What is mortar and where is it used?
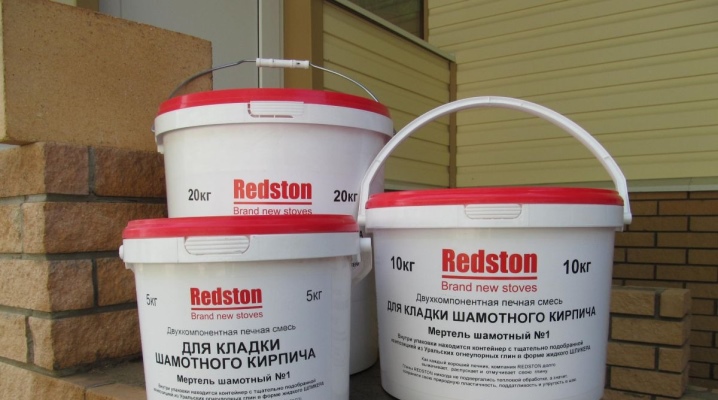
When laying a furnace or fireplace, as well as for the purpose of protecting blast furnaces or steel-pouring ladles, not only refractory bricks are used, but also fireclay fire-resistant mortar. A heat-resistant masonry mixture is made of such a material, which not only reliably fixes all structural elements to each other, but also acts as a sealing compound that does not lose its functions even at very high temperature conditions.
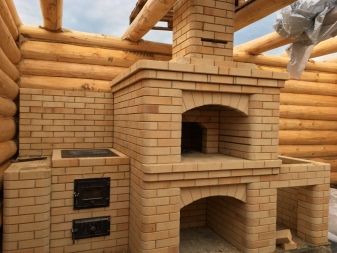
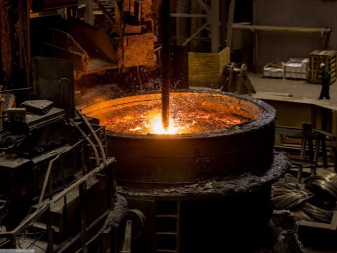
What it is?
Mortar is a material that belongs to the class of refractory, its production is carried out in the factory. The production of the material consists in preparing a dry mixture of kaolin and chamotte powder in a 1: 1 ratio.
Kaolin is a special type of clay with a refractory composition; to prepare a mixture, the clay is dried and crushed.
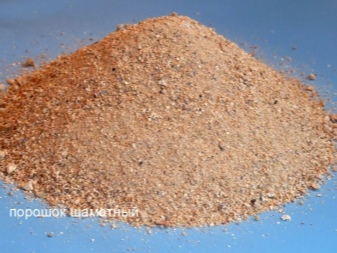
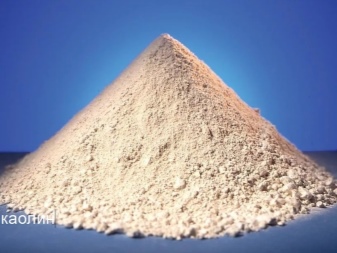
The finished mortar has the form of a fine powder of a grayish-brown or reddish-brown hue. The powder should consist of components with equal size fractions. The presence of caked lumps in the mortar is considered a marriage. Depending on the size of the fractions, fireclay powder is divided into types.
- Coarse-grained - the particle size of the mixture is in the range of 2-2.8 mm. This material consists of 75% chamotte and 25% additives.

- Medium-grained - the particle size of the mixture is 1-2 mm. The mixture contains 80% chamotte and 20% clay.
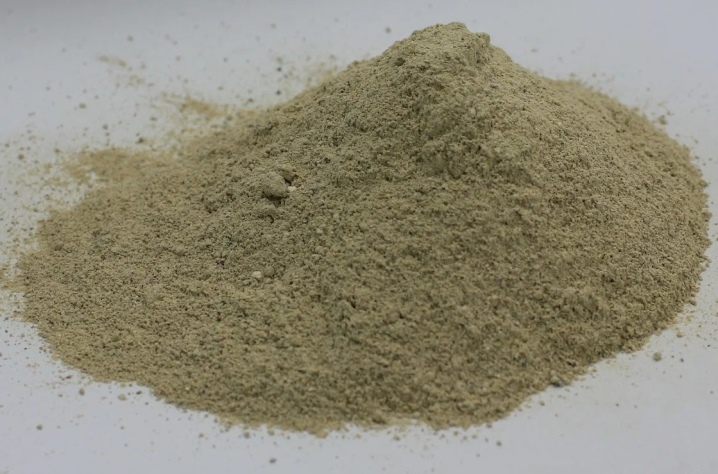
- Fine-grained - the particle size of the mixture is in the range of 0.24-1 mm. The mixture contains 85% chamotte powder and 15% kaolin clay.
