Gypsum plaster: varieties and applications
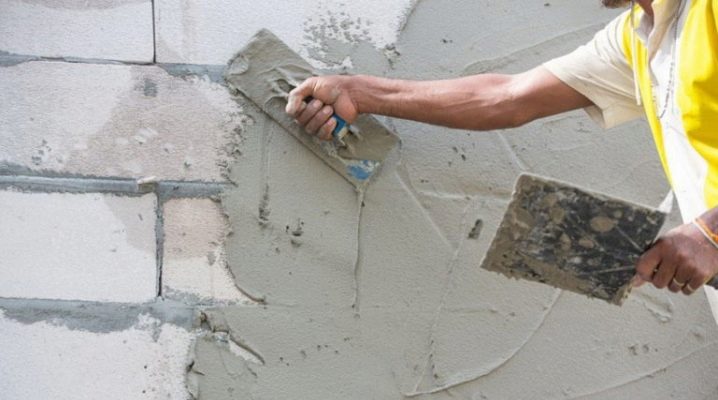
For decorative coating, it is often required to create a perfectly flat surface of walls and ceilings. Modern gypsum-based materials are especially popular among plaster mixes. Thanks to special admixtures, their scope of application is no longer limited to rooms with moderate humidity. Some types of gypsum plasters are suitable for use in bathrooms and building facades. And the possibility of their use as a decorative topcoat opens up new horizons for creativity.
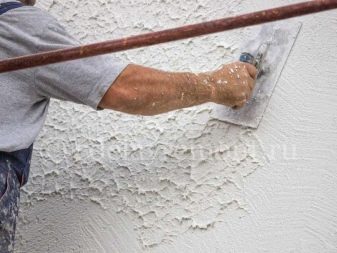
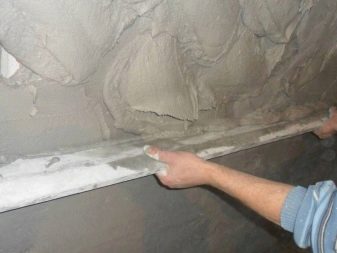
Peculiarities
Gypsum plaster is a modern finishing material that is used for applying both rough and final coatings. Basically, gypsum-based mixtures are recommended for interior decoration with low air humidity. But new technological additives and some additions to the process technology make it possible to use gypsum plasters in the bathroom, toilet or for outdoor use.
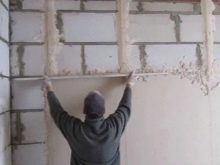

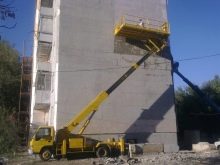
Such modifiers are free-flowing fillers with various sizes of fractions and polymer or mineral additives. They make the mortar lighter and more plastic, and also improve its adhesion to various surfaces. The gypsum component regulates the microclimate of the room by absorbing moisture from cold air and then returning it when the temperature in the room rises.
Gypsum plasters are suitable for correcting small and large surface defects and are easy to use.
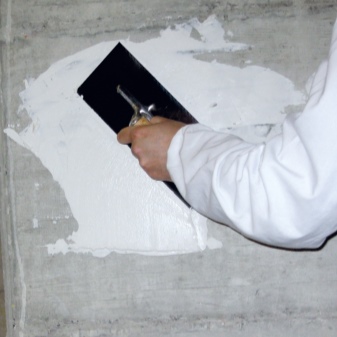
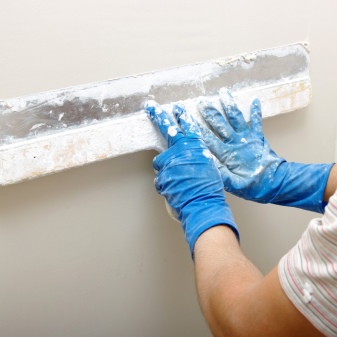
Specifications
In terms of their technical characteristics, gypsum plasters differ in many respects from cement and lime plaster mixtures. The features of these parameters mainly depend on the base component, which is a mineral of natural origin - gypsum. The differences between the properties of the mortar and the finished coating are caused by the technological additives present in the mixture.
Regardless of the manufacturer and the characteristics of the ingredients, the finished gypsum coating has the following characteristics:
- Environmental friendliness. The surface of the material does not emit substances harmful to health, even when heated and wet.
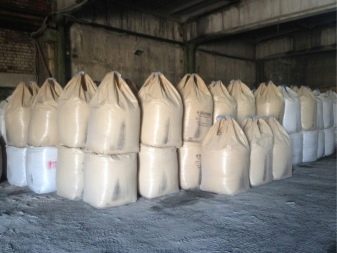
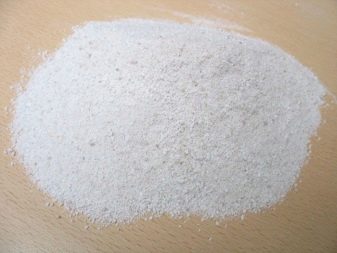
- Thermal insulation. The thermal conductivity of gypsum plaster at a density of 800 kg per m3 is in the range of 0.23-0.3 W / (m ° C).
- Noise isolation. Gypsum is a soft material and absorbs external noise.
- Water vapor permeability. Natural ventilation and a comfortable microclimate in the room are achieved due to the absorption and release of moisture by the material, depending on the temperature and humidity of the air.
- Frost resistance. The hardened surface can withstand temperatures from -50 to + 70 ° C.
- Hydrophilicity. Gypsum absorbs water very well. When too wet, the material acquires the structure of the dough.
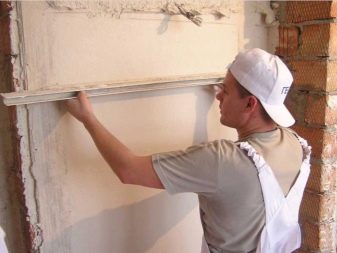
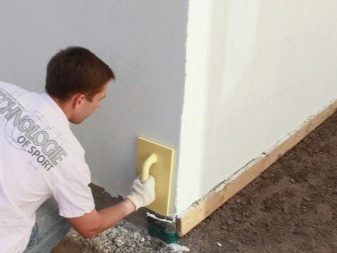
During the work, it is necessary to observe the air temperature from +5 to + 30 ° С. The room must be well ventilated, but drafts must be excluded. Direct sunlight on wet plaster can lead to cracks.
Material consumption for plastering 1 m2 of surface with a layer of 1 cm ranges from 8 to 10 kg.In one pass, you can apply a layer of mortar up to 5-6 cm without reinforcement, with the installation of a reinforcing mesh, it is applied up to 8 cm.
The setting of the composition usually occurs within 1 hour after application, the surface dries up after 3 hours, and the curing process can take from 7 to 14 days.
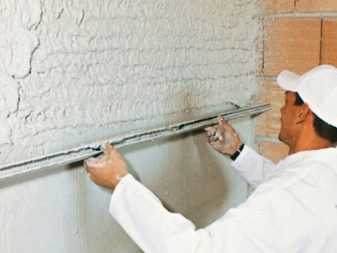
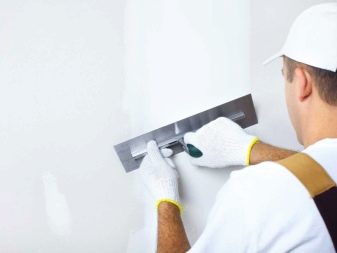
Manufacturers offer gypsum plaster in the form of dry powder and ready-mix. Delivery of dry material for solution preparation to points of sale is carried out in paper bags, the volumetric weight of which can be 5, 15, 20, 25 and 30 kg. To prepare the mixture, 2 parts of such plaster are mixed with 1 part of water. The finished material is supplied in the form of a plastic paste in 20 liter buckets.
