Features of chemical anchors for concrete
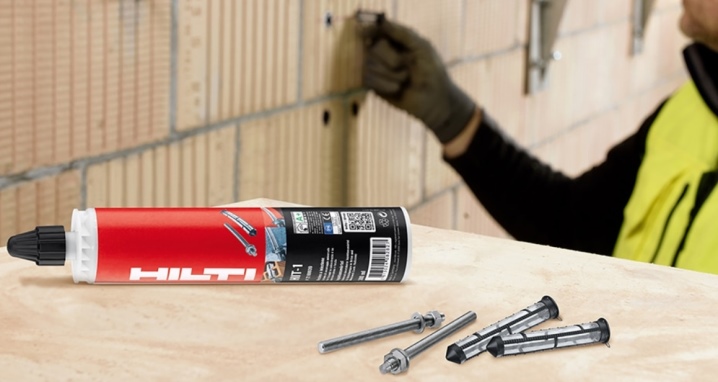
You can ensure the reliability of building installations using a chemical anchor. This type of fastener has settled on the Russian market not so long ago. Due to the strength of fasteners and the strength of adhesion in the interaction of solids and liquids, the fastening becomes many times more reliable than when using conventional anchoring connections.
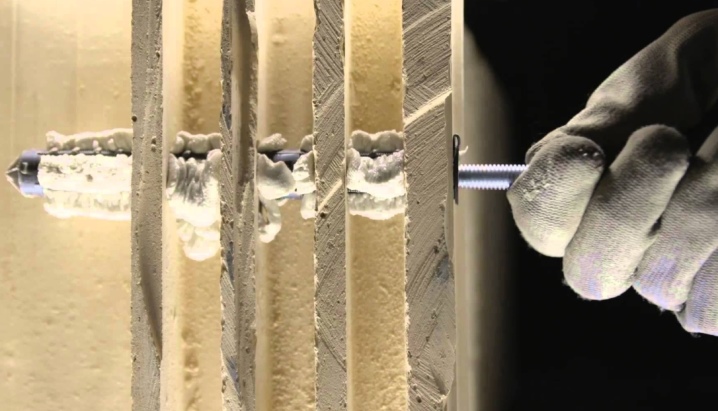
What it is?
Adhesive anchor, liquid dowel, injection mass - all these definitions of a chemical anchor are used in the simple language of workers. Fastener consisting of a conventional reinforcing bar or having an external thread, a sleeve with a helical surface inside and a special adhesive (made of synthetic resin), called a chemical anchor.
For the first time, this type of fastening system was used in the mining industry - with its help, it was possible to mount various fasteners to loose foundations. Later, anchors became popular in construction. Chemical materials provide reliable anchoring unlike traditional anchors.
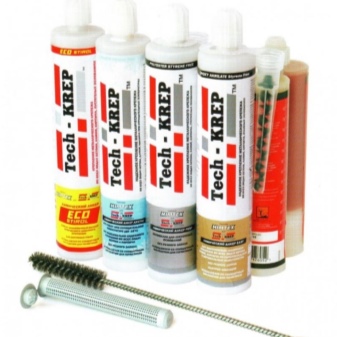
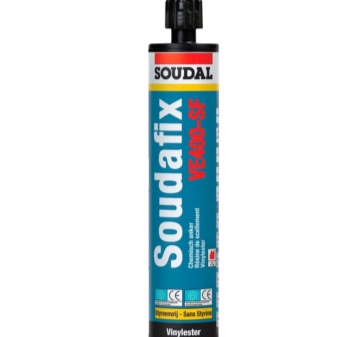
Chemical anchors are a complete and sophisticated system that includes additional drilling tools, mixing guns, precision dispensers, scrapers and brushes for surface cleaning and others. The adhesive composition is selected individually, taking into account the installation conditions and the base material. Most often, a chemical anchor is used for plain or porous concrete, for brick structures, for sandstone or limestone. The mass penetrates into the base, into its pores and cracks, the synthetic components harden - and a reliable monolith is formed, which holds the part.
Liquid dowels are indispensable for very high and pulling loads, can be used for the construction of balconies, bridges, canopies at the entrances to buildings.