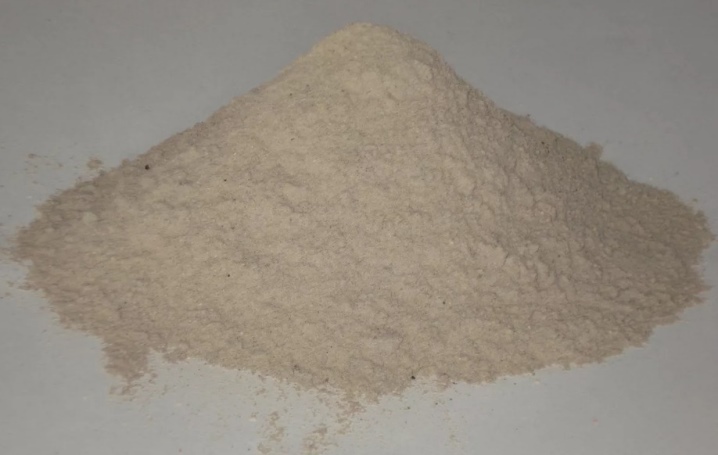
A mortar solution is prepared by combining the dry composition with water. Its qualities - heat resistance and fire resistance - are used for laying the furnace and internal coating of its surfaces. Manufacturers pack the mortar into 50 kg bags, less often 25 kg bags. The main requirement for the product is its absolute dryness, since the composition tends to lose its properties under the influence of moisture.
The mortar powder is highly fire-resistant and can withstand temperatures up to 1750 ° C. This high-temperature resistance implies the use of this material for protective and insulating purposes when surfaces are exposed to hot air-gas mixtures and open flames.
Mortar powder, combined with a certain amount of water, forms a working mixture that has the same properties as refractory bricks. The composition expands when heated, a reliable ceramic film is obtained on its surface, which seals the seams of the oven masonry, thereby protecting them from high-temperature effects.
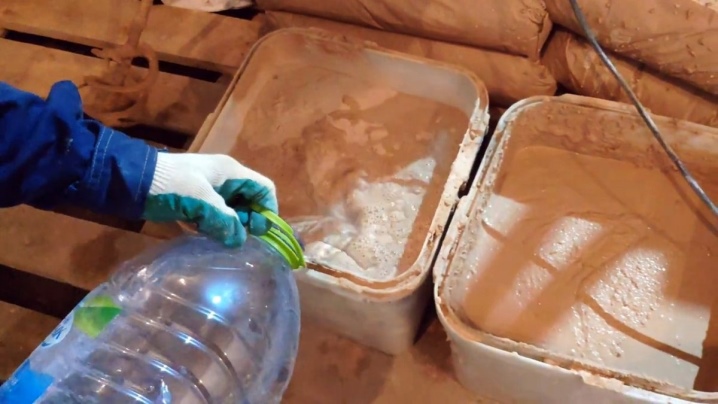
Overview of types of mixtures
Refractory mortar from mortar is subdivided into various types that have certain physical and chemical characteristics. The correct selection of refractory masonry composition can guarantee the protection of residential and other buildings in which a stove or fireplace is installed from fire. In addition, high-alumina and high-plastic mortar composition is used not only for laying furnaces, but also for industrial purposes when firing various types of workpieces. The mortar is classified according to the following main criteria.
By composition
Depending on the composition, mortar mixtures are as follows.
- Periclase mortar, brand MPSF - is made on the basis of periclase powders, where phosphate components act as binding components.Such a mixture is used to seal the seams of the furnace masonry and is part of the lining in the manufacture of refractory products.
