Everything you need to know about wood laser cutting machines
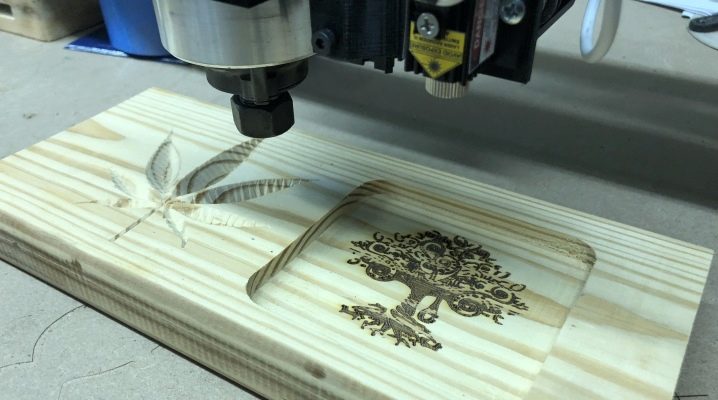
Laser cutting machines for wood are equipment designed not only for true professionals. It allows you to get involved in artistic burning not only by hand, but also using computer technology.
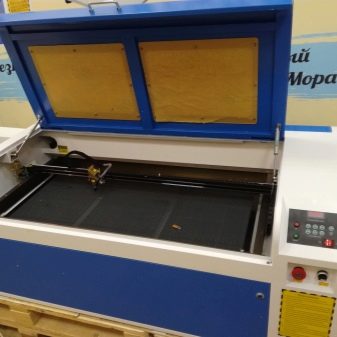
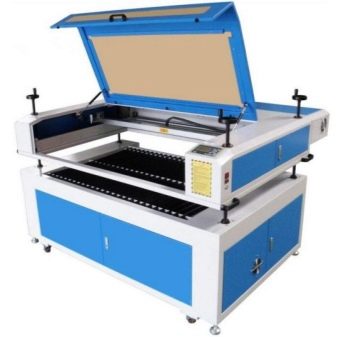
Device and principle of operation
The device of a machine tool with numerical control includes the following components: a frame with a horizontal working table, a movable platform with tools. The last component is located above the originally named one. The working surface is equipped with a laser gun. It is included with the laser unit. Lenses and mirror surfaces that re-reflect and redirect the flow are components of the optical system.
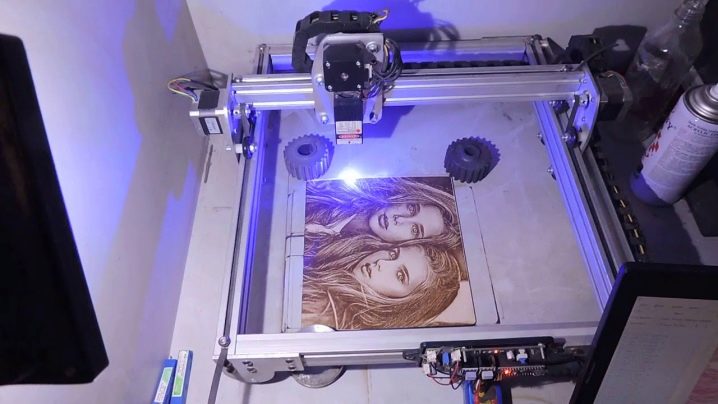
The laser machine for cutting wood is complemented by a stepper motor that allows the laser gun to move to the desired coordinates on the sheet or block of wood being processed.
The laser gun is controlled by a computer program that works with the workpiece image loaded into the memory of the on-board computer.
