All about delta wood
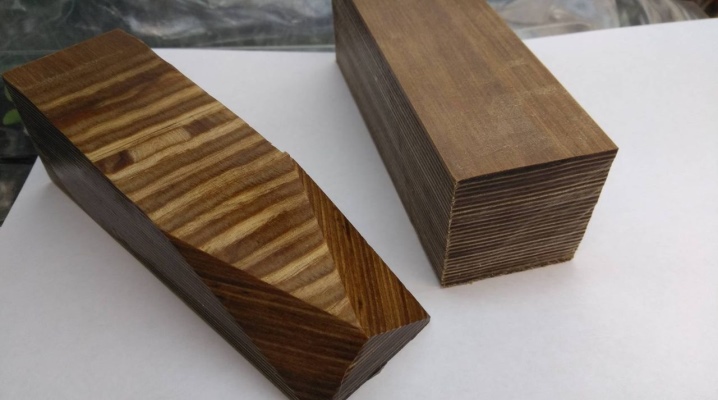
It may seem to many that it is not very important to know everything about delta wood and what it is. However, this opinion is fundamentally wrong. The peculiarities of aviation lignofol make it very valuable, and it is not only a purely aviation material: it has other uses as well.
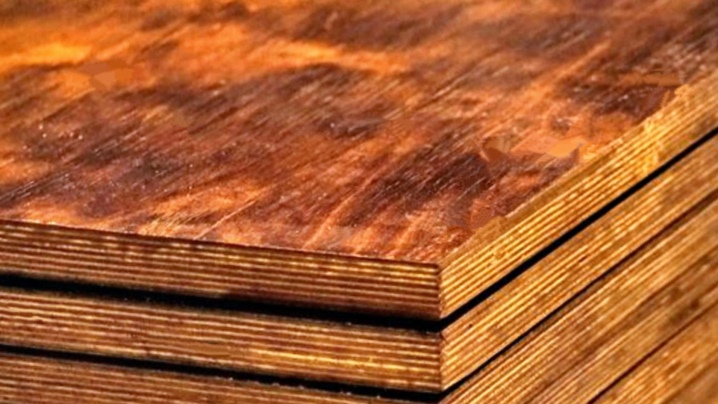
What it is?
The history of a material such as delta wood goes back to the first half of the 20th century. At that time, the rapid development of aircraft absorbed a large number of aluminum alloys, which were in short supply, especially in our country. Therefore, the use of all-wood aircraft structures turned out to be a necessary measure. And delta wood was clearly better suited for this purpose than the most advanced types of conventional wood. It was used especially a lot during the war years, when the required number of aircraft increased dramatically.
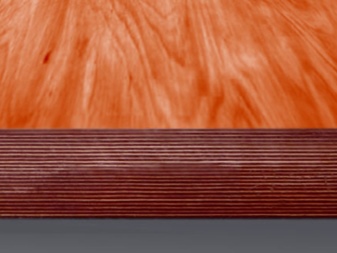
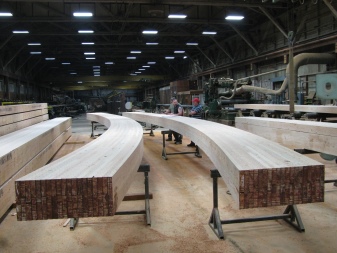
Delta wood also has a number of synonyms:
- lignofol;
- “Refined wood” (in the terminology of the 1930-1940s);
- wood-laminated plastic (more precisely, one of the types in this category of materials);
- balinitis;
- ДСП-10 (designation in a number of modern standards and technological norms).
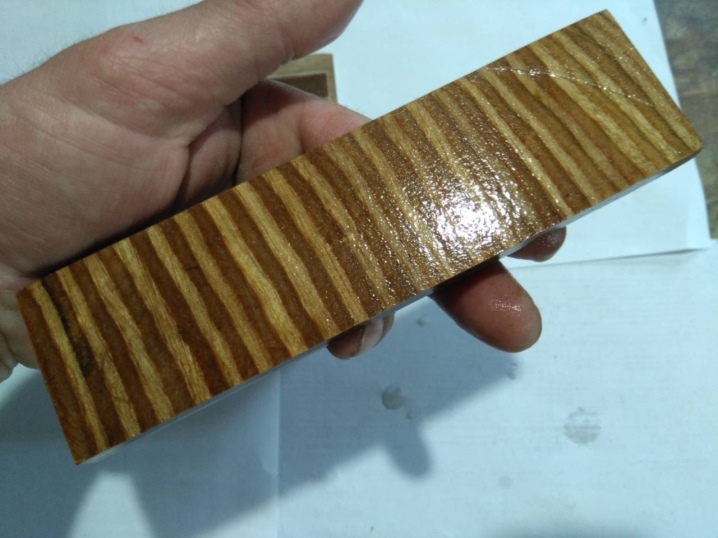
Production technology
Delta wood production was regulated by GOST as early as 1941. It is customary to distinguish two grade categories: A and B, in accordance with the physical and mechanical parameters. From the very beginning, delta wood was obtained on the basis of a veneer with a thickness of 0.05 cm. It was saturated with bakelite varnish, and then heated to 145-150 degrees and sent under a press. The pressure per mm2 ranged from 1 to 1.1 kg.
