Types of refractory materials and areas of their use
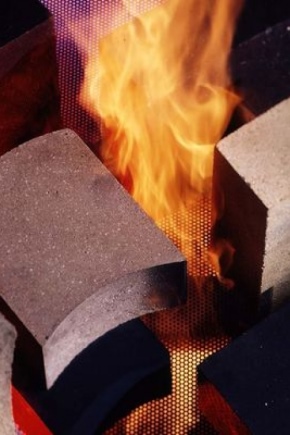
Refractory materials are structurally stable when exposed to high temperatures, flame and chemicals. They are used in industrial plants where the production cycle involves the use of thermal effects, as well as in residential buildings where heating devices are installed. Due to their high operational parameters, such materials are especially relevant for any facilities that have requirements for durability, reliability and safety.
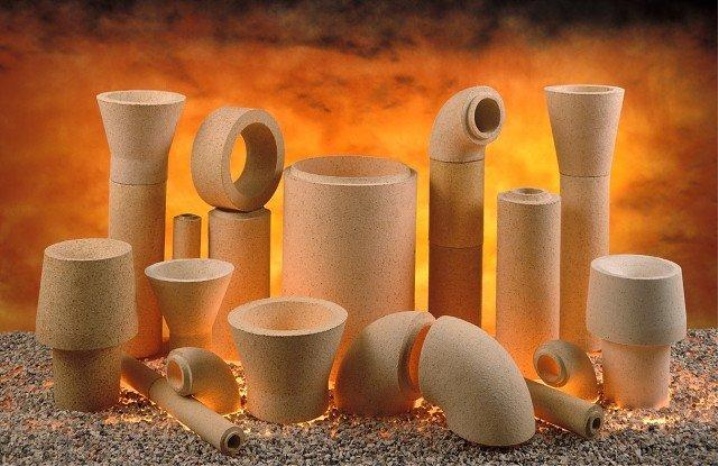
Peculiarities
The need for the use of fire-resistant materials appeared at the earliest stages of human development, when people learned to extract and use fire. Gradually, such materials became the basis for the construction of steel-making, blast furnaces and other heating equipment. In the middle of the 17th century. in many countries began to make refractory bricks from clay. By the beginning of the 19th century. fire-retardant products were actively produced in European countries, and by the end of the century, refractory products began to be produced everywhere in Russia. In the middle of the last century, fire-resistant paints and fire-retardant compositions were invented, and the requirements for heat-resistant products were officially enshrined in GOSTs and SNiPs.
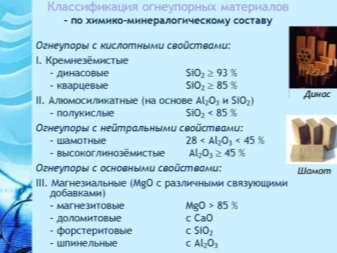

The main property of such materials is fire resistance. This indicator determines the temperature at which the product begins to deform. With regard to its value, the efficiency of material exploitation in certain types of work is considered. In addition, other characteristics are calculated, in particular:
- features of the behavior of the material under the influence of elevated temperatures;
- change in shape and violation of integrity when exposed to temperature;
- the stability of the structure, which is determined by the parameter of the mechanical compressive force during heating;
- force of reaction to the effect of aggressive chemical solutions.

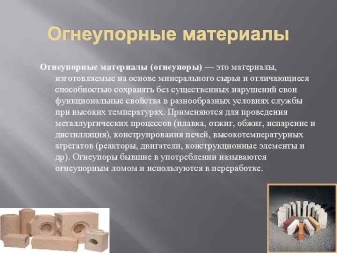
Typically, fire-resistant materials are materials that can withstand heating from 1580 to 3000 degrees Celsius. Materials that retain their appearance and physical characteristics when exposed to higher temperatures are marked as super-refractory.
Any refractory products are made on the basis of a combination of artificial and natural raw materials; for this, the optimal concentrations of mineral and chemical components are selected.
The final indicators of density, strength, as well as porosity and structure are determined by the application of a specific technology.
