Self-tapping screws for sandwich panels
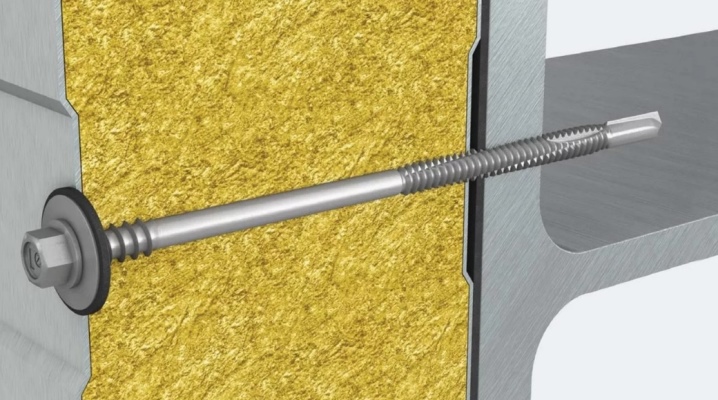
Self-tapping screws for sandwich panels are an important component of the correct fastening of finished building modules. Hex-head hardware for concrete and metal is easy to pick up using the size table, they securely hold the panels, and are quite easy to install. A detailed overview of all properties and product requirements will help you learn how to choose a self-tapping harpoon and other options suitable for fastening sandwich panels.
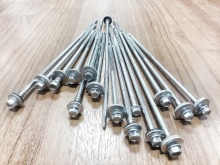
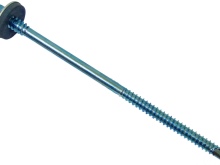
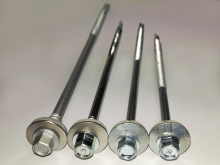
Self-tapping properties
Self-tapping screws for sandwich panels are a special type of multi-component fasteners that can securely fix in materials with different densities. The cladding modules themselves consist of an insulating layer and external support walls. Their installation is carried out on a prefabricated frame made of metal profiles, wooden battens, as well as directly on a smooth concrete base.
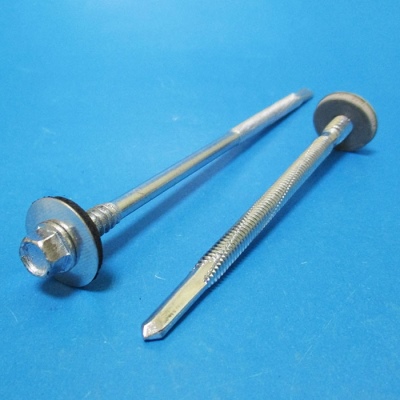
Several main properties can be distinguished: which self-tapping screws that fasten the sandwich panels must have.
- Fixation reliability. Regardless of the material of the base, the fastening must be strong.
- Security for the decorative layer. The hardware should not damage the panel when screwing in.
- Tightness of the connection. Protection against penetration of water into the drilled holes. For this, a special rubber washer is installed in the structure. There is a special groove under the head for it.
- Climatic and weather resistance. The metal must be protected from corrosion, not change geometry when the temperature drops or rises.
- Reliable fixation in the screwdriver bit. This makes installation quick and easy. Achieved by increasing the head height up to 5 mm.
- The presence of a double thread. It can have a variable or constant diameter; it differs at the base and at the end.
- Possibility of staining. Either with a washer or powder method.
- Service life up to 30 years. These indicators are achieved due to the highest possible weather resistance.

All self-tapping screws for sandwich panels have a rod, a pointed or drill-shaped tip, a hexagonal head on the outside and a thread applied at the base and at the end of the product. The middle remains smooth, during the screwing process, with the correct selection of the standard size, it is completely hidden inside the sandwich panel.
Varieties and sizes
For sandwich panels, self-tapping screws of the "harpoon" type are used with a sharp threaded tip, a smooth center of the rod and an enlarged threaded part at the base. They are usually divided into groups according to the purpose or type of coverage. Each self-tapping screw used during installation must correspond to its class.
