Yacht varnish: pros and cons
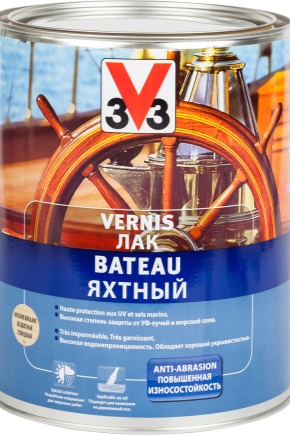
The invention of varnish in Europe is attributed to the German monk Theophilus, who lived in the XII century, although this point of view is not shared by many. Yacht varnishes are also called ship or yacht varnishes. There is an opinion that the names "deck", "yacht", "ship" are nothing more than an ordinary advertising move. Consider the properties, advantages and disadvantages of this material.
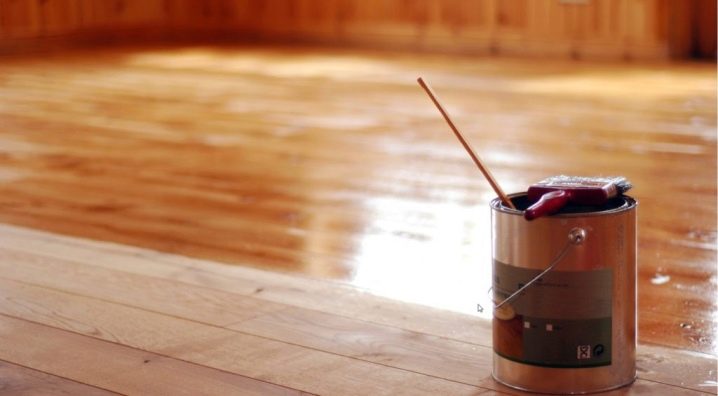
Scope of application
Initially, ship or yacht varnish was used in shipbuilding. It was applied to parts of the hulls of ships, boats and yachts made of wood in contact with water. They used it only outside, since the fumes from the varnish were poisonous enough for humans. This varnish is effective, water resistant and readily available.
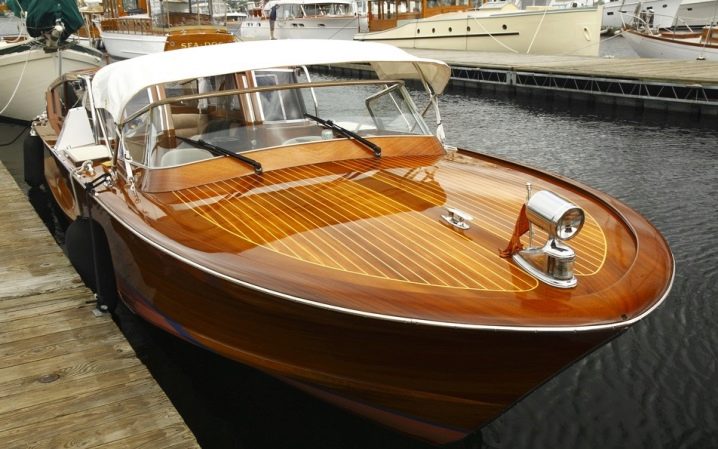
Today it is used not only for its intended purpose, but is used for varnishing the surfaces of parts:
- exposed to high loads;
- under the influence of an aggressive environment;
- during repair work inside and outside premises for various purposes.
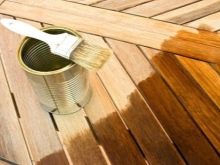
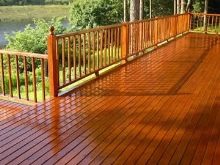
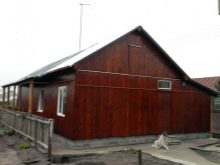
The main function of the varnish is protective. It forms a film based on urethane and modified polyesters that protects the material being processed.
Coating wooden structures with varnish on the outside provides reliable protection against moisture, sun heating, mechanical, chemical, biological and other damage.
This varnish is applied to a variety of types of surfaces and objects:
- pieces of furniture;
- musical instruments;
- over parquet;
- wood wall and ceiling panels;
- door frames;
- interior and exterior doors;
- wall cladding in saunas and baths.
It is also used when performing facade work (including covering a bituminous base).