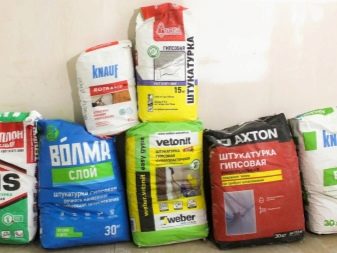
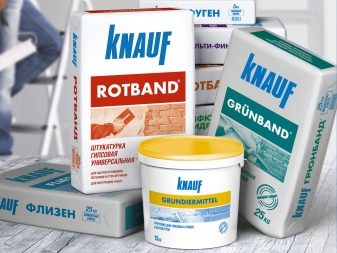
Composition
The main component of gypsum plaster is aqueous sodium sulfate, which is commonly called gypsum or alabaster. Stones made from this mineral of natural origin are subjected to prolonged firing at high temperatures, and then crushed to the desired fraction size. The smaller the size of the particles obtained, the better the quality characteristics of the finished raw material. The gypsum component is responsible for the binding properties of the mixture.
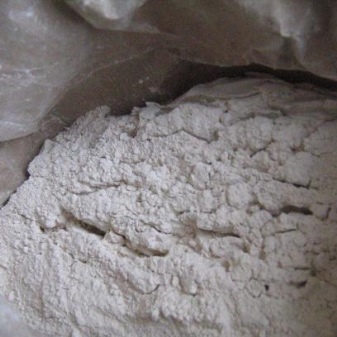
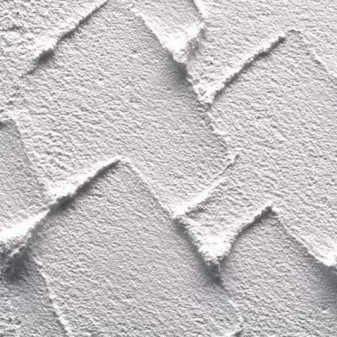
Additional ingredients in the form of fillers of natural or artificial origin give the gypsum-based plaster the desired properties. They make the mixture lighter, reduce material consumption and increase the strength characteristics. Also, the size and shape of the filler particles give the surface a different texture. Such components can be ground sand, expanded polystyrene, foam glass, vermiculite and perlite.
The thickness of the applied layer also depends on the size of their grains:
- fine-grained are applied in a thin layer from 8 mm;
- medium-grained: coating thickness up to 5 cm;
- coarse grains are used for making a thick layer.
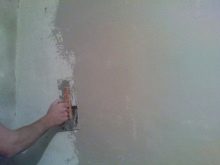
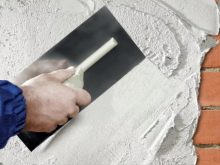
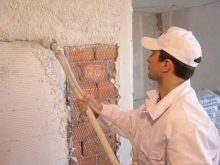
For bleaching the plaster mixture, the composition includes titanium or zinc white, which are metal salts. In addition to bleaching, lime fillers change some of the features of the solution. The setting of lime-gypsum plaster occurs after 5 minutes, after 30 minutes the surface hardens, and strength is gained in 1-2 days.
Polymer and mineral additives are used as plasticizers and regulators of the setting and hardening time of the mixture. These components give the composition additional plasticity and improve adhesion to the treated surfaces. The exact composition and production technology of such elements are not disclosed to the consumer for commercial reasons.
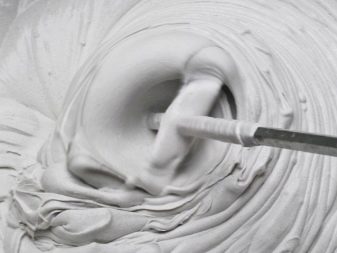
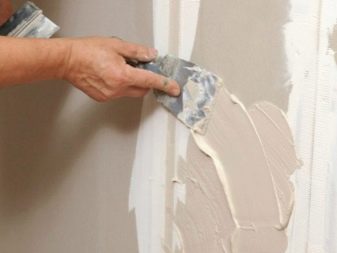
Dry plaster is diluted with water only, without adding any additional ingredients. Depending on the desired consistency of the solution, the amount of water can be adjusted. The liquid mixture is suitable for finishing a flat surface or decoration. As such, it spreads easily over the wall.
A thick mortar is used for rough leveling, sealing cracks, chips and potholes.
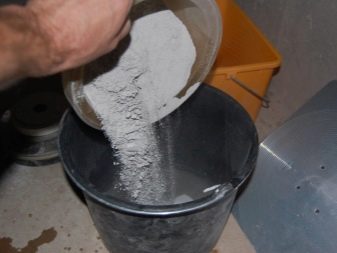
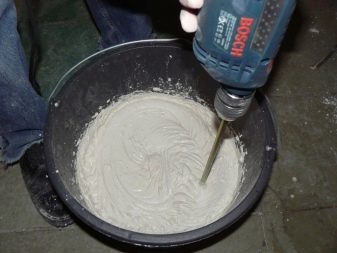
Storage conditions
The shelf life of any gypsum plaster is no more than 6 months from the date of production. When buying, you need to pay attention to the condition of the package; there should be no breaks or damage on it. A mixture that has expired or has been exposed to moisture loses all its declared characteristics. It cannot be stirred until smooth. The application of such a solution will be difficult or even impossible.
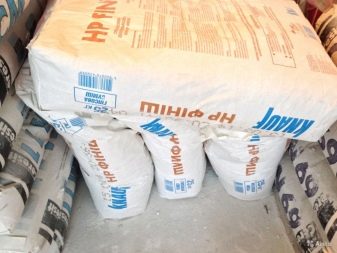
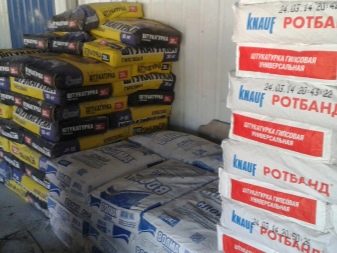
Advantages and disadvantages
Like any other building material, gypsum plaster mixes have their advantages and disadvantages.
Among the advantages are the following:
- The low weight of the composition does not increase the load on the foundation and reduces labor costs during operation, especially facilitating the alignment of ceilings.
- Due to its good plasticity, it is easily smeared on all vertical and horizontal surfaces, even in a thin layer.
- It consists of 95% natural ingredients and does not harm your health.It does not emit toxic substances even in contact with water and high temperatures.
- The plaster has good adhesion to almost all surfaces.
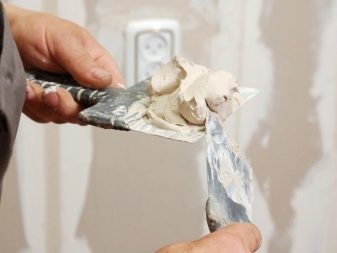
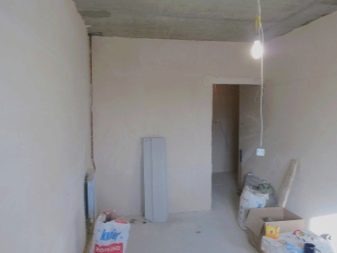
- It is characterized by high vapor permeability, due to which moisture does not accumulate under the gypsum layer, and natural air circulation occurs in the room.
- It is not subject to shrinkage, therefore, if the technology is followed correctly, cracks do not form on the surface.
- Completely fireproof. The material is not subject to fire at any temperature.
- Recovers on its own after flooding. If the neighbors flood from above, after a few days the stain will dry out and disappear by itself.
