Perforators Bosch: description, types and repair

A hammer drill is a tool that undergoes high mechanical stress. For normal operation of the unit, regular inspections and repairs should be carried out. If you do not take into account such rules, then after a short time the device will become unusable.
Bosch is one of the world leaders in the production of power tools, including rotary hammers. Maintenance of such equipment requires the participation of certified service centers. Minor problems can be repaired by yourself.

Specifications
The Bosch rotary hammer is a tool that is especially popular among professional builders. Seriously repairing these units is rare, but, like any other equipment, perforators from "Bosch" eventually need preventive repair.
Aggregates from Bosch are divided into two large classes:
- perforators in which the engine is horizontal (the layout of the barrel and anchors are parallel);
- perforators, where the engine is vertical - in this case, all working units are located at a certain angle.


The hammer drill has mechanical and electrical units. The second block consists of the following nodes:
- engine;
- engine control device;
- button and switch block;
- replaceable cord;
- block that reduces interference.



The mechanical assembly is assembled from the following elements:
- gearbox (mounted directly on the engine shaft);
- a mechanism that provides a shock impulse;
- cartridge, brushes, anchor;
- clutch that provides traction.

Also, along with the perforator itself, the set includes various replaceable removable elements:
- drill;
- borax;
- crowns;
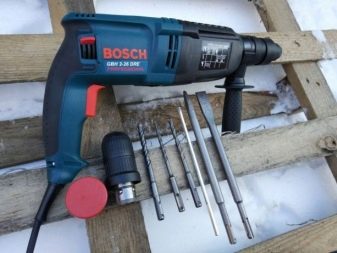

There is also a standalone vacuum cleaner that works in conjunction with the unit. The tool is in a handy case.
Advantages
The performance of the Bosch rock drill is characterized by three criteria.
- The number of spindle revolutions (from 650 to 2200 rpm).
- The impact power is directly related to the characteristics of the engine, the weight of the striker, and the distance of its working stroke. This is one of the main indicators of the quality of the tool. It varies from 1.5 J to 14 J. The most expensive models can cost 50 thousand rubles.
- The impact frequency is characterized by the number of mechanical impulses per unit of time (one minute). In models from "Bosch" the indicator can range from 1000 to 5600 beats per minute.

In models from "Bosch" all three parameters are organically combined, which makes it possible to call the perforators from this manufacturer the best in the world.
Rotary hammer models from Bosch can perform the following functions:
- rotation;
- hit;
- spin and kick at the same time.
In the "Rotation" mode, drilling of various materials occurs: metal, wood. In the "Impact" mode, the device can work as a jackhammer - rock drills are especially effective in demolition construction work. The last function - "Rotation and Impact" has proven itself perfectly when drilling particularly durable materials (granite, concrete, tiles).

disadvantages
The main disadvantage of the Bosch tool is the rather high price.

Views
Rotary hammers from Bosch are divided into types:
- Household models (engines 410-720 watts). Such units have three standard modes, their weight is small (no more than six kilograms).
The most popular hammer drill from this family is the Bosch PBH 2800 RE.
The letter "P" defines the model as a unit for use in a domestic environment. Usually such a tool is marked with a green color scheme. The disadvantage of such machines is not the best cooling and increased efficiency.


Such models have much more advantages than disadvantages, among which it is worth mentioning:
- average price;
- light weight;
- compact size;
- good performance;
- reliability in work.

- The second large class of Bosch instruments is professional rotary hammers with a capacity of 810 watts and more, their weight ranges from 6 to 12.5 kilograms.
The most popular rotary hammer in this class is the GBH 8–45 DV, it has a capacity of more than one and a half thousand watts, there are only two modes of operation: impact, as well as drilling and impact.
The advantages of this model are effective cooling of the unit, minimal vibration, and reliability in operation. If we talk about the shortcomings, then we should mention the large size of such devices and the high price.

- Cordless rotary hammers from "Bosch" they can operate from a 220 volt network. Devices are also available that operate in a wireless mode from a battery. Lithium and cadmium multi-charge power supplies are used. Such drills are extremely necessary in locations where there is no mains power. Professional cordless rotary hammers can work up to 6-8 hours.



- Everything units with a vacuum cleaner from "Bosch" are equipped with a useful device - a dust collector. Such a device significantly extends the service life of the unit. The manufacturer also includes a vacuum cleaner in the kit, which operates from an autonomous power source.


