How is crumb rubber produced?

The service life of car tires is short-lived - in a few years after the purchase, tires must be replaced, while the number of used cars annually increases by at least 10-15%. That is why environmentalists around the world are faced with the task of recycling used tires.
In our review, we will tell you more about the processing of this material and the manufacture of crumb rubber.

Expendable materials
Much has been said about the roads in our country - the Russians themselves call this problem nothing more than “trouble”. Hundreds of kilometers of worn out asphalt pavement, pits, bumps cause premature wear of tires, which accumulate in garages, cellars and on the loggias of our compatriots. As they say, it's a pity to throw it away, and there's nowhere to put it.
However, this problem has long found a practical solution. In some regions of our country, there are specialized factories for processing wheels in production conditions. Automobile tires are crushed into crumb rubber. This product serves as a raw material for the manufacture of high quality outdoor and floor coverings. The material is characterized by resistance to wear, good shock absorption and durability.
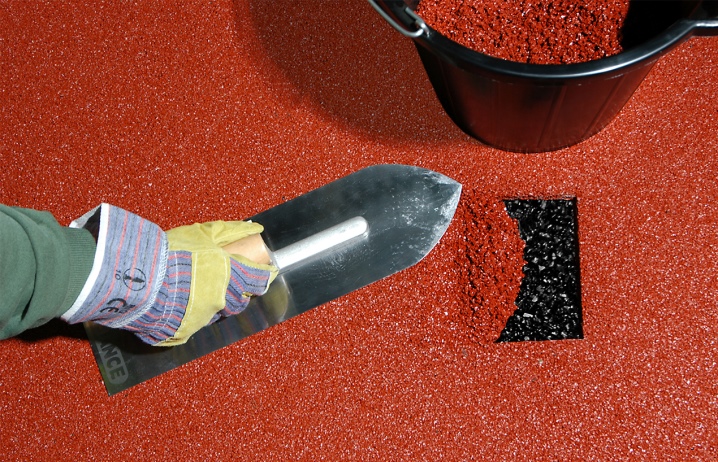
Products made of crumb rubber have a fairly high density, while retaining plasticity due to the introduction of polymer binders into the raw material. They have a slight relief, due to which, even after wet cleaning and rain, the coating remains rough - this makes it possible to carry out any active actions without the risk of slipping and getting injured. Rubber granules have the same benefits as rubber itself.
In addition, according to the manufacturers, the crumb is absolutely non-toxic, so the use of such materials does not cause any harm to either people or pets.


In addition to the floor and road surface, the crumb is also used to make:
- speed bumps;
- chippers;
- curbs;
- figurines for decorating sports grounds;
- substrates that protect goods during transportation;
- some types of soundproof finishing materials;
- bitumen-rubber mastic;
- dielectric products for the electrical industry.
The granules are also injected into the asphalt, resulting in a fairly dense and durable coating.




To create crumb rubber, you can use not only tires, but also use semi-finished products from synthetic or natural rubber, as well as rubber shoes, bumpers, transport belts and other rubberized products.
However, the most popular is the use of a car tire, it is no coincidence that this product "flies away like hot cakes" - this is explained by the exceptional performance parameters of car tires.

Grinding equipment
Let us dwell in a little more detail on the minimum set of equipment required for the highly efficient processing of used car tires into fine-grained crumbs.
Board removal machine
This is one of the basic units required at the very first stage of technological processing. The functionality of the machine is reduced to removing the bead rings from the tire. Depending on the design features of the equipment, the seat rings can be removed by punching, cutting or pulling out. All methods are equivalent, none of them has a pronounced advantage over all the others.

Subsequent processing of the removed rings is carried out in crimping installations, where the metallized base is simply squeezed out of the workpiece. The rubber remaining after processing is crushed in the remaining mass of raw materials.
Tire shredders without bead
This group of machines includes hydraulic shears, all kinds of mills, shredders, tape cutters, as well as roller grinding mechanisms.
Tape cutters and shears cut the tire into large pieces. Further, the raw material enters the shredder, where it is processed to a coarse fraction. At the final stage, the roller unit brings the rubber fragments to the required granule size.

