Polyurethane foam at subzero temperatures: rules of application and operation
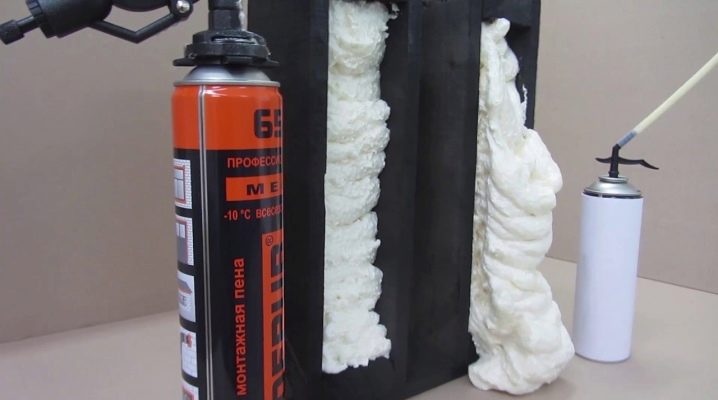
It is impossible to imagine the process of repair or construction without polyurethane foam. This material is made from polyurethane, connects separate parts to each other and insulates various structures. After application, it is able to expand to fill all wall defects.
Peculiarities
Polyurethane foam is sold in cylinders with a propellant and prepolymer. Air humidity allows the composition to harden with a polymerization effect (formation of polyurethane foam). The quality and speed of acquiring the required hardness depends on the level of moisture.
Since the humidity level is lower in the cold season, the polyurethane foam hardens longer. To use this material at subzero temperatures, special components are added to the composition.

For this reason, there are several types of polyurethane foams.
- Summer high-temperature foam is used at temperatures from +5 to + 35 ° C. It can withstand temperature stresses from -50 to + 90 ° C.
- Out-of-season species are used at temperatures not lower than -10 ° C. Even in sub-zero weather, sufficient volume is obtained. The composition can be applied without preheating.
- Winter low-temperature types of sealants are used in winter at air temperatures from -18 to + 35 ° C.
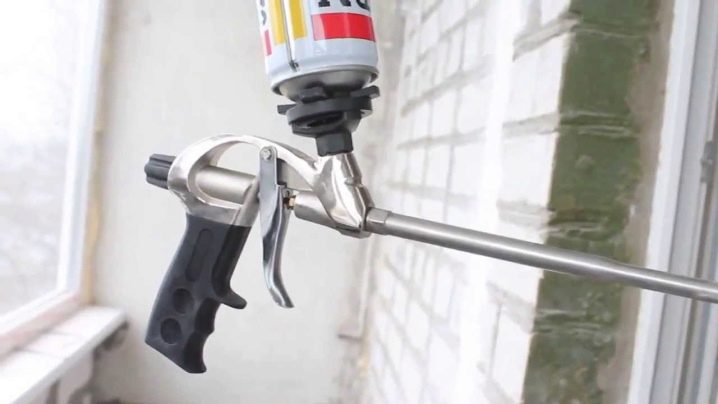
Specifications
The quality of the polyurethane foam is determined by several characteristics.
- Foam volume. This indicator is influenced by temperature conditions and humidity of the environment. At lower temperatures, the volume of the sealant is less. For example, a bottle with a volume of 0.3 liters, when sprayed at +20 degrees, forms 30 liters of foam, at 0 temperature - about 25 liters, at negative temperatures - 15 liters.
- Degree of adhesion determines the strength of the connection between the surface and the material. There is no difference between winter and summer species. Many manufacturing plants are trying to produce compounds with good adhesion to wood, concrete and brick surfaces. However, when using foam on top of ice, polyethylene, teflon, oil bases and silicone, the adhesion will be much worse.
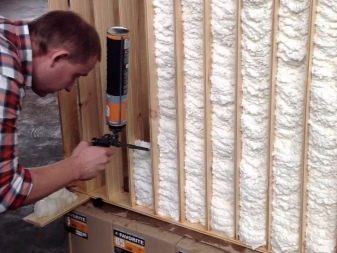
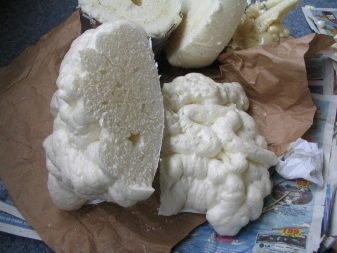
- Expanding ability Is an increase in the volume of the sealant. The higher this ability, the better the sealant. The best option is 80%.
- Shrinkage Is the change in volume during operation. In the event that the shrinkage capacity is too high, the structures are deformed or the integrity of their seams is disturbed.
