Features and stages of laying plywood on the floor

A number of modern floor coverings require a backing, which can be regular plywood. It allows you to make the base more rigid and even, reliable. They lay plywood on concrete, make the floor along the logs. This is not the most difficult task, although without basic theoretical knowledge, coping with it can be a problematic mission. If the task is to do everything competently and on a budget, you need to familiarize yourself with the installation rules.

Choosing plywood
Plywood is a finishing sheet material. In it, thin cuts of wood, called veneer, are glued together in layers with a synthetic adhesive. Each saw cut has a millimeter thickness (or slightly more). There are 3 or more veneer layers in a plywood sheet. The more of these layers, the thicker the plywood sheet will be and, accordingly, the stronger the material will be.... But the strength characteristics of plywood are not limited to this alone.
When choosing plywood for repair, you need to competently approach this. If you choose the wrong size, the flooring will not fit well.
When making a choice, you need to pay attention to important points.
- If there are no irregularities and defects, and the plank surface needs cladding to level the potential gaps between the parts, it is better to choose a material with a thickness of 6 mm. But it must be plywood without traces of rejection.
- If plywood is needed to adjust height differences and curvatures, which can be called significant, take plywood sheets of 12-15 mm. This will be a good substrate, providing the future coating with strength and durability.
- If during the flooring there is a problem of the impossibility of fitting the edges of adjacent parts under the same level, you will have to lay 2 layers (10, 12 mm each). So, the first layer will eliminate the main defects, and the second will remove the curvatures.



It is also important in which apartment or room the substrate is located. If there will be no massive furniture, then you can lay plywood 12 mm thick. If the floor is laid in a room with high traffic, if there will be heavy furniture or equipment, sheets up to 22 mm thick will be laid.
And, of course, what matters is what the floor will be. In this case the thickness of the material should be an adjustable characteristic. For example, laminate and linoleum are not so afraid of base movements associated with deformation, therefore they are also mounted under a single-layer flooring.
A two-layer scheme is used more often under the flooring of hard materials such as tiles with enhanced moisture resistance characteristics.



Alignment methods
The best alignment method depends on the substrate material and the condition it is in. This means that initially you will have to make an audit of the floors that are to be leveled.
It is worth listening to the recommendations of the experts.
- If the surface difference does not exceed 2 mm per linear meter, there is no need for special alignment for plywood laying. The surface putty will, in principle, be sufficient.
- If uniform deformation changes in the floor are detected up to 10 mm, you can align with fixation of auxiliary anchor points, adjustable in height. These will be either self-tapping screws with a wooden element, or anchors-bolts for a concrete screed.
- If the differences in the base are serious, up to 25 mm, the alignment can be carried out with point or tape backing supports, which are installed in the low areas of the base.
- If the base is even more uneven, then an effective solution would be to align with adjustable lags fixed on the studs. And already on this system, sheets of plywood are laid and fixed.
Plywood sheets are purchased, as a rule, with a margin of 10%. If there is a choice, the material that produces the least unused residue will be optimal.
Usually calculations are carried out on special calculator services.
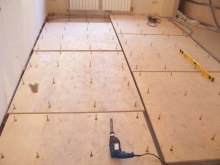


