Concrete varnish: types and applications
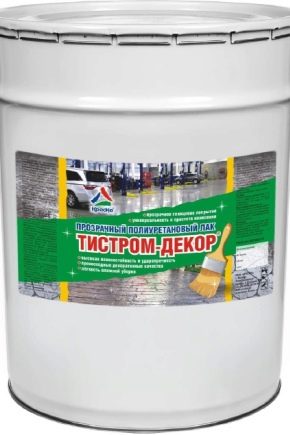
Today, concrete is used to decorate both residential buildings and public and commercial institutions. It is used for wall, ceiling and floor decoration. Despite its strength and durability, concrete needs additional protection and treatment. For this, special varnishes are used. Compositions for concrete foundations are used in the process of carrying out internal and external works. Varnishes differ in composition, appearance and technical characteristics.


Advantages
Professional finishers have been using varnishes for a long time due to their positive qualities.
- They are resistant to abrasion, are not afraid of constant stress and mechanical damage. The varnish is recommended for use in premises with high traffic.
- Flame retardants will protect concrete walls and floors from fire.
- The coating protects the base from the negative effects of frost and sudden temperature changes.
- Varnishing increases the service life and strength of the concrete.
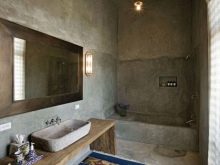
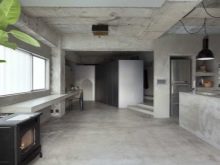
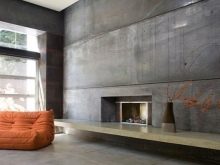
- High-quality varnish has anti-corrosion properties, it is not afraid of high humidity.
- After coating, the concrete will acquire an attractive appearance, be it colorless or colored.
- It is easy to varnish the surface. Simple operation has played an important role in the popularity of the product.
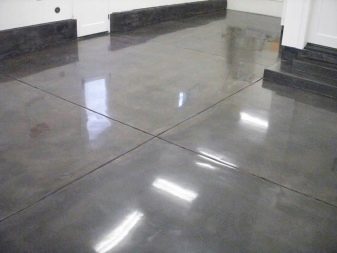
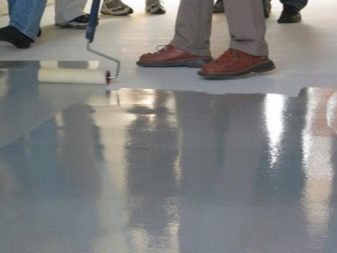
Areas of use
Lacquer products are used in various construction sites and for the processing of such objects:
- in an apartment, residential building or suburban building;
- on the basis of warehouses;
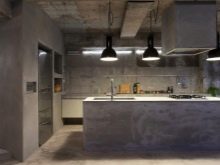
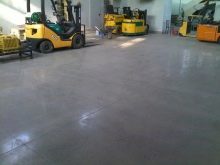
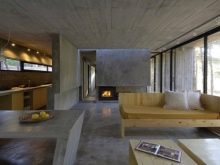
- buildings from the pharmaceutical and industrial sectors;
- concrete fences;
- platforms, terraces and verandas;
- paths and screeds.
This is the main list of the use of such a finishing composition.
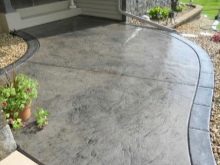
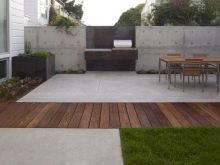
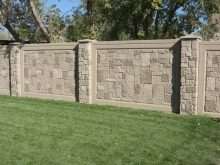
Views
The assortment of varnish for concrete is varied. Each product has specific characteristics.
Experts distinguish several classifications depending on such indicators:
- ability to reflect light;
- main cast;
- fire resistance.
