Enamel KO-811: technical characteristics and consumption
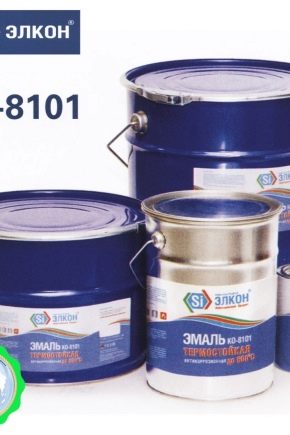
For a variety of metal products and structures used in outdoor conditions, not all paint is suitable that can protect the material from the negative effects of the environment. For these purposes, there are special organosilicon mixtures, the most suitable of which is the enamel "KO-811". Its special anti-corrosion and heat-resistant properties are considered optimal for metals such as steel, aluminum, titanium.
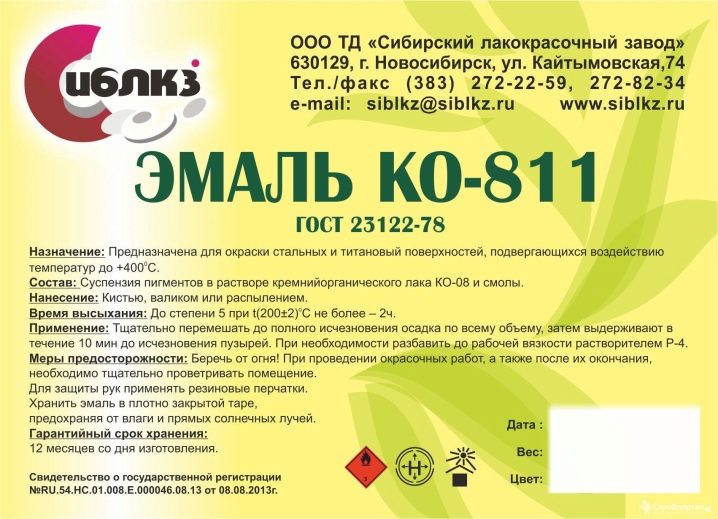
Composition and specifications
Enamel is a suspension based on silicone varnish and various coloring pigments. There are two types of product - "KO-811", produced in three basic colors (red, green, black), and "KO-811K" solution, enriched with fillers, special additives and stabilizer "MFSN-V". Thanks to this, its color range is more extensive - this paint is white, yellow, blue, olive, blue, dark and light brown, with a steel tint.
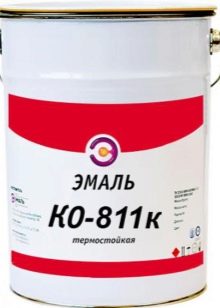
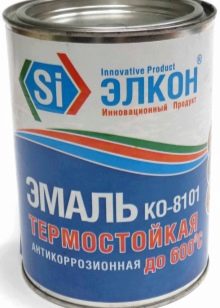
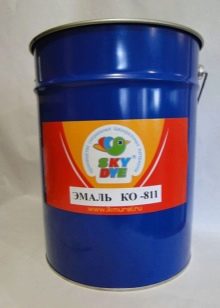
The main difference between the two types of mixture is that "KO-811K" is a two-component material, and in order to dilute it, it is necessary to mix the semi-finished enamel product with a stabilizer. In addition, it has a richer color gamut. Otherwise, the characteristics and properties of both enamels are practically the same.
The main purpose of the compositions is to protect metal parts during operation under conditions of temperatures reaching +400 degrees, and low temperature conditions - up to -60 degrees.
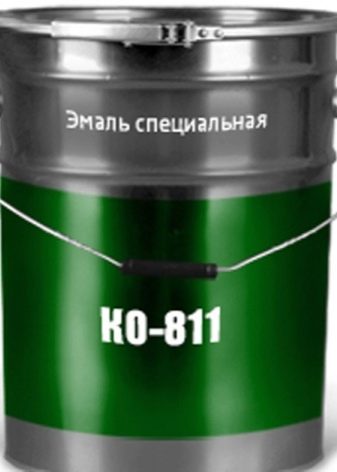
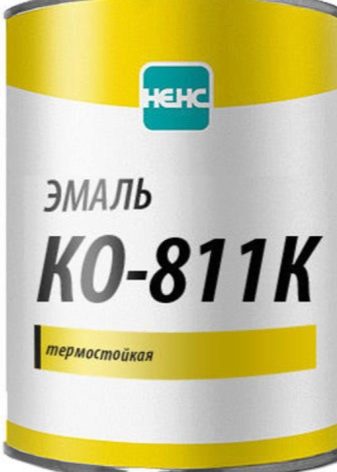
Paint specifications:
- The material is resistant to high humidity, oil and aggressive compounds such as gasoline, which allows it to be used in devices that have direct contact with these liquids.