How to lay on the floor?
Whatever the choice of the method of laying, leveling, work begins with preparation. And it's very important to do it right. It should be of high quality, without haste and ignoring important details.
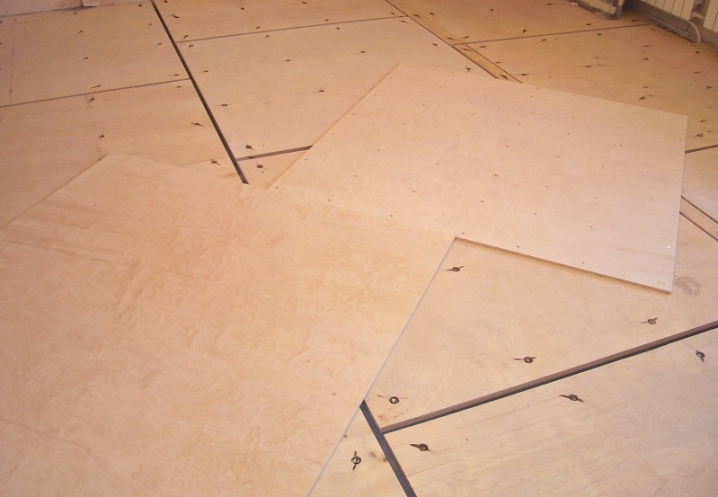
Preparatory work
Plywood sheets brought home or to the place where the new floor will be installed must go for acclimatization. That is, for a couple of days they just need to lie down indoors. This is a necessary measure so that later already laid sheets are not deformed. Plywood during this adaptation period should be kept only horizontally, in a pile.
If the sheets were purchased in the winter, it will not be superfluous to ask the seller how they were stored. If plywood was stored in warehouses without heating, then it will take 3-5 days to adapt indoors. If the installation of plywood occurs in an area with high humidity, then plywood should be laid with increased water resistance. True, there is another option: instead of expensive waterproof plywood, you can take an ordinary one and prepare it for special operating conditions.
Preparation of sheets includes several points.
- It is necessary to prepare a polymer-adhesive putty according to the manufacturer's instructions.
- Each plywood sheet is covered with putty evenly on both sides and ends. It is convenient to apply the composition with a spatula or a wide brush.
- It is necessary to cover the plywood with putty in 2 layers, and the second is applied only after the first has dried. Then the material is left for 3-4 days.
- Dried slabs are treated with an antiseptic, and it must also be allowed to dry.


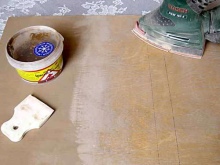
The surface must be prepared for leveling as follows:
- floors should be cleaned of dust and dirt;
- if the base is made of wood, it is checked for creaking and inter-board gaps; if the laying will be done on a concrete floor, it is checked for chips and cracks;
- if damage is found, they need to be repaired (primer, sealant, etc.);
- such preliminary repair is necessary if it is necessary to strengthen the thermal insulation of the floors and protect them from moisture penetration.
The repaired surface is tested for evenness with a building level, with a laser, the measurement accuracy will increase even more.
If you plan to make a substrate on the ground floor, it is possible to use a vapor-permeable film, it is needed for ventilation.



Floor marking and installation of logs, insulation
Leveling the floor with a device on logs is a fairly popular method. It is simple, since it is not difficult to bring the lags one level. It is popular for both the ability to lay insulation and soundproofing underlay. In this design, you can also hide communications. The work is carried out quickly, there will not be many "dirty" stages.
Finally, this method is also popular because such a substrate for a laminate or other material is not so expensive.

The workflow algorithm should be followed.
- The surface that has been previously repaired, cleaned and primed must be marked with a laser level. This is how the zero line of the new coverage level is calculated.
- This is followed by the marking of the steps of the installed lag on the surface of the rough base. Usually this is a step in the range of 570-600 mm. When marking, the fact is taken into account that the parallel logs closest to the wall are placed at a distance of 80-100 mm.
- Logs are laid out on the floor along the markings. Lags are called beams, the sizes of which can be different, for example, 60 by 30 mm.
- In order for the lags to reach the required level, you will need wooden pads, metal coasters or hairpins. They also regulate the height of the lag along the length.When using stands, it is worth remembering that they are attached with dowels to the base.
- Whatever fasteners the lags are fixed with, the fastening elements are located in increments of 600 mm. The beams are marked out, holes are drilled. Screw caps or nuts must be sunk into the wood.
- Next, you need to mark the location of the holes in the base.... The lags move, holes are drilled, the selected fasteners will be installed in them.
- A dowel is placed in the hole in the base... A hairpin is placed there. A nut is screwed onto it, put on a fairly wide washer, which has become a support under the bar.
- Then lags are pushed onto the hairpins, marked by level. When the beam needs to be raised / lowered, it is enough to tighten the nut in the desired direction.
- Put a washer on top of the stud, tighten the nut. It is convenient to cut off excess pins with a grinder.
- If the renovation takes place on the ground floor, there must be waterproofing under the final coating. For example, plastic wrap, roofing felt, glassine.
- The next stage is the installation of insulation. For example, mineral wool slabs. They will fit well into the space between the lags. Since the boards are elastic, they are pressed from the edges before laying. Then, straightening up, they turn out to be tightly pressed against the bars, with the desired quality of joints. But hard insulation cannot be laid so tightly, therefore the gaps formed with it are filled with polyurethane foam.
- Next, the insulation is covered with a vapor barrier, fixed on the logs with staples and a stapler.
After that, you can go to the main part of the work - it's time to fix the sheets themselves.



