All about film faced plywood
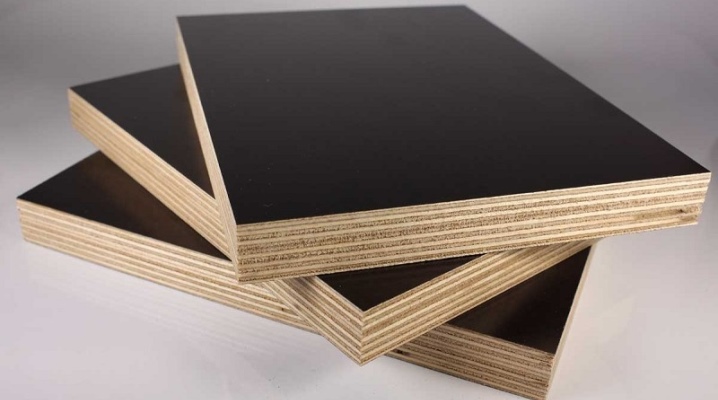
There are many types of domestic and foreign film faced plywood on sale. In the article we will give a description of them, consider the characteristics and application features.

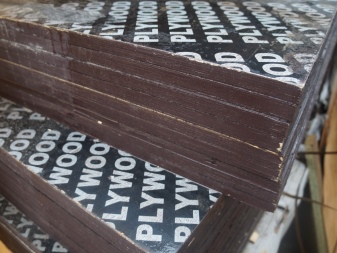
What it is?
Film faced plywood is a plywood that is not afraid of water and is resistant to mechanical damage due to a special protective shell that covers it from the outside. The inner layers, like ordinary plywood, are made of several layers of glued and pressed veneer (thin sections of tree trunks from 1 to 10 mm thick), fiberboard or a combination of these materials. To impart increased moisture resistance, veneer layers can also be impregnated with water-repellent compounds.
Typically, the technology for creating film faced plywood involves the following:
- veneer layers are impregnated with waterproof and adhesive compounds and joined by hot pressing (pressure from 13 to 30 kg / cm², temperature - 130 ° C);
- the surface of the resulting plywood sheet is sanded and a laminating film is thermally applied;
- the ends of the laminated plywood are protected with an acrylic compound, sometimes they are also laminated, but this greatly increases the cost of the material.


The result is a technologically advanced material that should perfectly withstand 50-100 turnover cycles, six-hour boiling in water, contact with an alkaline medium, hot water vapor or liquid concrete. Its surface is resistant to mold, open burning, easy to clean, allows the use of metal fasteners. At the same time, it is affordable, light in weight, and easy to process. It is these unique characteristics that some types of film faced plywood have, and this makes them indispensable in various industries - from furniture production to aircraft construction. However, for improved moisture resistance, their impregnation and coating may contain a large percentage of toxic phenols that are harmful to health.
But there are special types of products that meet the high requirements of Russian and international standards (BFU 100 DIN 68705, GOST) in terms of the class of emission (emissions) of phenol. They can be safely used indoors. In their composition, phenol-formaldehyde is not used or is used in safe quantities, and not in the material of the upper layers, but only in the inner ones.
Additionally, the surface is covered with finishing films and varnishes, which are harmless and shield toxic fumes.


Specifications
All quality sheets must have the following characteristics:
- density of the laminate - 120-300 g / m², depending on the type of film - this provides high strength and waterproof properties;
- laminate thickness - 0.4-10 mm, the thicker the layer, the higher the resistance to mechanical stress and aggressive substances;
- the emission class for plywood used in residential premises must be at least E1 (no more than 10 mg per 100 g of plywood weight), for all other tasks - no lower than E2 class (no more than 30 mg per 100 g of plywood weight);
- moisture content of the material - 5-10%;
- the density of a sheet of film faced plywood is on average 650 kg / m³ - this ensures strength and the ability to withstand heavy loads comparable to those that a solid solid wood can withstand (for comparison: the density of solid beech - 650 kg / m³, oak - 700 kg / m³, stained oak - 950 kg / m³);
- maximum tensile strength - 40 MPa;
- maximum static bending strength - 60 MPa.


