essential element of the monolith. It is collected from wooden boards, plywood sheets and chipboard. The most common use of planks 25–40 mm thick from coniferous wood. Of these, shields are mounted, which are fixed in the pit.
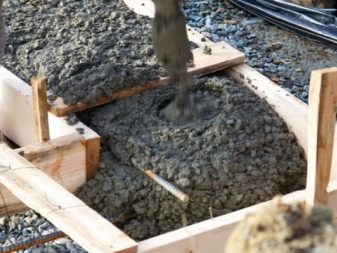
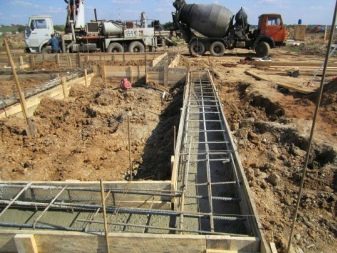
By the type of material and filling of the concrete mixture, monolithic foundations are divided into types such as:
- concrete;
- reinforced concrete;
- rubble concrete.
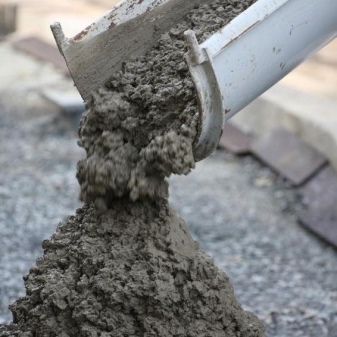
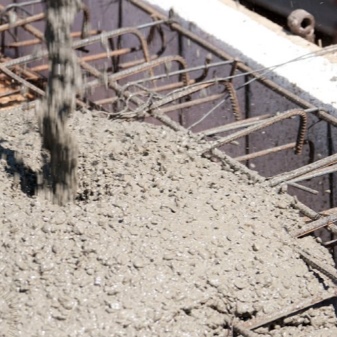
An important issue in the design and installation of foundations is the constructive solution of the floors. When installing a monolithic strip foundation, the soil under the floor remains saturated with moisture, from which the floor needs protection. With a low plinth, floors are made on the ground. In order to avoid subsidence, the pit is backfilled with crushed stone and sand on the compacted soil. A layer of waterproofing is arranged on top of them. The floor slab is made not connected to the foundation tape, the joints are provided with waterproofing. In addition, to remove excess moisture, a drainage system is arranged around the building, which includes a storm sewer to drain rainwater masses from the foundation. These activities are quite costly.
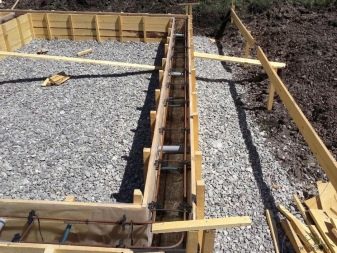
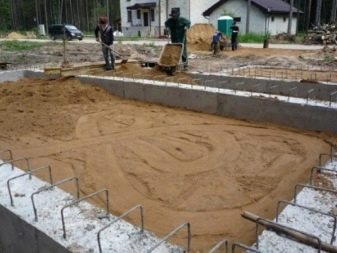
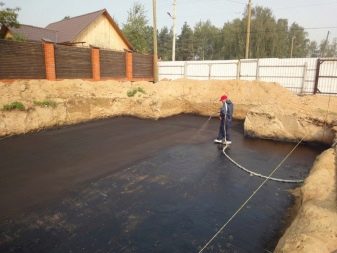
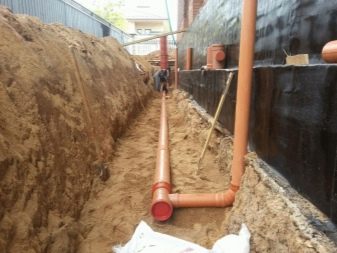
A striking example of a monolithic strip foundation device is the option with a blind area. Floor slabs in the form of slabs are usually used to create an underfloor space. In this case, ventilation holes are made in the basement of the house, which are open during operation all year round.
When creating a ventilated underfloor space, you can use any thermal insulation materials.
