Cast iron fireplace insert: device features

A fireplace is an invariable attribute of every private house, it is a symbol of the hearth, not only performing a heating function, but also giving the room a special comfort. Its most important detail is the firebox, it is good if it is made of cast iron, a material that can retain heat for a long time and withstand high temperatures. This element has its own characteristics that must be taken into account.
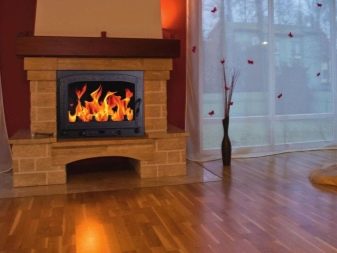
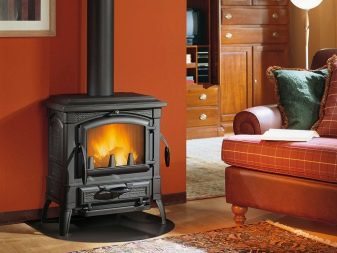
Cast iron design feature
The firebox is the main device that provides combustion of firewood stacked on the grate. Combustion is carried out by means of air supplied to the chamber.
The combustion chamber performs several tasks at once:
- it can be the main source of heating;
- is an additional heating component;
- plays a decorative role in the design of the room.
Taking into account these options, you can choose the furnace that is optimal in terms of power and other characteristics.
The fireplace consists of a facing part, a chimney and a combustion chamber. There are subdivided models closed with different types of dampers and open ones, which are practically not in demand due to frequent fires and low efficiency.
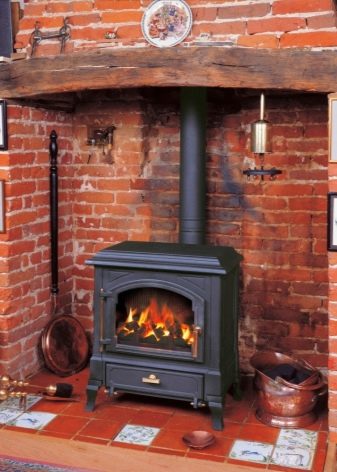
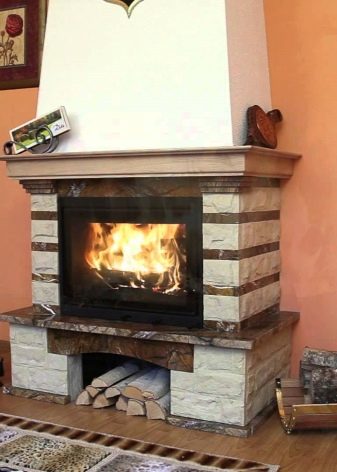
A cast iron fireplace insert consists of several elements that are important for the working process:
- a compartment for the combustion of heating materials - in this case, such a solid fuel as wood;
- some models have a door - a damper, fireproof glass or forged grating, such models are considered closed;
- necessarily the design provides for a smoke exhaust duct, through which combustion products are removed to the street - this supports the correct operation of the unit;
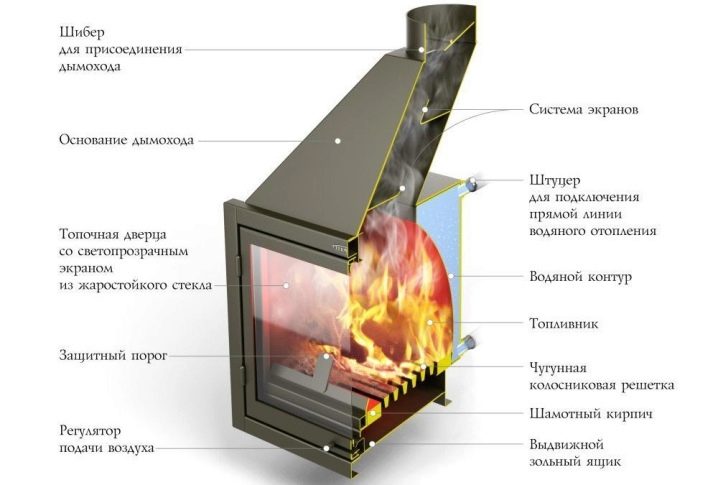
- a special air supply system with power adjustment parts in order to reduce or increase the combustion force;
- the ash pan is the place in the structure where decay products accumulate, it must be cleaned regularly, first pushing it out and then installing it back.
