Features of insulation and sound insulation of interfloor overlap on wooden beams
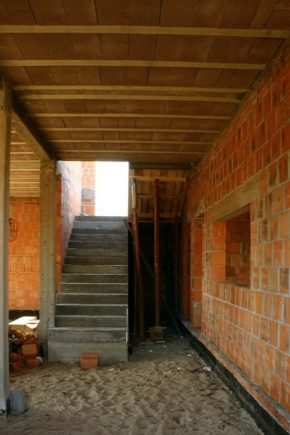
When building a house, thermal insulation and sound insulation are an important task. Unlike walls, floor insulation has a number of features. Let's consider the main ones.
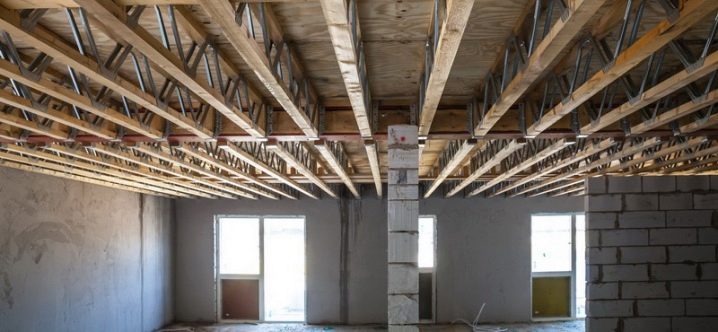
Description
The fastest and easiest method of interfloor insulation is timber beam decking. Installation of a bar at a certain distance does not require much effort. After that, it remains only to fill the resulting voids with heat and sound-insulating material and close everything with finishing the floor of the floor or attic. Wood is a good conductor of sound. Therefore, if you just sheathe the beams between the floors with wood, the heat and sound insulation will leave much to be desired.
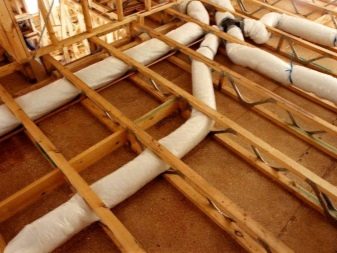

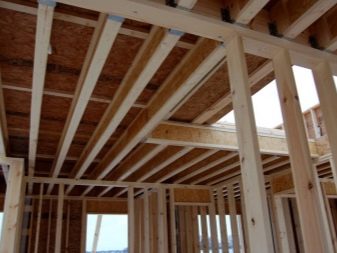
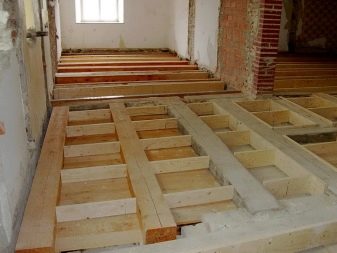
The correct choice of heat-insulating material must be carried out starting from where the overlap is located. So, for the overlap between floors, sound insulation is of great importance. The overlap between the floor and the attic should have more thermal insulation qualities. In a house with heating on all floors, the heat transfer to the upper floors should be taken into account. In this case, the choice in favor of the thermal insulation characteristics of the material will make it possible to maintain the microclimate of each room. Much attention should be paid to the protection of heat and sound insulating material from moisture. For this, steam and hydro insulators are used.