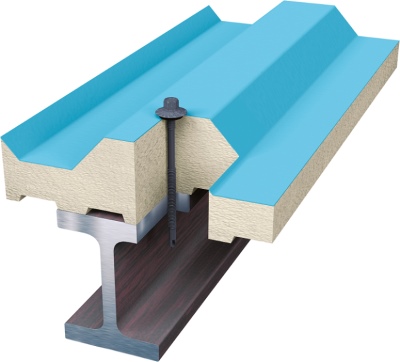
Their main varieties can be distinguished.
- On concrete. They are characterized by a variable thread in the lower part, as well as a mismatch in its pitch.
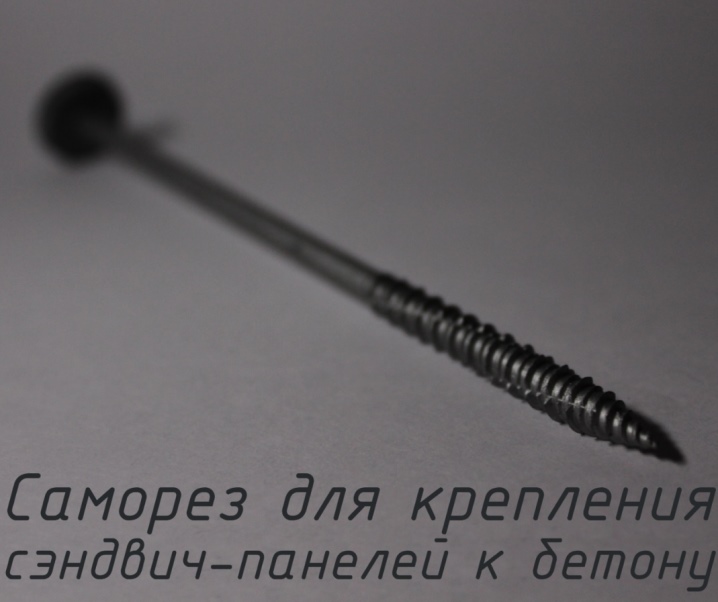
- Roofing. Self-tapping screws made of stainless steel or carbon steel with a synthetic rubber seal are suitable. The lower thread has a shallower pitch and a drill bit. They will also be optimal for fixing sandwich panels to metal structures.
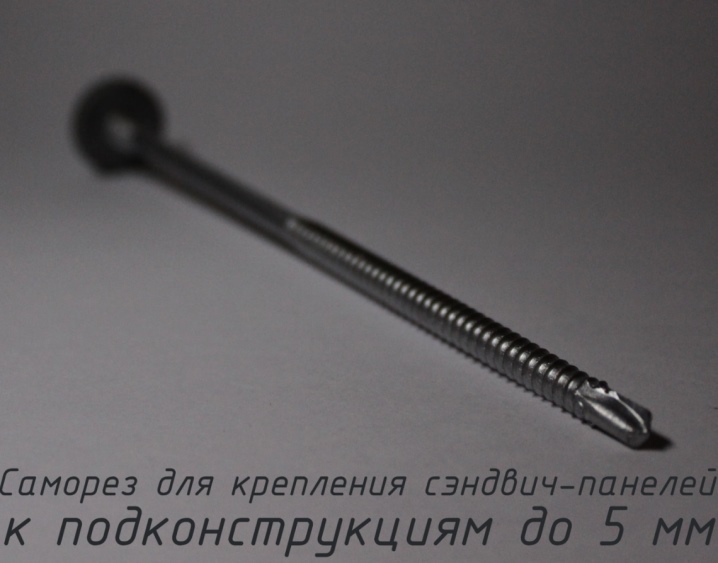
- Wood. They can be made of uncoated or galvanized ferrous metal. They are distinguished by an increased thread pitch.
