Features of mosaic grinders

Finishing porous surfaces made of concrete and other building materials is quite laborious and messy. The use of machines not only reduces the working time, but also copes with any surface defects with much greater efficiency. That is why mosaic grinders are in great demand in the market for tools and materials.
Features and purpose
The main purpose of the mosaic type grinders is to process porous concrete substrates and mosaic substrates, and the tool is also capable of grinding stone coatings. They successfully cope with pre-treatment, which includes the elimination of small cracks, sagging and plane leveling, and with the grinding of reinforced material.
In addition, the mechanism is often used to remove paint and varnish coatings on substrates of any kind. The purpose of such units is from the opening of pores in concrete in order to provide more effective penetration into the structure of the surface of the soil, thereby ensuring the durability of the finish. As a result, monolithic coatings become waterproof and resistant to acid-alkaline solutions, withstand even the most difficult equipment, while the appearance of the product is significantly improved.




It is worth dwelling in more detail on the design features of the units. The basis of the machine is a special supporting frame - it is used for fastening functional units. In most cases, manufacturers of such tools give preference to collapsible units, which greatly increases the technical and operational features of the mechanism. The operator contacts the rear of the frame, which houses the infrastructure control cabinet and stick.
If desired, the handles can be folded ergonomically together with the cabinet. A power unit is mounted in the center of the installation, which is attached using brackets, but the position of the engine can be changed at any time if necessary.
All the necessary parameters can be set by adjusting the belt tension.


The front of the frame contains the main functional infrastructure, which is driven by a V-belt drive through the sanding beam. All basic operations are performed with special diamond tools. They are enclosed in a metal body and differ in the degree of abrasiveness, shape and binder filler. All models operate in approximately the same way.
The machine moving on a concrete base performs surface grinding due to continuously moving cutters in a circle, fixed on the frame in a horizontal position. By changing the speed, as well as the direction of such rotation, you can achieve not only perfect smoothness, but also cut various flat patterns on it - mosaics.


Grinding must necessarily be wet, therefore, the design of such a tool involves periodic moistening of the treated surface with all kinds of aqueous compounds or organic solvents. After that, it remains only to fix the cutter on the shortened vertical shaft and connect it to the gear reducer, and through it - to a special drive motor.This entire structure is attached to a shock absorber frame and reinforced with support wheels, a cold water reservoir and a handle. Differences in design features are due to the peculiarities of the connection of individual parts of the circuit and the nuances of the operation of the unit.
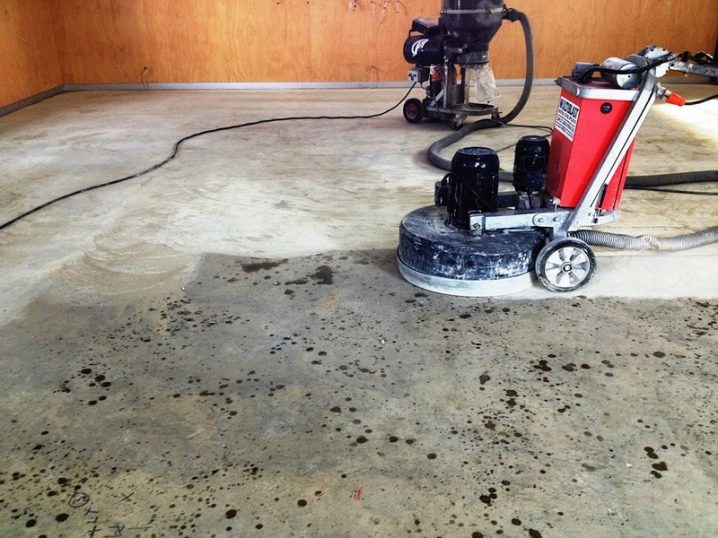
Views
Hand-held machines are very common, which are easily moved over the surface by the operator. These tools are optimal for small surfaces and occasional use. They are equipped with diamond cutters, which rotate towards each other during operation. The number of traverses can be one or more. Single traverse products are designed for use in confined spaces. With an increase in the number of traverses, a greater efficiency of the equipment is achieved.


For work with large bases, it is worth purchasing self-propelled models, but they are optimal only if the surface is smooth and free of obstacles. Self-propelled cars are equipped with a small chassis and an independent electric drive of the drive wheels, which provide a change in the operating speed from 1 to 10 m / min, and this transition is carried out as smoothly as possible.
This feature allows you to minimize the number of machine passes for each fragment and achieve the required cleanliness. The number of working heads in such mechanisms is 2 or 3. Such machines during operation are connected to the water main, although the device also has a small portable reservoir. The instrument is controlled remotely via the remote control, but the system itself is quite robotic and does not require any intervention from the operator.