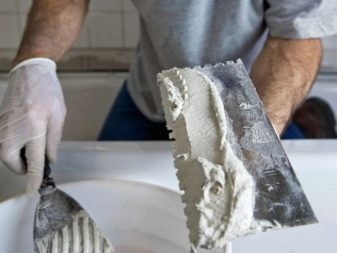
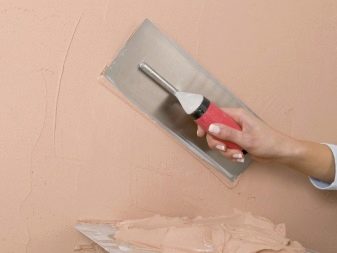
- Not susceptible to mold and mildew.
- You can get a smooth or textured surface with the desired shade without resorting to additional decoration.
- Unlike cement plaster, the consumption of gypsum mixture is 1.5-3 times less. The minimum layer thickness for cement is 20 mm, for gypsum - 5-10 mm.
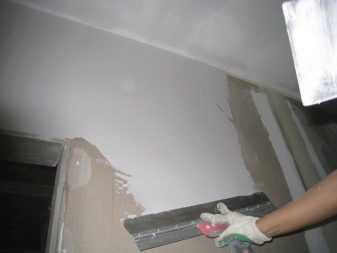
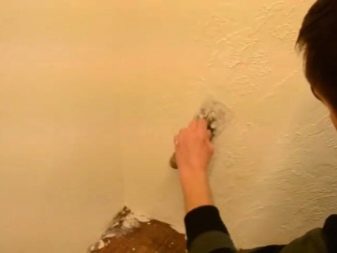
Gypsum plaster has several disadvantages:
- It is not protected from moisture. In damp rooms and with strong wetting, the plaster layer may be washed out or sagged.
- Low impact resistance. Mechanical stress may cause chips and scratches.
- Under a layer of gypsum plaster, metals are susceptible to corrosion, as gypsum constantly absorbs moisture.
- All work must be carried out before the solution begins to set.
- The cost of gypsum plaster mixes is about 20% higher compared to cement.
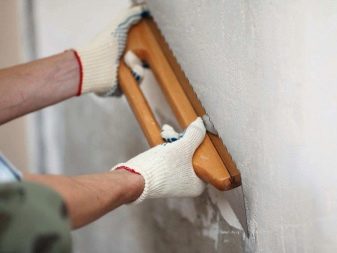
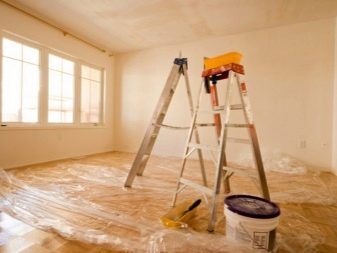
How is it different from plaster?
Despite the fact that the plaster is called gypsum, the correct name for its main component is alabaster. It is this substance that is presented in the mixture in the form of a finely dispersed powder. Gypsum is a generalized name for a rock, from which the material necessary for human needs is subsequently obtained.
Modern gypsum plasters differ from ordinary gypsum in additional properties of the solution due to the presence of polymer additives and various inclusions in its composition. Thanks to them, the surface texture, the speed of setting and drying change.
The material becomes more plastic, easier to fit, has enhanced strength characteristics.
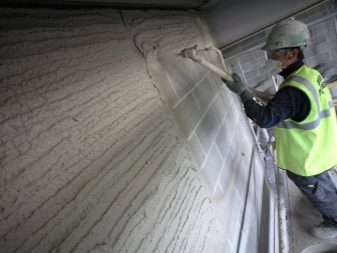
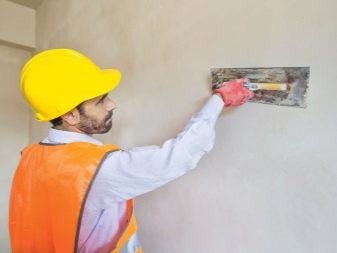
Views
Manufacturers mainly divide the types of gypsum plaster compositions according to two parameters.
Depending on the location of the surface to be treated:
- For interior work, cheap universal plaster mixes are used.
- For outdoor work and surfaces in rooms with high humidity, more expensive facade mixtures or moisture-resistant gypsum plaster are used.
Taking into account the further processing of the finished area:
- Starting - is done to level the walls and then apply a decorative coating on them.
- Finishing - simultaneously serves as a leveling and decorative layer.
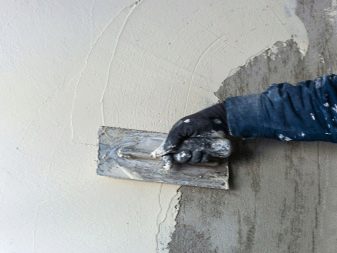
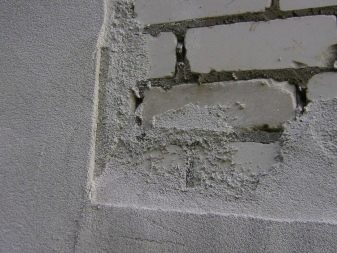
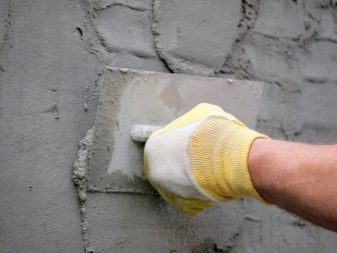
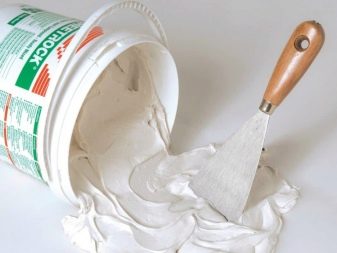
When choosing a plaster, you must carefully read the manufacturer's instructions. Usually, it indicates for which surfaces the use of this mixture is recommended, and which application method is better to use - manual or machine. Mechanized processing creates a stronger and more even layer, but the work requires special expensive equipment. If the plaster is water-resistant, then this will definitely be indicated on the package.
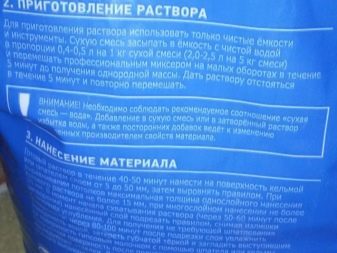
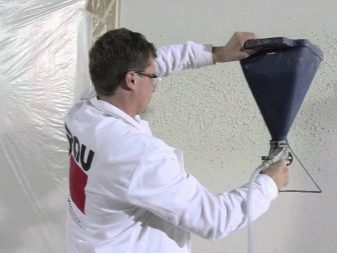
Polymer and mineral fillers make the structure of the mortar light and elastic, therefore almost all gypsum plasters are suitable for surfaces made of a wide variety of materials. They are intended for leveling ceilings, as well as wooden, clay and concrete walls. Perlite plaster based on gypsum will help to significantly reduce material consumption, improve its strength and thermal insulation properties. Gypsum-cement plaster creates a durable layer of the finished surface, which will be thinner than conventional cement plaster and dries much faster.
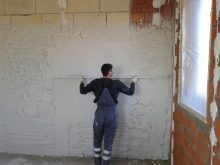
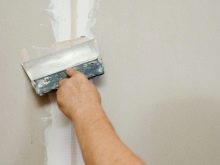
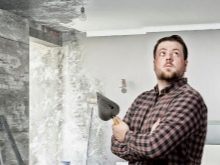
The largest selection of gypsum plasters is presented in the form of dry mixes. But if you are not sure that you will be able to independently prepare a solution of the desired consistency, you can purchase a ready-made paste. To start working with such a solution, you just need to open the container. This material is more expensive than dry mixes and is only suitable for manual application. It cannot be diluted with water or plasticizers, otherwise it will lose its properties.