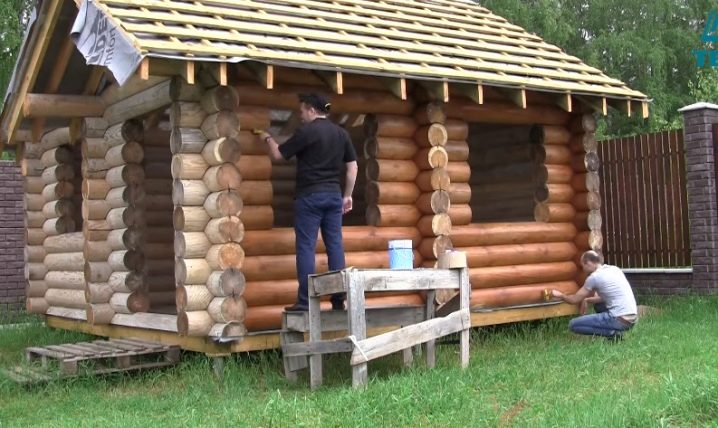
Advantages
Ship varnish has a wide range of significant advantages. Let's consider the most relevant ones.
- Excellent adhesion to wood. It has a high degree of adhesion to the surface material. Immediately impregnates the surface material, stays in wood structures for a long time and acts for a long time.
- Not affected by the harmful effects of UV. The sun has almost no harmful effect on the material covered with yacht varnish, as it contains special components that absorb this radiation, as well as light stabilizers that convert ultraviolet rays into heat. This keeps the protective film intact.
- Makes the surface attractive. The decorative component of the coating plays an important role in drawing attention to the product. This coating looks well-groomed.
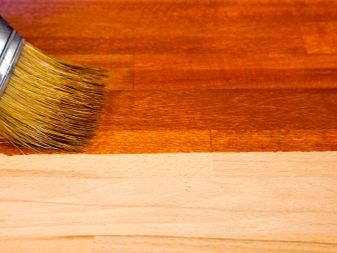
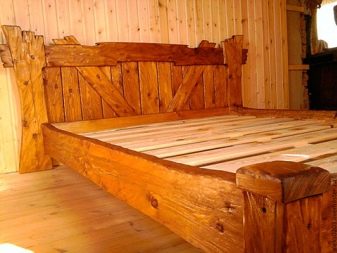
- Hydrophobicity. This tool increases the moisture resistance of wood, helps to get rid of the destructive effects of rot, the appearance of mold or fungus that destroys wood.
- Wear resistance. The film ensures durability and abrasion resistance of the material. At the same time, the coating is protected from scratches and chips.
- Resistant to chemicals. There is no reaction with acids, alkalis, salts. This allows, if necessary, to wipe the surface using household chemicals.
- Elasticity. The surface coated with this varnish can bend without significant damage to the film. Moreover, it will not crack.
- Relatively low price. Availability at purchase is another advantage of yacht varnish among other properties. Saving money makes these products in demand among a wide range of buyers.
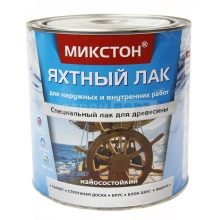
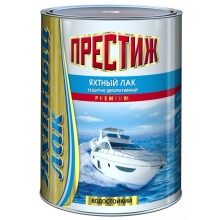
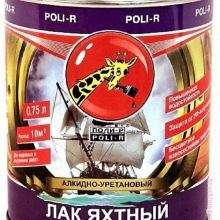
disadvantages
Yacht varnish is fragile in the cold.It cannot withstand low temperatures: this changes the properties of the material. In addition, it is hazardous to health. To improve the use of these materials, many manufacturers include various components in the composition. The problem is their toxicity.
Xylene and toluene are substances of the benzene group, whose toxic vapors enter the human body by inhalation and through the skin.
Such poisoning causes great harm to the human body., therefore, when working with yacht paints and varnishes indoors, safety measures are a must. Through ventilation, the use of respirators or gas masks is strongly recommended. Thanks to advances in production and the development of new technologies, today some varieties of yacht varnishes can be used for indoor work. From the point of view of human exposure, yacht varnishes based on acrylics cause the least harm to health, since they are produced on a water basis.