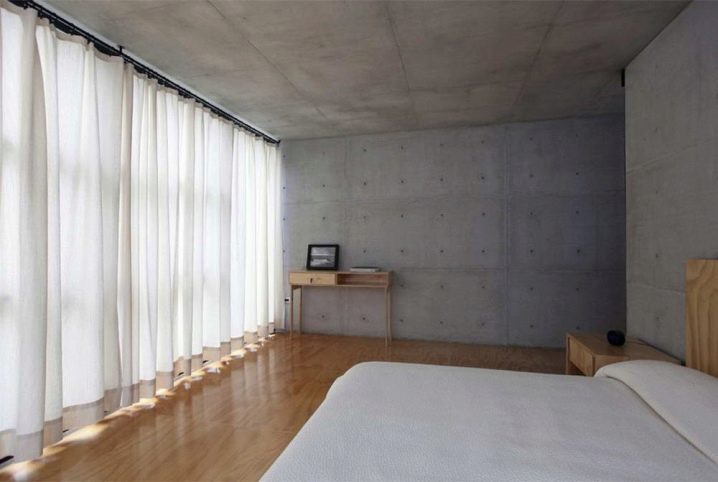
Color and various additives
The first segment is divided into separate types depending on the aesthetic effect.
Varnish can be:
- matte;
- glossy;
- semi-matte;
- semi-glossy.
This criterion is chosen depending on the style of the interior, as well as the texture of the pieces of furniture.
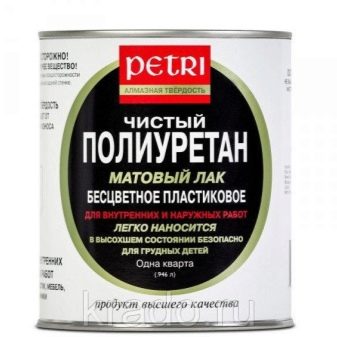
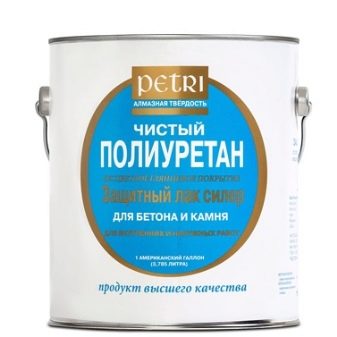
Varieties of compositions
The main aspect that influences the choice and classification of concrete varnish is the composition. Most often, it is the main component with various additives, on which the texture, color, elasticity, resistance to the effects of the spring environment and other indicators depend.
There are the following types of concrete varnish:
- Polyurethane compound. It is the best choice for treating surfaces that are exposed to moisture. The components will retain the practicality of the base in high damp conditions.
- Acrylic. This varnish has high aesthetic properties. It is more often used not for protection, but for decoration. This material is notable for its considerable cost, especially when compared with numerous analogues.


- Silicone. The composition successfully combines increased resistance to moisture and decorative properties.
- Polymeric. This type of varnish dries quickly and demonstrates excellent productivity on large surfaces.
- Epoxy. Before using such a varnish, you must carefully prepare the surface. It is based on epoxy resin. These are two-component formulations that must be mixed before application.
On the market you can find a special alkyd varnish, but it is usually not used for concrete treatment.

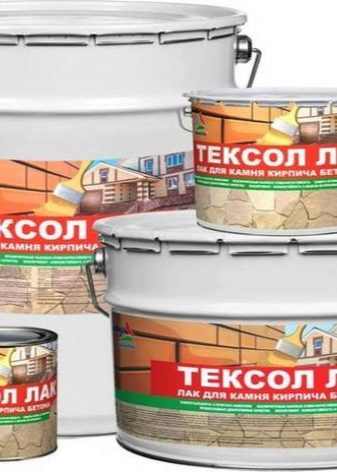
Polyurethane
This class of varnish is the most popular and widespread when it comes to concrete processing. This material has a special property of penetrating small cracks on the surface, increasing the protective properties. Experts recommend using such a varnish together with an impregnation based on the component of the same name.
The treatment will prevent moisture from entering the upper layers of the coating. The composition is ideal for use in such premises as garages, warehouses, workshops, as well as car services.
The advantages of polyurethane varnish are - simple and straightforward use; attractive visual effect; high rate of resistance to oil products; affordable cost; durability and reliability; the protective properties are retained even with frequent wet cleaning.