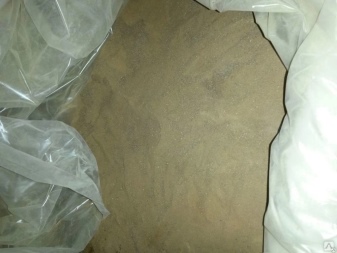
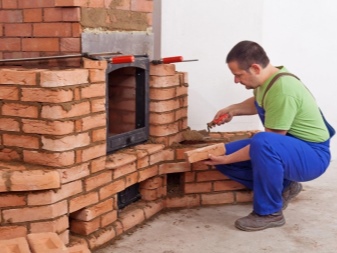
- Magnesian mortar - the mixture is based on magnesium oxide and its dioxides. This type of mortar is used in steelmaking when arranging the arch of furnaces for melting metal.
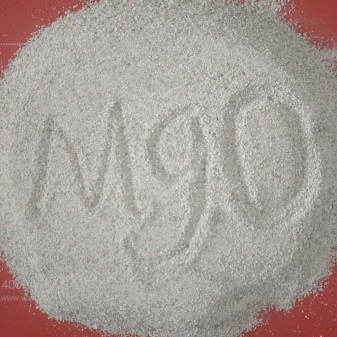
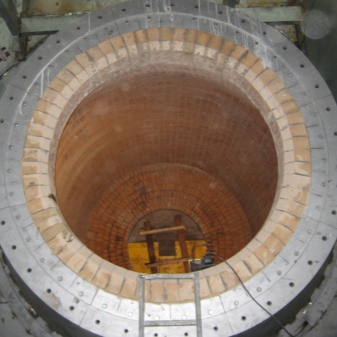
- Mullite mortar - in the composition of the mixture, a mineral is used, which is called mullite, consisting of the elements aluminum, iron and silicon. This type of mixture is used to protect steel-pouring ladles.
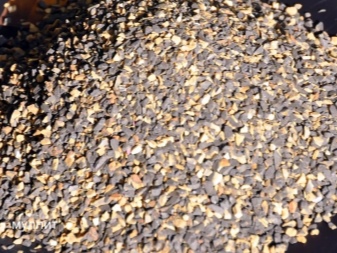
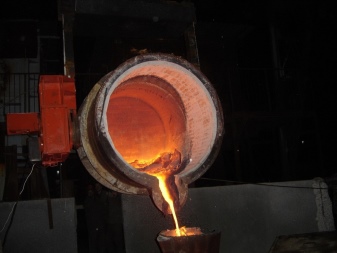
- Mullite corundum mortar - manufactured using corundum component and sodium polyphosphate. Corundum, as a mineral, has a hardness comparable to diamond, and in its composition corundum is one of the varieties of aluminum oxide.
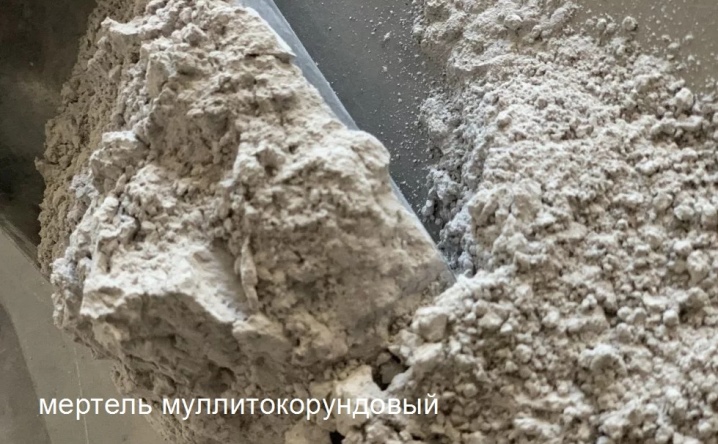
- Cordierite mortar - contains in its composition kaolin, alumina, quartz, feldspar, talc. Cordierite powder has a low coefficient of expansion when heated and does not crack when rapidly cooled. It is used in the manufacture of refractory products, filters.
