What is veneer and what is it like?

At all times, furniture and door panels made of solid natural wood were highly valued by connoisseurs. Wood is an environmentally friendly material for humans that has a number of undeniable advantages, but it has a significant drawback, which is the high cost of finished products. An alternative option, more affordable for the population, has become products made of composite panels, pasted over with natural wood veneer.
In appearance, such products look like natural wood, but their weight is much less., and besides, there are also features associated with the duration of operation. Today, furniture or door panels made of natural wood are produced only in exclusive batches, and veneered options are used for mass production.



What it is?
The word "veneer" in translation from German means "wood chips". This definition did not appear by chance, because the first veneer manufacturers in Europe were the Germans. The technology was developed in the 19th century, when thin canvases were cut from large-diameter logs of various tree species using specially designed woodworking machines. The solid surface of the cut wood material retained all the properties of wood, including its natural pattern. The veneer thickness varies and can be either 1 mm or 12 mm, which directly depends on the type of wood and the method of wood processing. Over time, the German technology was also mastered in Russia, but the name of the wood cut remained to sound in German - veneer.
Natural wood cuts are widely used in the manufacture of not only furniture products, but also musical instruments. Cheap blanks were pasted over with precious cuts of rare tree species, and as a result, things were obtained that, in appearance, could hardly be distinguished from those cut from a natural massif.



The veneer production technique allows us to distinguish 3 varieties of it.
- Natural - such a veneer is obtained by cutting a thin layer of wood from a log rotating around its axis. Veneer can be removed in different ways - by peeling, planing or sawing. The sawing technique is most often used for processing softwood, whereby the wood is cut into thin layers.
Planing is used in the manufacture of the most expensive types of veneer, which is removed over the entire width of a log rotating in a horizontal plane.


- Ribbed - natural material looks like thin sheets of wood glued together in the area of the edges. The cost of such veneer is low, but the performance properties are quite high and long-lasting.


- Reconstructed - for the production of this material, cuts of tropical trees with fast growth properties are used. Such veneer is painted and glued, the color may differ from natural traditional shades, but this material is completely natural, its second name is fine-line.



Natural wood veneer has various properties, among which there are pros and cons. Positive properties lie in the fact that thin cuts of plates are used in technologies for the manufacture of decorative finishing materials, furniture products and other items that in appearance are indistinguishable from massive wooden counterparts. The high decorativeness of the veneer is due to the obtaining of a multitude of texture patterns of the annual rings of the tree, and a solid board cannot possess such properties. A thin veneer sheet is versatile in its application - it can be glued to surfaces with almost any relief configuration.
High-quality veneer is a ready-to-use material that has been processed, thoroughly dried and straightened. To improve the appearance, the veneer is covered with coloring and protective compounds, so it has a certain resistance to mechanical stress, does not absorb moisture, is not prone to mold growth and cracking. After a long period of use, wood veneer is subject to restoration and extension of its service life.



Products, the surface of which is covered with natural veneer, have a low cost and durability. If we compare two products, one of which is made of solid wood, and the other is pasted over with veneer, then in appearance these specimens will be hardly distinguishable, but their cost will differ several times. As for the properties and features of operation, they will be identical. Therefore, veneer has received such widespread use in various areas of our life.
The disadvantages of the material include the fragility of the veneer sheet and the difficulty of gluing it - this is a rather capricious material, requiring certain skills and dexterity in handling. Veneer does not tolerate scratches and bumps, including from claws and teeth of pets - deep marks can remain on the surface.
If the air humidity is high in the room, objects treated with veneer may warp. In addition, such products cannot be washed with detergents and moistened with water.



How do they do it?
In woodworking enterprises, wood is sorted before veneer production. Natural material can be produced from various types of trees. Hardwoods are birch, maple, beech, pear, apple, cherry, hornbeam, mahogany, aspen, alder, poplar, lemon tree, willow, linden, Karelian birch, sycamore, elm, oak, ash, chestnut and others. Coniferous varieties are pine, cedar, fir, yew and larch.
Wood species with a pronounced tree ring pattern are processed with a special veneering technology to obtain a planed type of product with beautiful wood patterns. A particularly effective structure is obtained when the veneer is made by means of a radial cut, which is why such grades of material are highly valued. Oak, ash and larch are especially valuable in terms of veneer appearance. It is possible to obtain veneer with a wavy pattern from these trees, in addition, curls can be present here, which makes the material especially exquisite.