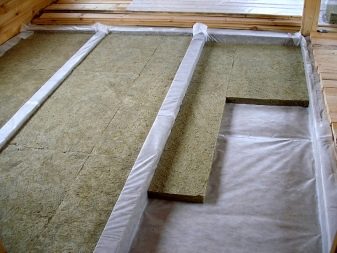
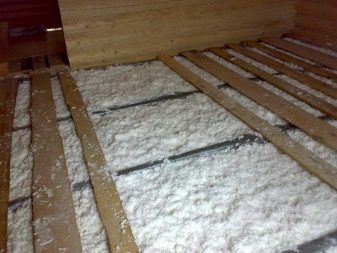
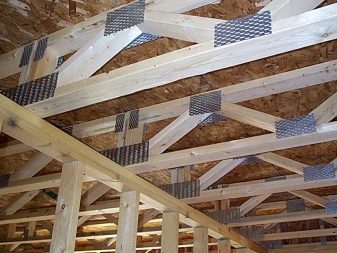
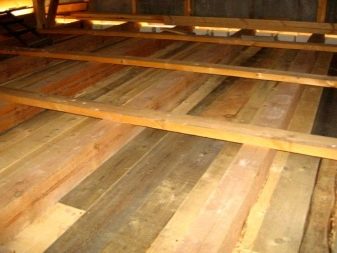
Norms and requirements
The overlap between floors is constantly under mechanical and acoustic influences that cause noise (walking in shoes, falling objects, slamming doors, TVs, speaker systems, people talking, and so on). In this regard, strict requirements for insulation have been established. The soundproofing ability is indicated by two indices. Airborne sound insulation index Rw, dB and index of the reduced impact noise level Lnw, dB. Requirements and standards are regulated in SNiP 23-01-2003 "Protection against noise". In order to meet the requirements for interfloor floors, the airborne sound insulation index should be higher, and the index of the reduced impact noise level should be less than the standard value.
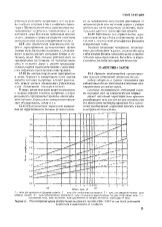
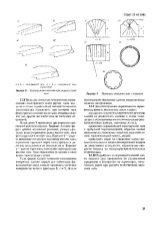
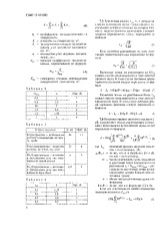
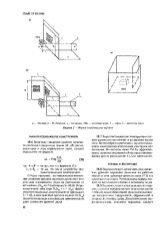
For insulation of floors on the territory of the Russian Federation, the requirements set forth in SNiP 23-02-2003 "Thermal protection of buildings" are also imposed. The requirements for insulation are determined by the location of the floor. When choosing insulation for floors between floors, they are more guided by what the structure will be. For example, if insulation is placed between logs or beams, preference is given to low-density basalt insulation or fiberglass.
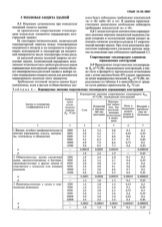
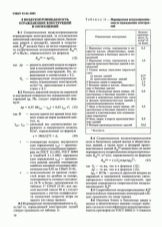
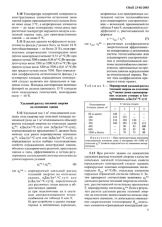
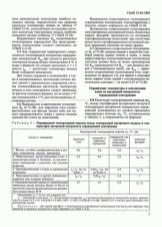
If the insulation is arranged under the screed, then the density should be high. In addition to thermal insulation properties, the insulation must meet the requirements of environmental safety.
Classification
To classify noise insulation, you can divide all methods of dealing with noise penetration into two parts.
- Soundproofing - reflects sound from a wall or ceiling, which significantly prevents the penetration of noise behind the structure. Such properties have dense materials (concrete, brick, drywall and other reflective, sound, materials) The ability to reflect sound is determined primarily by the thickness of the material. In construction, when designing, the reflection index of the building material is taken into account. On average, it ranges from 52 to 60 dB.
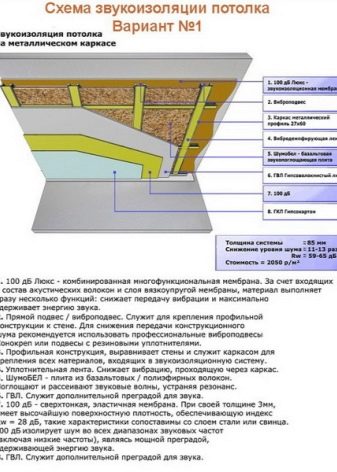
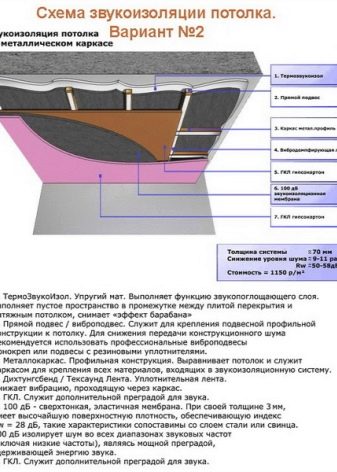
- Sound absorption - absorbs noise, preventing it from reflected back into the room.Sound absorption materials generally have a cellular, granular or fibrous structure. How well a material absorbs sound is assessed by its sound absorption coefficient. It changes from 0 to 1. At unity, the sound is completely absorbed, and at zero, it is completely reflected. It should be noted here that in practice, materials with a factor of 0 or 1 do not exist.