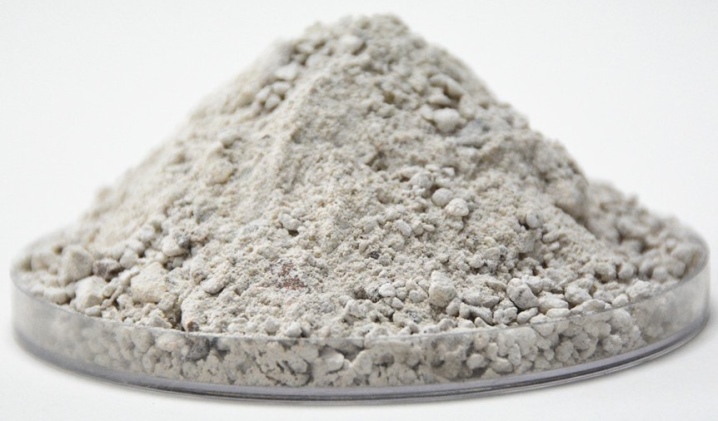
- Zircon mortar - the mixture contains zirconium oxide. This type of metal is fire resistant, therefore the mixtures are used in the steel industry.
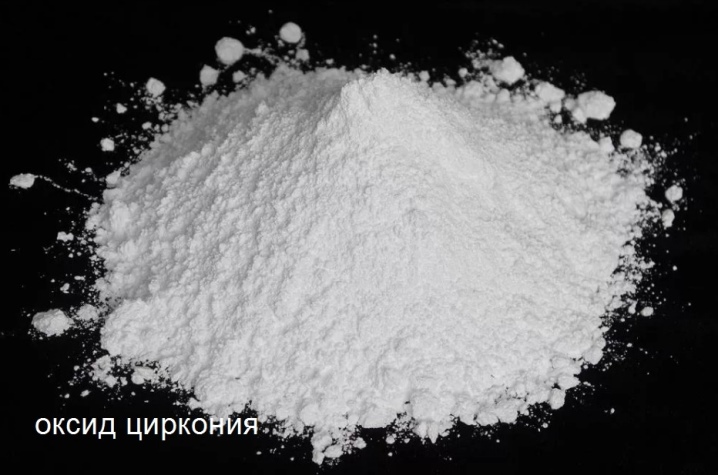
- Nitride mortar - the mixture contains silicon nitride. The heat-resistant properties of nitride mortar are used in the metal smelting and waste incineration industries.
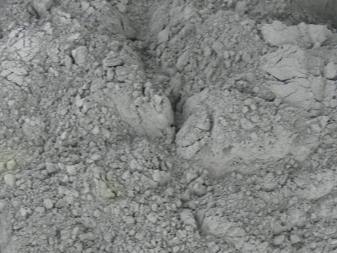
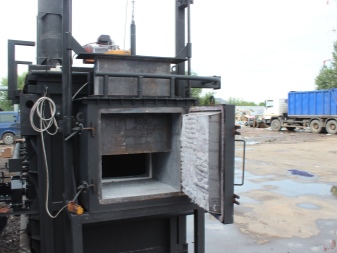
- Oxide mortar - contains oxides of such metals as beryllium, cerium, thorium. Mortar mixtures of this type are used for the nuclear industry.
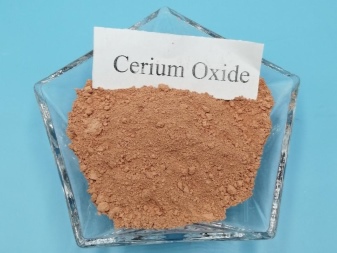
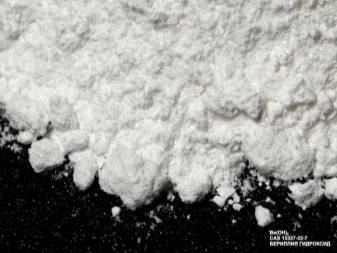
All types of mortars are available in the form of free-flowing mixtures. An exception is the oxide mortar, which is produced in a pasty form.
