Drills for a hammer drill: characteristics, types and sizes

In the construction and repair business, rotary hammers are used with a variety of drill types, allowing you to create different holes in almost all materials. The tool works in both rotary and reciprocating movements. When choosing a drill for a hammer drill, you need to take into account the characteristics and place of use of the drill to achieve an effective result.


Views
What is a drill and why is it not a drill? For the right choice of tool, it is worth considering what equipment the work will be done with. In essence, a drill and a drill are one and the same:
- drills are used in drills with different functions, creating indentations and holes in various surfaces;
- The drill works with a hammer drill, it is a long drill that is designed for working with hard and dense materials, it is capable of creating deep holes.
Each tool has its own external features and design characteristics when working with surfaces.

Woodworking
Twist drills are used to create a hole in wood surfaces, which can also be used for working with metal. But to achieve a clean and neat recess, drills with a special nozzle and a recess are used. They are constructed from carbon steel or alloy steel and are designed for wood only.

Boers are divided into several types.
- Screw. It has only one spiral and is distinguished by a particularly sharp edge. This shape minimizes the spread of chips during the operation of the hammer drill, allowing you to clearly see the drilling site. The edges of the treated surface are smooth along the entire length.
- Spiral. Designed for work on medium-thick surfaces, such as making holes for cabinet handles.
- Per'evoy. Designed for shallow depressions (approx. 2 cm).
- Faustner's drill. Designed for fixing holes (for example, hinges for hinged doors). A distinctive feature is the presence of a centering point and a cutter with a sharpened edge.
- Annular. Outwardly, it looks like a crown or glass with corners around the edges. Used for recesses with a diameter of 10 cm or more.



For metal surfaces
These boers differ in the following characteristics:
- cobalt perforating drill designed for high strength steel;
- soft metals (aluminum, non-ferrous materials) are processed with extra-long twist drills;
- drills with a cylindrical tip made of carbide are considered universal.


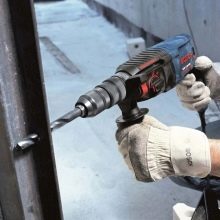
For concrete
When equipping a punch with a drill, it is necessary to take into account the material from which the drill is made. Soft and poor quality drills can break when machining high strength concrete.
There are several categories of drills.
- Auger drill. The tip of this drill is equipped with either a blade-like nozzle or working teeth (most often there are four). The nozzle is necessarily hardened, while acquiring a golden hue. Such drills do not require constant sharpening and serve an almost unlimited amount of time.
- Twist drill. These drills are equipped with special grooves that ensure quick removal of material residues and have a length of 8 cm or more. This design allows holes to be created at great depths.
- Core drill. As with all drills of this type, core drills have a large cutting surface diameter. The edges are diamond-coated or hard-alloyed.



Step drills
This category of drills is distinguished by the speed and quality of work. They are designed to work with various materials: wood, plastic, pipes, any soft and hard surfaces. The sharp tip allows you to precisely cut into the workpiece material, and it also eliminates the need for a centering element, which greatly simplifies the work.
The stepped drill replaces the use of angle grinders and file files, does not require manual processing of the ground surface. The conical shape is formed by translational grooves of various diameters, the transition between each section is 30-45 degrees. This drill silhouette effectively handles thin metal. Another feature of this attachment is that it is versatile. Allows you to replace a set of drills from a diameter of 4 mm to 50 mm.



Center drills
They are considered professional tools due to their use in industrial plants equipped with milling and turning machines. These drills guarantee complete perpendicularity of the finished hole in relation to the surface of the material, no bevels. When working with wood, such a drill is convenient to create a recess for a countersunk head.
Ham radio operators use center drills to create grooves in printed circuit boards. At home, tools with a small diameter (from 6 to 8 mm) are used. It is especially convenient for the center drill to tighten screws or screws that are flush cut.