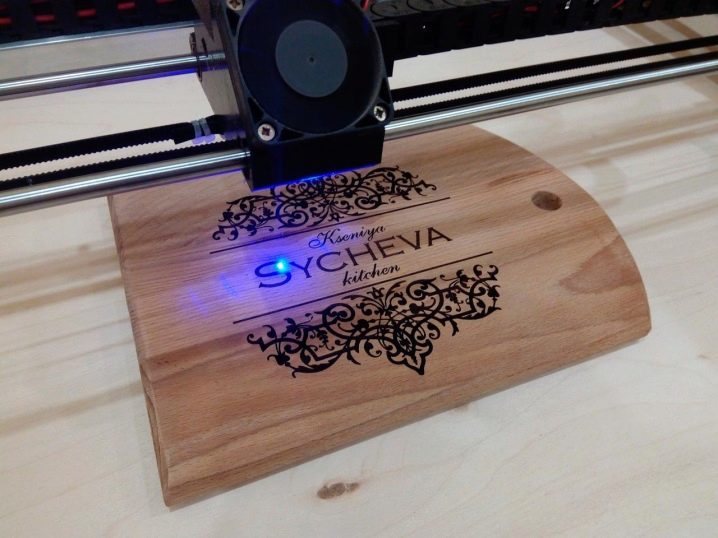
The algorithm of the laser machine is as follows.
- A mixture of nitrogen, helium and carbon dioxide is fed into the laser tube.
- With the help of a special transformer, the mains voltage of 220 volts is converted to the nominal value that is necessary for the correct and uninterrupted operation of the laser system.
- Laser beams are focused using mirrors and lenses. As a result, for example, a plywood sheet is processed with a laser head.
- The flowing or circulating water in the cooling circuit carries away with it a significant part of the heat, which is emitted by the laser gun. If a reliable heat removal system had not been placed in the laser system, the tube would not have worked for one minute without cooling, even in a pulsed mode.
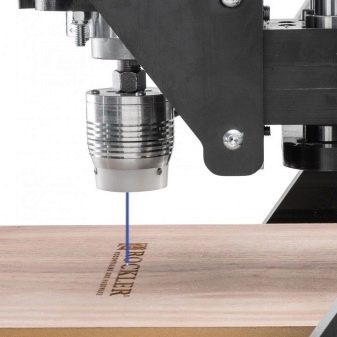

Full functioning will also require a current source, an active medium and an optical concentrator of the radiated energy. The laser beam has a highly concentrated potential.
Thanks to this property, it is able to penetrate into any material, causing it to melt and evaporate.
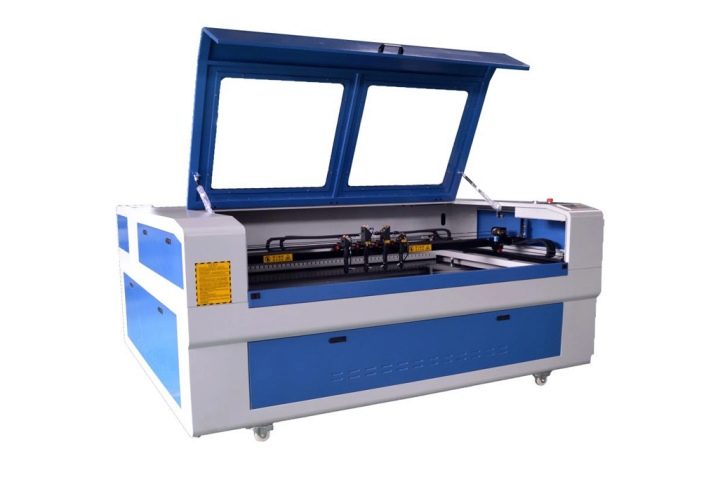
Species overview
All types of CNC machines have one important feature - they are automated. A manual woodburner, even equipped with a laser, cannot be considered a full-fledged machine. Laser units are mainly classified by size. Small models that do not have the most powerful laser tube are suitable for home use, while the low power consumption, not exceeding 400 watts, is not able to cope with the full flow of orders, since each of them would take much longer to complete.