By brands
All dead bulk mass is marked in a certain way, depending on its composition and properties. For example, the letter part of the marking contains the components of the composition, and the numbers indicate the percentage of aluminum oxides in the mixture. The following types of mortar are distinguished by brands:
- MP-18 - semi-acidic mortar mixture containing at least 20% aluminum oxide;
- MSh-28 - fireclay mortar with an aluminum oxide content of 28%;
- MSh-31 - fireclay mortar with an aluminum oxide content of up to 31%;
- MSh-32 - fireclay mortar with an aluminum oxide content of up to 32%;
- MSh-36 - fireclay mortar with an aluminum oxide content of up to 36%;
- MSh-39 - fireclay mortar with an aluminum oxide content of up to 39%;
- MShB-35 - chamotte mortar with bauxite, containing 35% of aluminum oxides and ore of the same name in the form of bauxite;
- MMKRB-52 - a mixture of mullite-silica with the addition of bauxite and a content of 52% aluminum oxides;
- MMKRB-60 - a mixture of mullite-silica with the addition of bauxite and a content of 60% aluminum oxides;
- MML-62 is a mullite mixture without impurities, containing 62% of aluminum oxides;
- MMK-72 - mullite-corundum mortar containing 72% aluminum oxide;
- MMK-77 - mullite-corundum mortar containing 77% aluminum oxide;
- MMK-85 - mullite-corundum mortar containing 85% aluminum oxide;
- MKBK-75 - a mixture of mullite-silica with the addition of bauxite and a content of 75% aluminum oxides;
- ММКФ-85 - a mixture of mullite-corundum, in the form of a binder-base, it uses phosphates, contains 85% of aluminum oxide;
- MC-94 is a zirconium mortar, a special mixture consisting of finely ground mortar powder and zirconium, intended for refractory masonry of heat-resistant elements.
Mortar compositions correspond to GOST 6137-37, but some of them can be produced according to the TU regulations.
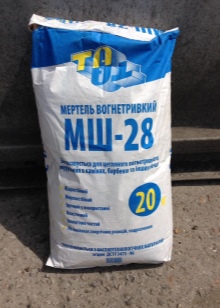
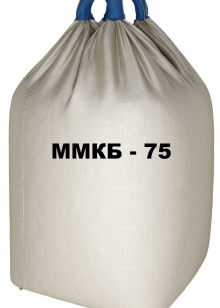
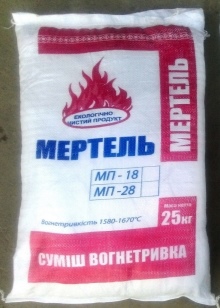
Applications
Mortar mixtures are used to perform masonry work when installing furnaces and other similar structures such as a blast furnace, a ladle for pouring steel, in coke ovens or air heaters. Open-hearth steel-making furnaces, mixers, crucibles and so on are subjected to grating. For surface treatment, solutions of a given consistency are prepared directly on site before starting work. Some types of mortar can remain diluted for a certain amount of time and can be used without fear of losing their fire retardant properties.
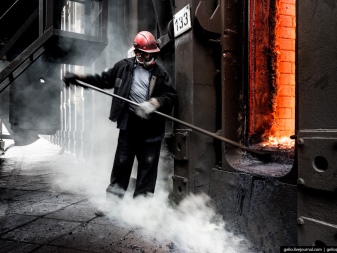
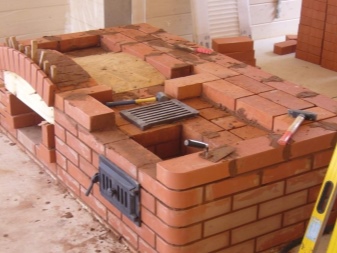
How to use?
In order to breed mortar, certain knowledge and skills are not required - the method of preparing the mixture is quite simple. The instructions for performing the work are as follows.
- First, you need to prepare and clean the workplace from foreign debris. In addition, all unnecessary items and tools are removed from the work area.
- You will need to prepare a capacious container for mixing the composition, while in advance you need to prepare all the tools - a mixer for stirring, a spatula, clean water for diluting the composition.
- Before laying, the bricks must be cleaned of dirt, dust, or, if the brick was in use, it will be necessary to carefully remove the remnants of the old composition from it. In addition, it is important to remove carbon deposits and soot deposits from brick surfaces.
- Work on the dilution of dry fine powder must be carried out in a protective respirator and goggles so as not to inhale the dust from the composition, since its components are harmful to human health. Hands will need to be covered with protective gloves.