- Hammer drill... Has the following technical indicators:
- power - up to 1.6 kW;
- rotation - no more than 3980 revolutions;
- the number of beats is about 50 per minute.
The technology "Anti-rotation" is used, which effectively protects against overloads. This tool can be used to drill low-density concrete. The rotation speed does not change both at idle and when a load appears. Such a drill can also be used to drill brickwork and dense beams.
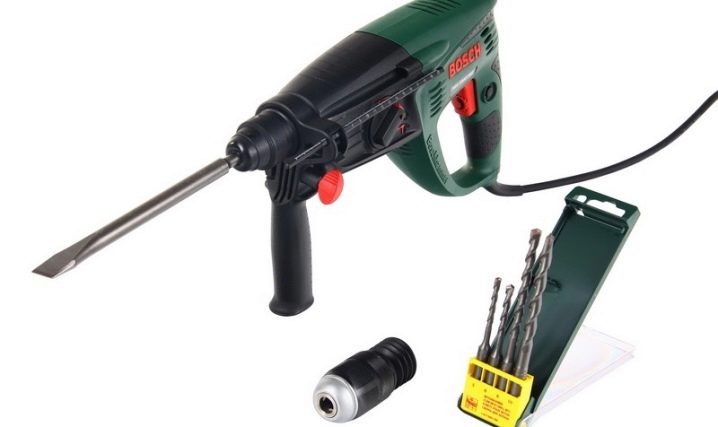
- Pneumatic rock drill Bosch is equipped with a 750 watt engine, while the speed reaches 855 rpm. You can drill holes in medium-density concrete (up to 25 mm thick), dense wood, steel (15 mm). Weight - about three kg.


How to choose?
To choose the right hammer drill for your home, there are several important factors to consider. For household work, units are suitable, the power of which does not exceed six hundred watts..
In the work of any punch, the layout of the engine is important. If the engine is located in a horizontal plane, then such a device is applicable for small narrow holes. The engine in such models is arranged along the impact axis, which does not allow it to cool quickly.
If a large amount of work is being done, then such a power unit should "rest" quite often (on average, every 15-20 minutes). Otherwise, it will simply overheat and become unusable.
The vertical arrangement of the engine increases the power of the rock drill, without the need to constantly cool the engine. Such devices are in demand among professional builders, the performance of such perforators is high.

When choosing, you should look at the marking. If the inscription SDS + is present, then this tool can work on concrete. When choosing a punch, you should read the instructions, consult with the seller, who can give valuable practical advice.
Also on perforators "Bosch" there are such letters: PBH or GBH.
- G means that the unit is suitable for professional use;
- R - this is the letter with which household appliances are marked.


The numbers show how much the hammer drill weighs (example: 3-30, 2-42). Letters in words:
- d - used for chiselling;
- f - use with a mixed cartridge;
- r - there is a reverse.

Fake drills from Bosch are also found. It is not recommended to purchase such a tool.
How to disassemble and repair?
The appearance of malfunctions in the hammer drill is characterized by sound signals:
- there is a grinding noise;
- strange background noise;
- the engine starts to work with roars;
- power is lost;
- there is a smell of burnt wiring;
- high vibration appears.

The most common breakdowns in the Bosch rotary hammer are:
- failure of switches;
- wear of the rubber sleeve between the striker and the striker;
- termination of the operation of the mechanism itself providing the blow;
- malfunction of gears or their wear;
- defect of the clamping unit - it ceases to hold the drill;
- violation of the electrical connection.

Also, defects in the wiring provoke sparks and overheating of the unit.
Electrical faults are as follows:
- the engine does not work;
- violation of contacts;
- burnout of the winding.

To fix mechanical and electrical faults with your own hands, you need to disassemble the hammer drill. All such devices are made according to the same principle. Repairing a Bosch hammer drill is not much different from disassembling a similar unit in any other hammer drill.
The disassembly of the tool should be photographed with a phone in order to reassemble everything correctly.
The beginning of dismantling begins with the cartridge: the rubberized boot should be removed, then the retaining ring, only after that the plastic boot is dismantled. Then you need to find the ball (located under the washer), carefully remove it. The cause of malfunctions often lies precisely in the wear of these parts.

The perforator body is dismantled - for this, the switch is removed, which controls the operating modes. The switch is placed in the "Strike" position (there is a hammer symbol on the body). If there is no such designation, then put a switch in the designation "Impact drilling"... After that, a small button is pressed, which is located on the switch itself. It should be slightly turned down the icon-symbol depicting a hammer, and a click should occur. After that, the switch is lifted with a screwdriver and pulled towards itself.
In some models, the switch is attached to the housing with screws, so it will be enough to simply unscrew them.