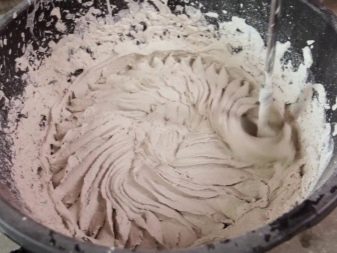
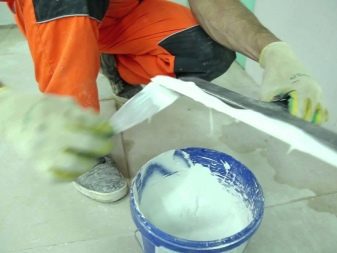
Colors and texture
The vast majority of common gypsum plaster mixes are presented in white and gray, sometimes shades of blue, pink or beige are present. The color of the mixture directly depends on the gypsum used in the composition. Given the field being developed, intensities and shades can vary greatly.
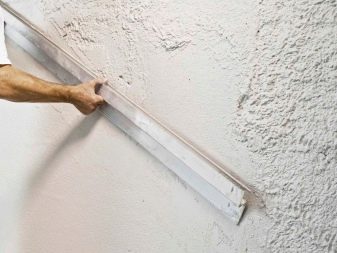
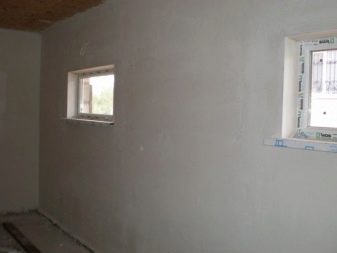
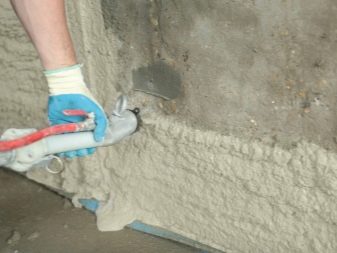
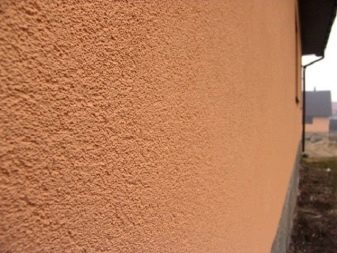
During production, decorative plasters are painted with special colors, and their color range is almost unlimited. For the correct choice of tone, it is recommended to familiarize yourself with samples and catalogs, which must be presented in specialized stores. You can also use Venetian plaster to decorate the walls. A surface that looks like granite or marble is created by applying several thin layers of different shades. Then a special wax is applied, which creates a smooth stone structure.
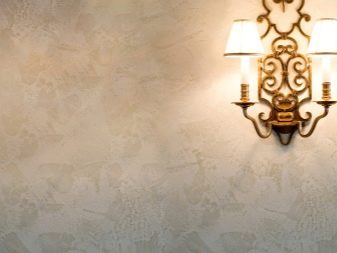

To create various textures, special fillers are added to gypsum plaster: small stones, mica, sand, cotton and wood fibers, ground brick. With their help, you can not only imitate a wooden or stone surface, but also achieve the effect of velvet or leather. Stylization of walls "like a brick" and the creation of patterns is carried out using special decorative rollers and stamps. You can use materials at hand, such as brushes or plastic bags.
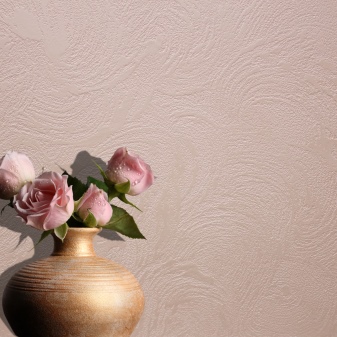
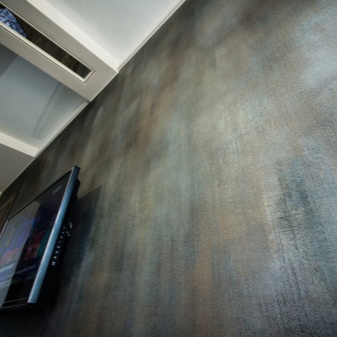
Which one is better to choose?
So that after finishing the room with plaster, the quality of the coating is not in doubt, you need to opt for materials that meet GOST. The parameters of gypsum plasters for interior work are detailed in GOST 31377-2008.
Dry:
- the moisture content of the material should be no more than 0.3% of the total mass;
- weight of 1 m3 in loose form - 800-1100 kg, in pressed form - 1250-1450 kg.
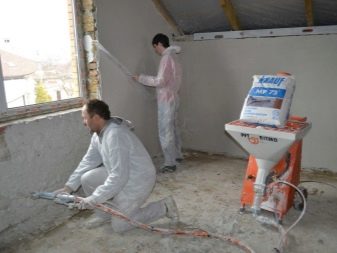
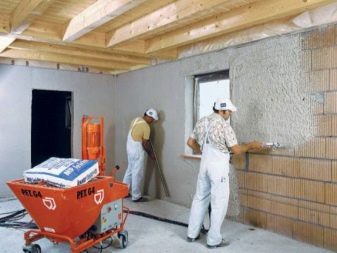
In solution:
- the use of water per 1 kg of the mixture should be in the range of 600-650 ml;
- setting time for manual application - 45 minutes, for machine application - 90 minutes;
- consumption per 1 m2 with a layer of 1 cm with manual application - 8.5-10 kg, with machine application - 7.5-9 kg;
- moisture retention without dripping - 90%.
Finished surface:
- compressive strength - 2.5 MPa;
- adhesion force with other surfaces - 0.3 MPa;
- density per m3 - 950 kg;
- vapor permeability - 0.11-0.14 mg / (mh · Pa);
- thermal conductivity - 0.25-0.3 W / (m ° C);
- shrinkage is not allowed.
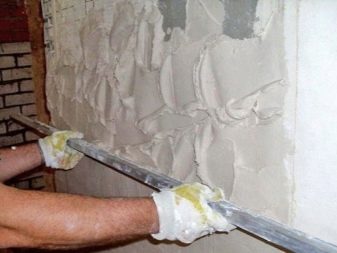

For surface treatment, there is a special SNiP 3.04.01-87. These are the requirements for the evenness of the application of the plaster and its moisture content. Deviation from the horizontal and vertical by 1 meter is allowed within 1-3 mm, and for the entire height of the room - 5-15 mm. There should not be more than 2-3 irregularities per 4 m2, and their depth is limited to 2-5 mm.
The maximum moisture content of the base is 8%.
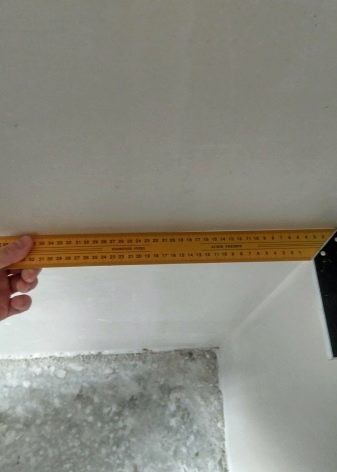
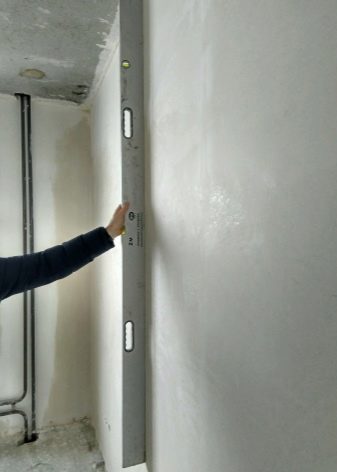
For wet rooms, you need to choose a plaster that the manufacturer recommends for this purpose. The usual composition is not suitable for work in such premises. To give the coating additional moisture resistance, a deep penetration primer or acrylic-based concrete contact is applied to it. For the same purpose, you can use a waterproofing mastic. Such mixtures must be applied in several layers on a completely dry surface.