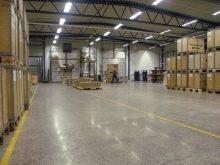
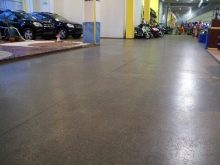
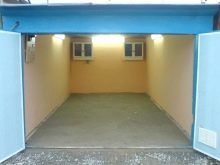
Polymeric
Typically, styrene is the main component of this material. Polymer varnish boasts excellent protective properties and other positive characteristics.
This finishing material has various features:
- Constant loads and pressure are not afraid of him. The layer retains its strength regardless of external influences.
- Indicators of strength and wear resistance of a concrete base increase significantly.
- High resistance to moisture and dampness.
- High degree of protection even in harsh environments.
- The drying process takes a little time. With such a varnish, you will complete the repair faster.
- The most favorable price.
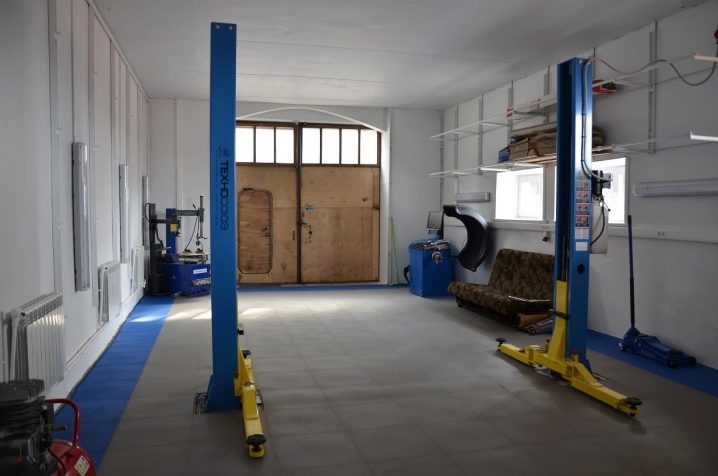
- The varnish can be used for interior or exterior decoration.
- Corrosion protection.
- A stylish decorative layer forms on the surface.
- Easy to apply.
- Low abrasion.
- Resistance to various atmospheric influences.
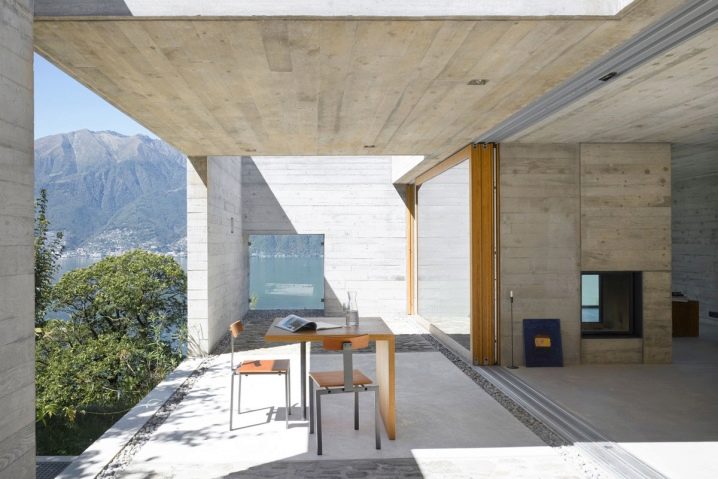
Silicone and acrylic based
The above two categories of varnishes can be combined into one due to their similar properties. The price of such material is much higher than a similar consumable finish. The cost of one kilogram can be about 700 rubles. The high price is justified by applying a thin layer to the surface. A small amount of varnish is sufficient to protect the surface or concrete product.
Many buyers are attracted by the possibility of finishing without interrupting the main work. After complete drying, a dense matte film forms.