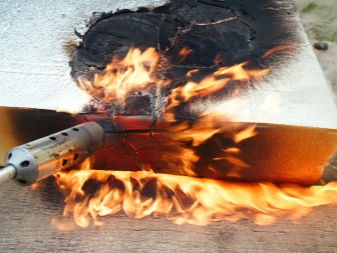
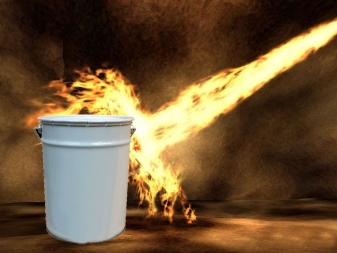
Classification
Fire resistant products can be produced in different forms and with different properties. There are several reasons for their classification.
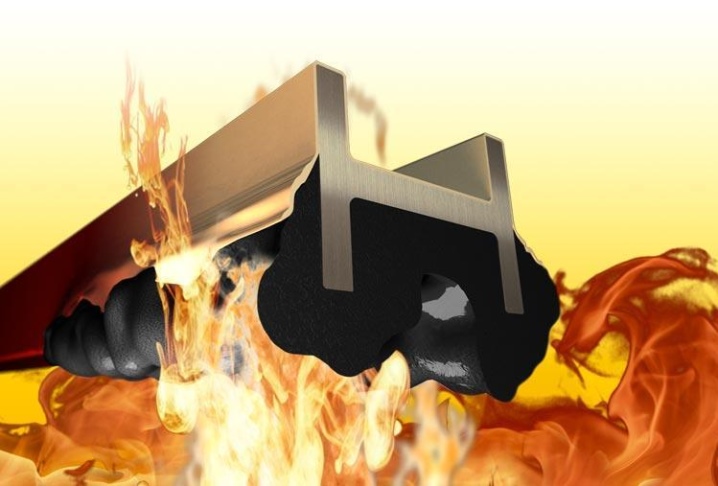
Refractoriness
According to fire resistance, materials are distinguished:
- ordinary refractory - withstand from +1580 to +1770 degrees Celsius;
- highly refractory - up to 2 thousand degrees;
- products with high refractoriness - up to 3 thousand degrees;
- super-refractory - must withstand heating over 3 thousand degrees.
The most fire resistant material in the world is hafnium carbonitride, with a melting point of 4200 degrees Celsius.
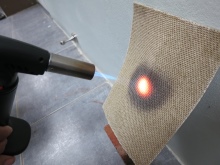
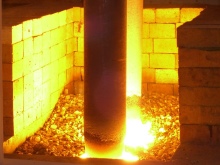
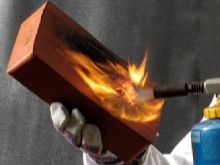
By molding method
There are several basic methods for molding refractory materials:
- liquid casting;
- molding from soft compounds with further additional pressing;
- molding from compressed powders;
- cutting of rocks;
- hot pressing method;
- thermoplastic pressing technique;
- molding from hot melt.
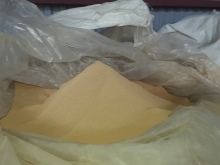
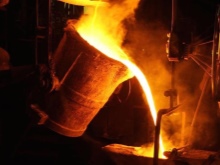
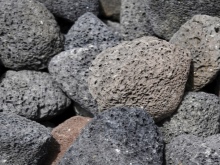
By chemical and mineral composition
Several types of raw materials are used to create fire-resistant products.
- Organic - these types of products are made from mineral raw materials. Most of these products can withstand significant heat. The only exception is polystyrene foam. They have a weak resistance to fire, however, you can lay out a stove with a weak heating from them.
- Inorganic Is the most impressive product category with a wide range of fire resistance. This includes basalt and mineral wool, fiberglass, perlite and vermiculite.
- Composite - this category includes asbestos products (asbestos-cement or asbestos-lime compositions), as well as foamed silica products.
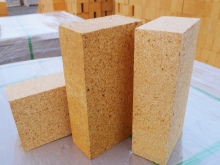
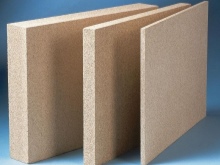
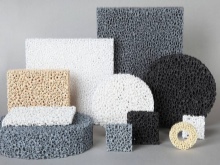
Several types of refractory materials are distinguished depending on the main active ingredient.