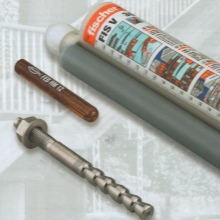

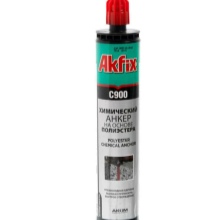
Advantages and disadvantages
The characteristics of chemical fasteners show high reliability of joints, the operation of which is accompanied by static, dynamic and vibration loads. The tensile strength is 2.5 times higher than that of conventional anchor bolts. Like all materials in construction, the bonded anchor has its pros and cons.
There are quite a few positive aspects.
- After installation, the hole is sealed and becomes airtight.
- The scope is very wide.
- For installation, the master does not require special training and experience - installation is as simple as possible.
- After the adhesive has hardened, the strength of the fastener increases.
- The load-bearing capacity is increased, that is, the anchor withstands tensile moments and breaking load.
- High resistance to external aggressive environment. Resistant to corrosion and chemical attack.
- There are specially formulated compounds for work in high humidity conditions, as well as for structures mounted under water.
- Capitality and durability. The service life can be at least 50 years.
- Environmental friendliness. Manufacturing plants produce compounds suitable not only for external, but also for internal work.
- Chemical anchors are not affected by high temperature fluctuations. Thermal expansion corresponds to the coefficient of expansion of the material where the fastener was installed.
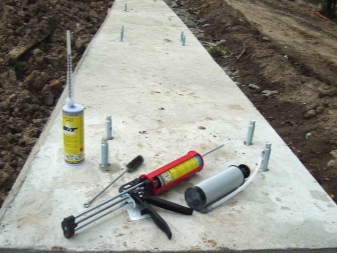
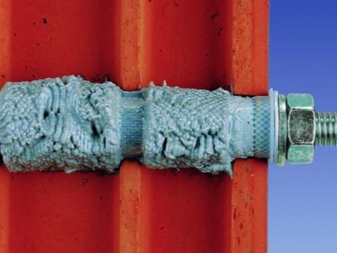
To avoid any troubles during work, do not forget about the negative aspects.
- The curing period of the adhesive is directly dependent on the air temperature.At + 20 ° С, this is 25-40 minutes, at + 5 ° С - 5.5-6 hours, if the temperature is even lower, then polymerization will take up to several days.
- Short shelf life. Unopened packaging must be used within a year. If the cartridge is opened, then it must be used immediately, since liquid anchors are not stored in the open form at all.
- The high price of fasteners - this repels many buyers.
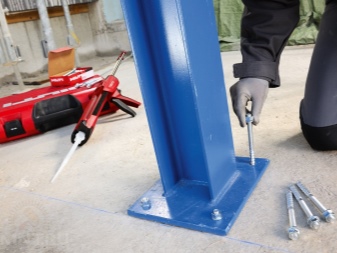
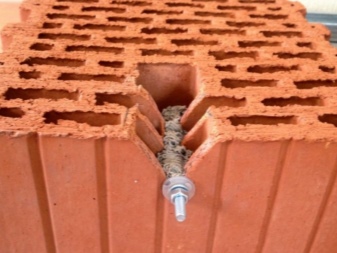
Species overview
Manufacturers usually do not disclose the proportions of elements in the composition of liquid chemical anchors. But what components are included in the adhesive mixture remains open:
- products of the chemical industry in the form of high-molecular compounds obtained by a polycondensation or polymerization reaction - in other words, synthetic resins;
- quartz sand is a free-flowing mineral mixture of natural origin, which consists of 95% silicon oxide;
- cement - is used as an additional binding element, thanks to which the adhesive mass gets its high-strength characteristics;
- the component due to which curing occurs is a hardener.
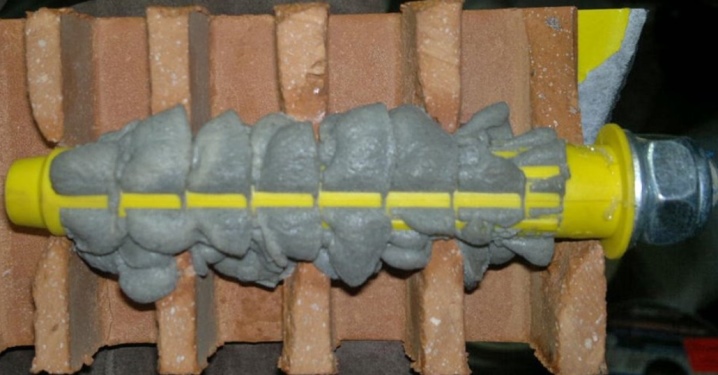
Ampoule
This type is used strictly for holes of a certain diameter. There is one ampoule for each hole. Ampoule anchors are mainly used for fixing bases, holes in which can be drilled with high precision and cleanliness.