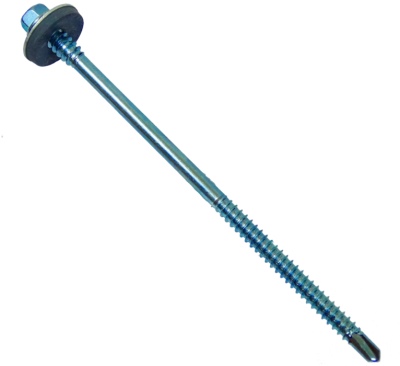
- Galvanized. Self-tapping screws with a protective layer applied by galvanizing. Not the most durable, but good at protecting ferrous metal from corrosion.
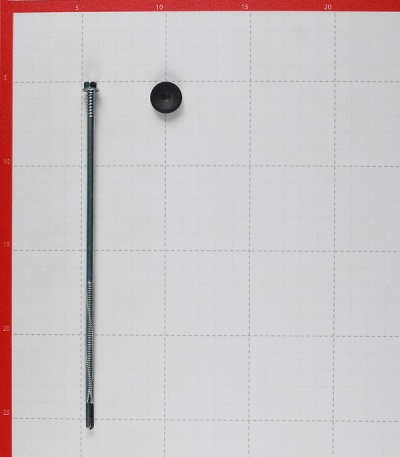
- Nickel plated. Such a coating is very decorative and provides full moisture resistance to the metal. Nickel is highly resistant to wear and tear and is almost impossible to damage.
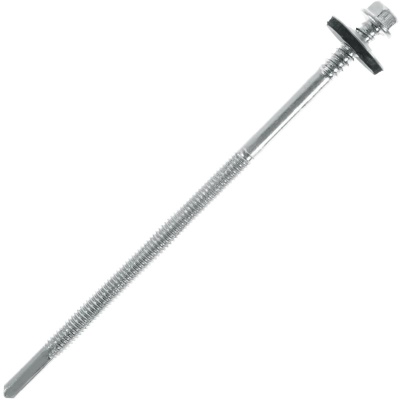
- Copper plated. Rare options. Such self-tapping screws retain their properties even after repeated use, they are not afraid of corrosion
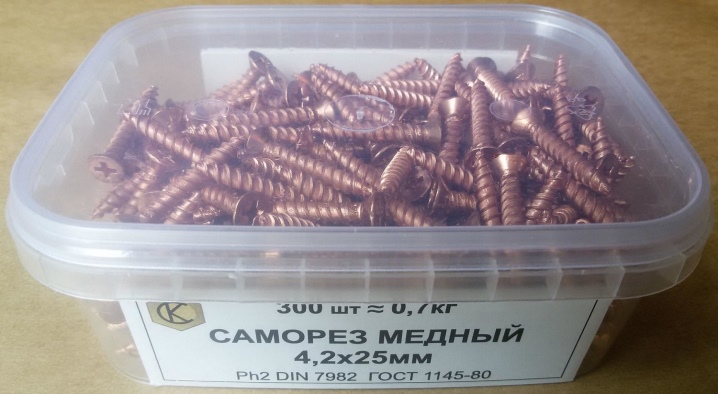
- Cadmium chrome plated. Similar to galvanized, but coated with a different chemical element. Corrosion and weather resistance is high.
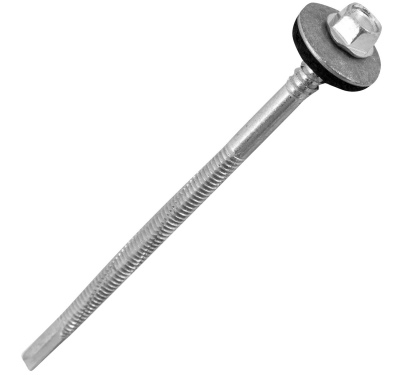
- Coated with tin. The best option for obtaining good adhesion to the surface of the sandwich panel. For tin, this ability is much higher than that of other metals.