- Refractories containing aluminum oxides sintered into blocks are called acidic - the base in this case reaches 90% of the total mass. This group includes mullite and fireclay bricks, which are considered an ideal solution for stoves and fireplaces operating on natural fuel.
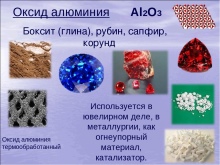
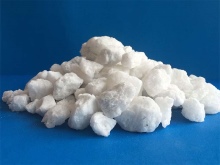
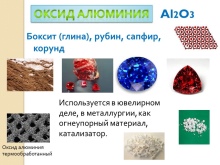
- Magnesian - such products are made from oxides of different metals by sintering when heated. The blocks are resistant to aggressive solutions and can withstand heating up to 2000 degrees.

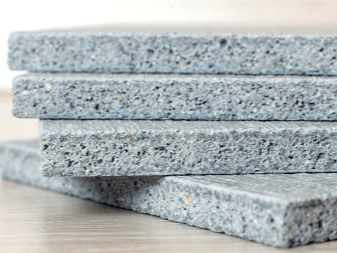
- Minerite - produced using environmentally friendly raw materials. Reinforced cements account for up to 90% of the composition. When heated, these products slightly increase in size, therefore, during installation, you need to leave small gaps between the layers.
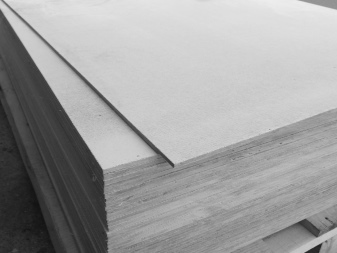
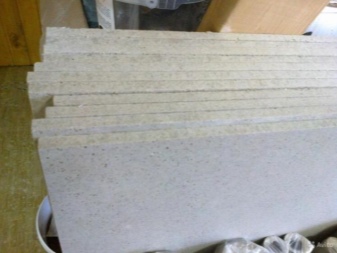
- Asbestos - slabs and panels made of asbestos have been used for a long time in construction. However, some time ago, the toxic effects of asbestos on human health were identified. The substances that make up the material are carcinogenic and lead to cancer. Nevertheless, the fire resistance of such products is extremely high. The material can withstand heating up to 500 degrees for several hours without changing its strength and density.
Sheathing with such panels is used in technical structures, while it requires mandatory coating with environmentally friendly materials.
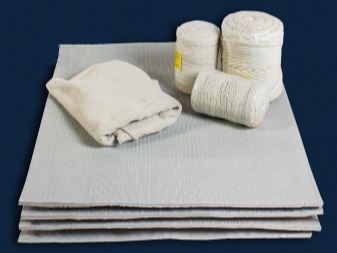

- Superizole - a material of calcium silicate, it is lightweight and easy to cut. Superizol can withstand heating up to 1000 degrees, while it has a reduced thermal conductivity. This material is in demand for the installation of partitions and protective wall decoration.
The disadvantages include fragility: under mechanical stress, such products break.
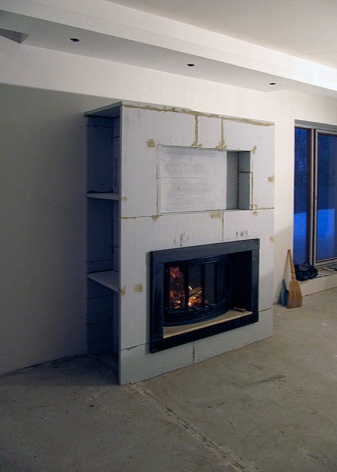
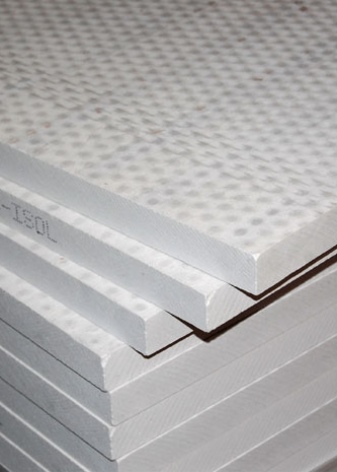
- Glass-magnesium panels Is a material consisting of magnesium chloride, fiberglass and expanded perlite with the addition of synthetic fibers. Possesses high adhesion, low thermal conductivity, moreover, it is easy to process.
