What is laminated fiberboard and where is it used?

The wood board market is saturated with a wide variety of products. Sometimes it is not easy to understand that several materials differing in physical and technological characteristics may belong to the same type. Fiberboard (it is hardboard or just a sheet of fiberboard) is one of the most versatile wood composites.
In Russia, most of the furniture is still made from such plates. This material is also used in the production of wagons. And in the construction business, partitions are erected from fiberboard in rooms, used for preliminary finishing of ceilings, it can even be laid on the floor. Relatively recently, laminated fiberboard has appeared, which is used for decoration. The material has different densities and levels of moisture resistance.

Peculiarities
This material, formed into sheets, is obtained by laying wood fibers in the form of a carpet of a specified thickness. Basically, for the manufacture of wood-fiber boards, waste obtained from the mechanical processing of wood was initially used. Today, whole trees can also be processed for this.
The shavings and sawdust are first mixed with artificial resins and antiseptics. Then it takes a certain time to compact the raw material by hot pressing. Based on how the material was pressed, Fiberboard is subdivided into several grades.
- Semi-solid (something like thick cardboard). Their density is 400 kg / m3.
- Solid (strong, pore-free). Density 850 kg / m3 - determined by GOST.
- Superhard (extreme stiffness). The density exceeds 950 kg / m3, its limit value is 1100 kg / m3.
- Insulating. This type of fibreboard belongs to the category of the least dense and is not used in places where there is a need to withstand even a small mechanical stress in the form of a load. Density is not more than 250 kg / m3.
- Finishing and insulating. This fiberboard is also not designed for loads. Its front part can be used to decorate rooms. The density of the slab is around 250 kg / m3.
- Soft (reminiscent of felt). Their lowest density is 100 kg / m3. This material is the first competitor to GKL, since it is very effectively practiced for finishing floors.



Fiberboard is relatively inexpensive, and if you use it only where the manufacturer advises, you can get a moisture-resistant, fairly durable and high-quality building material for quite reasonable money. In any case, today it is much cheaper to purchase a material containing wood than a solid dry board.
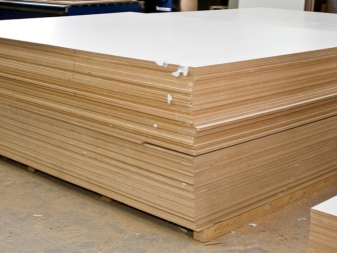

Production technology
Fibreboards are made from wood. To be more precise, not from an array, but from waste remaining during the processing of wood at sawmills and other wood processing industries. Additionally, the structure of the material can include used paper and its waste, other products containing cellulose. After crushing the components, the material is compressed into slabs and dried. To make the board resistant to moisture, various suspensions and precipitating substances are added to the fibrous semi-finished product.
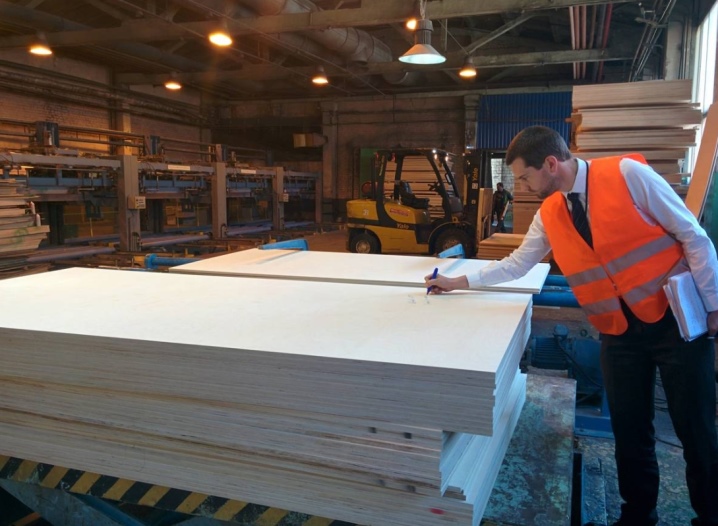
The fiberboard manufacturing process is divided into several stages:
- shredded wood waste is washed, after which garbage and sand are removed from them by means of absorption plants;
- then on disc centrifuges using electromagnets, metal elements are removed from the structure of the mixture;
- then the chips are sent for grinding, which can be both large and small, based on the conditions of use of laminated fiberboard;
- in the defibrator, kneading is carried out with the addition of resins, polymers and paraffins.
Upon completion of these activities creation of laminated fibreboard can be done dry or wet. In more modern industries, the dry method is practiced, only it is less environmentally friendly than the wet one. This is associated with an increased formaldehyde content in the binder mixture.