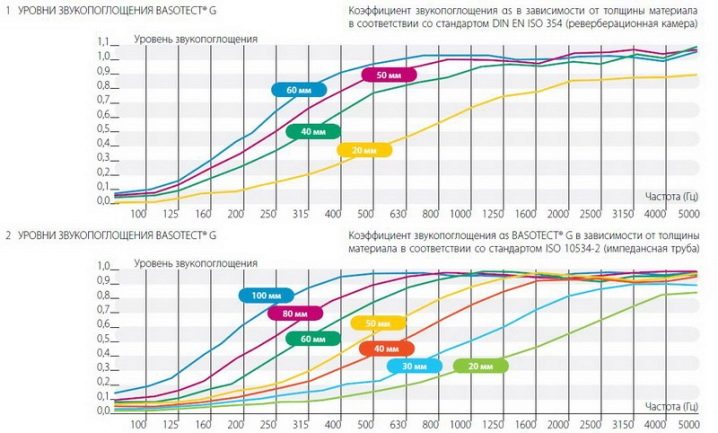
It is generally accepted that materials that have a sound absorption coefficient greater than 0.4 are suitable for insulation.
Such raw materials are divided into three types: soft, hard, semi-hard.
- Solid materials are mainly produced from mineral wool. For greater sound absorption, fillers such as perlite, pumice, vermiculite are added to the cotton wool. These materials have an average sound absorption coefficient of 0.5. The density is about 300–400 kg / m3.
- Soft materials are made on the basis of fiberglass, mineral wool, cotton wool, felt, and so on. The coefficient of such materials ranges from 0.7 to 0.95. Specific weight up to 70 kg / m3.
- Semi-rigid materials include fiberglass boards, mineral wool boards, materials with a cellular structure (polyurethane, foam, and the like). Such materials are called materials with a sound absorption coefficient of 0.5 to 0.75.
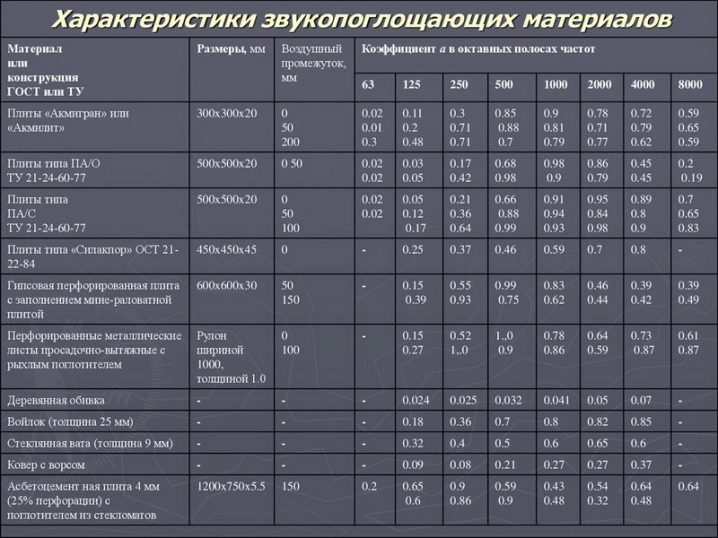
Material selection
Soundproofing and soundproofing in houses with wooden floors can be carried out with different materials.
A list of the most common ones is below.
- Fibrous sound-absorbing materials - are roll or sheet insulation (mineral and basalt wool, ecowool and others). This is the best way to deal with noise. Located between the plane of the ceiling and the floor of the ceiling.
