Types of wood drying

Environmentally friendly natural wood is always in high demand and is popular, which is explained by the high degree of durability, presentable appearance and reasonable price of wood products. There are budget options for lumber, but among them there may be expensive ones, made from elite species of deciduous or coniferous trees. In addition to construction, lumber can be used to make furniture, household items, or musical instruments.
The quality of wood blanks depends not only on the characteristics of the wood species, but also on the degree of drying. If an undried wood blank is used for work, then over time the finished product will begin to crack and deform, losing its original appearance and useful properties. To prepare untreated wood material for further use, various options for wood drying technology are mandatory.

The need for drying
Wood preforms in the form of logs have a high degree of moisture, so they will need to go through a cycle called wood drying.... The moisture contained in the workpieces can gradually decrease in a natural way, but this will take a long time and lead to a chaotic phenomenon of compression and expansion inside the wood fibers. For this reason, the drying of the workpieces is carried out under strict control and under certain conditions.
Wet and undried woody structure tends to rot, crack and warp. To avoid such unfavorable phenomena, various methods are used to bring the wood to condition, with the given parameters of the moisture level. Drying conditions and cycle times are directly related to how excess moisture is removed.
Each method of drying wood has its own properties, having both advantages and disadvantages.

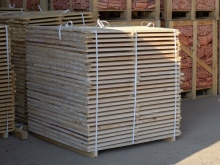

Basic methods
The modern woodworking industry approaches the solution of the problem of drying wood with different methods, these methods are used to dry any kind of wood. The description of the technological process in each drying method is different, but, as a rule, the technology consists of several stages. Today the following types of wood drying are used.


Microwave installations
Thanks to this technique, the board dries under the influence of high-frequency pulses. The principle of operation of microwave installations is similar to that which works in a microwave. The pulses allow you to evenly heat the wood, from which moisture leaves in the form of steam. Hot steam makes it possible not only to dry the saw cut with high quality, but also to level the board, which began to deform under the influence of high moisture content. The equipment of microwave drying chambers is designed so that excess moisture can be removed from the enclosed space using forced ventilation.
This is the most common drying method and is used to prepare thin cuts or small pieces of wood from high-value wood species.



Quick
When there is a need to dry the harvested raw wood in a short time, a special chamber is used in which artificial ventilation and air heating to the specified temperature parameters is carried out. The disadvantage of the fast drying method is the danger of burning wood blanks, therefore drying wood in this way is considered a rather difficult process. If the drying process is carried out at home, then the wood blanks are wrapped first with a layer of paper and then with plastic wrap. In such a winding, holes are made for steam to escape, and the wrapping paper should be replaced with a drier one every 8 hours.


Infrared rays
The method makes it possible to dry the original wet workpiece in a short time, but the cost of the finished product increases, since the process of drying with infrared rays is energy-intensive and therefore expensive. The infrared drying chamber, into which large-sized workpieces are stacked, is large in size and requires certain free areas with the ability to connect the camera to a power supply. Infrared rays, passing through the wet lumber, heat the wood and through its natural microcracks freely exit back.
The method of drying with infrared radiation allows you to dry the workpiece efficiently and evenly, while maintaining a certain amount of moisture in the wood layer, which ensures the elasticity of the sawn timber.



Vacuum
This option is referred to as an expensive type of drying sawn timber, since the organization of this process requires large free areas and expensive special equipment. Most often, the vacuum drying technique is used to dry noble tree species - cedar, oak, ash, beech. The quality of drying with the vacuum method is considered to be the best, but high energy costs significantly increase the final cost of production.
As a result of moisture evaporation, the wood material is not prone to cracking, since the whole process occurs evenly.
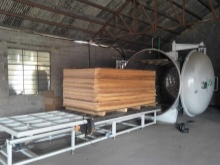
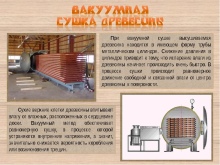

Atmospheric
The longest-lasting natural drying option for wood pieces, which does not guarantee perfect results. In this case, the wood dries out in stacks located outdoors under a canopy. Evaporation of moisture occurs when the material is blown with air, as well as when exposed to natural temperatures. The atmospheric drying option makes it possible to maintain the natural balance of moisture in the workpieces, but so that the wood does not twist, it is necessary to securely fix it in special holders.
Despite the economic benefits, this method takes a long time and some effort to properly organize the process.
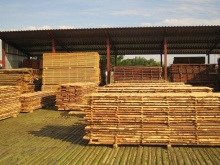

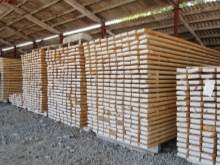
Conductive
The method of conductive drying is based on the use of hot plates, between which the original wooden blanks are placed under the press. The high temperature makes it possible to quickly dry wet wood and maintain an optimal moisture balance in it, in accordance with the established parameters. In addition, conductive drying also takes place under a press, which excludes the possibility of defects in the form of curvature of the workpieces and their subsequent cracking. The force for the press is selected in accordance with the thickness of the workpiece, the level of moisture and the type of wood.