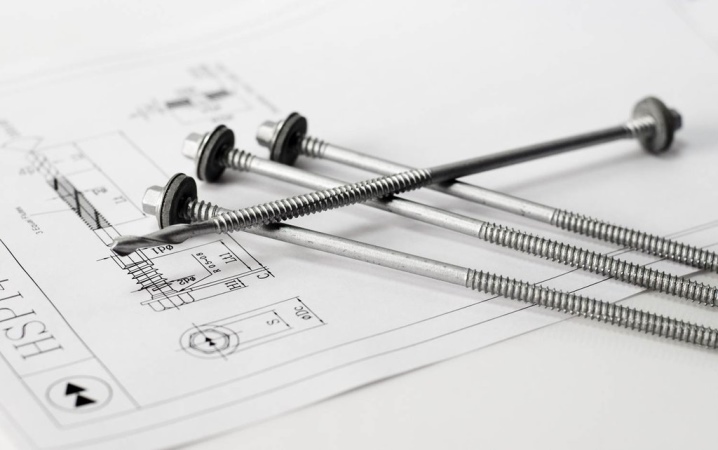
A special table will help to understand exactly what size of a self-tapping screw is needed for a 150 mm thick panel.
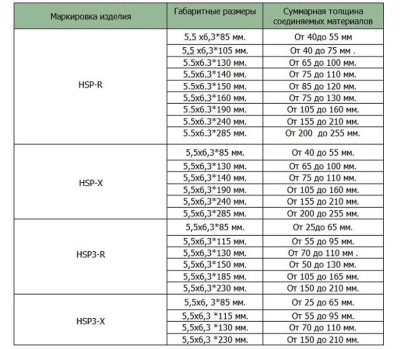
GOST standards
For fastening sandwich panels, self-tapping screws are used in the size range from 80 mm to 350 mm. The calculation of a suitable option is determined simply: the thickness of the panel and the frame is summed up, and then an increase of 5 mm is made. The allowance provides a secure hold during thermal expansion of materials. Usually the length of the product exceeds 100 mm.
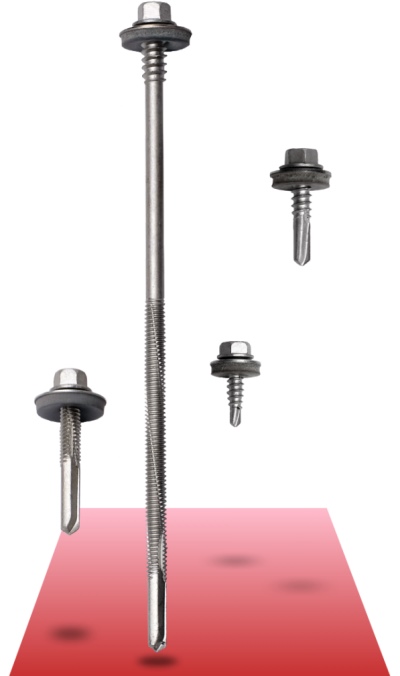
Product weight may vary. For the most popular diameter (thickness) 6.3 / 5.5 mm, the weight at a length of 130 mm is 22 g. The section is indicated for the base and end of the rod.
The permissible thickness ranges from 2.5 to 8 mm.
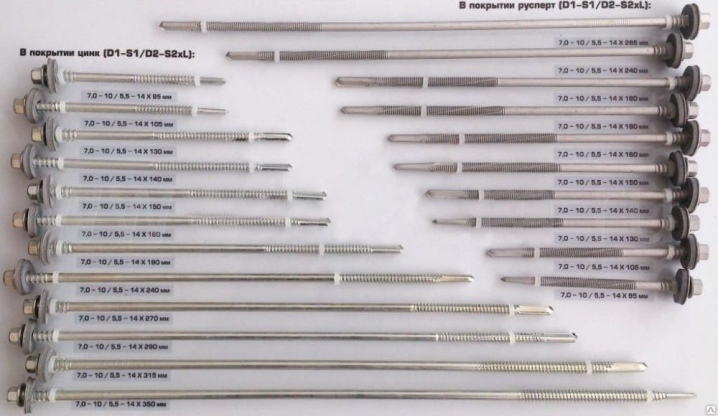
Requirements for self-tapping screws for sandwich panels are standardized in accordance with GOST 11652-80. The products are supplied with a sealing washer - metal at the top and rubber at the point of contact with the material. According to the standard, it is allowed to manufacture plastic self-tapping screws, a hole for them is drilled.