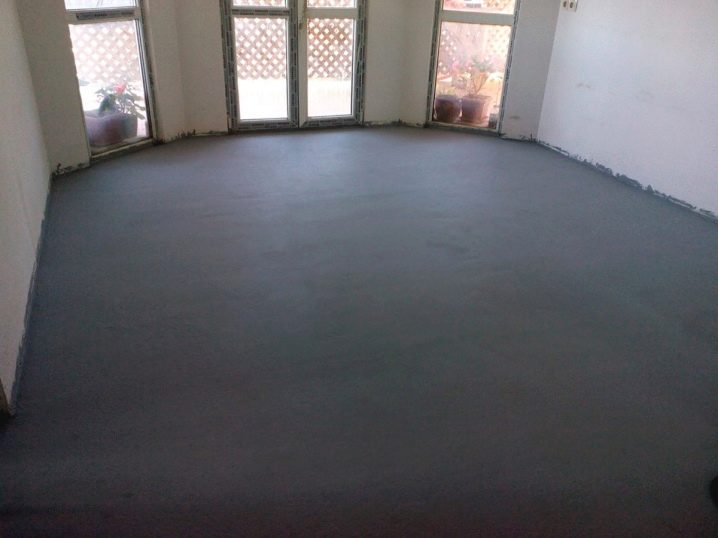
Epoxy
It is recommended to use such varnishes on the basis of such objects:
- Food industry buildings;
- Warehouses;
- Living spaces.
The material is used in rooms where the smell of solvents is contraindicated during finishing work. As an impregnating composition, such varnishes are somewhat inferior to polyurethane varnishes, since their penetrating power is lower. Despite this, epoxy varnish boasts excellent protective qualities. They will be quite enough for the surface treatment of industrial and commercial buildings.
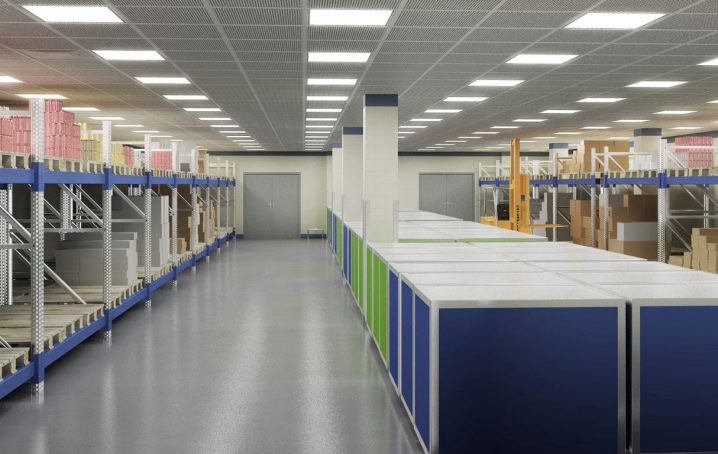
Pros of epoxy varnish:
- favorable cost;
- a remarkable indicator of mechanical strength;
- health safety (due to the absence of hazardous components);
- excellent reflectivity.
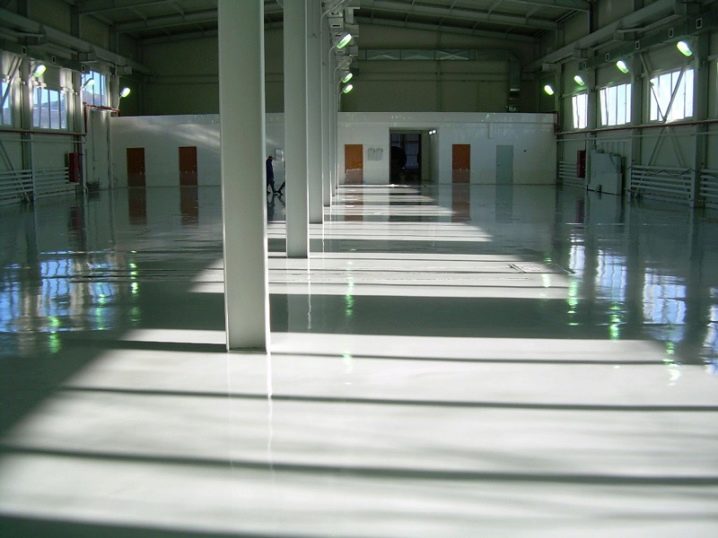
Experts highlight the following disadvantages:
- the material is inferior in terms of elasticity;
- to manufacture a product, you must strictly follow a special technique.