- Excerpt Is the duration of the complete polymerization of the material. With an increase in the temperature regime, the duration of exposure decreases. For example, winter polyurethane foam hardens up to 5 hours at temperatures from 0 to -5 ° C, up to -10 ° C - up to 7 hours, from -10 ° C - up to 10 hours.
- Viscosity Is the ability of the foam to stay on the substrate. Professional and semi-professional polyurethane foams are produced for widespread use. Semi-professional options are ready for use after installing the valve on a foam cylinder, professional ones - they are applied with a mounting gun equipped with a dispenser.
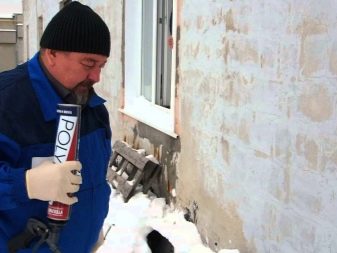
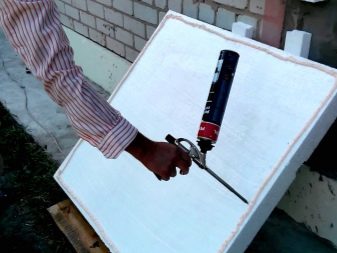
The advantages of the installation staff include the following:
- multifunctionality;
- heat and sound insulation properties;
- tightness;
- dielectric;
- resistance to temperature extremes;
- long service life;
- easy application.
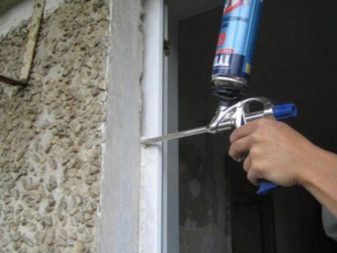
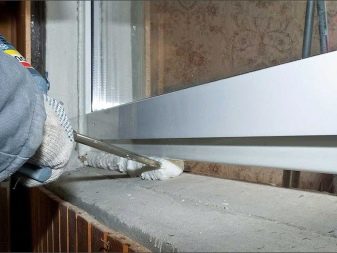
The disadvantages of the sealant are represented by the following features:
- instability to ultraviolet radiation and high humidity;
- short shelf life;
- some species are capable of rapid ignition;
- difficult to remove from the skin.
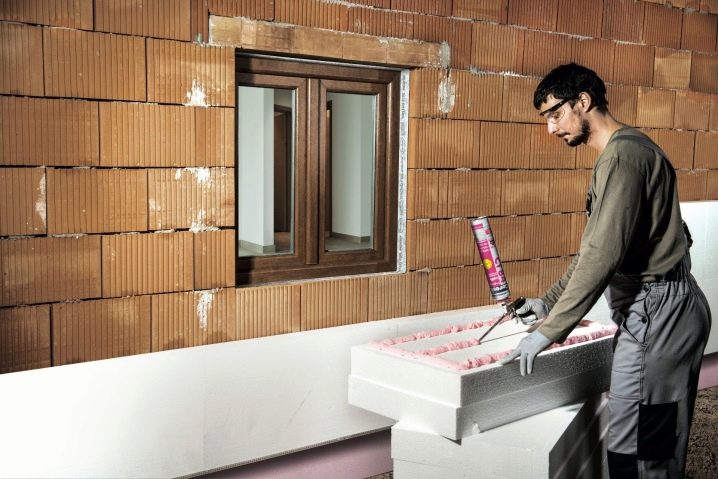
Polyurethane foam is a versatile product that performs several functions.
- Tightness.It fills in gaps, insulates interiors, removes voids around doors, windows and other details.
- Gluing. It fixes the door blocks so that there is no need for screws and nails.
- Secures the base for insulation and insulation, for example, for cladding a building with foam, the installation composition will be the best option.
- Soundproofing. The building material fights against increased noise during the operation of ventilation, heating systems. It is used to seal up the gaps between pipelines, the connection areas of air conditioners and exhaust structures.
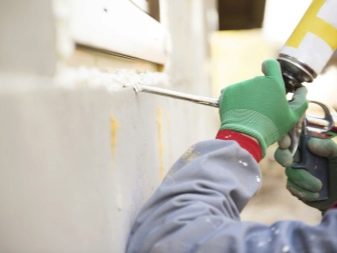
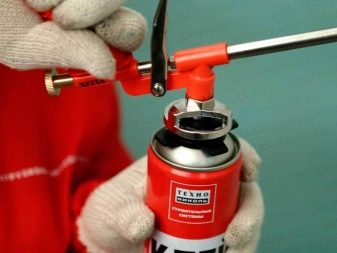
Terms of use
Experts recommend adhering to several rules when working with polyurethane foam.