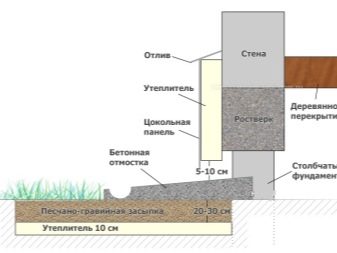
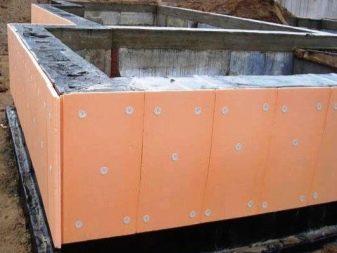
Payment
Foundation design begins with a calculation. Initially, it is necessary to determine the depth of the laying, the height of the above-ground part, the width of the tape. The parameters of the depth and width of the monolithic strip foundation depend on the type of soil, the depth of freezing, and the mass of the building. If the "tape" of the foundation is deepened, then the depth of the structure is calculated based on the maximum freezing depth at the design site plus 25-30 cm.
If the foundation is shallow, then its foundation is determined by the nature of the soil with the following minimum deepenings:
- clay soil - 75 cm;
- sandy and loamy soils - 45 cm;
- stony and rocky sites (including artificially prepared ones, with sand, crushed stone, gravel) - up to 45 cm.
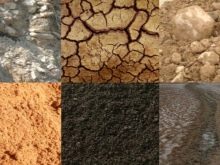
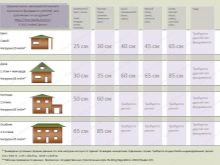
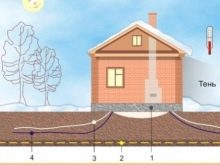
The width of the foundation should ensure that a load of no more than 70% of the bearing capacity of this soil is transferred to the ground. The minimum size of the thickness of a monolithic strip foundation is 30 cm. The calculation of the width consists in collecting the entire design load on the foundation, which must be divided by the full length of the foundation and the bearing capacity of the soil.
When collecting loads, the following values are taken into account:
- design weight of the house. It consists of a mass of all building structures - walls, floors, roofs. Approximate values can be taken from SNiP II-3-79 "Construction heat engineering";
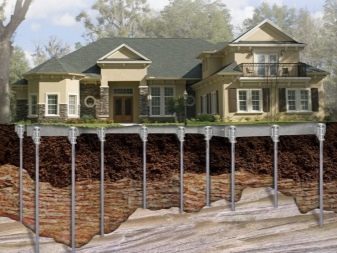
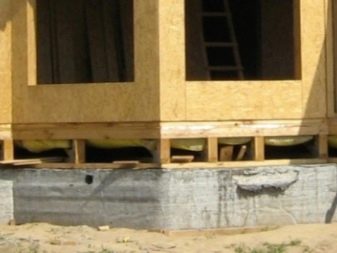
- snow and wind loads. They are determined for each climatic region and are calculated according to SNiP 2.01.07-85 “Loads and Impacts”;
- the weight of indoor equipment, furniture, people. It is calculated according to the regulations. A value of 195 kg per square meter of each floor is assumed, including the floor overlap on the ground floor.
The total weight is multiplied by a factor of 1.3 to determine the final load on the foundation. The value is obtained in kilograms. The length of the foundation is considered in total under all load-bearing walls and partitions. The bearing capacity of the soil on the site is determined approximately. The minimum is considered to be 2 kg / cm². It is suitable for all types of soils, except for clay and loamy soils.
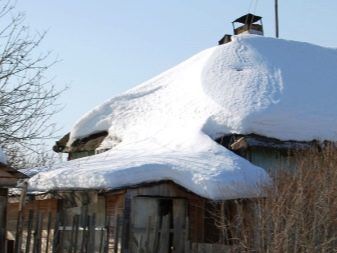
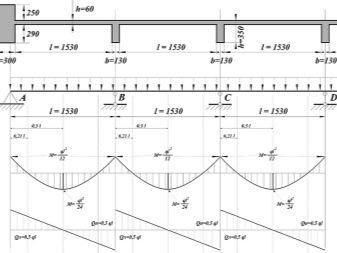
The height of the above-ground part of the strip foundation depends on the depth of its foundation and the width of the “strip” of the base. For this parameter, the maximum value is calculated at which the structure will be stable and firmly held in the base.
It is possible to determine the permissible height in two ways, such as:
- the values are taken in a ratio of 1: 1;
- the height is calculated relative to the sole. The projected width of the "tape" is multiplied by 4.
