All about crumb rubber tiles

Finely ground rubber tiles have unique characteristics. In terms of its comfort, safety of use and aesthetic appearance, it simply has no competitors among materials for covering adjoining territories, sports grounds and much more.
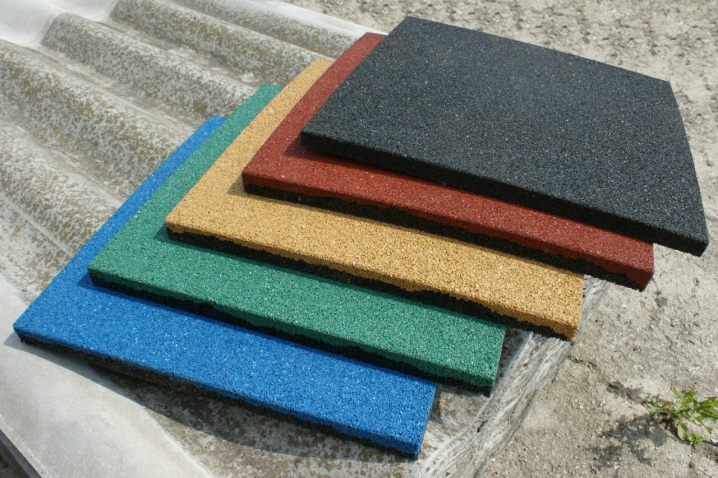
Advantages and disadvantages
The widespread use of crumb rubber tiles indicates that it has a huge range of advantages and excellent performance characteristics. Like any material, it has its pros and cons.
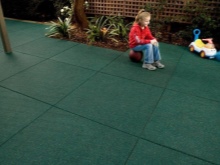


Consider the positives.
- A varied assortment of colors, which allows you to decorate the site in any style.
- The panels are available in different versions - water permeable and waterproof. This makes it possible to lay it both indoors and used for outdoor coatings.
- The high durability of rubber crumb products allows them to be used intensively for at least 5 years, and under normal conditions - at least 15.
- Safety and reduced injury in sports. Rubber panels are springy, and if you fall, the risk of injury is much less than on other types of surfaces. Thanks to this property, they are the main material for the arrangement of playgrounds and sports grounds.
- Environmental safety of crumb rubber panels. Materials that are harmless to humans are used in the production, so they can be used for almost any need.
- The rubber cover has an anti-slip effect, which significantly reduces the risk of injury during ice, snow or rain.
- Tile installation and dismantling is not difficult to carry out. It can be easily removed and stowed in another desired place without losing the shape and reliability of the products.
- Such a tile copes well with adverse weather conditions in the form of frost, precipitation, sudden changes in temperature and others, while maintaining its strength and aesthetic appearance.
- No special effort is required to leave. You just need to wash it with any detergent and it will again look like it’s just from the store.
- There are no special requirements for transportation.
- Since the rubber coating is highly resistant to UV rays, it will look like new for a very long time.
- The production uses old rubber tires, which allows them to be disposed of in huge quantities, while cleaning the environment. This is a big step towards protecting nature.



Now let's move on to the negative points. Like all rubber-based products, these panels burn well. But since in most cases they are used for outdoor coatings, this factor is not so critical as to refuse to use them.
The next drawback is the rather high cost. The price depends on many nuances such as thickness, color, components and other factors.
If we compare the list of pros and cons, then the second is much less. This makes crumb rubber tiles very popular, and in some areas simply uncontested.



Production methods
To make tiles from crumb rubber, you will need special equipment and premises.The latter should have an area of at least 100 m2, moreover, heated - during the cold period, the temperature in it should not fall below +5 degrees Celsius.
The main focus is on the means of manufacturing rubber panels. The initial amount that will be required to start will depend on their quality and power. You can buy everything separately, but it is better to purchase the complete line as an assembly. This will facilitate and unify the process.

Now for this, various kits are offered, but at least you will need:
- mixer - for mixing various components;
- ovens - for drying products;
- hydraulic press - to form products;
- forms;
- conductor - for punching holes for connecting elements;
- forming table and fixing stand.
This is the most necessary equipment for the deployment of production. With its help, it is already possible to start producing coatings based on crumb rubber of various thicknesses and sizes.