- Since it is not easy to remove foam from the skin, you should first equip yourself with work gloves.
- In order for the composition to mix, shake it thoroughly for 30-60 seconds. Otherwise, a resinous composition will come from the cylinder.
- For quick adhesion, the workpiece is moistened. Then you can go directly to applying the foam. The container must be held upside down to displace the polyurethane foam from the container. If this is not done, the gas will be squeezed out without foam.
- Foaming is carried out in slots whose width is no more than 5 cm, and if more, then use polystrile. It saves foam and prevents expansion, which most often leads to structural failure.
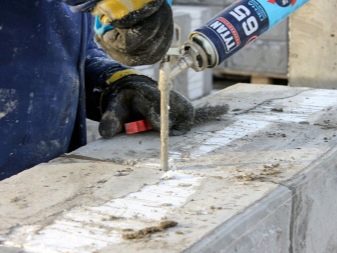
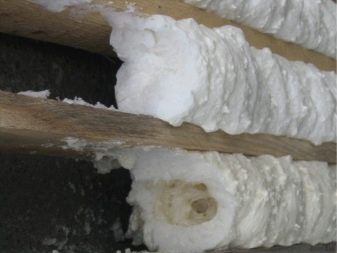
- Foam from bottom to top with even movements, filling a third of the gap, because the foam hardens with expansion and fills it. When working at low temperatures, you can only work with foam heated in warm water up to + 40 ° C.
- For quick adhesion, it is necessary to spray the surface with water. Spraying at negative temperatures is prohibited, as it is impossible to obtain the desired effect.
- In case of accidental contact with mounting foam on doors, windows, floors, it is necessary to remove it with a solvent and a rag, and then wash the surface. Otherwise, the composition will harden and it will be very difficult to remove it without damaging the surface.
- 30 minutes after using the installation compound, you can cut off the excess and plaster the surface. For this, it is very convenient to use a hacksaw or a knife for construction needs. The foam begins to fully set after 8 hours.
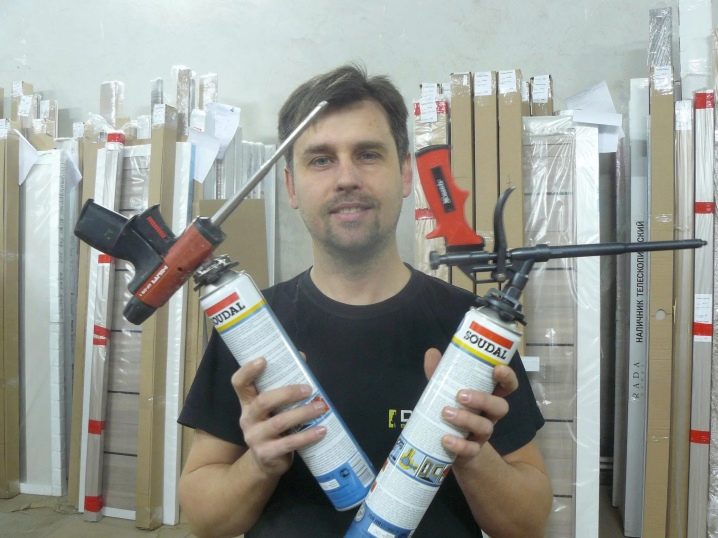
Professionals recommend that you carefully read the precautions before working with polyurethane foam.
- The sealant can irritate the skin, eyes and respiratory tract. Therefore, it is recommended that the worker wear protective goggles, gloves and a respirator when there is poor ventilation. Once hardened, the foam is not harmful to human health.
- In order to avoid the purchase of fakes, you should use some recommendations: ask the store for a certificate for the product; examine the quality of the label. Since they try to produce fakes with minimal costs, the printing industry does not attach much importance. Defects of the label are visible on such cylinders with the naked eye: displacement of paints, inscriptions, other storage conditions; date of manufacture. Expired material loses all its basic qualities.
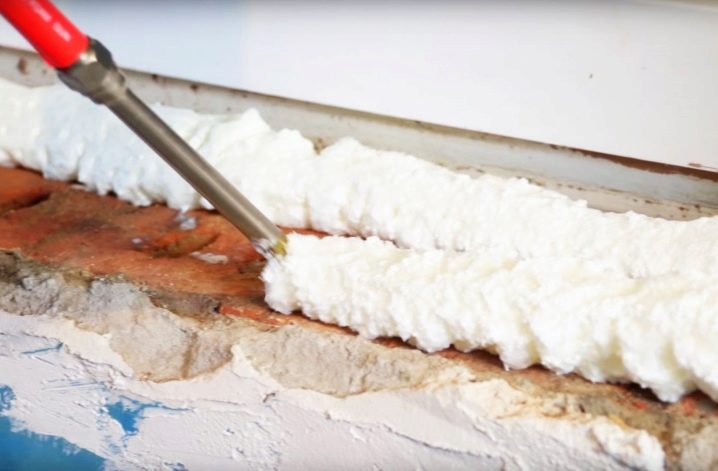
Manufacturers
The construction market is rich in a variety of sealants, but this does not mean that all of them meet the quality requirements. Often, stores receive foams that have not been certified and do not meet the necessary requirements. Some manufacturers do not completely pour the composition into a container, or instead of gas use volatile components that harm the atmosphere.
