Clinker facade thermal panels: application features and installation details
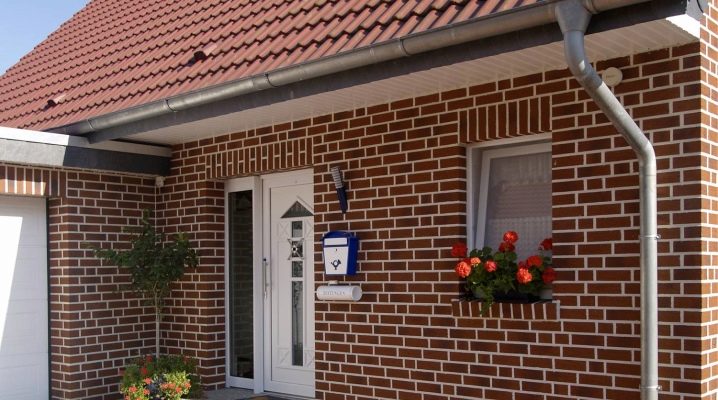
The facade is known to have a protective and decorative function. For its organization, materials such as insulation, facing plates and panels are used, and in addition, steam and waterproofing films. However, today there is a material that combines the best properties of clinker tiles and polyurethane insulation. We are talking about thermal panels.
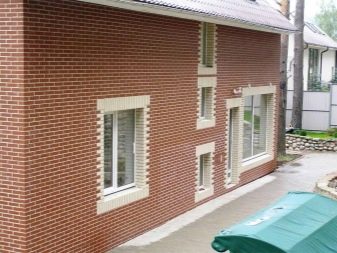
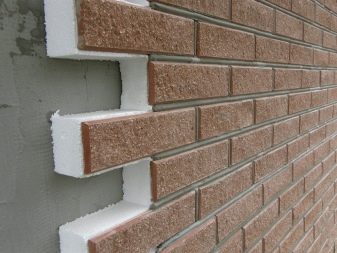
Peculiarities
Clinker thermal panels are a material that simultaneously performs the function of insulation and the function of a decorative facade material. Structurally, the thermal panel includes several layers.
- Clinker tiles, which contains natural clay of special fatty grades. The raw material is subjected to high-temperature firing, due to which it acquires increased strength and moisture resistance. Externally, the clinker is similar to the surface of the brickwork. Depending on the type of material, it can imitate bricks of different sizes and shades, aged bricks, as well as stone surfaces made of wild or processed stone. Clinker thickness is in the range of 7-15 mm.
- Insulation, due to which a low thermal conductivity of the tile is achieved. The most common, due to its technical properties, is polyurethane foam. When combined with clinker, it forms a non-combustible product, since both components do not ignite, and do not emit toxic compounds under the influence of high temperatures. Polystyrene can act as a substitute for polyurethane foam. The thickness of the insulating layer ranges from 30 to 100 mm.
- Layer of marble chips or compressed wood chips, which acts as a reinforcing component, gives the board additional rigidity. In addition, when it comes to a chip layer, it also contributes to an increase in the thermal efficiency of the material. This is due to the fact that the chips are made from coniferous wood, which is distinguished by its ability to retain heat well.
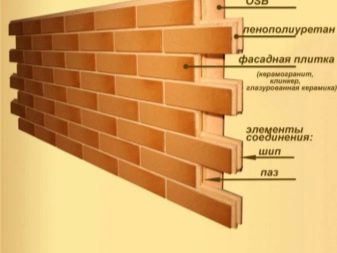
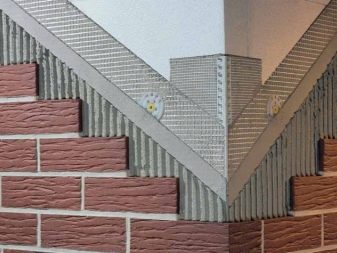
All layers are securely fastened together, forming a monolithic thermal panel. This design is the most popular among the cracked panels.
There are also two-layer options, which consist only of clinker and insulation, and four-layer, similar to three-layer, but have an additional refractory layer.
Fastening of products to the facade is carried out "dry", by means of fasteners and systems, or "wet", using adhesives and other mixtures, methods. Thermal panels of the type PK-1, PK-2, which have special locks that interlock with the frame elements, are fixed using the "dry" method. Panels of the type PK-1F and PK-2F are more versatile, they can be glued to the facade or attached to the crate. The choice of a specific installation method is primarily due to the state of the foundation of the building, the bearing capacity of its facade, as well as the thermal conductivity of the facade walls.