Laying plywood sheets
Plywood boards are fixed to the wooden base as follows. Fragments are placed on the floor according to the marks. Sheets larger than 1 m can be glued. It is necessary to maintain a distance of 2-3 mm between adjacent parts, the distance from the walls is 4-5 mm. The sections are fixed with screws, the length of the fastener usually exceeds the thickness of the plywood sheets by 2, and more often 3 times.
The pitch of the screws is calculated relative to the size of the pieces: for large products - at least 15 cm, if the sheets are not very large - 7-10 cm. From the edge, the indent is 20 mm. The hat must be flush. All places must be verified by the level. Adjacent joints between rows are shifted.
But in some cases, a finishing floor is made of plywood. Why do you need to lay a rough flooring of sheets of 2-3 grades. Then top-class plywood is prepared, in this case it is the facing. The material must be cut into fragments convenient for laying. Parts are sanded and stained in the required number of layers.
The cut fragments must be laid on liquid nails. They coat not one seamy side, but also the joining edges. Excess adhesive must be removed immediately. The dried floor is varnished in several layers.
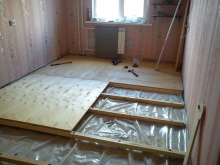


Finishing
Plywood, as already mentioned, may not be a rough floor, but a clean one. It is cut into fragments, from which a kind of parquet is obtained. The plywood of the lower grades is sheathed with plywood of the highest grade, cut into squares or other fragments. Each fragment can be painted with its own shade, or you can simply varnish it. Previously, they often make a stain in several layers and only then varnishing.
This option can be very interesting, albeit time consuming. After all, cutting the sheets alone will not work quickly, and if this cutting is also planned, calculated, thought over from the point of view of design, this is a serious work.
But for many, this option is ideal: and even if you need to work with glue for a long time, if you have to cover up the seams, choose the tones of the stain, this experience still fits into a small budget.


Recommendations
It should be remembered that the main enemy of plywood is dampness. It just destroys this stuff. If there are sudden changes in humidity, the plywood is likely to suffer. That is, it is necessary that the constant humidity in the room be at the level of 70%, not higher than that, and the short-term humidity should not be higher than 80%.It is strictly forbidden to lay plywood sheets on a damp base.
By the way, you can check the moisture content of a wooden base with a special device. But the concrete floor is checked like this: it is covered with a film for a day. If condensation appears under the film, then there is no need to rush to install the plywood sheets.
They also need to be laid in temperature conditions up to 30 degrees (but not less than 20).


Do not ignore antibacterial impregnations that will protect the leaf from the pathogenic action of fungi and other microorganisms that affect the state of the material. Acrylic varnish increases the strength of the sheet. If you fulfill the minimum requirements for the preparation of the material, its acclimatization in the room, the sequence of working with it, you can most likely predict the successful laying of plywood.
An interesting trend: recently, women also like to work with this material. And we are talking about laying the floor too. Perhaps this is due to the availability of tools / materials, an increased indicator of the comfort of interaction with them. It is possible that the matter is in the growing number of accounts, pages, channels where women demonstrate their success in repair.
Good luck!
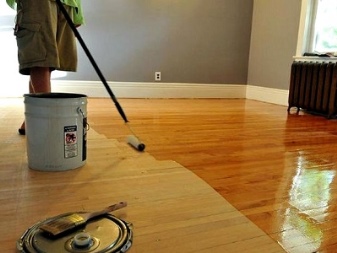

You can find out how to put plywood on a screed from the video below.
The comment was sent successfully.