- Felt - is laid over the logs, as well as at the joints of walls, seams and other areas where it is necessary to prevent penetration through structural leaks.
- Cork, foil, rubber, polystyrene backing - a thin material for laying on top of flooring or beams. Isolates the room from impact noise and vibration.
- Sand - placed on a polyethylene backing, at the bottom of the entire soundproofing. This makes it possible to almost completely solve the problem of sound insulation, in combination with other materials.
- Expanded clay - laying and the principle of operation is similar to that of sand, but due to its large-sized structure and lower specific gravity, it is more convenient. Eliminates spillage when the substrate breaks.
- Subfloor - mounted from chipboard and OSB sheets on the principle of a floating floor, does not have a rigid connection with the overlap, due to this it dampens sounds.

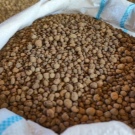
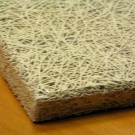
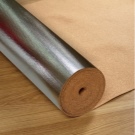
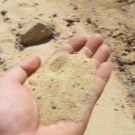
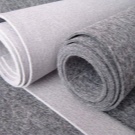
To achieve the required level of sound insulation, a "pie" is assembled from a combination of different materials. A good result, for example, is given by the following order of materials: ceiling covering, lathing, vapor barrier material, mineral wool with a rubber-cork backing, OSB or chipboard plate, finishing materials. It takes a little bit to choose insulating materials. study the most common of them in more detail and choose the most suitable ones according to the description.
- Glass wool - the material is made of fiberglass. Has high strength, increased vibration resistance and elasticity. Due to the presence of empty spaces between the fibers, it absorbs sounds well. The advantages of this material have made it one of the most common in heat and sound insulation. These include low weight, chemical passivity (no corrosion of contacting metals), non-hygroscopicity, elasticity. Glass wool is produced in the form of mats or rolls. Depending on the design of the floor, you can choose the most suitable option.
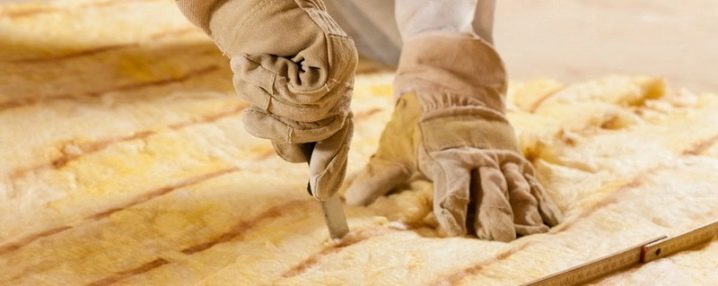
- Mineral wool - material made from rock melts, metallurgical slags or mixtures thereof. The advantages are fire safety and chemical passivity. Due to the chaotic arrangement of the fibers in vertical and horizontal positions at different angles, great sound absorption is achieved.In comparison with glass wool, the disadvantage of this material is greater weight.
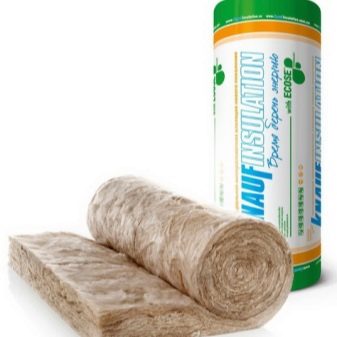
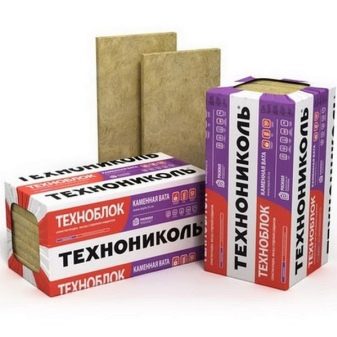
- Multilayer panel - at present, soundproofing systems are found convenient to use, since they are one of the leading means of soundproofing partitions (a wall of brick or concrete, etc.). These systems are made of plasterboard and sandwich panels. The sandwich panel itself is a combination of dense and light layers of gypsum fiber and mineral or glass wool of various thicknesses. The model of the sandwich panel determines which material is used in it and how the layers of materials vary in thickness. It is not fire hazardous, but it is also not recommended for use for insulation of floors, since in this situation the installation and cost of the material becomes more complicated, which will lead to unnecessary construction costs. For ceilings, it can be used in some specific situations, if this simplifies the installation of sound insulation. The big drawback of the panels is their heavy weight, which must be taken into account when installing.