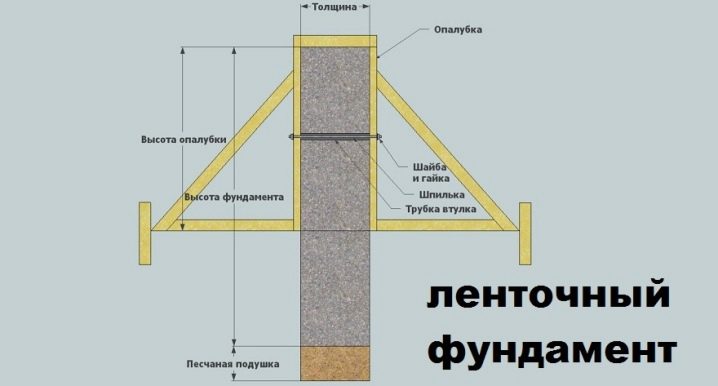
After calculating the parameters of the building foundation, the required amount of building materials is also calculated. Drawing up an approximate estimate will ensure a continuous construction process. From this point of view, it is important to calculate the required volume of concrete. The volume of the casting is calculated by the height, width and length of the foundation, using the formula for calculating the volume of a parallelepiped.
The total height is taken into account here: the aboveground and underground parts.
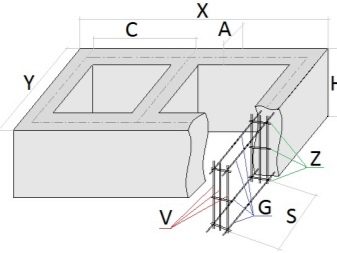
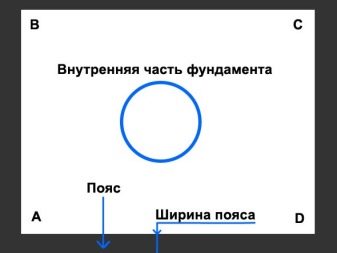
The number of reinforcement is calculated in total for the frame based on the length of the longitudinal rods and vertical rods, as well as their number. Vertical rods are usually installed every 50 cm, and at the corners. Their height is less than the height of the foundation by 10-15 mm. It is also necessary to calculate the formwork. The area of all surfaces on the side can be calculated by multiplying the height of the foundation by twice the perimeter. After that, you need to determine the area of the board (the length should be multiplied by the width). The area of the side surfaces is divided by the area of the board, and the number of formwork boards is obtained.
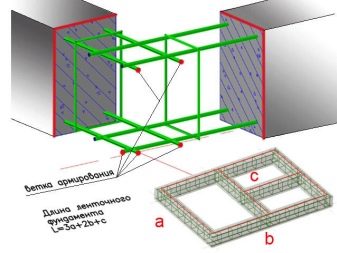
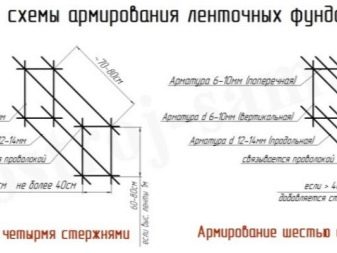
The estimate for self-laying of a monolithic strip foundation includes the following:
- materials for filling the "pillow" (sand, crushed stone, cement);
- ready-mixed concrete;
- fittings;
- soft wire for tying reinforcement;
- boards for formwork;
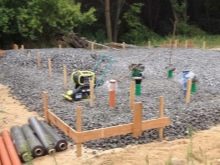

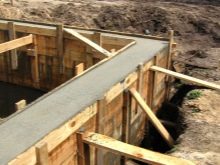
- waterproofing materials (bitumen, roofing material, polyethylene film);
- blind area materials (slab, concrete, sand, foam);
- Building tools;
- hiring workers or equipment for earthworks;
- equipment for concreting (concrete mixer, vibropress).
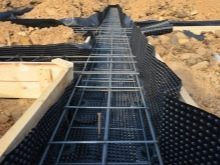
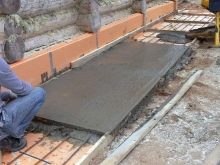
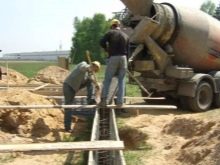
After determining the required dimensions of the monolithic strip foundation, a drawing of the foundation plan, joints and fittings is developed. The given example shows a diagram of the device of a monolithic strip foundation for a house with dimensions along the axes of 9800x11300 mm.It includes a foundation plan, section, reinforcement scheme.