The above products (concrete varnishes) are also used for processing materials such as stone or hardboard. When choosing a product, make sure it can be used over concrete.
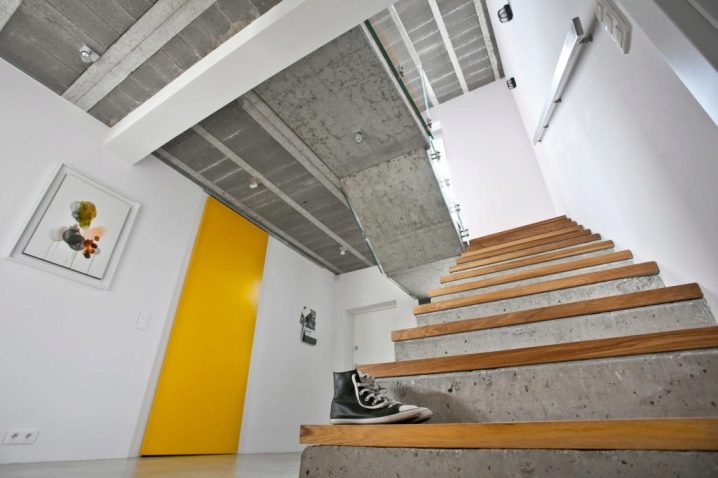
Water based
Water-based varnishes are rarely used for treating concrete surfaces, especially when sloping onto a protective coating.The material is chosen for colorless decoration of products and planes. A certified water-based varnish will be able to protect the base from the damaging effects of the external environment.
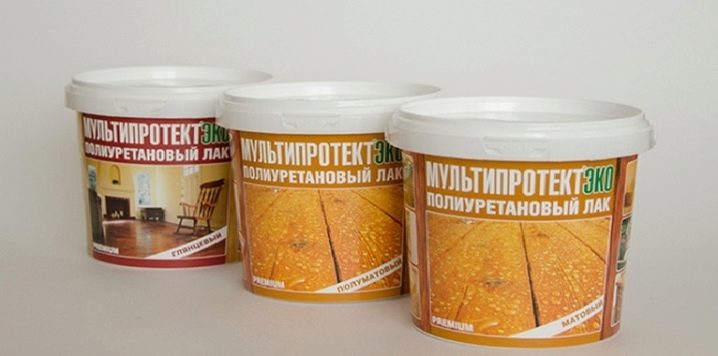
How to apply correctly?
Before using the varnish, it is necessary to carry out preparatory work. This process is necessary for the composition to lay down evenly, and also smoothly perform all the functions assigned to it. The work should be carried out in two stages. The first is preparatory, and the second is basic.
Preparation
When preparing the foundation, it is necessary to perform a number of actions:
- Clean the concrete surface. Remover from dust and other contaminants.
- If there are white marks on the surface, they must be removed by careful sanding. Such plaque appears due to the accumulation of salts.
- Next, a primer is carried out. This will significantly increase the service life of the post-treatment.
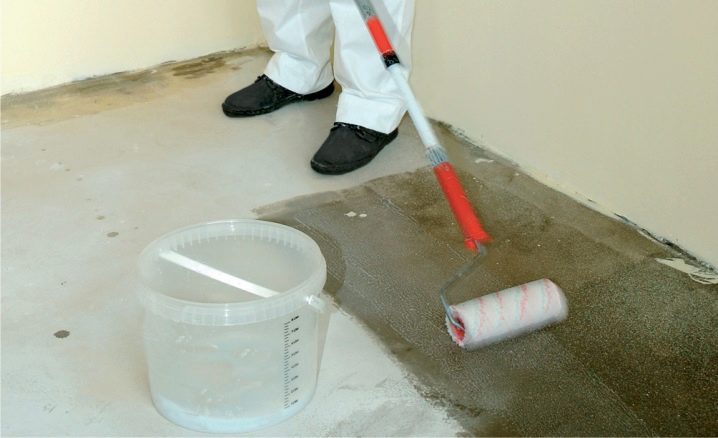
Varnish application
The main work on applying varnish should also be done in several steps:
- Apply varnish to the prepared surface. To do this, use pussies of various sizes, a roller or a spray bottle.