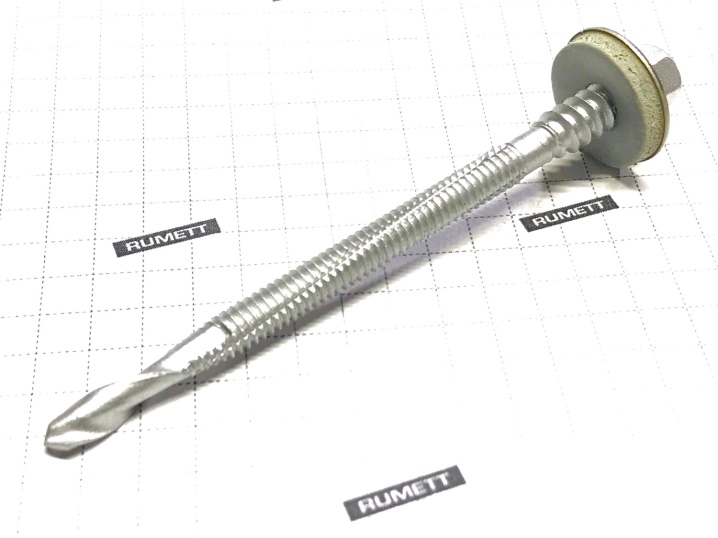
Criterias of choice
When choosing self-tapping screws for sandwich panels, several important parameters should be taken into account.
- Appointment. In addition to separation by the type of base (it can be metal or concrete), self-tapping screws can be wall and roofing, as well as intended for additional elements.
- Plastic. It affects the maintenance of the tightness of the screw connection under the influence of thermal expansion. This property is possessed by hardware made with the use of tempering technology. It is provided for by the GOST requirements, but is often forgotten by Chinese and other Asian manufacturers.
- Thread location. Specialized self-tapping screws for sandwich panels include only those fastener options that have an increased diameter thread just under the head. It is she who holds the outer skin of the panel, preventing it from creasing. The optimal thread size is considered to be from 7.4 mm at the top, otherwise the tightness of the fit will be too low.
- Washer diameter. Special self-tapping screws for sandwich panels are supplied with washers with a diameter of 16 mm with a synthetic rubber seal ring included. This combination provides a reliable sealing of the joint. It is optimal if the seal has a thickness of 3 mm, and the washer itself is made of aluminum - it is more ductile than steel.
- Type of protective coating. The most popular solution is considered to be products processed by the method of electrolytic galvanizing. But if you need to choose a really durable option, you should look for products with Durocoat, Xulan, Ruspert coating. All of them are much better at coping with their tasks.
- Manufacturers. Not all brands on the market make the same quality products. Among the noteworthy manufacturers are Scorpio, Harpoon, SFS intec. For any product, the seller must have a certificate, as well as other necessary documents. It is worth paying attention to the container - usually it is a cardboard box, which also contains the manufacturer's initial data.
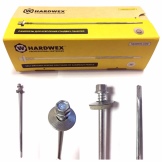
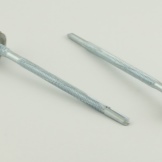
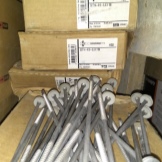
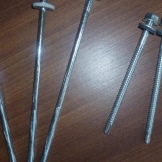
The calculation of the consumption of self-tapping screws is no less important than the study of selection criteria. Regardless of whether it is fixed to metal or concrete, the number of elements is calculated in advance based on the size of the sandwich panel, the frequency of the lathing.
Usually, 4 self-tapping screws are needed for a module up to 4 m long. With each increase in the length range by 2 m, 2 fasteners are added.
For more information on self-tapping screws for sandwich panels, see the next video.
The comment was sent successfully.