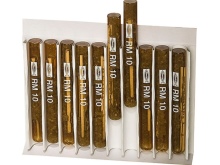
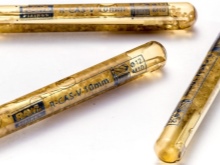
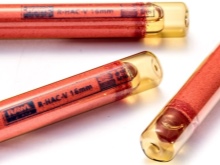
Injectable or capsule
More convenient, since the level of filling of the hole does not need to be controlled. The difference in diameters will not lead to inconvenience, because the adhesive mass tends to expand during hardening.
The packaging is made in the form of a pair of capsules - with an adhesive and a hardener. This type is not suitable for working with vertical surfaces, since the composition will flow out without having time to harden. Injection anchors can be of 2 types.
- With two cartridges of different volumes, the compositions of which are mixed at the exit. A special gun is required to ensure that the two components are fed evenly. There is a spiral inside the mixer spout, thanks to which the compositions are mixed even before they exit.
- With one cartridge. There are also 2 components that are in one tube, but separated by a special partition. Mixing takes place in the same way in the mixer spout. You can use it with a traditional syringe gun.

Capsule mechanisms are more versatile and popular in the modern market. This is because no calculations are needed to determine the required number of capsules. They are convenient for filling cone-shaped holes, that is, those that expand in depth.
Rebar or stud anchors have a thick consistency. An important role is played by anti-corrosion components and deoxidizers contained in the composition.
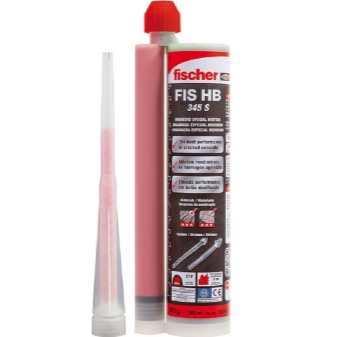

What to consider when choosing?
When choosing a liquid anchor, there are several points to consider:
- dimension - base thickness, part length and diameter;
- the position in which the installation will take place, that is, in vertical, horizontal or on the ceiling;
- load on the anchor;
- where the fasteners will be located;
- the material from which the base is made;
- humidity and temperature of the environment;
- the rate of curing of the adhesive mass.
Manufacturing plants usually indicate all these parameters on the packaging or in the accompanying instructions.
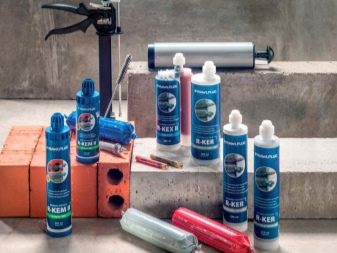
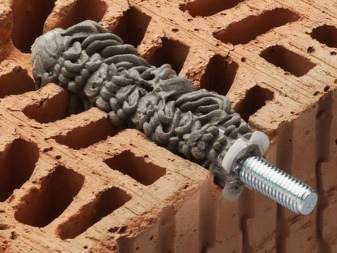
How to use?
Before installing an anchor, which belongs to chemistry, you need to carefully study the instructions for use. This allows you to take into account all the necessary nuances, for example, calculate the installation scheme and much more.
The first stage is the preparation of the borehole. On the basis, notes are made in the places where the fasteners will be mounted. Then a hole is drilled with a drill a maximum of 2 millimeters wider than the diameter of the stud. You need to hold the drill in a perpendicular position relative to the surface.The depth of the hole can be controlled with special stops, or by marking a mark on the drill. For future fasteners to be reliable, the hole must be cleaned of dust and dirt. The procedure is carried out using a special brush and a manual or construction vacuum cleaner - it all depends on the amount of work performed.