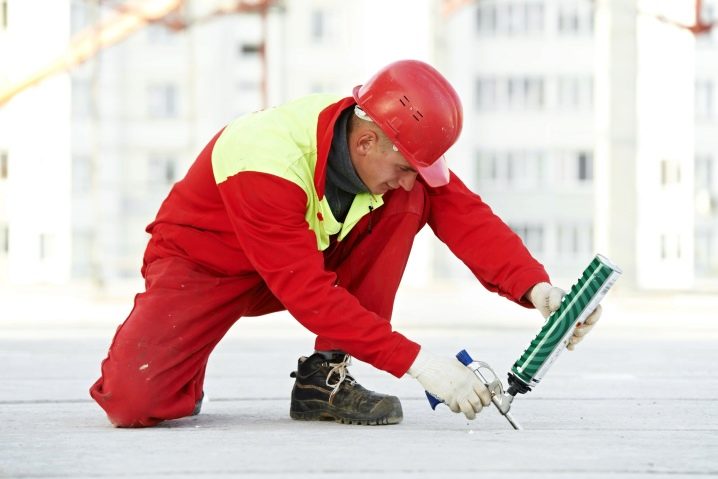
The most popular manufacturer of winter sealants is considered Soudal ("Arctic").
The products have the following characteristics:
- temperature of use - above -25 ° C;
- foam output at -25 ° C - 30 liters;
- exposure duration at -25 ° C - 12 hours;
- foam heating temperature - no more than 50 ° C.
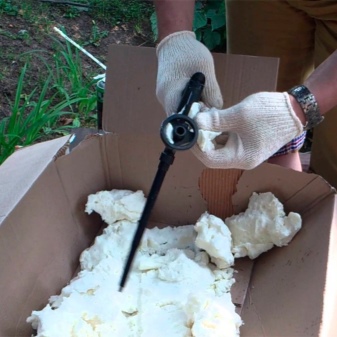
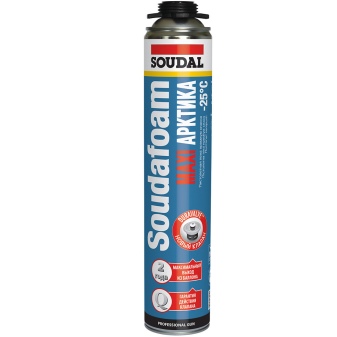
Another equally well-known manufacturer of building materials is the company "Macroflex".
Products have the following properties:
- use temperature - above -10 ° С;
- polyurethane base;
- dimensional stability;
- exposure duration - 10 hours;
- foam output at -10 ° C - 25 liters;
- noise insulation properties.
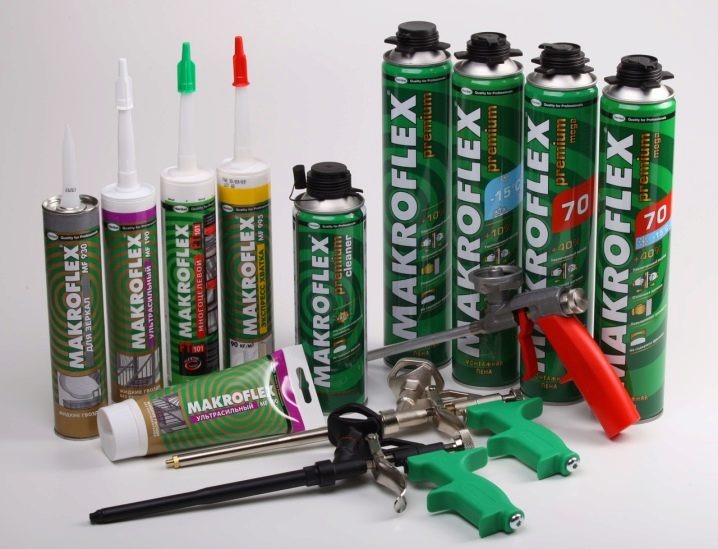
For the rules of using polyurethane foam at subzero temperatures, see the following video.
The comment was sent successfully.