- The ideal viscosity of 12-20 units at average room temperature makes it possible to apply quickly and conveniently by means of an electric and pneumatic spray gun.
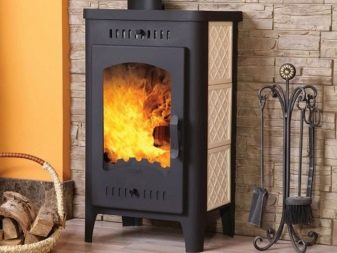
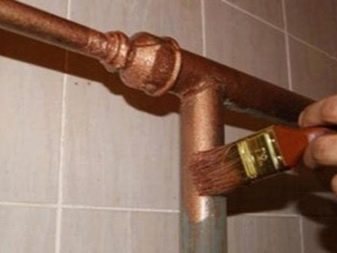
- After drying, an elastic film with a thickness of no more than 3 mm forms on the metal, therefore even small-sized products are subject to staining. In addition, the uniformity of the layer and its smoothness are the key to preserving the original appearance throughout the entire period of use.
- Heat resistance at critically high temperatures is 5 hours.
- The durable coating is not subject to mechanical damage under pressure and impact.
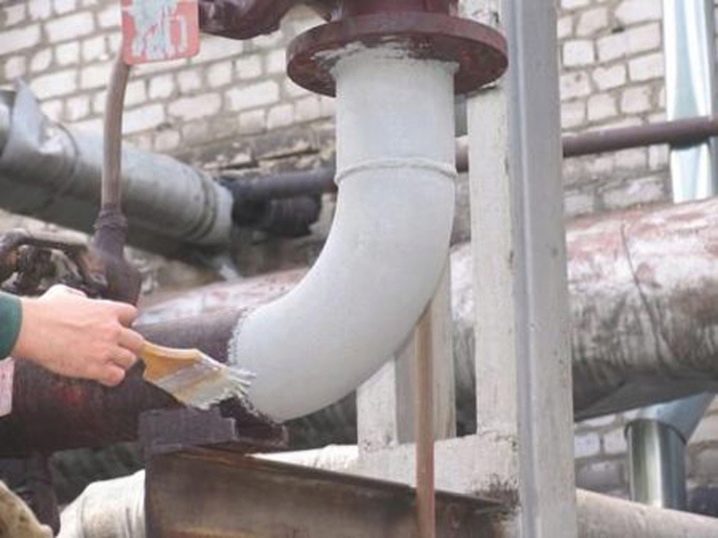
A pleasant bonus is the economy of enamel - its consumption per 1 m2 is only 100 grams with a coating thickness of 50 microns. Such a heat-resistant material can be used both in outdoor conditions and in rooms with high humidity.
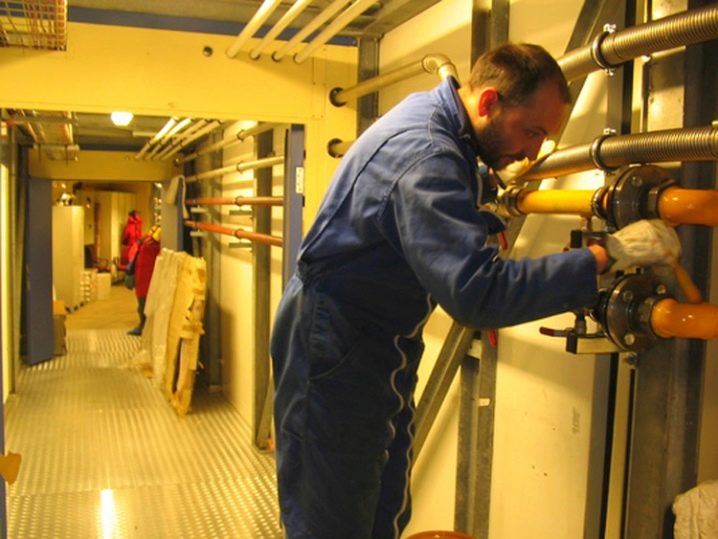
Solution preparation
Both types of enamels must be thoroughly mixed before use until smooth. It is important that no sediment particles or bubbles remain. Therefore, after stirring, the solution is kept for another 10 minutes until they completely disappear.
Enamel "KO-811" is diluted with xylene or toluene by 30-40%. The composition "KO-811K" is provided in the form of a suspension, paint and stabilizer. The dilution rate for white paint is 70-80%, for other colors - up to 50%.