The lamination procedure has a number of features.
- After surface preparation work, the slabs are sent to a hot pressing machine, in which heated mineral oil is constantly circulated to maintain the temperature regime.
- Attached to the press is a form with a textured pattern that determines the type of future embossed print (wood pores, skin roughness, brick texture, etc.).
- Fiberboard sheets are covered with a specialized melamine film with a low degree of hardening, after which a hot press imprints it on the surface of the fiberboard.
- Under the influence of pressure and high temperature, fragmented melting of melamine-based resins is carried out, which diffuse into the surface of the material, sticking to it without the use of any adhesive composition
- ... If necessary, fiberboard can be laminated on both sides.
This impregnation method guarantees moisture resistance of the material, a very attractive exterior and excellent functional and performance characteristics.

The need to use expensive equipment and the amount of energy required to obtain a unit of the product lead to the fact that the cost of laminated fiberboard is not at all budgetary. In addition, it depends on the thickness of the processed board, the uniqueness of the color and the depth of the color embossing.

Thickness and colors
The application of a decorative layer (lamination) has practically no effect on the thickness of the board. Based on the purpose of the product, its hardness and thickness are selected. This manufacturing technology makes it possible to create LDVP with a thickness of 2.5 to 4 mm.
The manufacturing process of hard and superhard types of fibreboard provides for panels up to 12 mm thick, which are used on wall panels. However, hard specimens can be made in thicknesses of 2.5 mm, 3 mm, 4 mm and 6 mm. In addition, based on the intended use, the density of the fibreboard can also be different, regardless of the thickness.



Painting of fibreboard carried out with water-dispersion paints based on polyacrylates (mainly polymers of butyl, ethyl and methyl acrylates), as well as polymers as film formers. Colors can be varied - like indifferent (silver, titanium, deep black, white, brown), and pretty colorful (red, sky blue, neon bright lime). The decorative surface is fixed by means of a filling machine, in which several layers of varnish are applied, each of them drying to dry to protect the fibreboard from scratches.

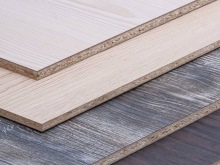

Differences from laminated chipboard
Laminated fibreboard (LFB) is manufactured using the same technology as laminated chipboard (LFB). The difference is that chipboard is produced by pressing shavings mixed with resins, while fibreboard consists of sawdust. Only they are first crushed into very small pieces, and before being pressurized on a press, they are processed with steam. These boards are significantly thinner than chipboards and are more flexible.
There is no decorative coating on the rough fibreboard, it is sanded on one side so that the surface looks smooth. It is advisable to use such a plate in those places that are invisible to others. This makes it possible to save some of the money, since a rough fiberboard is much cheaper than a decorated one.



Where is it used?
The use of laminated fibreboard depends on the characteristics of the panel. It has excellent sound insulation properties, and for this reason it is often practiced in those rooms where it is required to provide the utmost sound insulation - recording studios, radio broadcasting rooms. Fiberboard has perfectly demonstrated itself in office premises and educational institutions, where it perfectly copes with the role of a sound insulator.
The neat and smooth surface of the panel with the already applied texture of wood, granite, marble or other material is perfect for interior design both in composition with other materials, and when facing exclusively with fiberboard. This mainly applies to floors and walls with unsatisfactory surface quality.

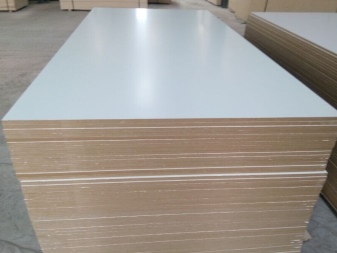
The specificity of using the plates, based on the technical parameters, has a number of nuances.
- Soft types have high porosity and therefore low density. Their use is appropriate for partitions and back walls of furniture.
- Semi-solid types are an order of magnitude stronger, but they are produced only for the rear walls of furniture wardrobes.
- Hard and super hard. This type of fiberboard has maximum strength. In this regard, doors, arches are made from it, and they are mounted on the floor.
- Finishing and insulating, as a rule, are laminated. A texture is applied to their surface. Such a fibreboard can be used for doors, partitions and possibly as a base material in the production of furniture items.
Wood-fiber panels, which have any kind of coating on one side or two-sided, are a promising material that never loses its relevance. They will be used both in facing work and in the creation of furniture, the construction of partitions and air arches, and composite suspended ceilings.
Laminated fibreboard will certainly be needed when performing repair and cladding work, the most important thing is the competent choice and knowledge of the methods of how to cut and lay it.
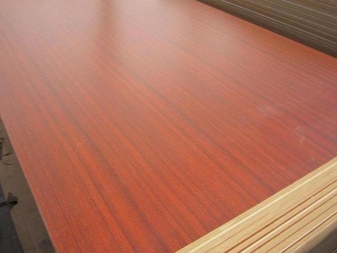

In the next video, you will learn how to lay fiberboard on the floor.
The comment was sent successfully.