In order to obtain a quality veneering material, it is important to determine the good composition of the raw material. The wood does not have a large number of knots, resin runs, ingrown bark and extensive cracking areas by standards. The production technology involves cleaning the workpieces from the bark, as well as removing the damaged inner layers. After this procedure, the wood is divided into ridges of a certain size, and, depending on the processing technique, they are subsequently again cut into fragments of even smaller sizes.
To soften the wood structure and correct its color shade, the wood blanks are subjected to a steaming process using hot water.which takes several days. Maple has to be steamed for the longest time, since this is the most capricious breed, with inept handling of which its light shade is lost.To obtain blank sheets, prepared wood fragments are passed through a woodworking machine.
After cutting, the finished veneer is dried, after which the sheets are sorted and stacked in bundles of 100 pcs.



Comparison with other materials
You can distinguish an array from a veneered product by the weight of the product, since furniture made of veneer consists of blanks that are made from cheap woodworking products - MDF or chipboard, whose appearance looks much better when finished with natural wood plates. Despite the identical appearance, products made from solid wood and veneer differ from each other, and this difference lies in many aspects. Furniture from a solid piece of wood is considered the most durable, high quality and elite. These properties are reflected in the high price, since such products - furniture, doors, parquet boards - belong to an exclusive class of goods and emphasize the financial viability of their owner. In addition, luxury products never go out of fashion and are classics that live out of time and beyond competition.
If you decorate such furniture with fittings made according to ancient traditions, the result will be a unique work of art. But solid wood furniture requires careful and careful care, which consists in processing with compounds containing wax. If you do not follow these procedures, over time, the products will lose their attractive appearance.
In addition, natural wood is sensitive to changes in temperature and humidity, so keeping such products is not only a big responsibility, but also the associated costs.



As for furniture and other products made with wood veneer coating, they are less capricious, easy to use, so the popularity of affordable models is steadily growing. The appearance of veneer products will look no worse than natural massive counterparts. Production technologies allow preventing the possibility of cracking of veneer on the surface it decorates. In addition, such furniture and other products are resistant to changes in temperature and humidity, they can withstand exposure to ultraviolet rays. This strength is possible due to the processing of the natural cut with a special protective coating in the form of a layer of polyurethane varnish. Veneered furniture does not have as much weight as solid furniture, so it is easy to move it. If part of the veneer is damaged, then this area can be restored to extend the life of the product.
In addition to the usual veneer, there is also the so-called eco-veneer, which also first appeared in Germany. The production technology of this product was based on the disposal of waste that remains in the manufacture of conventional veneers. Enterprising Germans decided to create a new type of material, which is a mixture of wood fibers and a polymer component. This type of facing products made it possible to switch to waste-free production, as a result of which a qualitatively new decorative material appeared, combining the properties of natural wood and the strength of a polymer. Eco-veneer has a lower cost compared to conventional veneer and has different color options. Thanks to this material, the purchase of furniture from the most valuable types of wood has become available to the ordinary buyer.
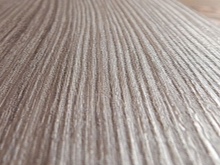


Besides, eco-veneer is particularly resistant to environmental influences and has a long-term operating life. Thanks to the polymer component that is part of the material, it is resistant to scratches and mechanical stress.Eco-veneer does not exfoliate, does not corrode due to changes in temperature and humidity, it can be washed using synthetic detergents, since the fibers connected to the polymer are absolutely resistant to moisture. Eco-veneer can imitate any species of valuable trees, while remaining an environmentally friendly material for human health.
Summing up the comparison of various materials, we can conclude that there are no ideal products, since each of them has its own advantages and disadvantages. Natural solid wood is an expensive material that requires certain operating conditions. At low humidity, wood dries up and cracks, and at high levels of moisture, it swells and deforms. As for veneer, it is cheaper than solid wood, but more expensive than eco-veneer. Being resistant to changes in air humidity, this material does not react well to scratches and bumps. The damaged area must be completely replaced, since there is no other way to restore it. Eco-veneer is the cheapest option, but in appearance it differs significantly from natural solid wood and veneer, although its performance is high.



Description of species
Natural veneer can be flexible and rigid, depending on the thickness of the material, for example, products with a thickness of 2 mm or 3 mm have greater ductility when glued than a thick sheet, the cut of which is 5 mm. For ease of use, thin veneer is produced on an adhesive basis and is self-adhesive. The range of shades of products repeats the colors of natural wood varieties, but it is also possible to color the material to which a light cut of wood is subjected to obtain a colored veneer. It is cut into plates, and a roll version is also produced. There is a glued type of product, where the edges of two plates are joined with a synthetic adhesive. Moreover, the plastic gluing element is absolutely not visible in a single canvas when the veneer is glued to the surface to be decorated.
On sale you can find cork veneer, which is made from exotic cork wood, and such a coating looks peculiar. Production technologies allow us to produce a laminated veneer, which has improved characteristics of durability and wear resistance. For the production of wood material, more than a hundred different types of wood are used, which makes it possible to obtain any color of products - white, creamy brown, dark coffee, whitish cream, caramel, pink, red and other shades.
In addition, wood veneer is classified according to other criteria.