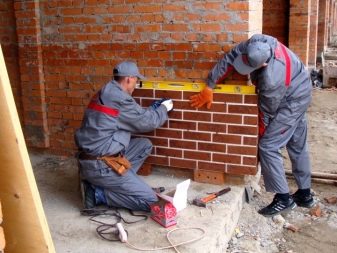
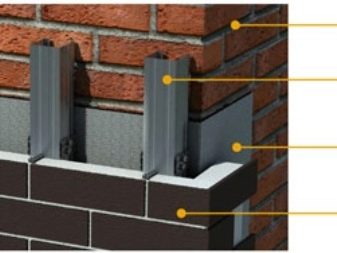
Advantages and disadvantages
Clinker tile itself is a popular finishing material, which is quite logical, given its high performance characteristics. However, clinker does not differ in thermal efficiency, while its combination with insulation made it possible to obtain an even more effective material for interior and exterior decoration.
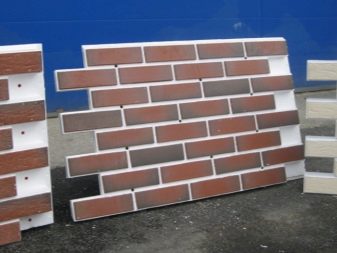
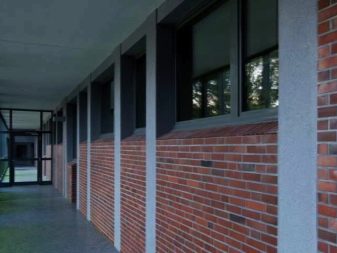
Thermal panels with a clinker surface have the following advantages:
- high strength indicators;
- long period of operation - up to 25-30 years;
- thermal efficiency of the material;
- improved performance of sound insulation;
- preservation of the color of the material due to the absence of dyes in the composition of the raw material - this or that shade provides certain types of clay and small changes in the technology of its baking;
- resistance to temperature extremes;
- biostability - mold, fungi and other forms of life of microorganisms do not appear on the surface of the material, rodents bypass it;
- environmental friendliness;
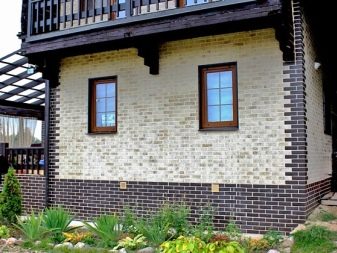
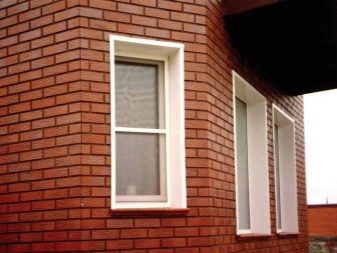
- ease of installation - insulation is carried out easier and faster due to the rejection of the alternate installation of insulation and cladding;
- versatility in use;
- the ability to hide small defects in the wall surface when choosing a curtain facade;
- attractive and respectable appearance;
- moisture resistance, vapor permeability;
- high rates of fire safety;
- frost resistance;
- weather resistance.
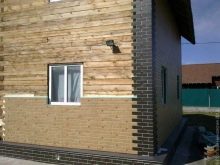

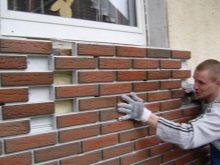
Unsurprisingly, a material with such impressive characteristics has a higher cost than many others.
Naming the shortcomings, professionals and ordinary users note the large weight of the material, therefore, it requires strengthening the facade and foundation, its fragility during transportation, installation and storage. Even falling from a small height, the clinker thermal panel can crack or burst.
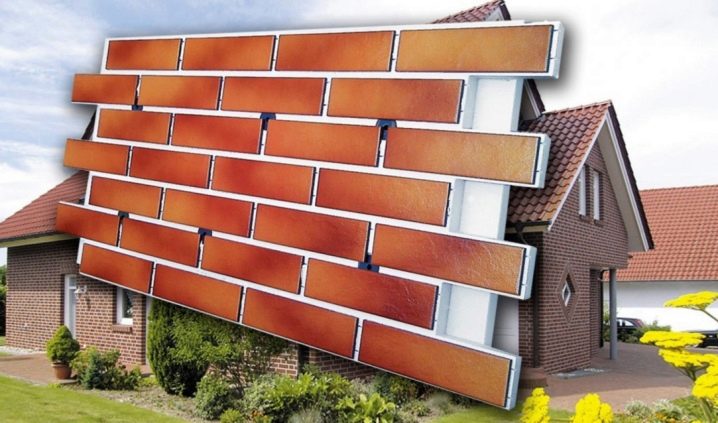
Specifications
Thanks to the technology of high-temperature air, it was possible to obtain a moisture-resistant clinker. Its water absorption rates are 2–4%. This, in turn, has a beneficial effect on the frost resistance of the thermal panel. It can withstand up to 150 freeze and thaw cycles (this amount is enough for 60-70 years of operation) without changing its technical characteristics. The insulation is also characterized by low moisture absorption, which is equal to - 0.5-1%.