When choosing ready-made structures, it does not hurt to pay attention to additional options, they are often quite useful. For example, a self-cleaning glass door system.
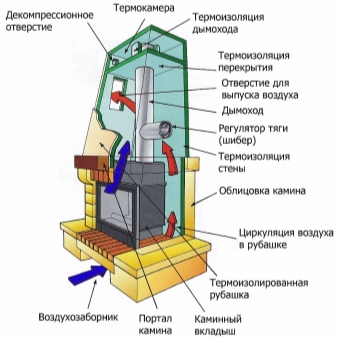
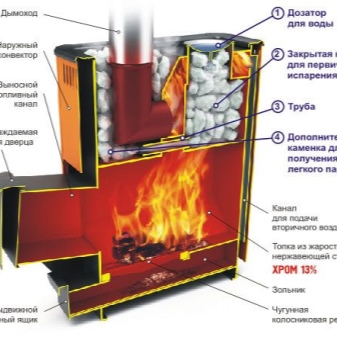
Types and design
Ready-made cast iron fireboxes are made in different design options. They can have a classic rectangular shape. But there are models made in radical, ultra-modern variations. There are angular, panoramic and prismatic designs in shape.
There are “aqua” devices with a water circuit for heating water coming from a centralized heating system. This is the most environmentally friendly type of appliance, equipped with a water jacket, a special cavity located on all sides of the firebox, due to which heating is maximum.
Such equipment can act instead of central heating or be operated simultaneously with it, is used for private houses with a large area.
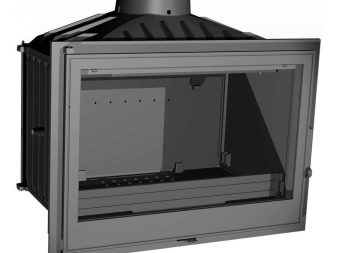
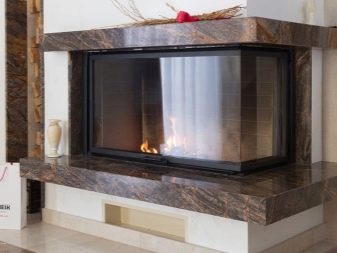

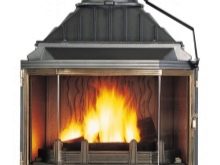
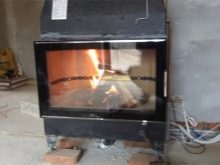
Vermiculite fireplaces are characterized by high fire resistance, resistance to critical temperatures and safety. Vermiculite is a modern thermal insulation material of natural origin that does not contain toxins and is durable in operation. It can be a full-fledged alternative to the cast-iron "chimney tooth" - the back inclined wall of the firebox.They are lined with the inner surfaces of the combustion chamber, which are in direct contact with the fire.
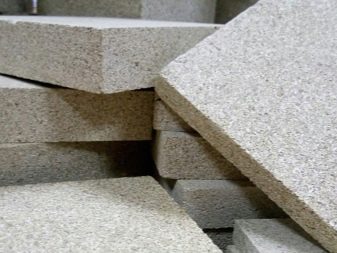
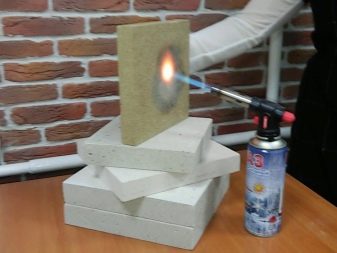
By the type of combustion, a higher heat output is given by hearth fireplaces that work without a grate, mainly with a steel or cast iron firebox, for which vermiculite is used for lining.
Also available are cast-iron heat chambers for barbecue, which are a brazier with or without a lid, used in the fresh air.