Dimensions (edit)
View | Diameter | Length | Material / shank |
Spiral for metal | 12 mm 14 mm 16 mm 18 mm 25 mm | 155 mm 165 mm 185 mm 200 mm 200 mm | Steel |
Spiral on wood | from 1 mm to 20 mm | from 49 mm to 205 mm | Steel |
Feathers | from 5 m up to 50 mm | from 40 mm up to 200 mm | Steel |
Spiral for concrete | from 5 mm up to 50 mm | from 40 mm up to 200 mm | Steel |
Faustner drill | from 10 mm to 50 mm | from 80 mm to 110 mm | from 8 mm to 12 mm |
Centering | from 3.15 mm to 31.5 mm | from 21 mm to 128 mm | from 0.5 mm to 10 mm |
Stepped | from 2 mm to 58 mm | from 57 mm to 115 mm |

How to choose?
Rotary hammer drills are divided into models with different coatings.
- Oxide. The appearance of the drills is painted black - this is the cheapest coating. The film covering the drill protects the hammer drill chuck from overheating and rust, increasing the service life.
- Titanium aluminum nitride coating. Allows to increase the service life of drills by 5 times. Reliable and high quality drills.
- Ceramic coating. These drills are not made of pure ceramics, but titanium nitrides. The disadvantage of such a coating is the impossibility of sharpening the nozzle.
- Titanium carbonitride coating. Also increases the service life of the nozzles, has high strength.
- Diamond spraying intended for work with stone and porcelain stoneware surfaces.
Drills with this coating are the most expensive on the market, but their life is unlimited.

When buying, you should pay special attention to some characteristics.
- Drill ponytail type. It is imperative to take into account the type of tail, otherwise the drill will not be securely fixed in the chuck, which will lead to equipment breakdown. To find out the type of chuck, you can use the instructions supplied with the tool. The tails of the hammer drill bits are marked SDS-max and SDS-plus and are made in a more complex shape than drills for drills.
- Manufacturer. Many popular firms produce a whole range of instruments with different pricing policies. Most often, in stores you can find quality products for household needs at quite affordable prices, but a professional tool is difficult to find.
- Drill length The length of the total or only the working surface can be indicated.

- Head diameter. For work with various materials, drills with the appropriate diameter are used.A hole smaller than the desired size will be difficult to enlarge with a narrow drill. In addition, this will lead to poor-quality work, which will affect the degree of fixation of the fasteners of the installed mechanism.
- Grooves. Drill grooves are different: semicircular, with projections and under bevel. The former are designed for homework that does not require high precision. The last two types are used in large enterprises, due to the ability to quickly remove.
- Tungsten carbide groove. Smooth and smooth surfaces of drills are intended for work with soft materials or external surfaces of bolts, screws. On drills, the geometrical surface of the drill tip is sharper and sometimes of complex shapes - this is due to the impact mode of operation.

How to use?
Before starting work, it is worth making sure that the type of tail of the drill used matches the chuck of the hammer drill. Professional drills recommend SDS-mount drills. This type of retainer allows for easy tool changes. The selected drill must be correctly inserted into the hammer chuck. To perform the procedure correctly, you should adhere to simple recommendations.
- The hammer drill must be disconnected from the power supply before inserting the drill into the chuck. Only after fixing the drill can you start working.
- The hammer drill uses drills that are suitable for the size and model of the equipment. A loose drill will damage the surface or hammer.
- The tail of the drill must be oiled and cleaned. These actions reduce drill wear and zero damage to the fastening mechanism.
Important: during work, do not touch the rotating drill with your hands. Doing so will result in soft tissue damage and serious injury. When processing a wall in an apartment where an anchor bolt is required, you should take a nozzle 110 mm long and 6 mm in diameter. This is due to the thickness of the concrete slabs.

Possible problems
A common problem is that the drill gets stuck in the chuck of the equipment. To extract it, you should choose one of several convenient methods:
- the free end of the drill is clamped in a vice and lightly tapped with a hammer with a rubber gasket on the parts of the clamping mechanism;
- the punch cartridge is placed in a bowl of gasoline and the drill is subsequently removed;
- if the jam has occurred in the key-type clamping mechanism, it is necessary to turn the key counterclockwise or drip machine oil;
- the stuck drill in the keyless chuck is removed by tapping the parts of the chuck counterclockwise;
- complete disassembly of the equipment is possible if none of the methods helped.

For information on how to clamp conventional drills into a hammer drill, see the next video.
The comment was sent successfully.