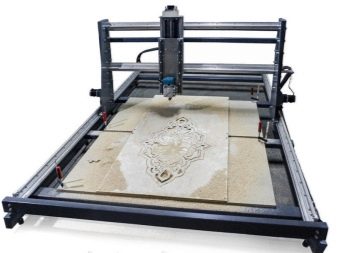
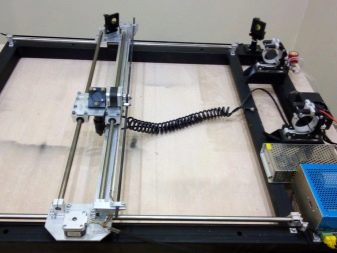
This power is active - constant, in terms of continuous consumption: as you know, the laser beam works in a pulsed mode, since if it was constant, the tube would quickly overheat and burn out. The flow of electrons has a lot of energy, which is not all converted into useful radiation.
For a home workshop, laser machines do not have a kilowatt (or more) power, since this is not required. It would not just burn wood, but melt and vaporize (turn into plasma) even granite and steel. The machine for working at home has a power consumption that starts from just a few watts - enough to light a match or burn wood.Any fuels and lubricants would ignite from a thin beam, the beam width of which reaches 25 microns, so you should always be careful with the laser. A mini desktop machine will take no more than 0.5 m2, given the small area of the workpieces that you are processing. More professional models will occupy a large table - or even two such tables can successfully fit on a workbench with an area of 1 * 2 m.
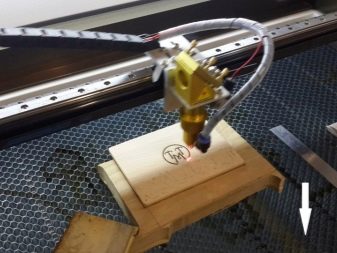
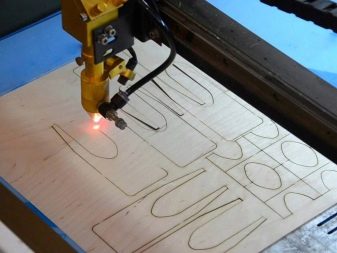
Popular models
Russian company Multicut, for example, issues machine model 3000 - under the order. They are used by woodworking enterprises, whose activities are related to wood processing, the production of furniture items and the manufacture of advertising and souvenir products. Model 3000 works with all wood materials, including composite (MDF), has an extended set of functions. The permitted and declared power of the three modifications of this model is 60, 80 and 150 W (power consumption from the network).
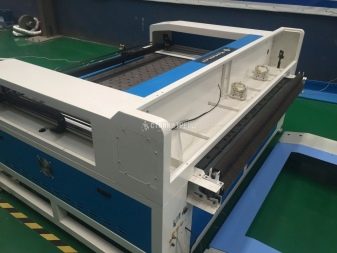
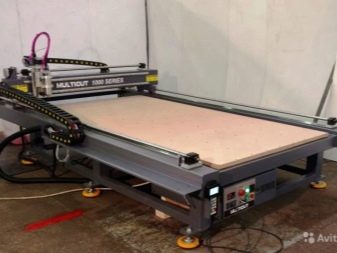
Rigging
The carbon dioxide laser allows cutting veneer, plywood, solid wood, and engraving materials. To do this, you need to choose a small power from tens of watts - it will allow processing any wood species and any materials from pressed and glued sawn timber. For processing of metals and their alloys, a power of more than 100 watts may be required.
Replacing the laser tube would require two reasons: either a spent resource, or replacing the old one with a more powerful one.