Separators for removing inclusions
All chopped up metal cord residues are removed from the resulting crumb by a magnetic separator. This device has a simple principle of operation - a high-power electromagnet simply pulls out all metallized waste from the workpiece and transfers them to a special hopper.
Removal of fragments of textiles is carried out in an air separator, working on the principle of cyclones, when an air jet blows out all the textile fluff.

Vibrating screens
Vibrating screens are part of any production equipment for the processing of tires. They represent a table with numerous holes according to the size of the fraction, as well as a mechanism that provides the necessary vibration.
The complete set of the production line should include at least two units: one for coarse, the other for fine cleaning. The first device separates large, incompletely processed fragments, the second separates conditioned crumb.

In the course of factory processing of wheels, belt conveyors are used, they are necessary to move fragments of tires, as well as the finished product from the place of technological operations to the place of processing. Many manufacturers install screw conveyors, and automated waste tire recycling lines are often equipped with hoppers, process controls and safety modules.

All of the above equipment must certainly be present on any line for processing used tires into small crumbs. In this case, the total number of installations and machines directly depends on the scale of production, as well as on the requirements for the final type of material obtained.

Manufacturing technology
In industry, there are two basic methods of producing crumbs from old wheels: shock-wave and mechanical. Let's dwell on them in more detail.
Shock wave
This technique of crushing car tires and other rubber raw materials to a state of fine crumb has been developed relatively recently. In this case, processing is based on freezing blanks at ultra-low temperatures with their further crushing by a powerful shock wave. Usually, cryogenic chambers are used for freezing, and a powerful shock wave is created by a special electrical installation or a small portion of explosives.


This technology requires expensive equipment, so this production method is economically beneficial only for the largest enterprises with huge volumes of processing of raw materials.

Mechanical
This processing method is considered standard technology. It is used everywhere, even in the smallest industries. The essence of this process is a step-by-step mechanical action on rubber blanks in order to obtain a certain fraction of rubberized crumb at the output.
There are several technologies used for mechanical processing of tires:
- crushing and cooling of rubber raw materials;
- at high temperatures;
- with a normal temperature background;
- using the "ozone knife";
- with the pressure of raw materials under a powerful press.

The most widespread is crushing at ordinary temperatures. This technology makes it possible to obtain automobile crumb even in the conditions of small enterprises, and the output fraction can be absolutely any - from large fragments to a dusty substance.
The process of processing tires mechanically can be roughly divided into several main stages:
- At the very beginning of the technological process, tires are sorted according to their size - this will allow in the future to adjust the machines for wheels of certain dimensions. Crushing itself begins with cutting out bead rings on specialized equipment.
- In the second stage, the tires are cut into medium-sized belts with hydraulic shears.
- Further, the raw material enters the shredder, where even the largest fragments are crushed to the size of chips - 2-10 cm².
- The resulting blanks undergo further processing, during which they are crushed to a fraction of the desired size. At this stage, a mill with sharp quadrangular knives or other mechanisms that can withstand increased loads are used.
- At the final stage, the crumb should be separated directly from other by-products, that is, textile residues and steel cord.
- The material is almost ready for use, it remains only to pass it through a vibrating sieve - it will divide the resulting rubber crumb into separate fractions.
Depending on the features of the equipment used, the number of technological stages can be either increased or decreased.

Owners of summer cottages who do not plan to produce rubber crumb on an industrial scale, but just want to make an inexpensive and practical coating for garden paths with their own hands, can grind the tires on their own. Procurement of raw materials, most likely, will not cause any difficulties - you just need to walk around the neighbors. Surely, many of them will gladly take out tires from the barns.
At home, they mainly use mechanical cutting of old tires, the freezing option for the house is unprofitable, since in this case you will have to buy a low-temperature chamber. In everyday life, they often resort to mechanical cutting and further bringing to the desired fraction in household grinders and crushers.

To create a colored crumb, a laprol-based coloring glue is added.


A visual overview of the mechanical transformation of old tires into crumb rubber is presented in the following video.
The comment was sent successfully.