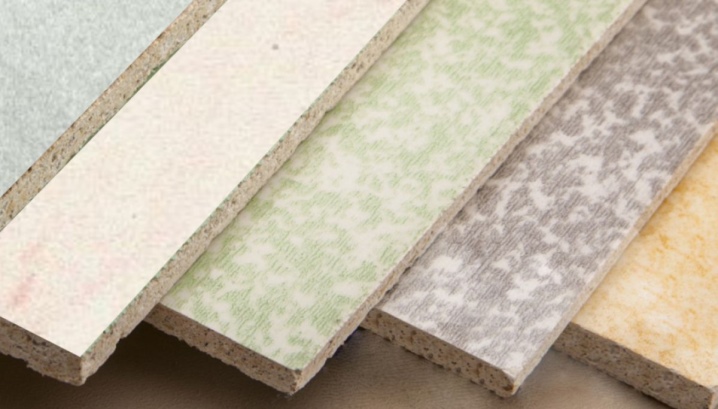
- Vermiculite - slabs based on silicate mica mixed with synthetic components. It is an environmentally friendly and non-toxic material that retains heat. The disadvantages include low moisture resistance, therefore, during operation, additional protection from water is required.
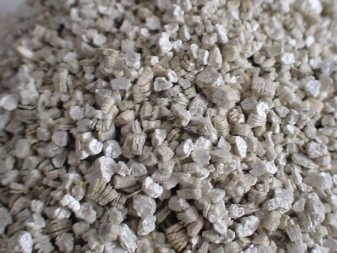
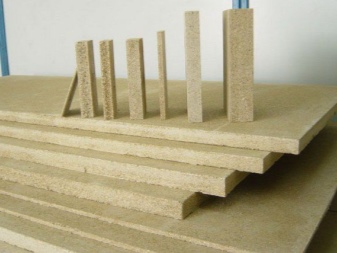
- Metal screens - sheet fire-resistant material with a reflective surface. Such products not only protect the walls from excessive overheating, but also allow you to maintain a comfortable temperature in the room, reflecting it inward.
Typically, these sheets are made of stainless steel.
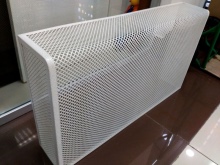
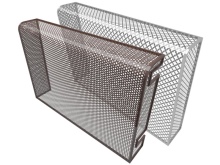
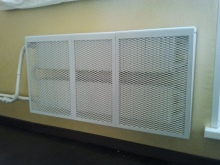
- Clinker - This ceramic material is made from finely porous clay. It is distinguished by its resistance to temperature extremes, the ability to withstand not only fire, but also severe frosts.
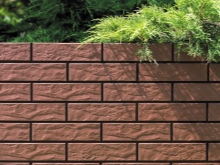
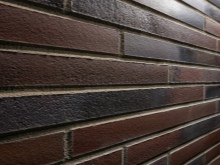
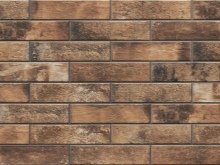
- Porcelain stoneware - material based on marble, granite and quartz chips with the presence of salts and metal oxides. Differs in the ability to withstand heating up to 100 degrees or more, is characterized by high moisture resistance.