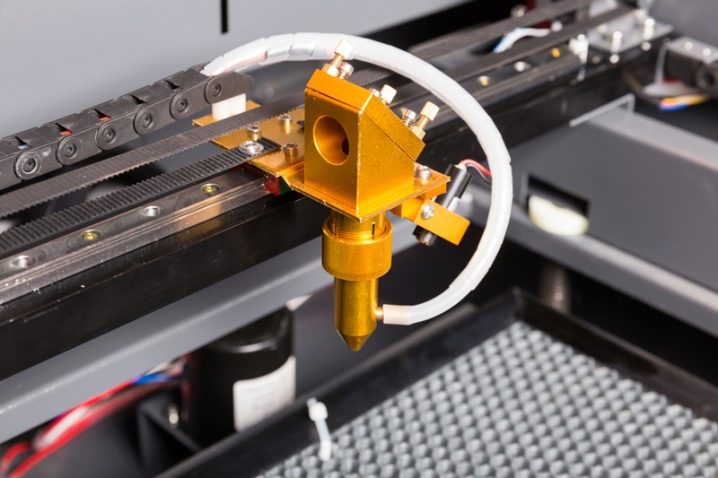
A mismatch in power with the laser starting module will lead to incomplete output of power or the impossibility of its operation initially.
The optical beam visible to the naked eye (through protective goggles) is concentrated on the workpiece being processed. The optics for its re-reflection and concentration in a narrow beam must be quite transparent, otherwise it will start to warm up and fail itself. The collecting lenses are made from zinc selenide and gallium arsenide. They are very fragile; in the process of careless movement of the machine to another place, they can be easily broken - just like the pipe itself. But they transmit 99% of the rays very well without retaining them in their thickness. Plain glass lenses already absorb a few percent of the laser energy, although tempered glass is used to produce them.
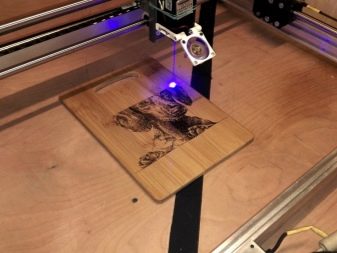
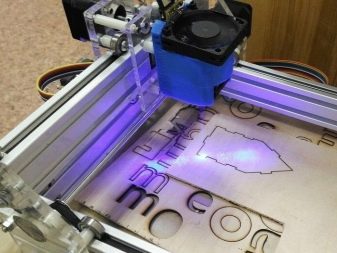
Long-focus lenses are suitable for woodworking, short-focus lenses are suitable for films and engraving, not burning. The focal length is 1-4 inches.
The format of the working table of the machine is 1.5 * 3 and 2 * 3 m. The thickness of the table top does not exceed 3 cm. The table cover is chosen such that the beam, when cutting the workpieces, does not spoil the surface of the working platform and does not create glare of the reflected laser radiation. Cutting out thin blanks allows you to use a table with mesh filling, which prevents the films from sagging and getting a curve cut. Series production machines are equipped with a conveyor line that allows material to be fed directly from the roll.
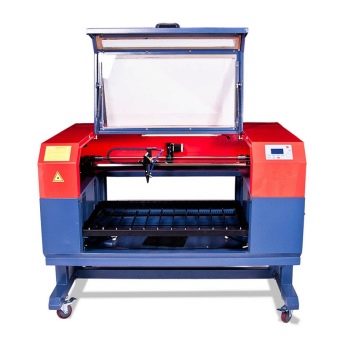
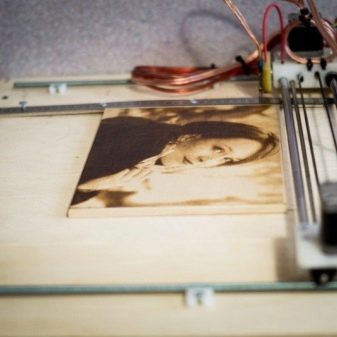
Secrets of choice
Make sure that the set includes protective ammunition, which always starts with glasses. Due to non-observance of safety precautions, inexperienced craftsmen partially lost their eyesight, having received a retinal burn with the reflected laser beams, not moving away to a safe distance and not turning away at the moments when the beam burned wood or melted / evaporated metal.