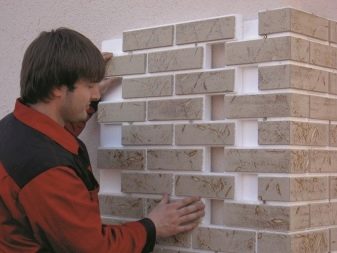
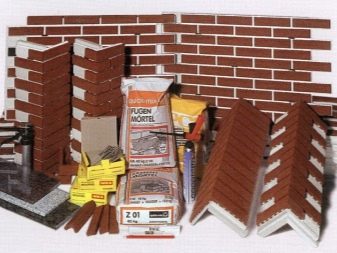
The strength figures are also quite impressive, averaging 3 kg / cm². This means that you will need to apply a force of at least 10 kg in order to tear off at least one element of the thermal panel from the wall. In practice, an attempt to divide the thermal panel into layers ends in the worst case in the destruction of the panel, but not in its division into layers.
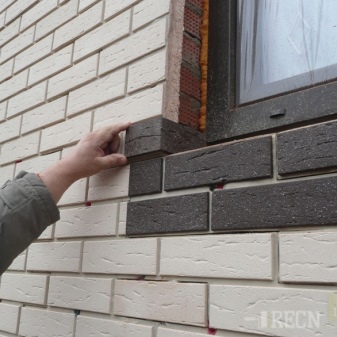

All types of thermal panels belong to the G-1 class, that is, they are materials that do not support combustion. A feature of polyurethane foam and polystyrene foam is its instability to UV exposure. Under the influence of sunlight, the upper polymer layer of the insulation is destroyed, which causes a violation of the strength of the material. The use of a protective layer of mineral chips or wood chips in some way neutralizes this disadvantage. However, proper transportation and storage of the material will help prevent the destruction of the insulation.
It should be transported and stored in packaging; it is important to protect open packages with clinker thermal panels from sunlight.
Clinker panels can be of various sizes. There is no single standard governing size requirements. The most widespread are slabs 113x65 cm, as the most convenient in installation. The weight of the material ranges from 10-23 kg and depends on the thickness. Facade clinker panels are usually larger and thinner, while basement panels are smaller but thicker.
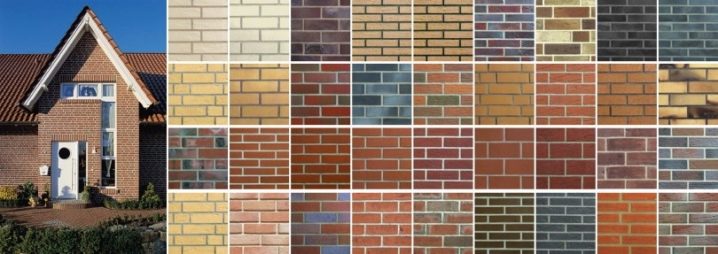
Installation rules
The first step is to calculate the required number of panels. To do this, you need to find out the area of the facade (multiply its length by width), as well as the sum of the areas of all door and window openings. Further, the second is subtracted from the first value. The result is the area provided for the cladding.
Knowing the dimensions of the tiles, it will be possible to easily calculate how many pieces are required for a 1 m² cladding. Usually, this information even contains instructions for the material. The resulting number of tiles for one m² can only be multiplied by the number of m² to be finished. If you get a fractional number, round it up. In addition, we must not forget that a stock is needed - usually this is another 7-15% of the total material.
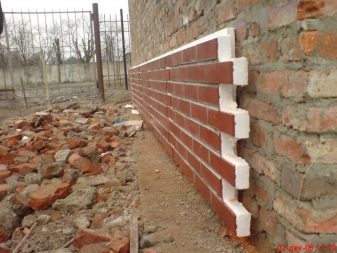
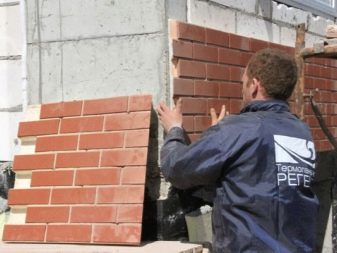
The cladding of the house should begin with the preparation of the wall surfaces. They should be cleaned and leveled. If a hinged system is used, it is possible not to strive to eliminate all minor defects.
