Features of low pressure polyethylene
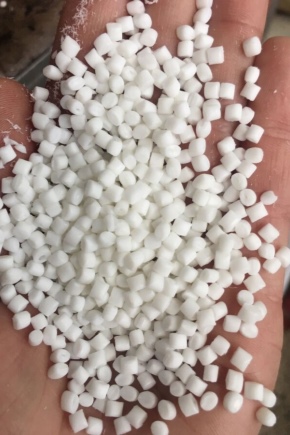
If you look around, you can see a huge number of different things made of polyethylene - these are all kinds of bags, and film packaging, flower containers and boxes, game modules and thousands of other plastic goods. Low pressure polyethylene is widely used in the household and industrial sector. We will talk about its operational characteristics in our article.

What it is?
The abbreviation HDPE (HDPE) means low pressure polyethylene. Material is high density plastic... It is obtained during the polymerization of ethylene under reduced pressure. The polymer under such conditions is hard and hard, relatively transparent. Molecular cells of this material have a special structure with an increased level of intermolecular bonds. This makes HDPE more dense than other types of polyethylene, which is why it is called "high density polyethylene" (HDPE, and the English version is HDPE).
The HDPE manufacturing technology involves the polymerization of ethylene under a pressure of 0.2-0.5 MPa at a temperature of 80 degrees. The reaction takes place with the participation of an organic solvent with the addition of organometallic catalysts. The density of such polyethylene at the outlet is 959-960 kg / m3, the molecular weight corresponds to 80-800 thousand, and the degree of crystallinity varies within 75-90.



Usually HDPE is used as a raw material for the further production of household and industrial items.
The main technological difference between low-pressure polyethylene and high-pressure analogs is the difference in polymerization parameters. Different levels of pressure and different heating give the polymer fundamentally different physical characteristics that have a direct impact on the scope of use of the material.
You can tell the difference between these films tactilely and visually. So LDPE is smooth to the touch, a bit like wax.
It is distinguished by high plasticity, such a film can be given a large thickness - in this case, it is used to form sufficiently dense products, including dishes.



HDPE can be distinguished by its ability to rustle, such a film resembles paper and wrinkles, while exhibiting exceptional tensile and tensile strength. It is no coincidence that practical bags made of this material have long become a must-have item in stores. Their handles do not stretch until the ultimate strength is reached, and this limit is quite high, but when passing through the critical level, the package will break.
The high strength characteristics of low-density polyethylene are widely used in many other areas of production, in addition to the manufacture of packaging materials.
They are in demand in the production of roofing elements, the assembly of greenhouses and boats.



Main characteristics
The following technical and operational parameters of low-pressure polyethylene can be distinguished:
- absolute hydro and vapor tightness;
- low water absorption;
- good plasticity, extensibility;
- reduced density index (0.93-0.96 g / cm3);
- melting of the material begins when heated at 110-130 degrees, which is why containers made of this polymer can easily withstand steam sterilization and heating in a microwave oven;
- chemical inertness - resistance to technical solutions and oils;
- the strength of intermolecular bonds gives the product special wear and tear resistance;
- high weldability when performing chemical, gas and heat welding;
- transparency;
- lightness - even the most massive barrels and tanks are much lighter than analogues made of other polymers;
- dissolves in the environment of aromatic hydrocarbons when heated to a level of 120 degrees and more.


It can also be noted that the granules of this polymer can be easily processed by any available methods used for plastics.
You should be aware that HDPE (High Strength Polyethylene) is considered the hardest polymer among all other types of plastics made from ethylene. And as you know, in any plastics, an increase in density causes an increase in the parameters of chemical resistance and wear resistance. Hence the differences between low-pressure plastic and other types of polymer raw materials - LDPE and LDL. Compared to LDPE, the polymer of this brand has:
- greater rigidity, but less transparency;
- greater strength and strength, but at the same time less resistance to deformation under the influence of low temperatures;
- high melting temperature, which allows for steam sterilization;
- less vapor permeability and hydroabsorption;
- high resistance to aggressive solutions.
Advice: when hitting any hard surface, objects from PVP emit a rather sonorous sound.
Thus, it is quite easy to distinguish them from products made of plastics of other categories. This property is often used to evaluate material.


Varieties
High density polyethylene sheets are produced in different categories depending on the production technique used. In the raw material, the presence of all kinds of impurities is allowed, which can be both precipitation of accompanying substances and the main participants in the reaction being carried out.