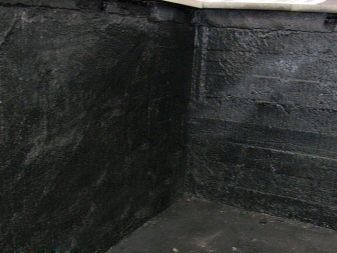
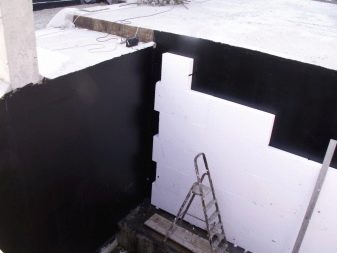
Before finally deciding on the choice of plaster mix, you first need to read the reviews about various manufacturers and compositions. You can purchase materials only in specialized stores, and when buying it is recommended to consult with a specialist.
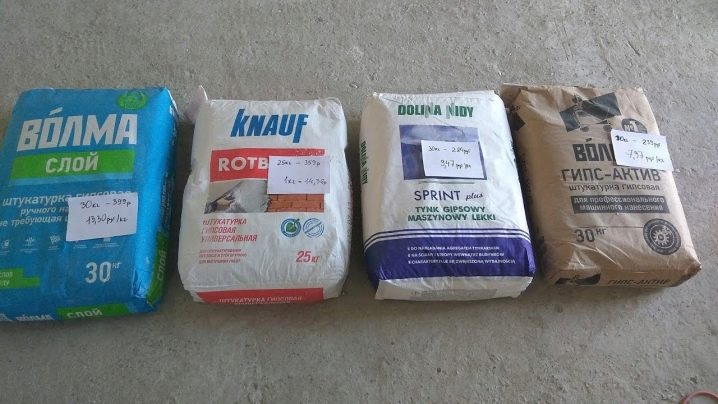
Application
Gypsum plaster is usually used in rooms with low humidity.The mixture is great for the bedroom, nursery and living room, since it does not use substances that can be harmful to health. Initially, gypsum mortars are intended for leveling walls for wallpaper and painting. They are convenient for sealing drywall joints.
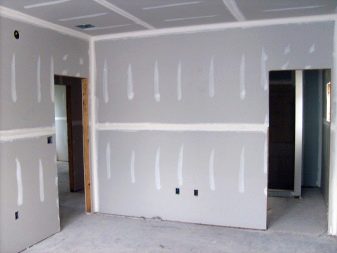
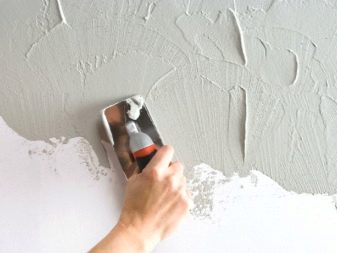
To get an even high-quality coating, the plaster is spread over the surface in thick layers. Leveling is best done as a rule, but if it is absent, you can use a spatula. The walls are aligned from bottom to top, in parallel making the movements the rule to the left and right. When working on the ceiling, the rule is pulled over.
A layer of gypsum can float, so it must be periodically pulled up and leveled.
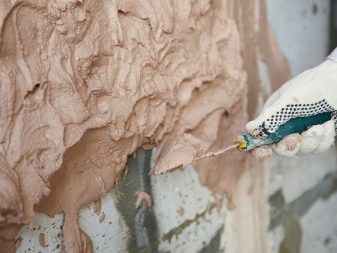

After 20-30 minutes after application, you need to cut off the excess mixture as a rule and smooth out the irregularities with a spatula. After about 1 hour, if the layer is not deformed by finger pressure, it should be moistened with water or a primer. When the surface becomes dull, rub it in a circular motion with a spongy metal or plastic float. Excess mortar should be removed from the grater during grouting. Then it is necessary to smooth out the entire layer of plaster with a spatula.
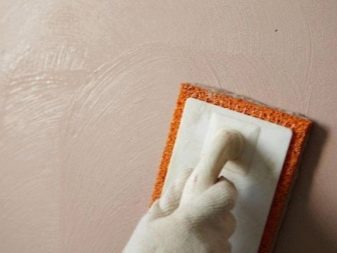
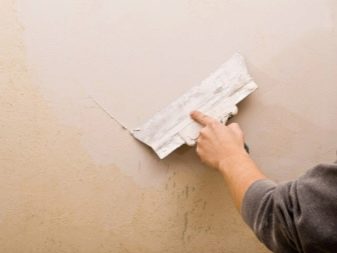
It is recommended to repeat the grouting after another 5-6 hours. After that, the surface is polished with a spatula or a special trowel. These actions are aimed at making the coating perfectly even and closing large pores. Such a surface does not need to be putty, and before painting and applying other decorative coatings, it will be enough to treat it with a primer.
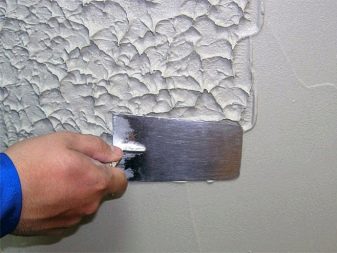
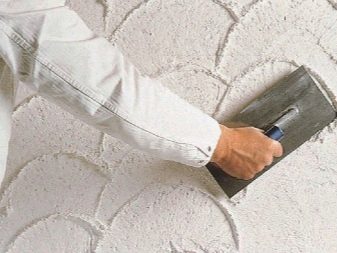
For the machine method, special expensive equipment is used, which, if necessary, can be rented. The gypsum plaster is mixed in a container intended for this and fed through a hose. In this case, the layers are applied with an overlap, leveling is done in the same way as with the manual method. This treatment creates a more uniform layer, which has a positive effect on the quality of the coating.
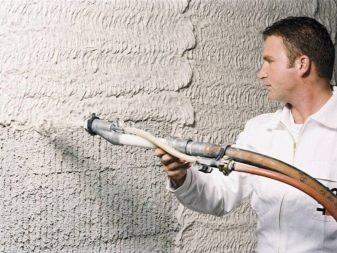

Payment
On average, material consumption per 1 cm of plaster layer is 8-10 kg.
It directly depends on the following parameters:
- manufacturer and characteristics of the mixture;
- evenness of the surface;
- layer thickness.
To determine what layer of plaster is needed, you need to check the difference in the blockage of the walls at 3-5 points on each side. To do this, a cord is stretched under the ceiling at the same level, and several cords are drawn from it strictly vertically down at an equal distance from each other. It is necessary to measure the distance from each cord to the wall: the smallest distance will indicate the most protruding point, and the largest will indicate the maximum obstruction.