If you think that the problem lies precisely in the electrical unit, then the following steps should be taken:
- screws are unscrewed, the back cover is removed;
- the fasteners that fix the network cable are removed;
- the "Start" button is dismantled;
- dismantle all fasteners that hold the stator and armature wires;
- the brushes are taken out;
- the electrical and mechanical unit is disconnected - for this it is enough to unscrew a few bolts;
- the rotor is removed, the bearings are inspected;
- the air intake is removed;
- the stator is removed.

A slightly different design is present in rotary hammers, in which the electric drive is arranged vertically. In this case, the handle is first dismantled, then the bolts connecting the body to the engine are removed with a screwdriver.
Often it is necessary to replace the engine brushes, the appearance of such a malfunction is not difficult to determine: it manifests itself as a smell of burnt wiring, abundant sparking. This defect is one of the most common.
The presence of sparks indicates that the bearings need to be replaced; there may also be defects in the insulation of the rotor and stator. This option is also possible: the collector plates burned out. Damage to the stator also generates copious sparks, and only under one electrode.
You can't do without a tester, you should ring both the rotor and the stator... It will be necessary to measure all the parameters step by step, especially carefully - the resistance level on the windings (the resistance must be constant). If it is established that all problems are in the rotor and stator, then the unit should be returned to the service center. - such a malfunction can only be eliminated by an experienced specialist.

The easiest repair is to replace the brushes. It is enough just to open the lid - the brushes are in special holders.
Brushes are differentiated into several types.
- Brushes made from graphite... Such brushes are reliable and can work for a long time without interference. Among the disadvantages, it can be noted that their wear is uneven, which negatively affects the collector.
- Carbon graphite brushes more durable, replacement is required if 30% of the material is worn out. Even if one brush is normal, and the other is completely worn out, then both need to be replaced.

When working with brushes, pay attention to the spring and contact attachment. The spring must be firmly attached - if it comes off, the engine will be damaged. A weak spring will not provide the desired fit, which will adversely affect the quality of the contact.
After completing the work, all units should be cleaned from graphite chips; in this case, alcohol or vodka should be used. Then the electrodes are fitted to the collector. In this case, sandpaper with a minimum grain size is used, which is applied to the collector and the electrode is lapped with small rotational vibrations.
When the electrode area is slightly rounded, it will be considered a full contact. This contact will ensure good adhesion to the surface of the collector plates.

The impact mechanism depends on what type of hammer drill is being repaired. Barrel units have a vertical layout of the engine, the impact block is present on the basis of the crank mechanism (KShM). The connecting rod mechanism contains only one bearing - it is mounted on the cam itself of the eccentric wheel.
There are also designs where the bearing is attached directly to the base of the connecting rod. When carrying out repairs, as a rule, the connecting rod and eccentric are changed.

Another type of breakdown is the failure of the striker. It is easy to establish this malfunction: the unit works, but there is no blow. To eliminate the defect, it is necessary to disassemble the barrel. The striker is easy to replace. Also, rubber gaskets often wear out - they also need to be replaced.
Pistol rock drills have a different design: the piston does not move with the help of a connecting rod, but as a result of a dynamic oscillating bearing. Such a bearing is subjected to maximum loads and is subject to frequent wear. The bearing will need to be replaced. It is easy to remove the bearing using a screwdriver - it will be enough to hook the bracket and pull it out.
During the work, you should stock up on rags, as well as alcohol - it will be necessary to rinse the gearbox.

Other mechanical failures can manifest themselves in the failure of the mode switch. In this case, it should be cleaned. If after that it still does not function, then it must be replaced. If gears with an oblique tooth fail, the perforator stops "hammering", also these assemblies must be replaced.
There are 2 reasons for gear breakage: the clutch is broken or the gear is out of order. Replacement of these elements will be required.
If the drill flies out of the cartridge, then there are several reasons:
- there was a deformation of the ball elements;
- The safety ring is "old";
- the spring that fixes is deformed.
With such malfunctions, you will have to disassemble the cartridge and look at all the details.

If the drill gets stuck, this indicates that the lubricant on the shank is dry or insufficient. To eliminate such a malfunction, it will be necessary to drip oil into the nest.
The drill also gets stuck due to the "hardening" of accumulated dust. In this case, a little machine oil should also be added.
If a standard drill was used in the hammer drill, then it will need to be processed with special WD-40 solutions. Then wait a few minutes, then gently loosen the drill in different directions.
If the shank is riveted, then in this case it will be necessary to add a special liquid, and then try to pull the tool out of the socket.

For information on how to fix a Bosch rotary hammer, see the next video.
The comment was sent successfully.