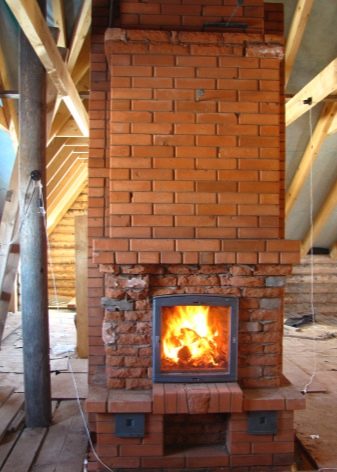
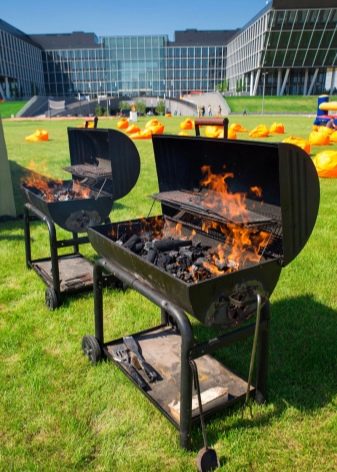
Advantages and disadvantages of a cast iron furnace
Cast iron furnaces have indisputable advantages over their counterparts - fireclay and steel types.
The advantages of such equipment:
- cast iron has maximum heat transfer, can operate in continuous and economical mode;
- this option has increased resistance to high temperature amplitudes, is not subject to deformation, since the material is thermoplastic;
- closed models have an efficiency of up to 80% and can serve large areas;
- cast iron construction is more convenient to use, its assembly is simple;
- such structures have the longest service life - up to 50-60 years.
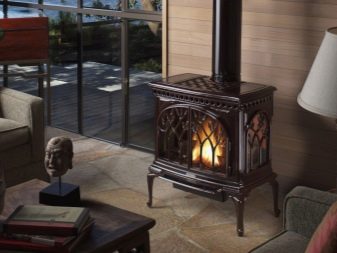
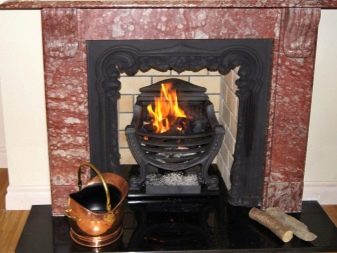
An undoubted advantage is the mobility of cast iron products - the compact unit can be moved around the house and transported. Standard heat-resistant glass is generally not contaminated due to the soot-emitting channels. In addition, different types of fuel are suitable for a cast iron furnace.
The disadvantages primarily relate to open models, which have low efficiency, since most of the heat (almost 85%) goes through the chimney. In addition, they create a fire hazard situation, and ancillary equipment at home is required to avoid a fire.
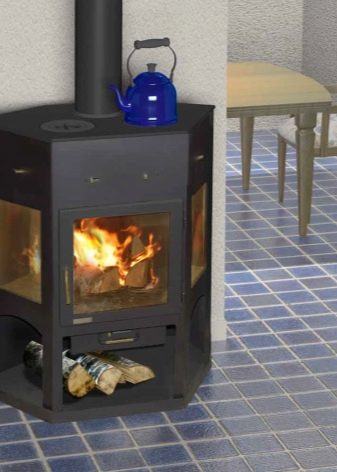
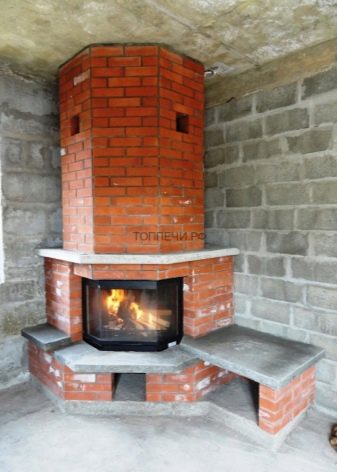
For closed versions, especially inexpensive ones, the quality of the glass leaves much to be desired. There is also an insufficient view of the viewing windows and a uniform color scheme - in fact, all options are made in dark colors.
True, this disadvantage can be eliminated by fixing decorative gratings on the fireplace.
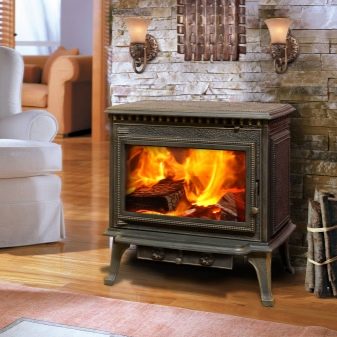
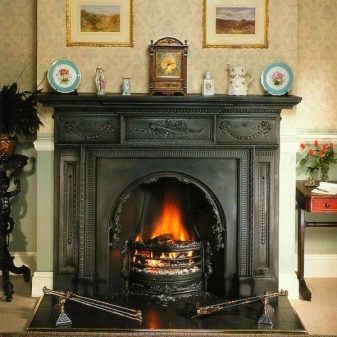
Fuel types
How to heat properly is the main question when installing cast iron equipment. It is already clear that this is wood, but it can be different and has its own characteristics of combustion.