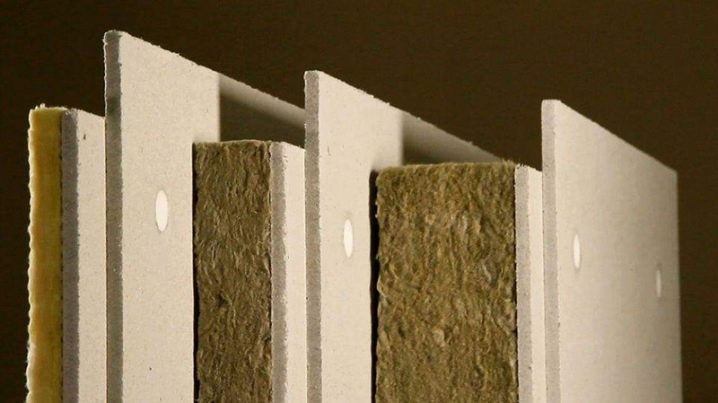
- Pressed sheet from natural cork chips - one of the most effective materials for insulation against impact noise. The material is resistant to rodents, mold, parasites and decay. Inert towards chemicals. In addition, durability is a plus (it lasts 40 years or more).
- Polyethylene foam - most suitable as a substrate for laminate, parquet and other floor coverings. Effective against impact noise. It has several varieties, which is a plus for achieving the corresponding sound insulation requirements and minimal costs. Resistant to oils, gasoline and many solvents. It has a number of disadvantages such as fire hazard, instability to ultraviolet radiation, it loses up to 76% of its thickness under prolonged loads. Moisture incidents create conditions for mold and mildew growth. One of the inexpensive materials.
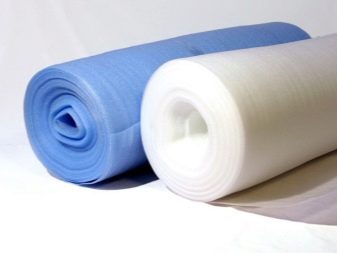
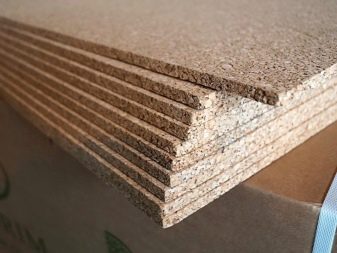
- Cork rubber backing - made in the form of a mixture of synthetic rubber and granular cork. Designed to reduce shock Noise. Convenient for use under elastic and textile coatings (linoleum, carpets and others). It is also used with no less efficiency under hard floor coverings. The disadvantage of this material can be called the fact that in the presence of moisture it can serve as a favorable environment for mold, therefore additional moisture insulation is needed. For this, plastic wrap is well suited.
- Bituminous cork substrate - made of kraft paper impregnated with bitumen and sprinkled with cork chips. Cork filling is located at the bottom, this helps to remove moisture from under the laminate. No waterproofing required. The disadvantages of this material are that cork crumbs can fly off the canvas, with excess moisture, it rots, stains when laying.
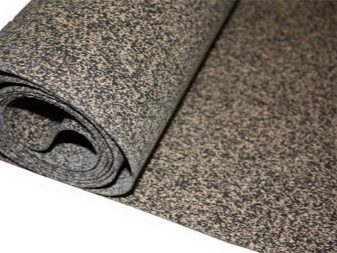
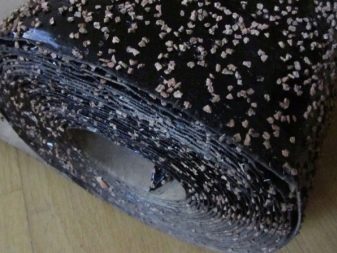
- Composite material - consists of two layers of polyethylene film and a layer of expanded polystyrene granules between them. Polyethylene films have different structures. The upper one protects the coating from moisture, and the lower one allows moisture to penetrate into the middle layer, which removes it around the perimeter.