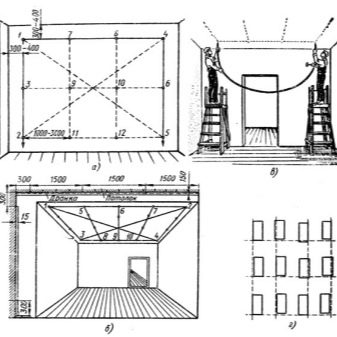
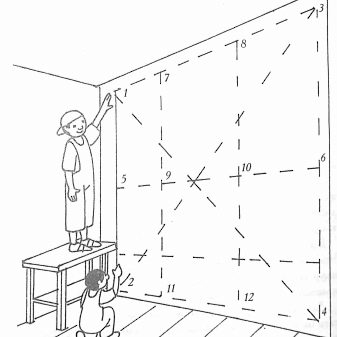
Then the difference between these distances is calculated and the result is divided by 2. This will be the main layer thickness. This value is added to the thickness of the additional layer of at least 3 mm and 10-15% for the reserve.
So, with a wall blockage of 3 cm per 1 m2, about 2 kg of the mixture will be needed.
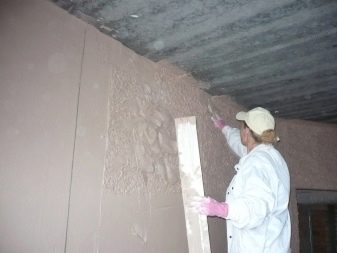
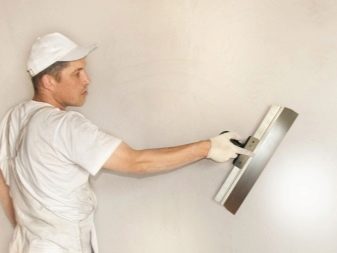
How to prepare gypsum mortar?
Self-production of a solution from ready-made dry mixes must be done strictly according to the manufacturer's instructions.
There are also general guidelines that are suitable for almost all formulations:
- In a container with 1 liter of water, the temperature of which should be in the range of 20-25 ° C, you need to pour 2 kg of dry mixture.
- Mix thoroughly with a construction mixer or a drill with a special nozzle. As a last resort, mixing small volumes of the mixture can be done with a spatula or trowel;
- Leave the solution for 3-4 minutes to gain strength and plasticity. Stir it again. The resulting mixture should not drain from the tool and have lumps.
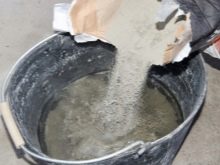
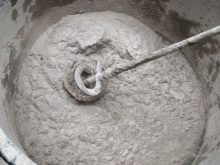
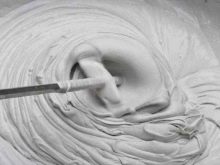
All manipulations for the preparation of the mixture must be done in a clean container and clean tools. The amount of ingredients for each new serving must be carefully measured, as differences in the mix can lead to poor coverage.
There are recipes for making gypsum-based plaster yourself:
- For 4 parts of gypsum, add 1 part of sawdust and 1 part of tile adhesive.
- In 1 part of gypsum, 3 parts of chalk are added in the form of a powder with fine fractions and wood glue in an amount of 5% of the total mass of the mixture.
- One part of gypsum is pre-soaked in water and mixed with 1 part of lime dough.
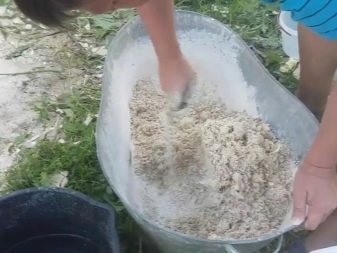
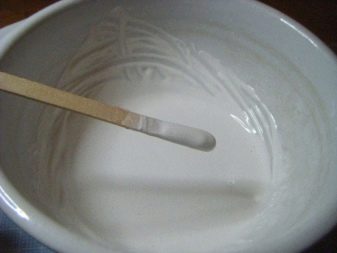
In the first two recipes, the dry components are first mixed, and only then they are diluted with water to the desired consistency. Stirring is carried out in two stages with a break of 3-4 minutes. Various plasticizers can be added to such mixtures. PVA glue is added in an amount of 1% of the total mass, the use of tartaric or citric acid and special plasticizers is allowed.
Lime also gives the mortar plasticity and increases the setting and drying time.
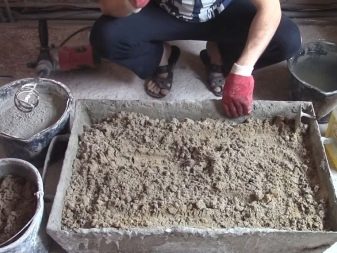
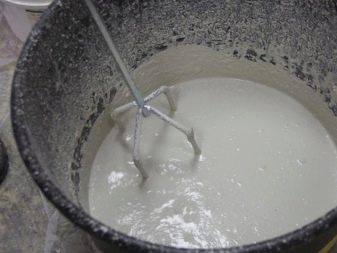
How to dry?
Drying of the surface must occur naturally. The room should be free of drafts and operating heating devices, the required air temperature should not be lower than +5 and not higher than + 25 ° С. Do not allow direct sunlight to hit the coating. Do not accelerate drying with a heat gun or any other heating equipment.
After 3-7 days, the room must be thoroughly ventilated to remove moisture from the plaster layer. The plaster will dry completely and gain strength only after 1-2 weeks. The finished surface should be smooth and light. Then you can glue tiles or wallpaper on it. And the moisture content of the coating for painting should not exceed 1%.
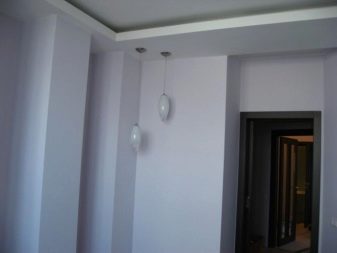
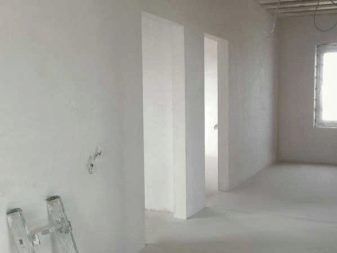
How to paint?
A wide variety of paints are suitable for painting walls and ceilings over gypsum plaster: oil, adhesive, acrylic, latex and water-based paints. In terms of composition and characteristics, the most suitable for gypsum is a water emulsion due to its porous structure. The only paints that cannot be used on gypsum surfaces are lime paints.
When using oil and acrylic paints, the surface must be treated with a not very hard metal brush to obtain a rough finish. This is necessary so that the paints adhere well to the gypsum and do not peel off the walls after drying.
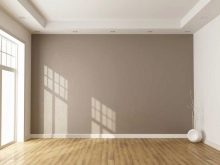
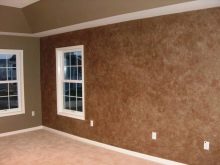
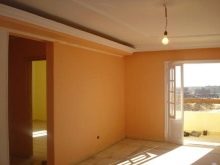
Before painting, you need to make sure that the moisture content of the gypsum plaster does not exceed 1%. To carry out such measurements, a special device is used - a moisture meter. If the surface meets all the requirements, then it must first be treated with a primer. Priming is carried out in 2-3 stages so that a period of time is maintained between the application of layers, during which the previous layer is completely dry.
The primer will remove excess dust from the surface and improve adhesion between coatings.