By cutting angle
The varieties of the wood pattern on the cut of the workpiece depend on the processing technique, which is performed at a certain angle relative to the annual rings of the tree trunk:
- radial cutting angle - characterized by the presence of strips of a straight direction on the canvas, located along the entire field of the surface;


- semi-radial cut - strips of growth rings are parallel to each other and occupy no more than 70% of the surface area of the web;


- tangential cutting angle - layers of annual rings form a pattern consisting of curved lines and cones with increasing and decreasing;


- tangential-end cut - the surface of the canvas is covered with circles uneven in outline or an elliptical pattern.
In the process of making a cut, the finished canvas has a front and a seamy side. The side that touches the cutting edge of the woodworking machine is the wrong side.
It can have small cracks that are barely visible to the eye, it is looser in structure and not so even compared to the front side, which has a perfectly smooth surface.


By manufacturing method
No artificial finishing material will be able to convey the living texture of wood.Depending on the method of woodworking, not only the options for cutting log blanks differ, but also the method of cutting. According to the manufacturing method, veneer is subdivided into 3 types.
- Sawn view - the most expensive option, which is obtained when woodworking round blocks or logs. For work, a special type of saw is used, thanks to which thin planks are cut from the massif - their thickness ranges from 5 mm to 12 mm. This method of manufacturing involves the remainder of a large amount of waste, so sawn veneer is produced in small batches and is made from inexpensive conifers.


- Peeled view - the most affordable option, which is available in the range from 1 mm to 5 mm. For its production, cuttings of a log are used, which is subjected to the action of a special cutter. For rotary cut veneer, alder, beech, oak, birch and aspen are used. Most often, this type of veneer is used for the production of combined-type finishing materials.


- Planed view - is in the middle price category and is available in the range from 4 mm to 10 mm. For its manufacture, machines with cutting knives are used, where the workpiece can be fixed at a different angle of inclination, which makes it possible to produce plates with a varied texture pattern. For sliced veneer, beech, pine, fir, cedar, birch are used.


Among others, natural veneer can be produced in fine-line format. Often such a product is mistakenly considered plastic, but in fact it is made from natural species of exotic trees. The technology includes peeling large-sized wood plates, which are subsequently cut into strips of the required parameters. In the production of this type of veneer, natural dyes and adhesives are used, which makes it possible to imitate precious wood species.
The material has excellent decorative properties - it is flexible, resistant to changes in humidity and temperature conditions.



Where is it applied?
Wood veneer is used for decorative purposes in the furniture and woodworking industries. It is used to finish surfaces made of cheap materials. Coating with veneer creates the effect of natural wood at a low cost of finished products. Thin veneer is used in the manufacture of door leaves, as well as decorative wall panels. Boxes for matches are made of this material, boxes for fruit are made, and also used in the technology of production of plywood multilayer sheet.
As a basis for pasting with veneer, a sheet of chipboard, MDF, drywall can be. Wood-cut sheets are suitable for restoration work when repairing used furniture. Sliced veneer is used in the manufacture of sports equipment, designer souvenirs, household items and much more. Sawed veneer is used in the creation of bodies for musical instruments, doorways and arched structures, exclusive models of furniture, boxes, panels, gift products. The veneer of noble tree species, which has a colored color, is a subject for creativity.
With its help, craftsmen create objects of art using the technique of marquetry, intarsia, mosaics, where pieces of material are selected according to color and shape, making up a canvas of a painting or ornament.






Care Tips for Veneered Furniture
In order for a product decorated with wood veneer to last a long time and retain its original aesthetic properties, it is necessary to adhere to certain rules related to the care of the product. The veneer must not be rubbed with abrasives, metal shavings brushes. Contamination treatment is not carried out with acidic or alkaline solutions. It is allowed to wipe the veneer with a soft, slightly damp cloth using special aerosol wax compositions.
It is not recommended to place hot objects without a backing on the surface of furniture decorated with veneer. Dust and dirt are removed with a suede cloth, soft brushes with natural bristles or special napkins designed for furniture care.



How to glue a wooden veneer on an MDF panel with your own hands, see the next video.
The comment was sent successfully.