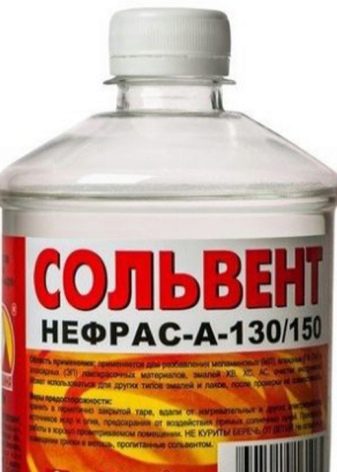
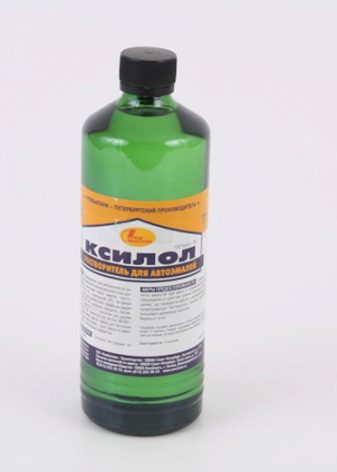
This should be done before the metal surface is prepared. The prepared solution should be used within 24 hours. Sometimes the resulting mixture needs additional dilution for working condition. Then use the solvent "R-5", solvent and other aromatic solvents.To obtain optimal consistency, the solution is measured with a viscometer, the viscosity parameters are usually specified in the quality certificate.
If interruptions in coloring are expected, it is better to store the mixture closed and be sure to stir it to resume work.
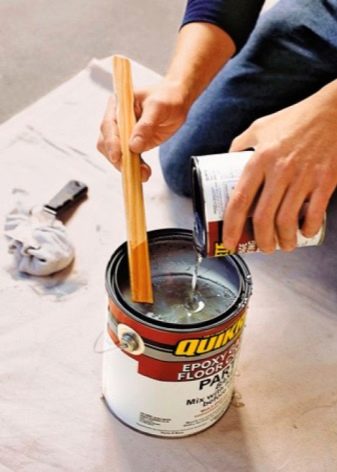
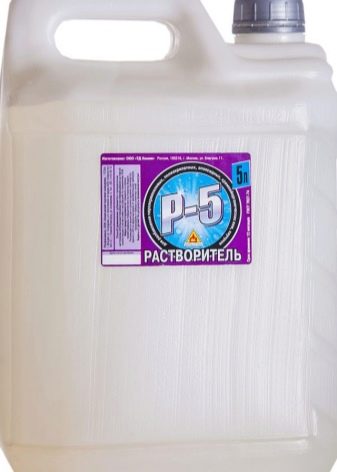
Cleaning metal surfaces
Preparing the substrate for painting is critical for proper adhesion to the enamel.
It includes two main stages:
- Cleansingwhen dirt, old paint residues, grease stains, scale and rust are removed. This is done mechanically or manually, or with the help of a special device - a shot blasting chamber. Mechanical cleaning provides the grade "SA2 - SA2.5" or "St 3". It is possible to use a rust remover.
- Degreasing produced by xylene, solvent, acetone using rags. It is advisable to do this before starting painting, no later than a day later during internal work. For outdoor work, a minimum of six hours should elapse.
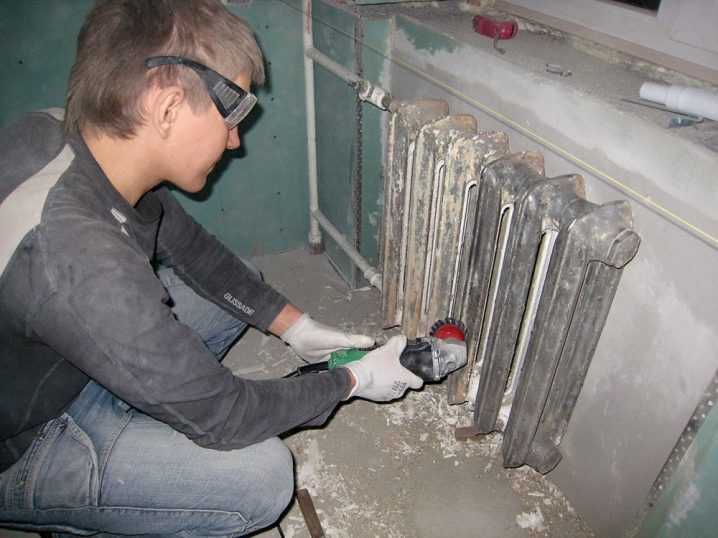
Partial processing of the metal is allowed in case of general good condition. The main thing is that the base is clean, dry and has a typical metallic luster before applying the enamel.