To achieve better strength, resistance to bending and torsion, the pieces of veneer are laid out strictly taking into account the direction of the fibers - stacking can be used at angles of 30 °, 45 °, 60 ° or 90 ° to adjacent pieces or the edge of the sheet. But in all cases, the veneer is placed symmetrically with respect to the central layer. Therefore, most often the plywood sheet has an odd number of layers (3, 5, 7, 9), although there are also 4-layer types.
The weight of a film faced plywood sheet depends on the type of raw materials used. The mass of a square meter of laminated birch plywood (FOB) is 1.95 kg with a thickness of 3 mm, with a thickness of 30 mm - 19.5 kg.
A standard sheet of such plywood with dimensions of 2440x1200 mm and a thickness of 4 mm weighs 7.7 kg, with a thickness of 21 mm - 40.6 kg.


Views
Film faced plywood is divided into several types depending on its characteristics and materials used for its manufacture.
By material of manufacture
Some hardwood hardwoods, especially birch, are best suited for making moisture-resistant plywood. It contains a lot of lignin - a natural polymer that gives the material high strength and at the same time elasticity, resistance to stretching and compression. Due to the suitable pore structure, the components of resins and adhesives penetrate well into the material and impregnate it, providing the necessary moisture resistance. Therefore, in accordance with GOST 53920-2010, high-quality moisture-resistant plywood with a laminated coating must be made of birch veneer corresponding to high grades A and B. Such products are marked FOB or FOF.
The standard allows the production of products with top layers of birch and inner layers of alder, maple, beech, elm, aspen or conifers. If poplar is used, then such additives are allowed no more than 10% of the total mass of the sheet, since a higher content of this loose wood can negatively affect the strength and durability of plywood. Combined plywood is in demand, which is made from alternating layers of birch and pine veneer, which allows combining the advantages of these materials to obtain a relatively inexpensive and high-quality plywood sheet. All pine plywood is also produced. Coniferous wood, due to its structure, is less susceptible to impregnation, therefore, in terms of moisture resistance, such plywood may be inferior to birch. But on the other hand, it is lighter in weight and affordable, therefore it is excellent for those tasks where a light and reliable material is needed - for example, for roofing, cladding.



By type of joint compound
Health safety is determined not only by the veneer and laminate material, but also by the composition with which the veneer was impregnated and glued. The type of impregnation is indicated when marking plywood:
- FC - urea-formaldehyde;
- FSF - phenol-formaldehyde;
- FBV, FBS - bakelite (phenolic-resole).
For residential premises and household tasks, plywood FC and FSF are used. Plywood FC is the most environmentally friendly - the urea-formaldehyde composition contains the least toxic substances and does not evaporate at room temperature. FSF plywood is considered the most versatile, and most of the products manufactured in Russia are of this type.
The most harmful glue, but also giving excellent performance properties, is bakelite; it is used only for industrial needs.



By type of laminate
Plywood is laminated with phenolic, melamine or polyvinyl chloride (PVC) film.
- Phenol-formaldehyde film - Kraft paper impregnated with phenol-formaldehyde resin. Has a characteristic dark brown color (if no coloring pigments were added). This coating is very dense, provides high moisture resistance, excellent performance. But it is used only for industrial tasks and outdoors, since it contains toxic formaldehyde.But for creating reusable formwork and temporary frames - this is the ideal option.
- Melamine foil - Kraft paper is impregnated with safer melamine-formaldehyde resin, which does not emit harmful substances at room temperature (below 40 ° C). Without the use of coloring pigments, such a film is light yellow or transparent, under it the natural pattern of the veneer is clearly visible. Such plywood externally looks like veneered (lamination and veneering are different technologies). But most often the film is painted in various colors and shades, a drawing or even a 3D relief that imitates natural materials is applied. Such plywood can be used in residential premises, for the manufacture of furniture.
- Polyvinyl chloride (PVC) film - a thin layer of plastic, which is thermally applied to the surface of the plywood. This is a completely environmentally friendly and safe coating - according to sanitary standards, polyvinyl chloride is approved for the production of dishes and even containers for donated blood. An additional advantage of plastic coatings is their aesthetics and many options for textures and colors.
Mesh, anti-slip coatings are sometimes applied in addition to the base laminate. For this, a special fine-mesh polymer mesh is used. Anti-slip plywood is needed for flooring in vehicles, for creating various decking, as well as for formwork. Plywood of the FSF type with a formaldehyde coating is usually taken as a basis.