- Extruded polystyrene foam - has low water absorption, high strength. Ease of installation of this material is determined by the ease of cutting, simple and quick installation, minimal waste. Ease of installation determines the low cost of work. It is durable, retains its properties for 50 years.
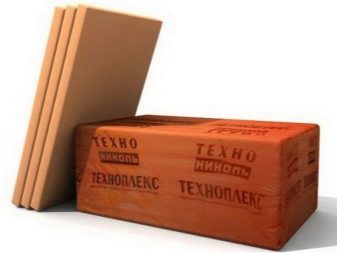
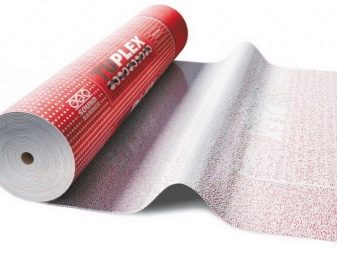
- Fiberglass - applicable for the isolation of structure-borne noise. The porous fibrous structure provides this opportunity. It is used with sandwich panels, frame sound-insulating facings and partitions, wooden floors and ceilings. Depending on the material with which it is used, the installation technology is also selected. When installing wooden floors or floors, it is laid in places of support on walls and under beams.Moreover, if the ends of the beams rest on the walls, in order to avoid hard contact with other building structures, the fiberglass must be insulated with a gasket.
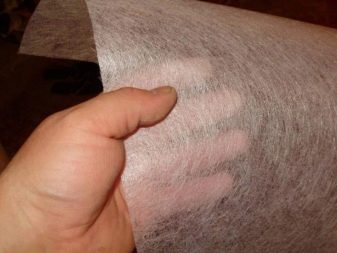
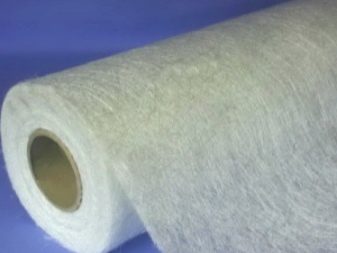
- Vibroacoustic sealant - serves to provide vibration isolation. To reduce structure-borne noise, it is located between structures. Convenient to use for filling words in constitutions. Good adhesion to plaster, brick, glass, metal, plastic and many other building materials. After hardening, there is no smell, does not pose a danger in handling. During the performance of work, the premises must be ventilated. Avoid contact with eyes during operation.
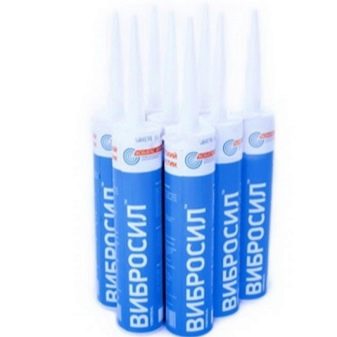
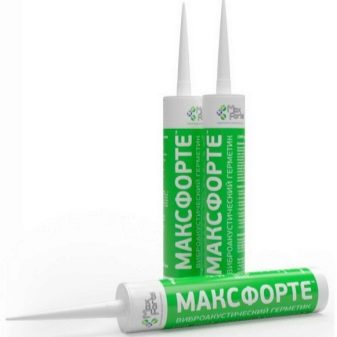
Based on the properties outlined above, you can select the most acceptable material for the constructed floor.
Payment
Typical errors in the calculation of sound insulation is a comparison of two materials, which indicate the characteristics of sound insulation and sound absorption. These are two different indicators that cannot be compared. The sound insulation index is determined at frequencies in the range from 100 to 3000 Hz. The popular belief that foam is a good sound insulating material is also a mistake. In this case, a 5 mm layer of good soundproofing material is superior to a 5 cm layer of foam. Styrofoam is a tough material and prevents impact noise. The greatest effect of sound insulation is achieved when hard and soft insulation materials are combined.