The resulting diagram explains the following information:
- main structural elements and their sizes;
- the exact dimensions of the building in the axes;
- distance between elements in axes and in dimensions;
- exact mark of the foundation;
- waterproofing and thermal insulation. The building material used for the work is signed on the drawings;
- the diagram indicates the place of formation of the basement and blind area;
- device of the future floor covering with a floor slab adjoining unit.
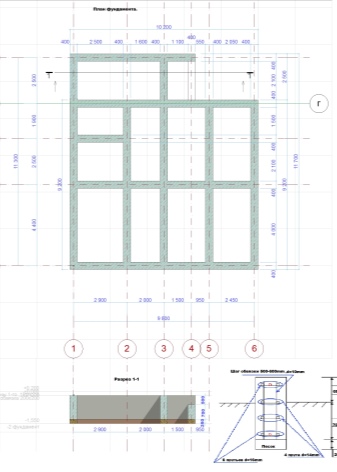
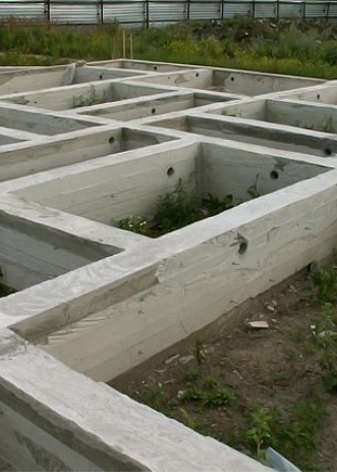
Construction
Regardless of whether the foundation is being made with your own hands or with the hiring of workers, it is very important to know the technology. Step-by-step control of the process is necessary at all stages of the installation.
Installation of a monolithic strip foundation includes several stages.
- Preparation of the construction site. First of all, it is necessary to clear the area of debris, prepare a place for storing materials. The dimensions of the pit are taken out to the cleared area. According to the marked dimensions of the house, the fertile soil layer is excavated. The corners of the future foundation are marked with pegs, from which the direction of the walls is indicated with cords. Marking works are carried out using the building level.
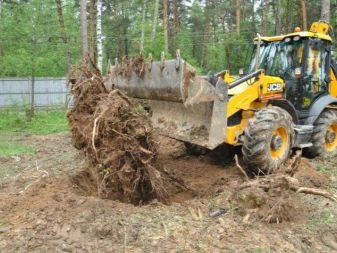
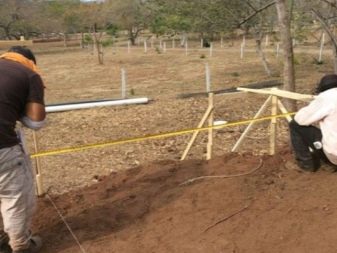
- Excavation. A trench is dug along the cord to the depth of the foundation. The width of the trench is determined by the design width of the tape, taking into account the installation of the formwork. Usually 20-30 cm are left for this on each side.
- Preparation of the base. The bottom of the trench is covered with a layer of sand, depending on the type of soil. For heaving soils, the layer thickness should be at least 20 cm. The backfill is tamped and lined with a waterproofing layer.
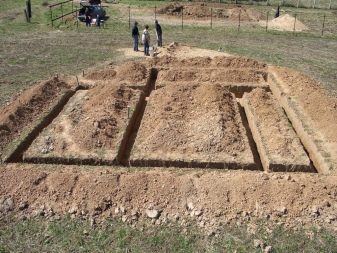
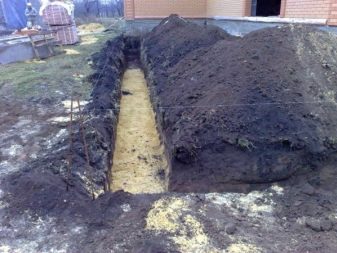
- Formwork assembly and installation. For the installation of the formwork, boards are prepared from the boards. When installing the formwork, the wall of the shield should be strictly vertical, the edge of the boards should be 5–10 cm higher than the pouring of the formwork. The panels are fastened together with self-tapping screws or nails and mounted in a trench using spacers and pegs. It is important to carry out this stage very carefully so that when pouring concrete, the formwork retains its shape. The walls of the formwork are covered with foil or mastic for ease of disassembly after the concrete has set.