It is imperative to apply 2-3 layers of primer on the surface, which will protect the facade from moisture and microorganisms, and will also improve the adhesion of materials. Further, along the plinth, 20 cm below the floor level, an aluminum profile is mounted - this is a kind of start for the subsequent clinker rows. Begin laying the panels from the lower left corner, laying out a horizontal row.
The glue is applied both to the very surface of the walls and to the tiles. Spread the glue on the wall over an area slightly larger than the tile area. Glue should be applied to the tile from the wrong side, it is more convenient to do this with a notched trowel. Further, the panel is pressed against the wall, leveled and held for some time for better fixation.
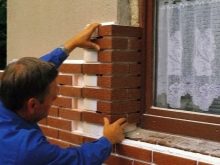
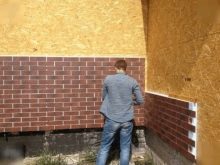
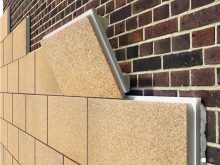
The material should not be stacked end-to-end, it is necessary to maintain a small gap between the elements. This can be done using construction beacons. If it is absent, a steel rod with a circular cross-section with a diameter of 6-8 mm is suitable.
To decorate the corners, you can use special corner elements or fasten panels on each side of the corner, keeping the joint at the sharpest point of the corner... After the glue dries, all joints are sealed with a silicone-based compound. As the latter hardens, the seams are treated with grout. It must be moisture resistant and elastic. The shade of the grout is matched to the color of the panels to create the effect of a monolithic wall, or a tone darker or lighter than the shade of the base material, then a very realistic imitation of brickwork is obtained.
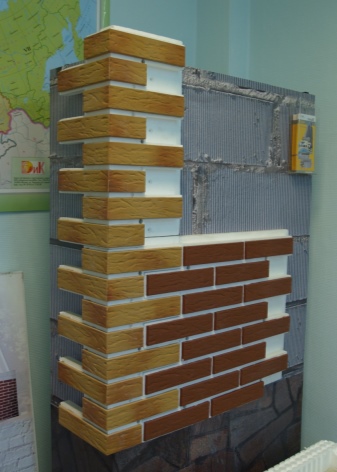
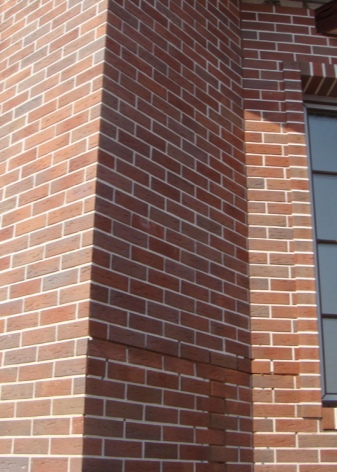
The installation of the hinged system is carried out in a slightly different way.
- A subsystem is mounted on prepared surfaces made of metal profiles or wooden logs.
- Metal elements must have anti-corrosion protection, and the wooden surfaces of the crate must be impregnated with antiseptics and fire retardants. It is attached to the façade with dowels.
- Further, thermal panels are hung on the crate with the help of fasteners. In some cases, the wall under the crate is protected with a vapor-permeable film, for example, when laying panels on aerated concrete.
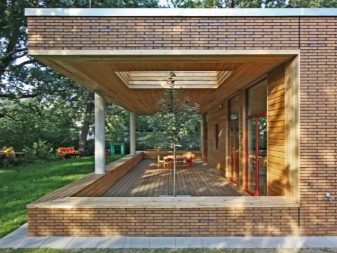
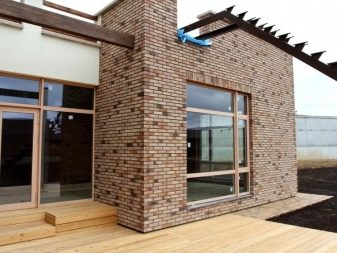
This is how ventilated facades are usually organized. Their characteristic feature is an air gap between the wall and the facing material.
An important point: when calculating the required amount of material for a hinged-type facade, you should calculate the area of the lathing, not the facade. If you neglect this rule, then the material may not be enough.