- Wait for the first coat to dry completely. The average drying time is approximately 2 hours.
- Only after complete drying (if required) is the next layer applied.
Remember: you can only walk on a treated concrete floor after 5 hours. Heavy and bulky equipment should be used only a day after applying the varnish.
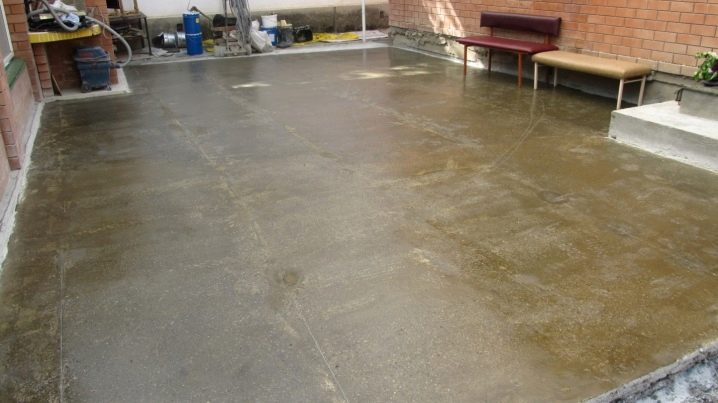
In the next video you will see a fragment of the process of applying Litapur 2KM matt polyurethane varnish.
Selection rules
When choosing a varnish, you must adhere to several basic rules.
- Don't skimp on consumables. Purchase products from trusted and trusted suppliers. A certified product is a guarantee of high-quality results and long service life.
- If you find it difficult to make a choice among a huge assortment, pay attention to popular and demanded brands. The brands "Texol" and "Tystrom" have earned the trust of buyers.
- Each train has its own expense. You need to know it in order to purchase the required volume of products.
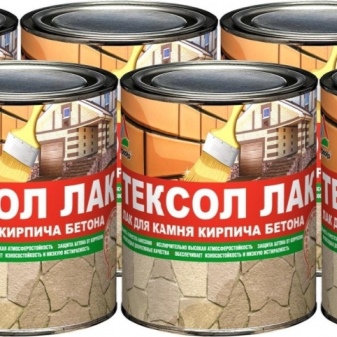
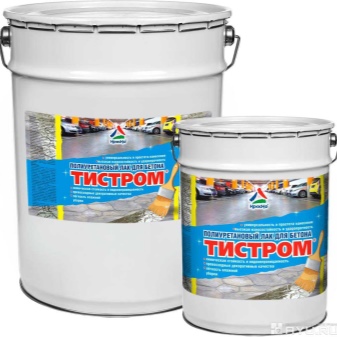
- Pay attention to the technical characteristics: thermal protection, abrasion resistance, wear resistance, resistance to cold, moisture, heat. The service life of the treatment and its practicality will depend on the correct choice.
- The external effect is also important. For some rooms, a matte texture is better, for others - a glossy one. Also, customers have the opportunity to choose semi-gloss and semi-gloss compositions. Matte outdoor lacquer will make the exterior softer and more versatile, and will also create a great backdrop for landscaping. While the glossy texture will attract attention with the play of light and shine.
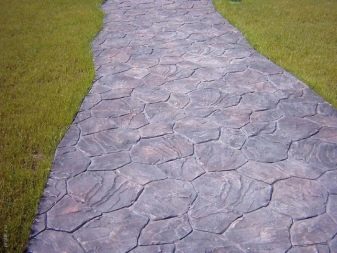
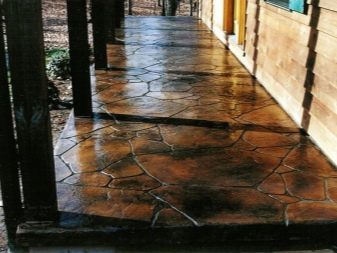
The comment was sent successfully.