Firewood is a natural material that, in addition to good heat release, has a pleasant smell, but not everyone knows that not all raw materials are suitable for heating. Wood material that has been stored for at least one and a half years should be used.

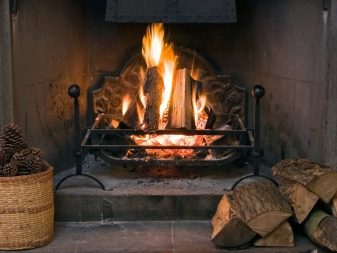
Different types of trees have their own type of combustion, it should be borne in mind that:
- coniferous varieties quickly burn out and emit a large amount of resin vapors, which can be unsafe for health;
- birch, despite the fact that it gives a lot of heat, smokes heavily;
- apple, juniper and cherry are mainly used to create coziness due to their pleasant aroma;
- any soft wood species - alder, linden, chestnut, willow, poplar, emit a little heat and burn quickly.
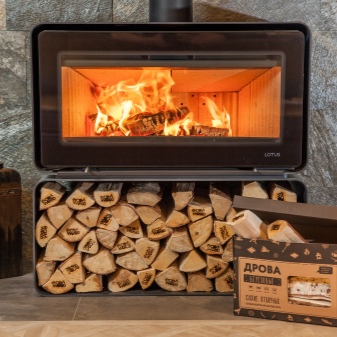
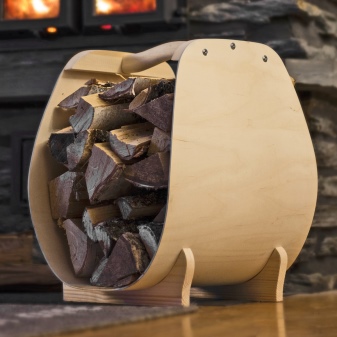
It is most effective to use hard wood material such as oak, pear, ash, poplar. It burns well, produces high heat output. The only relative difficulty is the processing and ignition of these trees.
If you do not attach importance to the woody aroma and characteristic crackling, you can heat cast iron stoves with other raw materials, for this anthracite, peat, coke, charcoal, brown and coal are suitable. For different types of coal fuel, accurate calculations should be made, since it can give a temperature above 1200 degrees during combustion, which can cause the cast-iron chamber to melt.
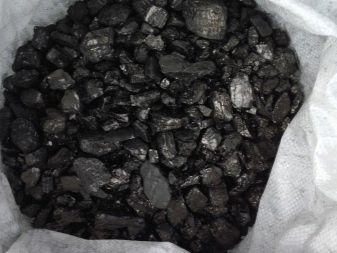
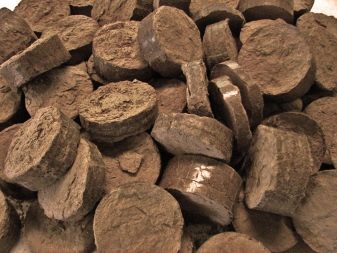
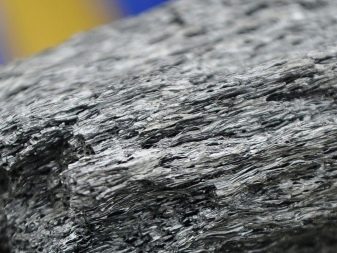
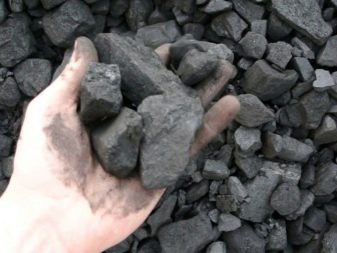
Preparing for installation
Do-it-yourself fireplace installation is a difficult job that requires a clear understanding of the workflow and sequence of actions. The success and duration of the equipment operation depends on the quality of the installation.