Decide how much power - and for what purpose - you need. The reserve of this power should be triple, and not "end-to-end", since the tube will work an order of magnitude longer at a much lower power. The optimal loading is 30 ... 35%. It is better to overpay a little once than to waste time on additional repairs.
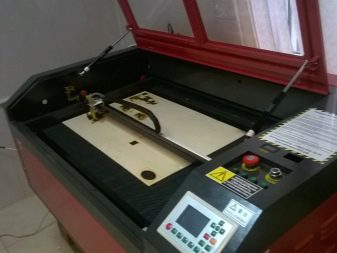
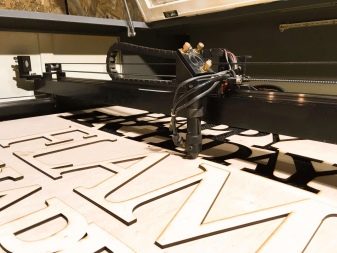
Make sure that the optics and tube are not damaged, and that the lenses and mirrors themselves are not cloudy or scratched. Used optics, clouded by an abundance of internal defects or massive scratches (this happens when reusing lenses and mirrors left over after repair), cannot fully transmit optical rays through themselves. Lenses and mirrors must be new.
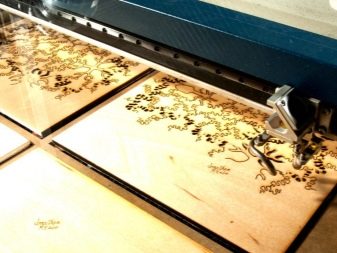
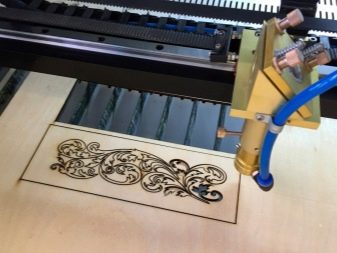
Possibilities
For cutting, cutting on a desktop machine, a large power is suitable - 150 W or more. For burning out, including delicate work performed in a residential building, a parameter of 60 ... 100 W is suitable. This applies not only to Multicut laser cutting machines, but also to other manufacturers. The scope of the laser machine is art and advertising, medicine and space technologies, mechanical engineering and any technical processing of materials, up to steel. The laser machine helps to make the same type of serial parts, simply "tracing" them in the process of CNC machining.
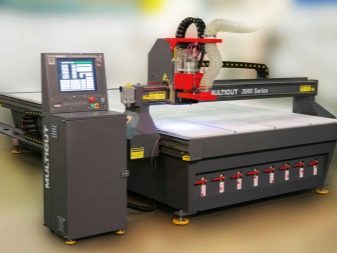
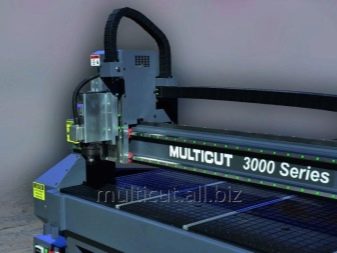
Material consumption for laser cutting and engraving with a laser is minimal, accuracy is one hundred percent, work is accelerated to any conceivable limit that can be imagined without going beyond the consumer characteristics of the equipment. Lasers work with material from 100 microns in thickness. The waste gas generated during the cutting is removed automatically from the system. If, when cutting blanks and manufacturing products, the gas is unnecessarily harmful (for example, phenol-formaldehyde, sulfur-containing vapors and other compounds), then the material is sent for milling / turning, and not laser processing, since this procedure is considered hazardous to the health of machine operators. On equipment with a laser, you can work with most metals and alloys (except for mercury and lead-containing compounds, radioactive materials), wood - but it is not recommended to cut and engrave plastic and rubber: the first is crumpled, the second sags and crumbles, while acrid and poisonous smoke is released. If you suspect the release of toxins, you should think about non-laser processing methods, in which heating of the material to hundreds of degrees is excluded - even with a high throughput of materials.

The comment was sent successfully.