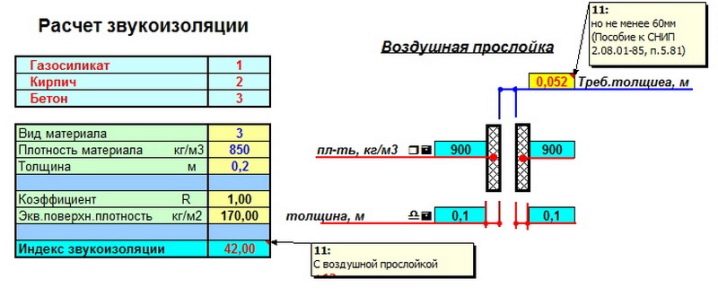
Each insulation material is characterized by its resistance to heat transfer. The greater this characteristic, the better the material resists heat transfer. To provide the required level of thermal insulation, the thickness of the material is varied. Currently, there are many online calculators for calculating thermal insulation and sound insulation. It is enough to enter data on the material and get the result. Comparing with the tables of SNiP requirements, find out how the proposed option meets the necessary standards.
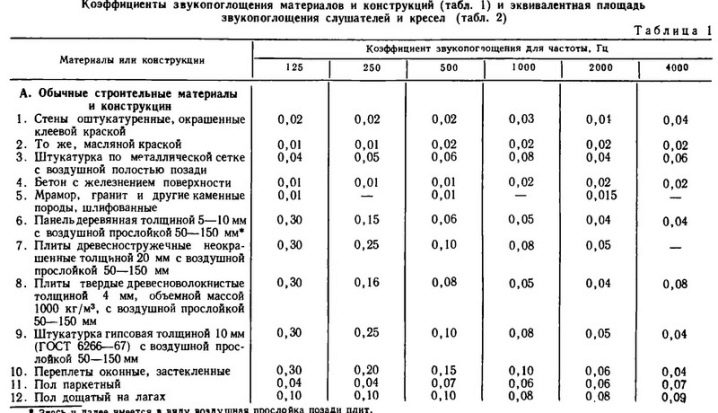
Laying technology
In a private wooden house, the installation of noise and sound insulation is best carried out during construction or at the stage of rough finishing. This will get rid of the contamination of the finishing materials (wallpaper, paint, ceiling, and so on). Technologically, the process of laying noise and sound insulation is not difficult, and you can do it yourself.
An example is the following order of installation steps.
- First of all, the entire timber must be covered with an antiseptic. This will protect the tree from the appearance of parasites, mold, fungi and decay.
- At the next stage, the rough flooring is packed from the bottom of the beams. For this, boards with a thickness of 25-30 mm are suitable.
- Then the vapor barrier is installed on top of the formed structure. The joints of the vapor barrier must be glued together with construction tape. This will prevent the insulation from shedding. The edges should go on the walls to a height of 10-15 cm, which will protect the insulating material on the sides from moisture penetration from the walls.
- After the vapor barrier layer is hermetically fixed on the rough flooring, insulation is laid on it. In this case, the thermal insulation material is mounted not only between the beams, but also on top of them. This is to avoid crevices through which sound and heat can pass. In general, this approach will provide the highest level of noise and sound insulation.