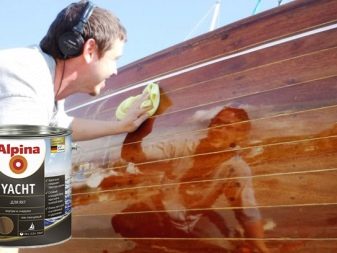
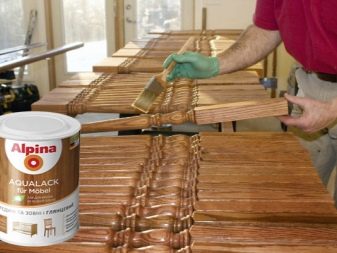
Protective coatings
To choose a varnish, it is necessary from all the variety of today's offer to choose a paint and varnish material that is suitable in composition, properties, appearance.
Consider the varieties of yacht varnish:
- Alkyd view is the most popular among buyers. It is durable and inexpensive. However, it cannot be used in closed rooms due to the toxic fumes of the components, therefore it is used only for outdoor work.
- Urethane-alkyd contains toxic substances, like alkyd varnish, but in much lower concentrations. For this reason, it is allowed to be used for interior decoration of premises. The film it creates is heat resistant thanks to the urethane plasticizers included in this type of varnish. Urethane alkyd is the only varnish that can be used in combination with a "warm floor" without the fear that cracks will appear during operation.
- Alkyd-urethane type resistant to sudden changes in temperature, it dries quickly enough. However, the varnish itself is toxic, so it can only be used outdoors.
- Acrylate varnish produced on a water basis, it contains a low percentage of harmful substances, it is the safest to dry and use. This type of varnish is called yacht varnish, but it is not recommended to use it where it can come into contact with water, which refutes its name.
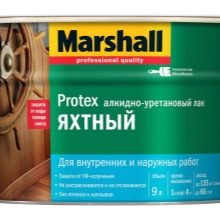
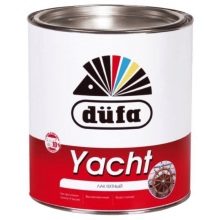
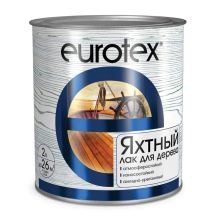
According to the reflectivity of light, the varieties of deck varnish are divided into three types:
- Glossy has a good degree of light reflection, but requires more care when leaving, ideally smooth surface for application.
- Matte ones do not reflect light as well as glossy ones, but they mask the dirt that has got on them, visually hide irregularities.
- Sometimes varnishes are called semi-gloss or semi-gloss.
Application methods and safety measures
Any ship varnish is applied according to certain rules.
- It is necessary to thoroughly clean the surface from any irregularities, residues of glue, paint.
- It is recommended to apply varnish at temperatures from +150 to +35 degrees C and air humidity below 80% using a roller, brush, or spray.
- The wood must be dried to a moisture content of less than 20%.
- It is advisable to prime the surface before painting using disinfectants.
- The varnish is applied in 2-3 layers, it is possible to add color combinations.
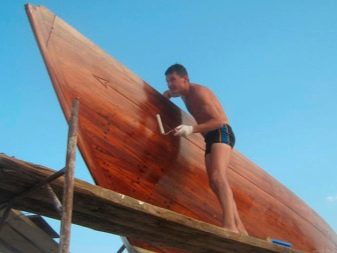
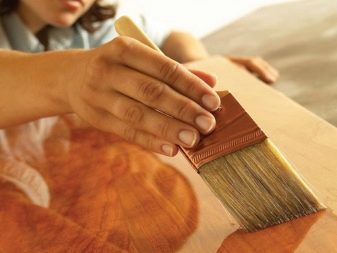
- The degree of drying of the varnish, at which it ceases to be sticky when touched, is about four hours.
- It is imperative to check that it is completely dry before applying the next coat.
- Average consumption is 80-120 g / m2.
- When applying, it is recommended to use protective equipment; after finishing work, the room should be thoroughly ventilated.
This varnish is flammable. It is strictly forbidden to dispose of it in sedimentation tanks (sewers).
In conclusion, I would like to list some of the most reliable manufacturers whose products are in demand among buyers.These include: Tikurilla (flow rate 1 l / 11 m2), Eurotex, Marshall, NovBytKhim, Rogneda, Polir, Neomid, Belinka.
See the result of painting the boards with yacht varnish in the next video.
Was delighted with the high quality Dulux yacht varnish.
The comment was sent successfully.