After choosing a suitable model, it is necessary to find the optimal place for its placement.The room must be provided with normal circulation of air masses - reverse draft can lead to poisoning of residents with carbon monoxide.
In advance, you should think about high-quality thermal insulation between the wall and the fireplace, taking into account the existing safety standards.
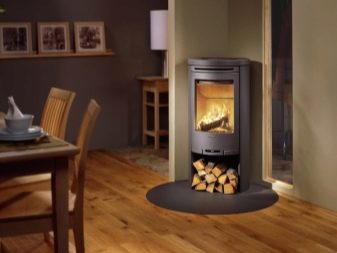
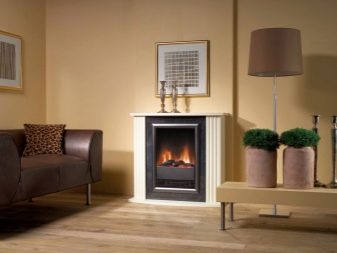
Cladding work is equally important. Cast iron stoves are very hot to keep warm for a long time, the fireplace should be sheathed with bricks, ceramic tiles, natural stone or drywall. Some perform outdoor cladding with porcelain stoneware, marble or metal.
Finishing with any coating also fulfills an aesthetic task in order for the fireplace to fit into the interior with dignity.
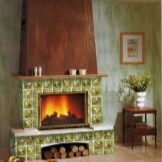
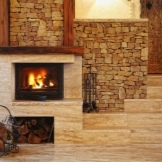
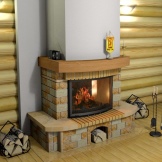
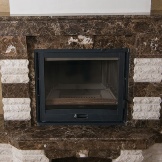
For work, you will need the following materials and tools:
- heat chamber cover;
- special thermal insulation products;
- decorative elements;
- cement mixture for mortar;
- building level, plumb line, spatulas.
In order to reduce the installation time, not to carry out additional insulation for cladding, you can immediately choose a material that tolerates high temperatures well - it can be refractory brick, fireclay, pre-plastered plate, stove tile specially designed for these purposes. Otherwise, along the perimeter of the firebox body, you will have to carry out insulation with foil foamed foam or other refractory materials.
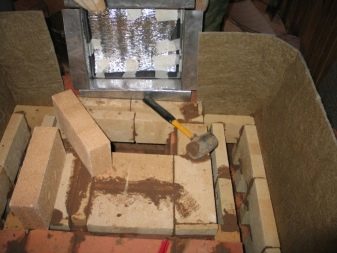
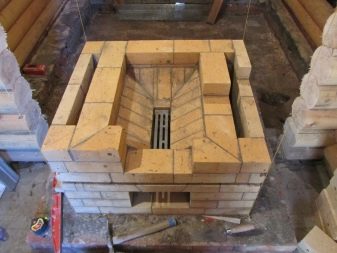
Rules for installing a cast iron fireplace
In order to carry out the installation correctly, you will need a fireplace project, developed personally or by professionals.
- First, the base is erected, the floor is removed from the floor, and the platform is made of fire-resistant material. Usually, its width is taken equal to the width of the fireplace with the addition of 20 cm on each side with a total length of at least 50 cm.
- The distance from the oven to the wall must be observed (20 cm). Spaces of up to 6 cm are left between the facing plates and the firebox - this is necessary for the free passage of air.
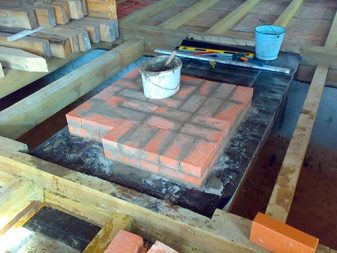
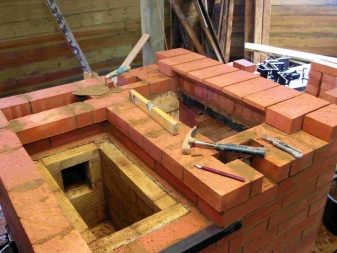
- The floor part near the building is finished with special glass or metal.
- The axes of the combustion chamber and the chimney should be positioned as close to each other as possible.
- For strengthening, the connection with the chimney is sealed with heat-resistant materials and pastes.