There are other grounds for classification as well. So, according to the type of engine, electric drives and gasoline engines are distinguished. The former are optimal for processing internal surfaces, and the latter for external ones. According to the design of the lifting unit of the head, the mosaic grinder can have linear and angular movement of the cutter. The tool of the first type moves rather slowly, but the wear of the working community is also much slower. Machines can also vary in performance, engine power, mass and parameters of cutters.
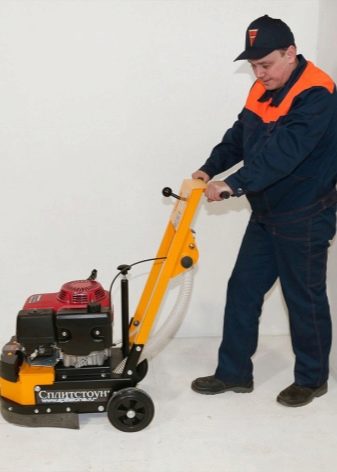

Model rating
For grinding and finishing of concrete bases, various types of tool models are used. However, users note that the manual and self-propelled mechanisms of the Splitstone company are of the highest quality and most practical. They are characterized by a fairly high efficiency and durability. In the rating of tools, among the top manufacturers there are products from Husqvarna, as well as Grost and others. Among the most budgetary models are domestic products "Caliber", TCC and MISOM, as well as Ukrainian machines of the SOM brand. It is worth dwelling on the most popular models.
- Manual GM-122. Splitstone's GM-122 single traverse is used for small surfaces with limited maneuvering. The model is equipped with a 4 kW engine with a working width of approximately 30.5 cm. The traverse moves at a speed of 1100 rpm. The plant's productivity is low - only 60 m² per work shift. This indicator is calculated for concrete M300 with a removal height of 1 mm. The weight of the tool is 120 kg.


- Manual GM-245. This is a two-door machine with a fairly high performance from the Splitstone company. It is needed to process large areas with an increased degree of accessibility without pronounced differences in plane. This model is strengthened by an engine, which is presented in two versions - 5.5 kW or 7.5 kW. The processing strip is 60 cm, and the rotation speed of the traverses is 1000 rpm. The plant productivity is 100 (140) m² per shift. The mass of such a machine is 175-180 kg.


- Self-propelled HTC 1500 ixT. This machine is used for grinding large and small surfaces.The mechanism works absolutely silently and in one shift it processes about 30 m² of the working surface with a swath of 145 cm. The machine is quite maneuverable, in case of collision with an obstacle it can turn 180 degrees. The unit is equipped with 2 engines, each has a power of 11 kW, power is supplied either from a battery or from an alternating current network.


Selection Tips
When choosing a mosaic grinder, you need to pay attention to the size of the working surface. For quick grinding of the floor, it is better to use small plates. The motors must have a power of at least 4 kW, and the speed must not exceed 1500 rpm. When choosing, the specifics of setting the traverse and the selection of consumables are very important, the work process is based on the use of abrasive parts, which are diamond segments. When buying such material, you should clearly understand the difference between soft and hard segments, which is as follows:
- solid ones provide a special, rather intense effect, while their functioning affects the operation of all other components of the equipment, as well as the electric motor, to which vibration is transferred;
- soft parts do not so much affect the design features of the unit, and when abraded, they provide only the finishing of the concrete surface.




Important! In addition to diamond segments, care should be taken to purchase a floor surface lubricant that can reduce the impact of material resistance on the tooling. In addition, segment holders, as well as protective panels, couplings and carbon brushes, often fail - it is better to buy spare parts in advance.
User manual
Before using a mosaic-type grinder, it is imperative to make sure that all its mechanisms, assemblies and parts are working, check the reliability of the fasteners, and also clean the surface to be treated. After that, the machine is installed on the surface to be treated, a traverse is set in it and all the necessary communications are connected - a special pump and a hose with a water supply mechanism to moisten the surface. Grinding on a typewriter should be used for concrete screeds, the height of which exceeds 3 cm. The maximum allowable height difference is 5 mm.
If the surface has ridges and depressions above this parameter, then the concrete surface must be leveled first. Processing, as a rule, is carried out 5-6 days after the screed is poured, and the final grinding is carried out a month later.

Before the start of grinding, the concrete coating is treated with a special sealant. It completely closes all existing pores in the material. For work, most often they take discs with a grit index equal to 40. The second grinding is performed with discs with a grit size of about 400, and for finishing grinding, discs with an indicator of 2000-3000 are needed. At the end of grinding, the concrete should be coated with polymer compounds, which increase the surface's resistance to various kinds of mechanical stress.

After finishing work, turn off the engine and make sure that there are no extraneous noise and increased vibration. The machine is lowered into the working position rather slowly. Please note that diamond elements should begin to come into contact with the work surface only when the motor picks up the required speed. The unit should be controlled smoothly, without any sudden movements. At the end of the work, the grinder should switch off.

From time to time, the machine needs to arrange a technical inspection in order to check the serviceability of the fixing components of the protective apron and other internal elements of the machines. The equipment should be regularly cleaned of dirt. The traverse must be checked for firmness of fixation, and the faceplate must be checked for correct attachment. It should be located strictly perpendicular to the axis of the shaft.
For how to work with a mosaic sander, see the next video.
The comment was sent successfully.