When working, situations cannot be avoided when the clinker panel needs to be cut. To do this, it is better to use two tools: for clinker - with a diamond disc, a layer of insulation - with a thermal knife. This will avoid cracking the tiles and the loss of insulation particles at the cut.
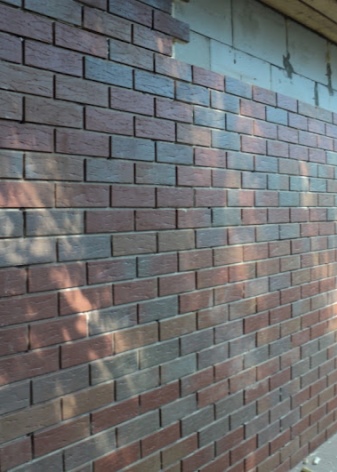
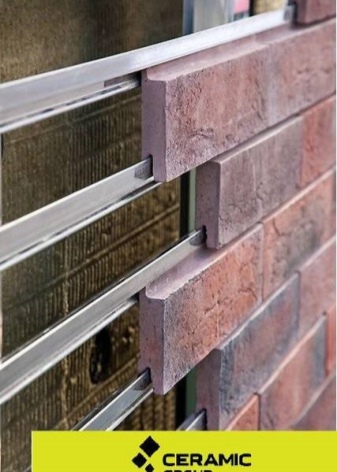
Manufacturers and reviews
There are many types of thermal panels on the market today. You should only trust well-known brands with a good reputation. Quality clinker has long been produced in Germany.
Today, clinker-coated thermal panels can be found in the products of the German companies Feldhaus Klinker, Stroeher, ABC. They are of the highest quality, almost without fail have a reinforcing layer and a fireproof coating. The latter guarantee the safety of products and their durability. Among the disadvantages is the high cost of production.
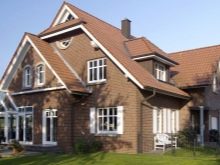
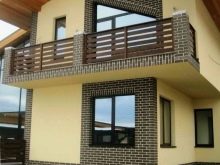
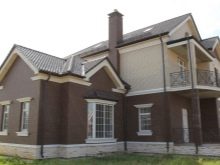
Polish panels are about 20% cheaper than their German counterparts. However, leading companies carry out production using German technologies. The result is more affordable products that are not inferior in quality to German ones. Przysucha and Cerrard are among the Polish brands of thermal panels that have been highly appreciated by users.
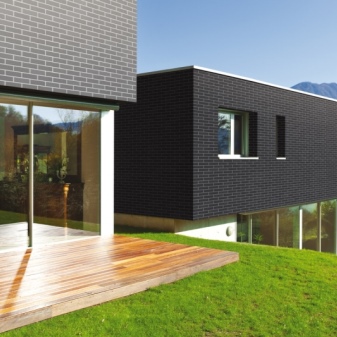
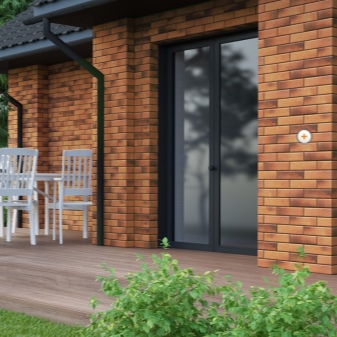
For a long time, there were no domestic manufacturers who produce quality products.Fortunately, the situation is starting to change today - decent clinker panels Now manufacturers from Russia are also offered by such companies as "Workshop of Facade Materials", Termosit, UMB and FTP-Europa... Demonstrating good quality, these panels are 20-30% cheaper than European products.
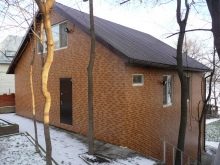
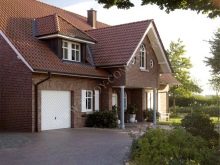
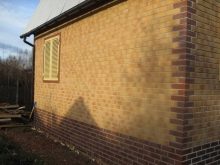
Boards based on polyurethane foam usually have a higher cost than counterparts with expanded polystyrene. This is due to the best thermal insulation properties of polyurethane foam, the best indicators of environmental friendliness and fire resistance.
For information on how to install front thermal panels, see the video below.
Our house outside the city turned out to be just wonderful. Well insulated with clinker thermal panels and looks pretty. For the money, it turned out fine and good, that everything is quick and simple, you can do it on your own. Of course, the house has become warmer and now there is no dampness in the corners.
The comment was sent successfully.