By type and grade of coating
The coating can be smooth or corrugated, matte or glossy, one-sided or applied on both sides. Depending on the type of coating, the following markings are used:
- F - smooth surface;
- W - mesh surface;
- SP - smooth surface for painting;
- U - bare veneer without coating.


According to the quality of laminate application, the material, in accordance with GOST, is divided into 3 grades.
- 1st grade corresponds to the highest quality - the surface of the product should not have non-laminated areas and defects;
- 2nd grade allows no more than 10% of visual lamination defects that do not reduce the characteristics of the material;
- material with a large number of defects is referred to the lowest, 3rd grade.
If the sides have a different surface, two values are indicated in the marking through the separator. For example, F / W - film faced plywood, covered with a smooth film on one side and mesh on the other, grade 1/2.


Dimensions (edit)
For plywood sheets, there are optimal calculated sizes. After all the larger the plywood sheet, the lower its rigidity, and if the area is too large, it will bend like paper, deforming under its own weight. Because of this, the laminated film will peel off, and the plywood itself will crack, and it will not make good formwork or high-quality cabinet furniture.
In accordance with GOST, sheets are produced with sides of 1200, 1220, 1250, 1500, 1525 mm. Plywood, the length of one or all sides of which is more than 1525 mm, is considered large format. According to GOST, it is produced with sides of 2400, 2440, 2500, 3000, 3050 mm. The most popular sizes are 2440x1200, 2500x1250, 3000x1500 mm, they are considered the most versatile.


The sheet thickness can be 4, 6, 9, 12, 15, 18, 20, 21, 30 and 40 mm. In professional language, material up to 12 mm thick is called a sheet, over 12 mm - a plate. Manufacturers can also produce sheets according to their size. Among the popular sizes in length and width are 1525x1830, 1525x2950 mm, in thickness - 8, 10, 24, 27 mm. Many companies offer such products.
Also, plywood can be made to individual sizes. This is relevant if you need a plywood sheet of non-standard dimensions and with special properties that can only be imparted in the factory. For example, plywood with atypical dimensions, laminated on both sides and ends, is in demand for the production of factory and designer furniture, and is used for the installation of window sills.
Also sheets with special dimensions and coatings are in demand for various industrial purposes, the production of packaging, containers.


Manufacturers
On the Russian market, mainly domestic and Chinese products are presented, and a small percentage of the market is fixed for Finnish plywood. The material produced in China is in demand due to its low price, but its quality is not guaranteed by anything and may not correspond to what is stated on paper. You can come across both very high-quality products that meet Russian and international standards, and products from low-grade raw materials, containing a significant percentage of poplar veneer, unsafe in terms of emissions.
Finnish plywood is considered the safest - its quality and environmental friendliness are confirmed by international and European certificates. In addition, the Finns are considered world leaders in the industry, developing and introducing new technologies into the production of wood-based materials, in particular, safer adhesives. But Finnish plywood is more expensive than domestic counterparts.