All actions related to the preparation of the mortar mixture are carried out in a room with good ventilation, but drafts should be avoided so that the dry mixture is not scattered over the surfaces by gusts of air masses.
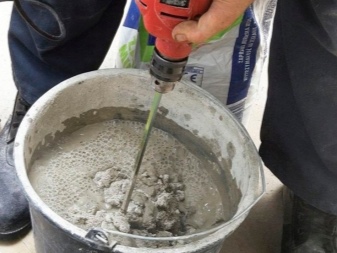
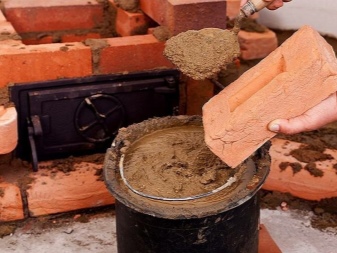
Working mortar mixtures are divided into 3 types depending on their density, that is, the degree of dilution of dry powder with water:
- liquid consistency - it turns out when 13-13.5 liters of water are added to 20 kg of powder;
- semi-thick consistency - obtained by mixing 20 kg of powder with the addition of 11.5-12 liters of water;
- thick consistency - such a solution is prepared at the rate of 20 kg of the mixture and 8-8.5 liters of water.
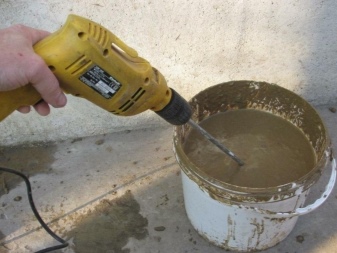
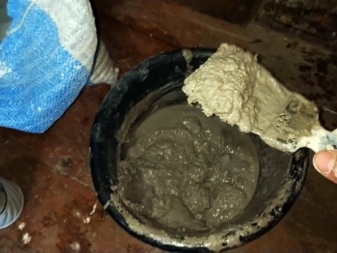
Liquid and semi-thick compositions are used when it is necessary to make sealing joints of the masonry, the thickness of which does not exceed 3 mm. If a seam with a thickness exceeding 3 mm is required, then only formulations with a thick consistency are used for them. The thickness of the joints in the ceramic masonry is made from 3 mm, while the refractory masonry allows for thinner joints. The process of preparing the mortar is as follows:
- take a container of the required volume and pour dry mortar into it;
- water (clean, without impurities and inclusions) is added to the powder in small portions, in stages;
- when adding new portions of water, the mortar powder is mixed well with a mixer for construction work or a drill with a special attachment is used;
- when mixing the composition, it is important to achieve a homogeneous mass in which lumps of any size are completely absent;
- after adding a small portion of water and thoroughly mixing the mixture, the resulting composition is left to stand for about 25-30 minutes, after which its consistency is determined and, if necessary, a new small portion of water is added, thus bringing the entire mass to the desired condition.
A well-prepared working mixture of mortar powder will be able to ensure reliable adhesion of all elements of the oven masonry and seal the seams. The consumption for 100 bricks will on average be 2-3 buckets of the finished composition, but this amount is very conditional, since it directly depends on the consistency of the solution.
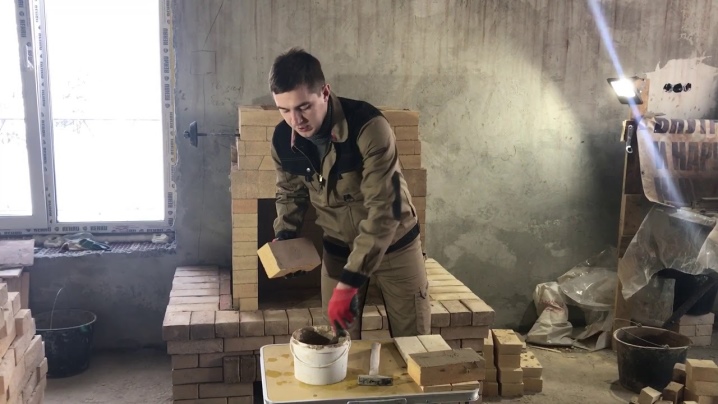
The comment was sent successfully.