Chamber
Drying sawn timber in a special large-sized drying chamber is considered the most affordable and common option, which provides fast processing of the original blanks. In the chamber, you can adjust the temperature level, the speed of the ventilation air flows, and also set the humidity level... Most often, timber or floorboards are dried in such drying chambers. The duration of wood processing depends on its initial moisture content and is on average 7-10 days, while the moisture level of the material decreases to 18-20%.
The disadvantage of the chamber drying method is considered to be uneven drying and the possibility of defects on the wood.



In a liquid medium
The technique is based on the use of special formulations of liquids that do not enter into a chemical reaction with water. Ceresin, various fats, paraffins and other waterproof components can be used as such components, which, according to the process technology, must be heated to more than 100 ° C. A wooden blank is placed in the heated composition, while moisture evaporates from the wood, as it is heated. The technique is rather laborious and is not widely used.
Wood drying technology options are selected depending on its initial moisture content, the size of the blanks, as well as their quantity and requirements for the quality of the material after drying.



Subsequent storage
After the end of the drying process, only completely cooled wooden blanks are removed from the drying chamber. It is impossible to accelerate this process artificially, it must go through a natural way. Next, you need to take the necessary measures to preserve the lumber, which will provide it with a certain level of moisture. Good results can be achieved if a number of requirements are observed when storing wood.
For example, in the case when it is necessary to save a timber or a standard board, then small gaps should be made between the rows of these lumber, which will facilitate free air circulation and prevent the appearance of fungus or mold spores on the wood. For long-term storage of dried lumber, it is necessary to remove the bark from the workpieces. This is done for the reason that pests can be in the bark that feed on wood and spoil its appearance.
In addition, during storage, lumber must be protected from the effects of precipitation and sudden changes in temperature conditions.



What vices can form?
In the process of carrying out work on drying lumber, timber defects may appear in the workpieces, which are usually subdivided into hidden and obvious, that is, visible to the naked eye. If the natural tension of the wood fibers exceeds the permissible limits, then visible defects are formed, which are customary to include any cracks, fungal or mold damage, knots falling out, a discoloration of the wood towards darkening, as well as warping of blanks.
The appearance of hidden defects occurs after the formation of stresses in the wood fibers, which is facilitated by the uneven distribution of moisture relative to the section of the workpiece... In addition, uneven drying of the material is also considered a hidden defect, most often this is observed when stacking blanks during drying. Cracks, wrinkling, and warpage on wood are usually caused by uneven drying. Such defects can be seen on the end cuts of the workpieces, in addition, they can also appear in the form of internal or surface cracks located on the plane of the board.



The appearance of cracking in the end parts of the workpieces is the most common type of defect, which manifests itself earlier than other types of drying defects.... This is explained by the fact that evaporation of moisture on the end parts of the board or timber occurs due to the high moisture conductivity of wood fibers located in the shared direction. Loss of moisture causes shrinkage and tension on the fibers. The higher the degree of such stress, the greater the likelihood of cracking, which most often appears in the radial direction. A properly selected drying mode helps to avoid such a defect, which will not cause exceeding the tensile strength of the wood fibers.
Cracking of wood material occurs in stages. At the beginning of this process, shallow and small cracks appear, the direction of which is oriented 4-5 mm deep into the thickness of the material. If at this stage the drying process is continued with the same parameters, then minor cracking will begin to expand, they can go even deeper into the structure of the wood and penetrate the entire section of the workpiece.
It is possible to exclude the appearance of cracks on the lumber only if the rate of the intensity of moisture evaporation from the end sides of the workpiece is reduced.

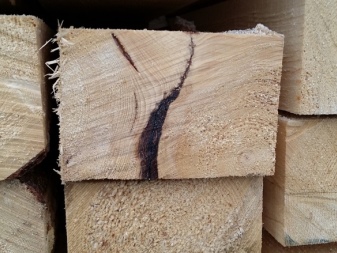
As for such a defect as warpage, then on lumber it can be helical, as well as longitudinal and transverse... All types of warpage can be present even on one workpiece, but only one of them will be pronounced. Most often, lumber with a wide surface area of 20 cm or more is susceptible to the transverse warping. This defect is especially often seen when sawing a mixed or tangential type.
When sawing radially, workpieces are rarely warped. The quality of the wood also affects the twisting of lumber or its longitudinal warping. For example, such a defect most often occurs if the original workpiece has a roll or oblique layer of wood fibers, but it is advisable to discard such workpieces even before starting the drying process. Warping is a consequence of a violation of the technology of the wood drying process being performed. During storage, an insufficient number of spacers between the boards, as well as different heights of such spacers, can lead to the formation of this defect.

If uncooled materials are unloaded from the drying chamber immediately after the end of the drying cycle, there is a risk that the wooden blanks will be subjected to warping after cooling. To avoid the appearance of such a defect, it will be necessary not only to observe the technology of the material drying process, but also the rules for its storage.I am. For this purpose, in a pile of sawn timber, 2-3 upper rows of blanks are fixed in special pneumatic clamps, and sometimes a load pressing on them is evenly placed on top of the dried boards.

The comment was sent successfully.