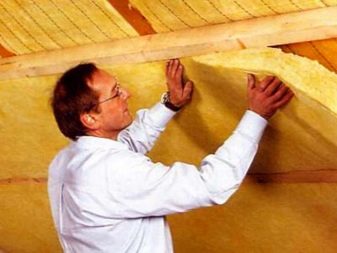
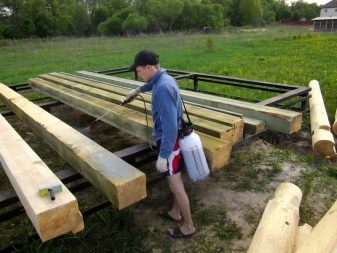
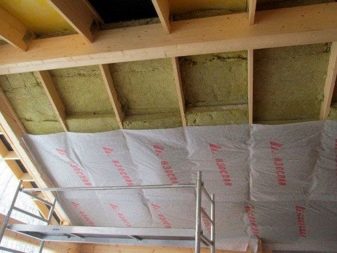
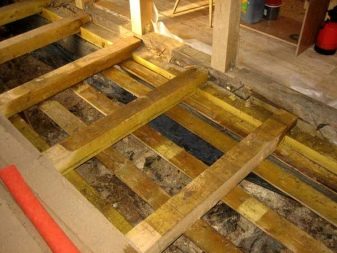
- At the final stage, the entire insulation is covered with a layer of vapor barrier. As in the initial stages, this will serve to protect the insulation from moisture and steam. It is also necessary to glue the vapor barrier joints tightly with tape. After completing these stages, heat and sound insulation are ready. It remains to mount the subfloor. For this, you can use boards with a width of 30 mm. But the best option would be to fix the chipboard, in two layers. In this case, the edges of the chipboard should lie on the logs, and the second layer should be mounted so as to overlap the joints of the first layer.
- As a result of the operations done with the subfloor, a coating will be obtained that does not have a connection with the beams, the technology is called a floating floor. In this case, the coating is held by its own weight, and the absence of an attachment with a beam structure prevents the passage of impact noise. This method is additional soundproofing. When purchasing boards made of chipboard and OSB, insulating materials, it is imperative to find out their manufacturer and, if possible, the type of material. Building materials can give off toxic gases, therefore better materials are recommended.
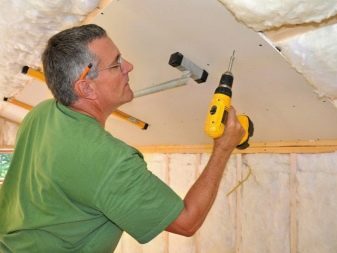
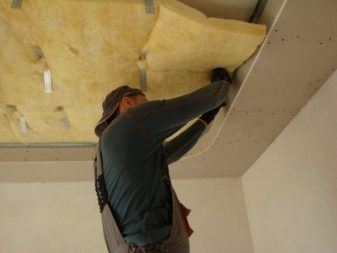
In monolithic houses, two-story or having more floors, on concrete floors, heat and sound insulation are arranged under the screed.
Helpful hints
When choosing sound insulation and thermal insulation, it is necessary to take into account all the characteristics of materials in terms of resistance to the passage of heat and noise. Find out how they meet standards or personal requirements to pay attention to cost savings. Since the desired effect can only be achieved with alternative materials or another order of installation of insulation. An important role is played by the extent to which the raw materials used are harmless to health.
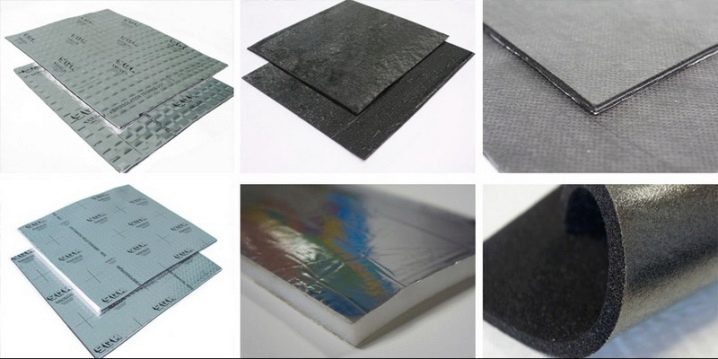
An additional role in increasing noise and sound insulation can be played by a change in the structure of the ceiling. For example, different types of wood have different thermal conductivity and sound conductivity. Large voids between the joists also contribute to an increase in sound insulation. You can use different types of spacers for fixing logs, subfloors, topcoats. If the insulation and sound insulation is mounted independently, then it is advisable not to neglect the advice and recommendations of specialists. Particular attention should be paid to the fact that a violation of the technology of laying insulating materials can lead to a decrease in the desired result, an increase in costs, and in the worst case, to the loss of material and fragility of work.
For information on how to insulate the interfloor overlap using wooden beams, see the next video.
The comment was sent successfully.