- Knitting of the reinforcing cage. After the formwork has been installed, reinforcement can begin. The reinforcement frame is knitted from longitudinal rods A-III and transverse steel rods. When placed in the formwork, the reinforcement mesh is provided with a protective layer of 30 mm. To do this, you can use the trimming of the rods.

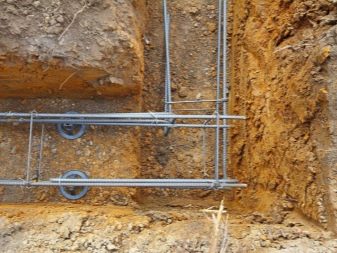
- Pouring with concrete mixture. After completing the installation of the reinforcement, it is necessary to pour concrete. Quality control, process continuity and temperature are important here. The filling of the formwork is carried out evenly. To achieve density, uniformity, and removal of air bubbles, concrete must be vibrated after pouring.
- Curing. All further work is carried out after the concrete has set. On average, wall installation can be started 1–2 weeks after pouring. For waterproofing a monolithic strip foundation, the side surfaces of the tape are covered with bituminous mastics. Backfilling can then be carried out.
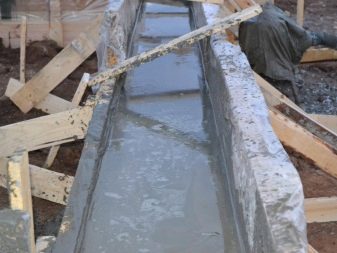
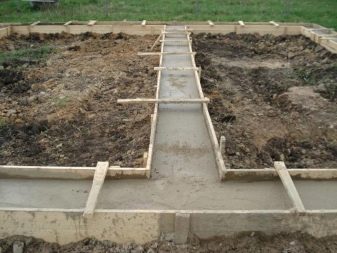
Advice
When building the foundation of a house, you need to take into account many nuances.
- The speed of the concrete hardening process depends on the temperature during work. In hot weather, the poured foundation is covered with plastic wrap to retain moisture and the top of the fill does not dry out.
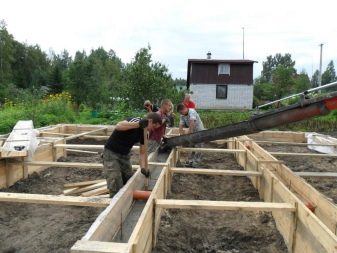
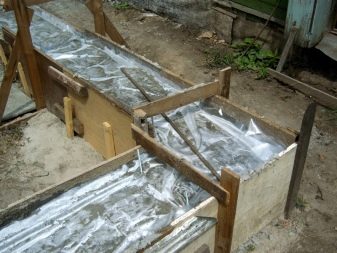
- The optimal temperature level for pouring concrete is considered to be about + 20 ° C, the strength of the mass of 50% is achieved on the third day. Further, you can remove the formwork and carry out further work. At a temperature of about + 10 ° C, this period is 10-14 days. A temperature of + 5 ° C requires insulation of the formwork or heating of concrete, concrete does not naturally freeze at this level of heat. Before the final hardening of the concrete, it should take about 28-30 days.
- When installing a monolithic strip foundation, it is important to take into account the place of passage of communications.For this, plastic pipes of the appropriate size are laid through the formwork.
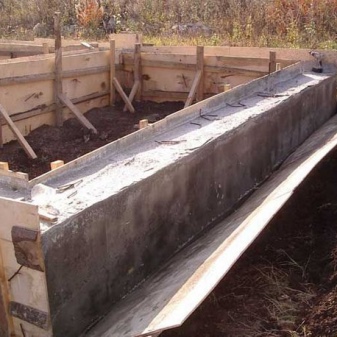
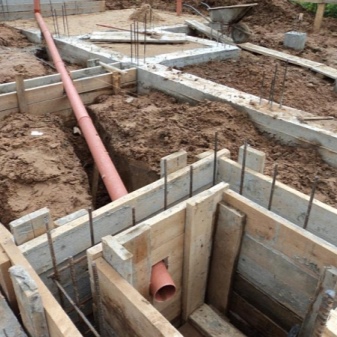
For information on how to make a monolithic strip foundation, see the next video.
The comment was sent successfully.