Dyeing process
Work should take place at a humidity of less than 80%, in a temperature range of -30 to +40 degrees. The spray gun will provide high-quality spraying, the minimum number of layers is two.
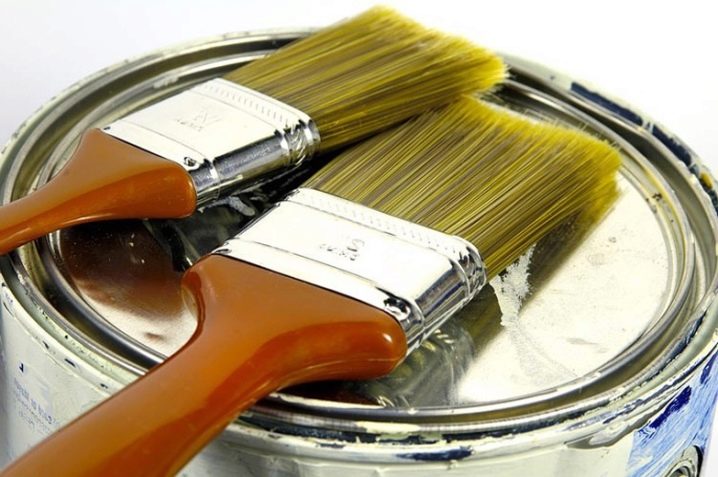
It is necessary to take into account some of the subtleties when painting:
- On areas with low accessibility, joints and edges, it is better to apply the compound with a brush by hand.
- When using pneumatics, the distance from the tool nozzle to the surface should be 200-300 mm, depending on the device.
- The metal is painted in two or three layers at intervals of up to two hours, if the temperature is below zero, the break time is doubled.
- Initial drying takes two hours, after which polymerization occurs and final drying, which is completed in a day.
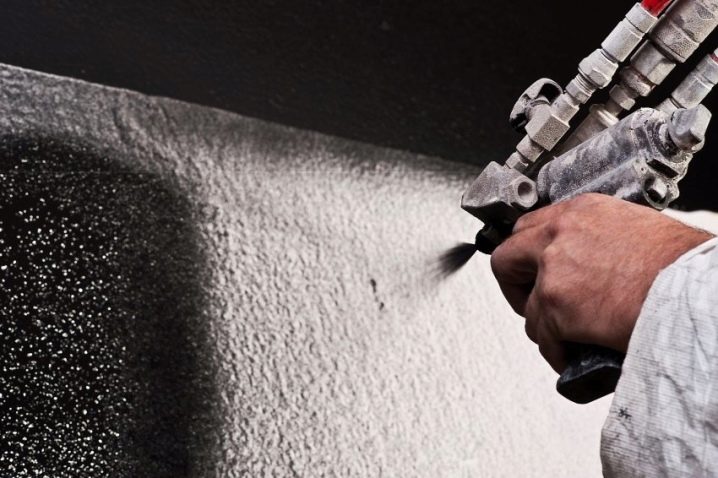
The consumption of the dye can vary from 90 to 110 grams per square meter, depending on the texture of the base, the degree of its porosity and the experience of the master.
When working, follow the safety regulations. Since the enamels contain solvents, this determines the III class of hazard to human health. Therefore, for quiet operation and harmlessness of the process, you should take care of the maximum ventilation of the room, personal protective equipment, always have on hand materials at hand - sand, asbestos fire blanket, foam or carbon dioxide fire extinguisher.
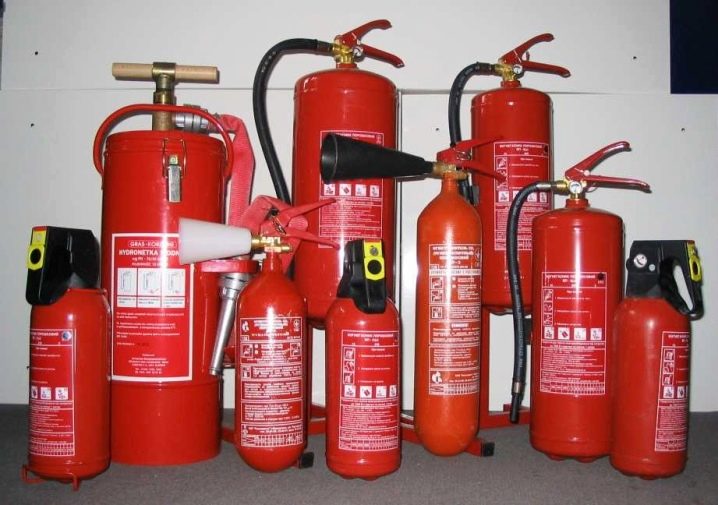
For information on safety when working with such materials, see the video below.
The comment was sent successfully.