Products manufactured in Russia, in most cases, do not differ from Finnish in terms of characteristics and safety, comply with international requirements and GOST standards, are made from high-quality domestic raw materials using modern technologies. The list of manufacturers is very wide, and you can easily find products with the desired properties.
Buying material from a well-known company that has earned a good reputation is a guarantee of the quality and reliability of the material. Among the Russian leaders in terms of the volume and quality of plywood are the Vyatka Plywood Mill, the Sveza Group, and Zavetluzhie LLC.
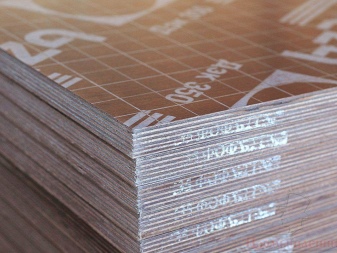

Applications
Film faced plywood finds its use in a wide variety of industries.
- In monolithic construction, film faced plywood - an irreplaceable material for the creation of formwork and temporary frames. It is resistant to liquid concrete, mechanical stress, can be easily cleaned with a solvent and helps to significantly reduce the cost of work, since it can be used 50-100 times. You can not even buy such a formwork, but simply rent it. With its help, the foundations of private and multi-apartment residential buildings, columns, bridges, ceilings are erected. For formwork, laminated FSF sheets with a thickness of 18-21 mm with a smooth or mesh surface are usually used. Such plywood is also widely used for the construction of temporary partitions, flooring, and fences.


- For external and internal finishing works, moisture-resistant and fire-resistant plywood with a smooth laminated coating is used. At the same time, it is recommended to use FC plywood with melamine or plastic coating for interior work in residential premises. It has good emission rates, while being moisture resistant. It can be used for covering both warm and damp and unheated rooms, for example, a country house, a bathroom. For decorative cladding, usually thin sheets of 8-12 mm are used - they have an attractive appearance, low weight, are easy to process, withstand metal fasteners.
Also, film faced plywood is widely used as a substrate for floor screed, a material for the manufacture of doors.

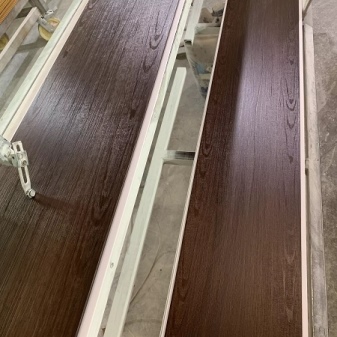
- The manufacture of durable, waterproof containers is another area where film faced plywood is indispensable due to its unique properties. FK plywood with a plastic coating is allowed to be used for the transport of food, medicine and medical products. It reliably protects the cargo, does not deteriorate when fruit acids or pharmaceutical products hit the surface, and has bactericidal properties. Thanks to these qualities, laminated plywood is often used to make shelves and display cases for pharmacies and shops, warehouses, cabinets for storing household chemicals. For these tasks, both thin 6 and 9 mm sheets are used, as well as thick 30-40 mm - it all depends on the severity and dimensions of the goods or the weight that the shelf must withstand.

- In the transport industry, it is important to lighten the weight of a structure as much as possible without sacrificing its safety and reliability. Film faced plywood copes with this task perfectly. Walls and doors of cargo vans, semi-trailers, cladding of railway cars, sea and river vessels are made from FSF sheets with a thickness of 18-30 mm. Mesh non-slip plywood is ideal for flooring in public and commercial vehicles. Public transport seats are also often made of laminated plywood. Thin 6mm plywood is used for cladding refrigerated vehicles and industrial refrigerators.


- In the manufacture of factory and designer furniture, laminated plywood is used very widely today. - it combines good safety, low price and attractive technical and aesthetic characteristics, looks good in any interior. Bearing walls and doors of cabinet furniture, shelves for heavy things are made of plywood FC with a thickness of 20-30 mm. Thin plywood (4-6 mm) is used for the back wall. The material 15-21 mm is well suited for creating standard shelves. Renowned design bureaus from all over the world actively use laminated plywood in their projects.


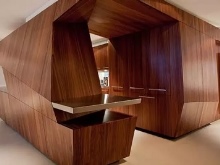
In the next video, you will find additional information on the properties and applications of film faced plywood.
The comment was sent successfully.