Currently, slabs are made using three different methods.
Cold
This method is considered classic, it was developed by the very first and is already considered obsolete.
The process consists of 2 stages. Thoroughly mixed in a mixer, the mixture is poured into selected forms, located on a special table. Then there is pressing under high pressure (about 5 tons) and transfer to a drying oven, where at a temperature of 55-60 ° C the products are dried for at least 6 hours. Then the molds are disassembled - and the product is ready for use.
This method has the following advantages: the equipment is widespread and available, and tiles can be produced on a small scale.
The disadvantages include the need to constantly monitor the process, a fairly large percentage of defects and a high price.

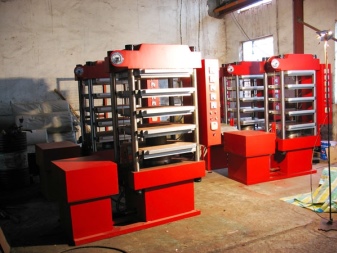
Hot
The hot pressing method is considered to be the most progressive. The first stage coincides with the previous method, and the difference is in pressing the panels. The prepared composition is placed in metal molds, heated to a temperature of + 120 ... 220 ° C and simultaneously pressed.
Based on the parameters of the product, the process takes from 3 to 20 minutes. During this time, the adhesive spreads evenly over the mixture, creating a more reliable bond between the rubber crumbs. This technology makes it possible to obtain tiles with better characteristics than with the cold method.
Advantages: a wide range of products, low cost, excellent quality of panels and a small percentage of defects in production.
There are also disadvantages: the equipment is quite expensive, and the workers must have the appropriate qualifications.


Thermochemical
This is the newest method that allows you to get products that meet all requirements, even the most stringent ones. The difference from the first two technologies is that, if necessary, it is possible to set the required parameters. In other words, products from the same material can have different indicators of density, hardness, elasticity and other parameters.
The process goes like this:
- crushed rubber is mixed with glue;
- depending on the requirements, the necessary components are added to the panels;
- placement in molds, heating and pressing takes place (it may take from 2 to 10 minutes).
Upon completion, we receive products of the highest quality, ready for use.
The advantages are the same as with the hot method, plus the ability to manufacture specialized types of coatings. The disadvantages also coincide, and in addition, you need to constantly monitor the production process with special attention.


What happens?
Crumb rubber tiles vary in thickness, size and shape. The most popular are rectangular or square, but also available in the form of "paving stones". Sometimes you can find exotic types of rubber panels in the form of "puzzles", equipped with special fasteners around the perimeter.
The shape does not affect the parameters of rubber tiles, and it is worth choosing it based on the future purpose.
The surface of the panels can be smooth or ribbed, with various patterns, which, in addition to the anti-slip effect, allows you to give the walkway or sidewalk an unusual look.
There are many color solutions, and the most popular colors are brown, black, terracotta, red, yellow, green.


Dimensions and weight
All crumb rubber tiles are manufactured in accordance with TU 2533-001-0171450779-2012, which contains all the requirements for products. The dimensions of the panels can be varied, they are found from 200x100 mm to 1000x1000 mm, of various thicknesses and weights.
The most demanded tiles are 500x500 mm. Depending on the thickness, they are placed either on a hard surface (10-30 mm), or on a loose base (40-45 mm) outside.
Dimensions, mm | Weight, kg |
500x500x10 | 2,25 |
500x500x16 | 3,5 |
500x500x20 | 4,25 |
500x500x30 | 6,4 |
500x500x40 | 7,4 |
500x500x45 | 8 |

All rubber tiles can be used both as sidewalk and garden paths, and they also proved to be excellent as a street covering in yards.
Laying technology
Such material is laid in several ways.
Tiles with a thickness of 40 and 45 mm are mounted on a base made of bulk materials. The process is very similar to laying conventional concrete. To do this, prepare a sand and gravel pillow of 10 cm, tamp it very well. The perimeter of the tracks or area is marked with a curb made of both rubber and concrete. After this, the plates are laid. The panels are attached with special locks to each other.
Mounting on a solid base suitable for panels with a thickness of 6-45 mm using polyurethane adhesive. The substrate is cleaned of dust. Before gluing to the surface, the base is primed. Glue is applied with a spatula, then tiles are glued starting from the middle.
After installation, you need to wait about 48 hours - at this time, walking on the panels is undesirable. And also you need to ensure that air does not get under the tiles during installation. If he suddenly got there, then you can remove it by pressing firmly on the product from the center to the edge.
When installing on a solid base, you need to consider the slope so that water does not linger on the surface.
When laying on the ground, a slope is not required - the water will leave naturally through the tiles and then through the drainage into the soil.


You can learn how to choose the right rubber crumb tile from the video below.
The comment was sent successfully.