Suspension
Such polyethylene may include chemical stabilizers. During the polymerization of ethylene, they contribute to the formation of a suspension substrate from the granulate. Usually this includes alcohols, oxides of light metals, slightly aggressive acids, as well as certain types of clay.
The output plastic is more homogeneous and of high quality; destruction of the structure and the presence of weak zones are uncharacteristic for it.


Solution
In most cases, it contains residues of catalysts that are involved in polymerization under high temperature.


Gas phase
The structure of such polyethylene is composed of fragments of ether components, as well as gases. And of all the listed varieties, it has the weakest structure, since it is relatively heterogeneous and contains less wear-resistant areas.


Applications
The presence of extraneous components, including catalysts, determines the widespread use of HDPE for industrial purposes, where strength and strength are considered more important criteria than toxicity and environmental friendliness. Only a small part of the finished product is used to meet household needs.
The scope of use of the material directly depends on the method of processing polyethylene. In accordance with GOST, the following areas are distinguished - extrusion, injection molding, as well as blow molding and rotational molding.
Each of them at the output gives products that differ in appearance and technical and operational characteristics.


Extrusion
This method involves the production of polyethylene from polymer raw materials by forcing the finished material through the forming cone - the hole of the extruder. The method makes it possible to produce packaging bags, conveyor belts and air-bubble belts for packaging goods, as well as electrical wires and nets of various types. (household, agricultural and construction).There is a wide demand for material for the production of sewage pressure pipes, drainage and gas pipes of different diameters. HDPE retains its characteristics when exposed to temperatures from -60 to +100 degrees.
Plastic does not undergo oxidation in the soil, and does not deform when water freezes.

Injection molding
This method of processing polymer raw materials involves the injection of a melt under high pressure into a mold with its subsequent cooling. In this way, fittings, kitchen attributes, as well as furniture fittings, plastic covers, tare boxes and some types of plumbing are produced.

Blowing out
During processing, heated plastic is injected under pressure into a special cavity shaped like the product to be manufactured. The technology allows you to get tanks, tubs, cisterns, barrels and all kinds of cosmetic bottles.

Rotational molding
This method of manufacturing polymer products in our country appeared relatively recently. It allows you to make a variety of products according to customer drawings. Rotoforming is used to create children's playgrounds, mobile dry closets, garbage containers, traffic cones and many other products. This direction of using HDPE is considered one of the most promising.


From high-strength polyethylene, you can get the thinnest film, the thickness of which is comparable to tissue paper and does not exceed 7 microns. It can be a good alternative to heat-resistant paper, for example, parchment - unlike the latter, HDPE has good water resistance, exceptional aroma and vapor barrier characteristics.
It is noteworthy that worn-out items from PVP do not decompose under the influence of external natural factors. That is why the issue of their recycling is especially relevant - such a solution can be not only economically profitable and safe for the environment. The processing of polyethylene in recent years has become one of the most promising areas of the industry. Recyclable materials are widely in demand in the manufacture of plastic containers, dishes and other products that do not require high quality products.
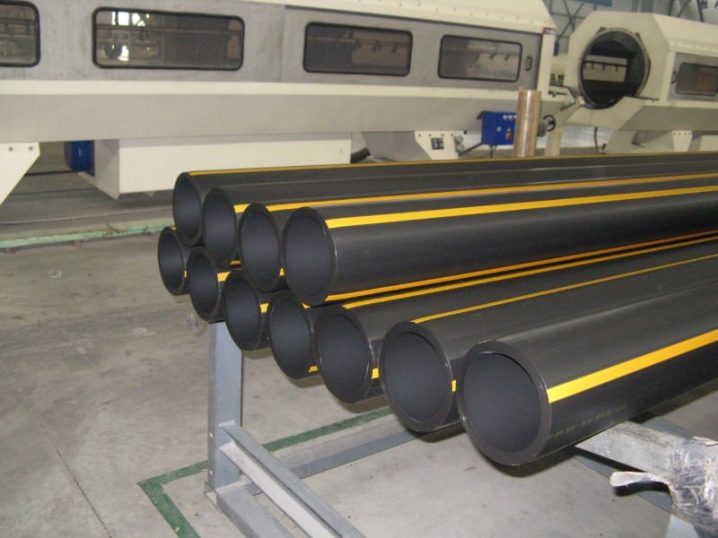
What is the difference between LDPE polyethylene and HDPE, you can find out from the video below.
The comment was sent successfully.