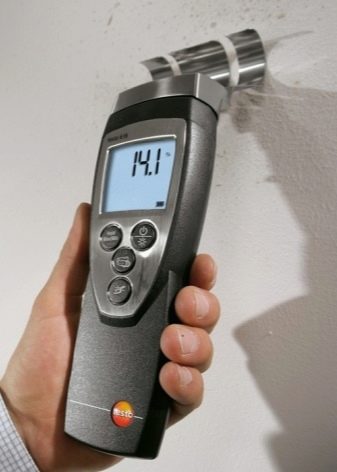
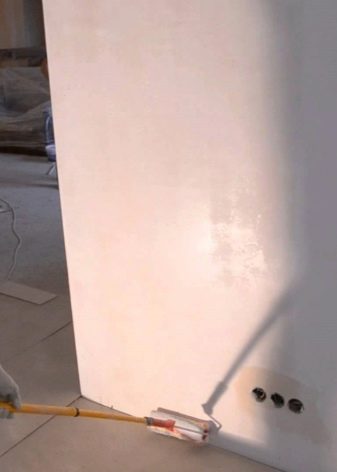
Important nuances
Gypsum plaster is suitable for many surfaces. It can be applied to cement and lime plaster, drywall, wood and paint. Also, gypsum mixtures are allowed to work on gas silicate blocks, logs, chipboard and expanded clay concrete. Such surfaces must always be primed. For most of these materials, a regular universal two or three coats primer will work, while concrete contact slabs and paint are best applied to concrete slabs.
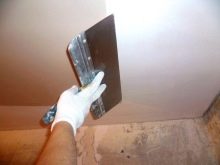
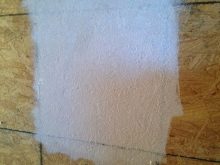
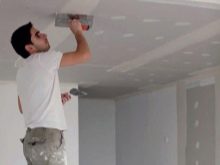
Before proceeding with the application of gypsum plaster, you need to carefully prepare the surface. All old decorative coatings are completely removed, remove grease stains, glue and dust. If the wall or ceiling has been previously painted, it is recommended to completely remove the paint layer. To do this, you can use a scraper or grinder with a grinding attachment. Lagging layers of old plaster also need to be removed.
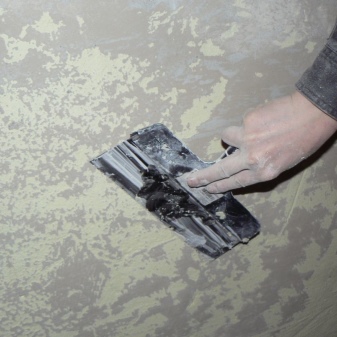
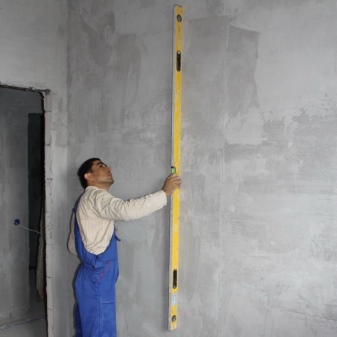
All metal elements must be removed from the surface to be treated, since the gypsum layer increases the effect of corrosion on them. Metal parts that cannot be removed are abundantly coated with an anti-corrosion compound.
Large cracks, chips and other significant defects must be covered with cement mortar.
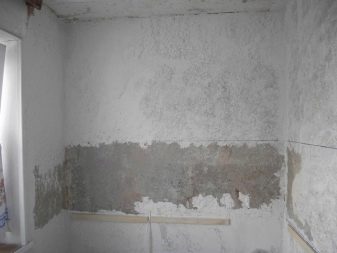
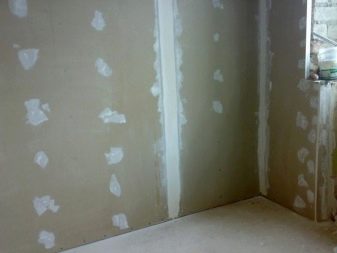
The minimum layer for some plaster mixes is 5 mm.But the optimal thickness for a layer of plaster is within 1-2 cm. In cases where there are large defects on the surface, it may be necessary to increase the thickness of the coating to 8 cm. Under these circumstances, surface reinforcement with galvanized or plastic mesh will be required. Also, wall reinforcement must be done in new buildings in order to exclude deformation during shrinkage of the building.
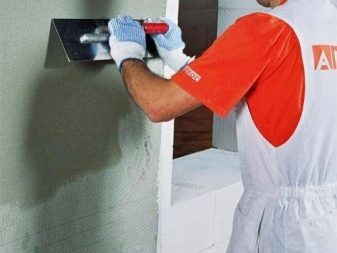
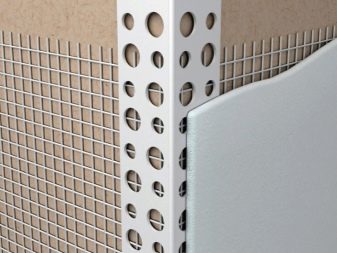
To install a reinforcing mesh on the entire surface of the wall, you need to apply a marker for every 35-45 cm with a marker. At these marks, holes are drilled with a punch, and plastic rods from the dowels are inserted into them. The mesh is cut into small rectangular pieces and overlapped with self-tapping screws. The distance from the wall to the reinforcing material should not be more than half the plaster layer.
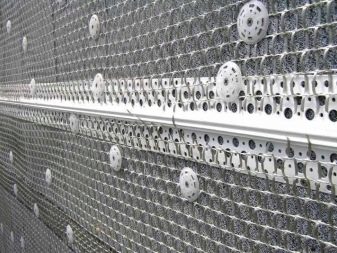
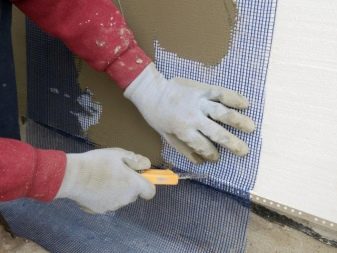
No deflections are allowed on the reinforcing frame, and when you touch it, there should be no vibration. To correct such shortcomings, a wire in the shape of the letter Z is threaded between the mesh cells to strengthen the structure. A plaster mixture, which is more liquid in consistency, is poured onto the inner side of the mesh. This layer is left to dry for 10-20 minutes and only after that a thicker outer layer is applied.
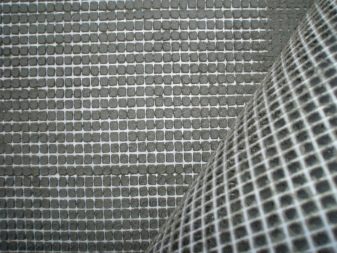
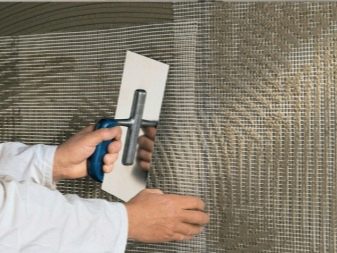
You may also need to install guide beacons. As them, you can use an aluminum profile for drywall, which must be removed after the plaster layer has dried. You can make your own beacons from a plaster mix. To do this, a vertical strip is built from the solution and leveled with a level. You can work on plaster beacons in 3-4 hours.
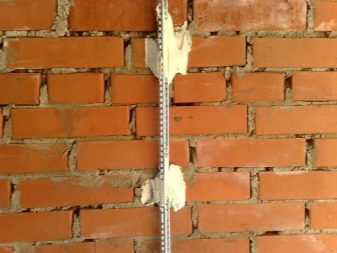
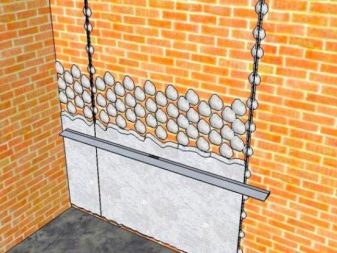
After the plaster has completely dried, it is necessary to check the uniformity of color and the evenness of the surface. You can only check the color in the right bright light. Cracks and chips are not allowed on the finished coating, and it should not be perfectly smooth or very porous. Only small pores are required on the surface. If there are flaws, then a second thin layer of plaster should be applied over the finished coating.