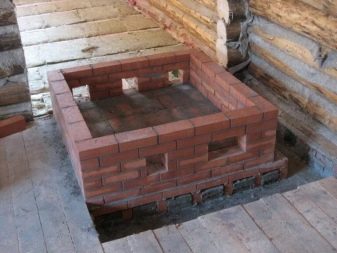
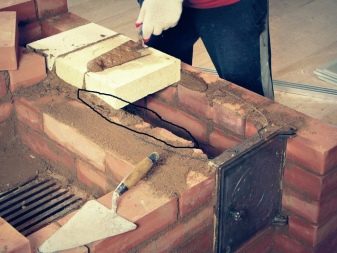
The thicker the outer shell, the longer and better the fireplace retains heat. It is important that a sufficient amount of cold air is supplied to the equipment from below, and hot air can freely escape from above. After covering the firebox, they begin to isolate the chimney.
You can decorate the heat chamber with fire-resistant tiles, especially if brick is used for decoration. But this should be done only after the masonry is completely dry.
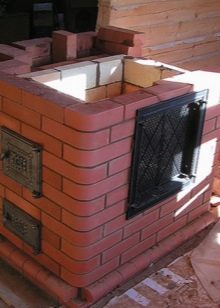

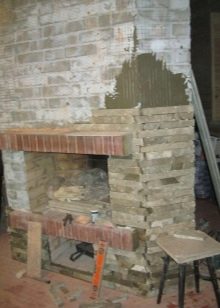
Manufacturers
Russian-made cast iron furnaces are of high quality and have many positive characteristics, among which are high efficiency, durability, high heat conductivity.
The following equipment is in particular demand:
- Fire chambers "Selenik" - closed heat chambers with a capacity of 14 kW. They are distinguished by decent quality and affordable prices.
- "Promo" (12-14 kW) - these structures are capable of heating rooms with a huge area of up to 150 sq. m.
- "Axioma" - furnaces with a slide gate, with a capacity of 12 kW. Heating areas up to 140 sq. m.
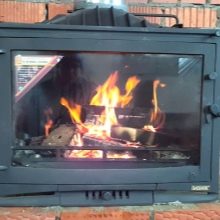
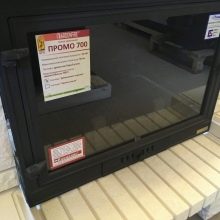
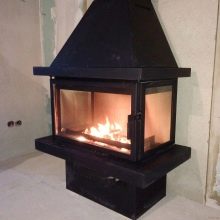
The most popular are the modifications of the Meta group - reliable fireplace constructions with a low price and different power. Dimensional models cope with heating large rooms with a size of 200 square meters. m.
Among the foreign analogues of the products, the most noteworthy are the furnaces from France - Invicta "Grand Vision 900" with a power of 18 kW, Godin B16 and Invicta "Double Port". They have the best technical and operational characteristics, but they also have a significant drawback - high cost.
In Russia, no less high-quality equipment is produced, but it is much more affordable.
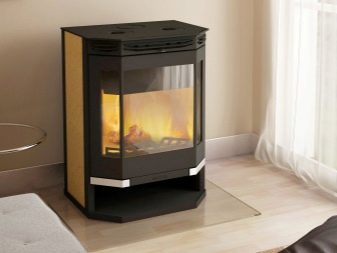
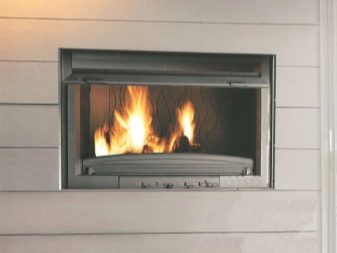
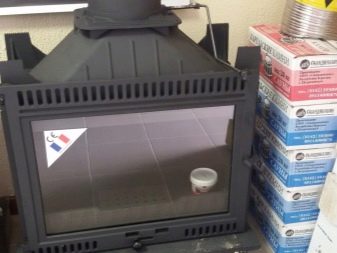
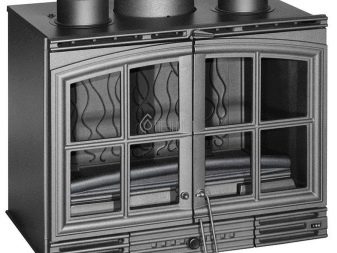
For information on how to make a fireplace with a cast-iron firebox with your own hands, see the next video.
The comment was sent successfully.