The second stage is the introduction of the adhesive mass. A nozzle is installed on the cartridge, and the whole structure is inserted into a special gun. First, squeeze out a small amount of the chemical composition, about 10 centimeters, to make sure that all the components are mixed evenly - you do not need to use them. The mixer spout is placed in the hole, then by pressing the trigger button of the gun, the mixture consumption is controlled. The veneer is filled to about 2/3 of its volume.
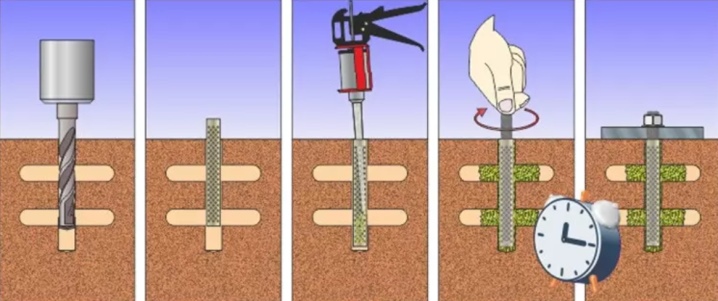
The third stage is the installation of a metal rod. To distribute the adhesive evenly inside the hole, the fasteners can be “pulled out” a little and then screwed in to the end. While the adhesive hardens, the position of the anchor can be controlled. It is possible to determine whether the mass has filled the hole or not by its appearance - if the glue comes out, it means that the installation is airtight.
The final step is to install and tighten the nut. After the solution has completely hardened, all materials and elements can be fixed. Tighten the nut with a torque wrench. Manufacturers in their recommendations indicate what maximum force should be applied when tightening the nut. It is not recommended to use a traditional key, as there is a risk of exceeding the force and deteriorating the material.
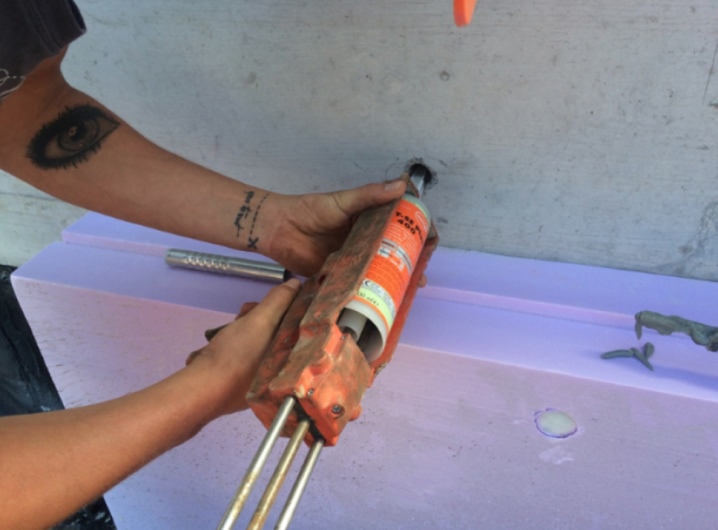
If there are breaks during installation, the mixer spout is not removed from the cartridge, but before continuing work it is changed to a new one.
Some builders are engaged in the preparation of the solution on their own. For this, epoxy resin, hardeners (UP-583), cement or gypsum mortar and a plasticizing agent (DBP or DEG-1) are mixed. The resulting mixture is thoroughly kneaded. It is best to mix the solution in small quantities, then use immediately.
The main advantages of a homemade anchor are small shrinkage, high strength and wear resistance, the ability to mount at different temperatures from -9 ° C to + 35 ° C. The mixture hardens within 2 hours.
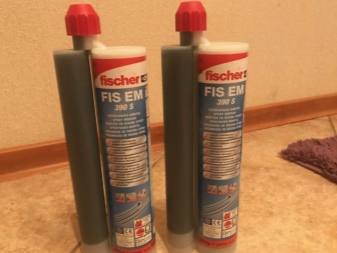
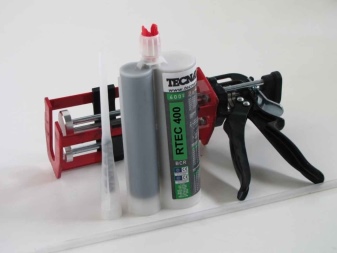
The following video describes the installation of chemical anchors.
The comment was sent successfully.