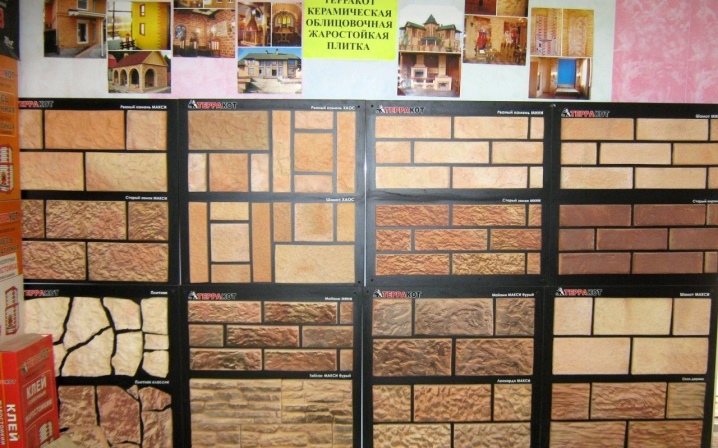
By porosity
Depending on the degree of pore openness, there are:
- up to 3% - superdense;
- up to 10% - high-density;
- up to 16% - dense;
- up to 20% - compacted;
- up to 30% - medium density;
- up to 45% - low-density;
- up to 75% - highly porous;
- more than 75% are ultra-porous.
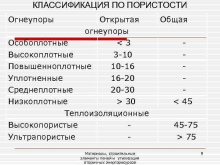
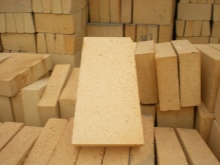
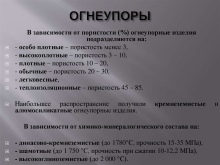
Shapes and sizes
Refractory materials are offered in different shapes and sizes:
- wedge or straight - can be small, normal or large;
- shaped, simple, as well as complex - weighing over 60 kg.
The greatest demand was received by sheet panels. Their functional purpose depends on the size and set of product performance characteristics. They are indispensable for the lining of boiler rooms, home fireplaces, stove blocks, they are heat-insulating for columns, boilers, as well as heating systems in baths and saunas. They play the role of protective screens and increase the production effect of the equipment as a whole and its individual parts.
Molding and powdery products are relevant in instrument making. It solves the problem of adjusting the operating mode in accordance with the technical specifications. Unshaped raw materials are used to make clothes for employees of foundries.
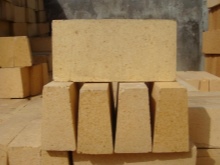
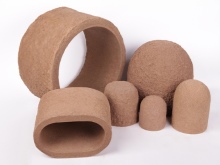
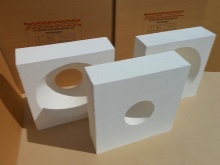
Applications
All types of flame retardant materials are commonly used in industrial applications. They are involved in non-ferrous and ferrous metallurgy - this area accounts for about 60% of products made of heat-resistant materials in general, as well as in the manufacture of ceramics and glass. Fire-resistant compounds are the basis for the manufacture of acid and heat insulators. They are lined with industrial furnaces, as well as other installations with an open flame.
In everyday life, such products have found application in the arrangement of fireplaces and stoves, barbecues and chimneys. These finishing materials are widely used in the construction and arrangement of buildings. They are used for upholstery of ceilings and walls in rooms. Such a solution greatly increases the fire safety of the structure, therefore they are used in structures with increased requirements for PPB.
It is important to keep in mind that most building fire-resistant materials cannot withstand fire, so they can burn. Heat-resistant and refractory products are distinguished. The latter can withstand a source of open flame at close range for a long time - they are widely demanded in the construction of baths and saunas.
Heat-resistant materials can withstand intense heat, but open fire will destroy their structure.
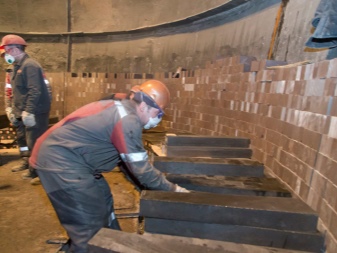
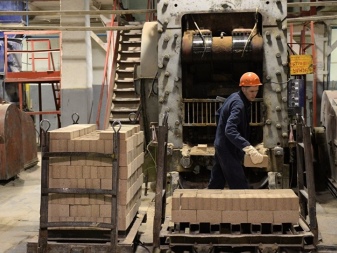
The comment was sent successfully.