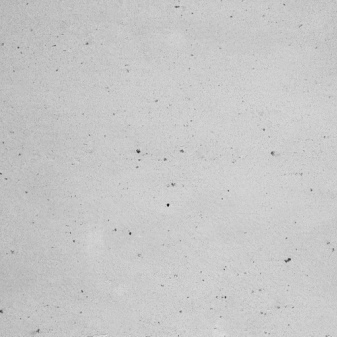
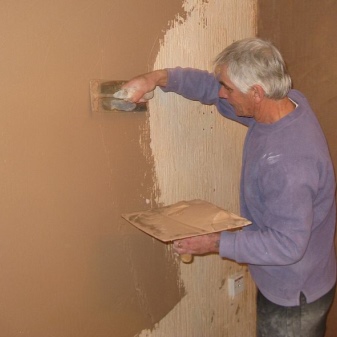
There are many nuances to consider when working with gypsum materials. For example, you can add cement to gypsum, mix it with alabaster or sawdust. Various additives impart new properties and texture to the solution. Any gypsum solution needs to be worked very quickly. If it hardens, then it will not work to soak the frozen mixture for further work with it.
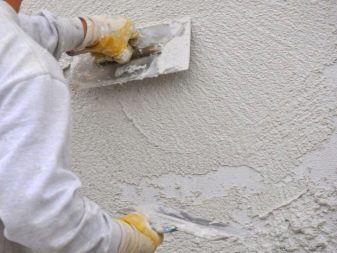
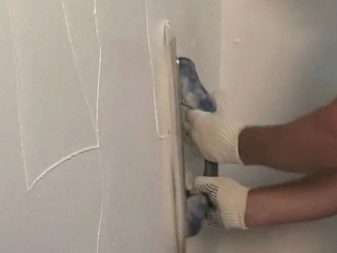
Manufacturers
Domestic and foreign manufacturers supply gypsum plaster of various compositions and purposes to the market. Almost each of them in the product line contains mixtures for indoor and outdoor use, as well as for manual and machine application. An exact rating of firms in terms of quality and prices for gypsum mixtures does not yet exist, so the choice of material can only be made on the basis of a comparison of technical characteristics.
Ideal parameters of Etalon gypsum plaster for interior work from a domestic manufacturer:
- color - light gray;
- the amount of water for solution preparation - 0.55-0.6 l / kg;
- the thickness of one layer is 2-30 mm;
- compressive strength - 40 kg / cm2;
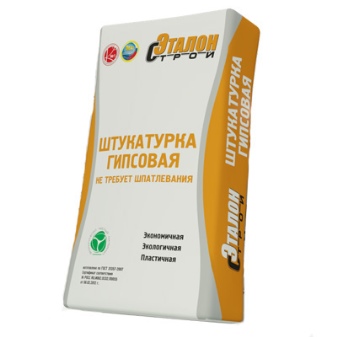
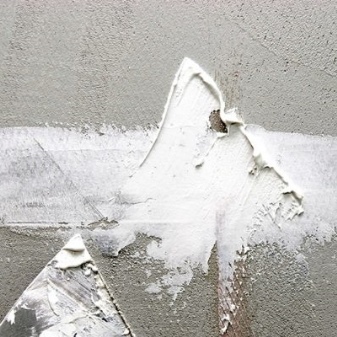
- temperature during work - from +5 to + 30 ° С;
- the solution is suitable for work within 1 hour;
- consumption per 1 mm layer - 0.9-1.2 kg / m2.
The plaster Standard for machine application has all the same characteristics, except for the time for work, which is increased to 100 minutes.
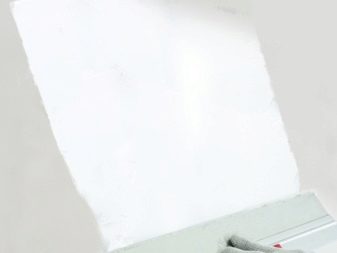
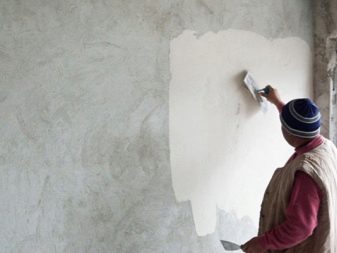
Plaster "Teplon" from the Russian company "Yunis" is suitable for interior work and is applied both manually and mechanically:
- White color;
- the amount of water for preparing the solution - 0.4-0.5 l / kg;
- the thickness of one layer is 5-50 mm;
- compressive strength - 25 kg / cm2;
- temperature during work - from +5 to + 30 ° С;
- the solution is suitable for working within 50 minutes;
- consumption per 1 mm layer - 0.8-0.9 kg / m2.
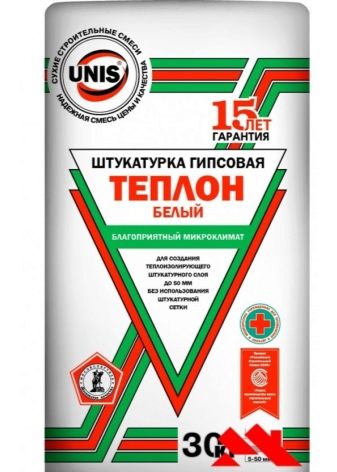
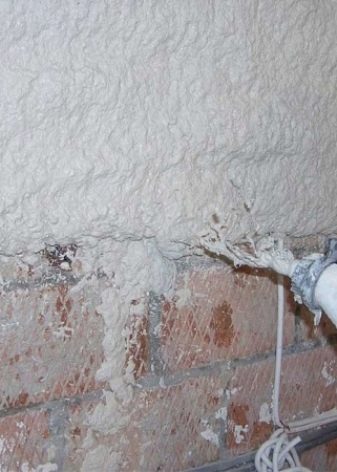
Bolars plaster is also produced in Russia and has the following parameters:
- White color;
- the amount of water for solution preparation - 0.44-0.48 l / kg;
- the thickness of one layer is 2-30 mm;
- compressive strength - 25 kg / cm2;
- temperature during work - from +5 to + 30 ° С;
- the solution is suitable for work within 1 hour;
- consumption per 1 mm layer - 1 kg / m2.
Turkish gypsum plasters from Dr. mix. satin, Rigips, Siva and many others.
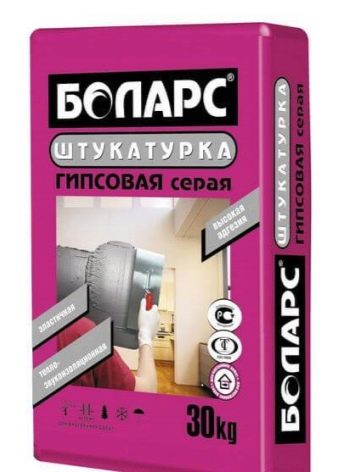
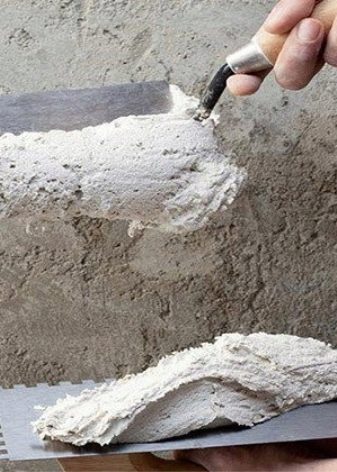
For information on how to carry out gypsum plaster on lighthouses, see the next video.
The comment was sent successfully.