As a result, the ultimate tensile strength reached 27 kg per 1 mm2. This is worse than the alloy "D-16", obtained on the basis of aluminum, but clearly better than that of pine.
Delta wood is now produced from birch veneer, also by hot pressing. The veneer must be impregnated with resin.
Alcohol resins "SBS-1" or "SKS-1" are required, hydroalcoholic composite resins can also be used: they are designated "SBS-2" or "SKS-2".
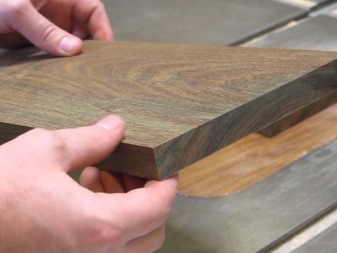
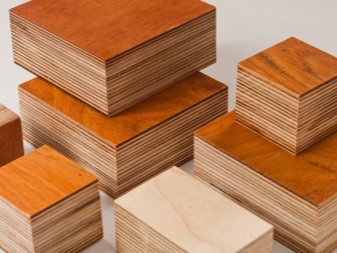
Veneer pressing takes place under a pressure of 90-100 kg per 1 cm2. The processing temperature is approximately 150 degrees. The normal thickness of veneer varies from 0.05 to 0.07 cm. The requirements of GOST 1941 for aviation veneer must be complied with impeccably.
Having laid 10 sheets according to the "along the grain" pattern, you need to put 1 copy in the opposite way.
Delta wood contains 80 to 88% veneer. The share of resinous substances accounts for 12-20% of the mass of the finished product. The specific gravity will be from 1.25 to 1.4 grams per 1 cm2. Standard operating humidity is 5-7%. A good material should be saturated with water by a maximum of 3% per day.
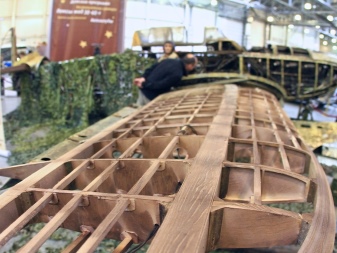
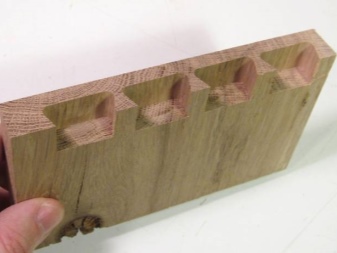
It is also characterized by:
- absolute resistance to the appearance of fungal colonies;
- convenience of machining in various ways;
- ease of gluing with glue based on resin or urea.
Applications
In the past, delta wood was used in the production of LaGG-3. On its basis, individual sections of the fuselages and wings were made in the aircraft designed by Ilyushin and Yakovlev. For reasons of economy of metal, this material was also used to obtain individual machine parts.
There is information that air rudders are made of delta-wood, which are placed on the first stage of P7 rockets. But this information is not confirmed by anything.
However, we can definitely say that some furniture units are made on the basis of delta wood. These are structures subject to heavy loads. Another similar material is suitable for obtaining support insulators.They are placed on the trolleybus and sometimes on the tram network. Delta-wood of categories A, B and Aj can be used for the manufacture of power parts of aircraft, used as a structural material for the production of dies for processing non-ferrous metal sheets.
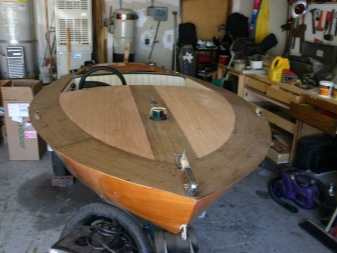
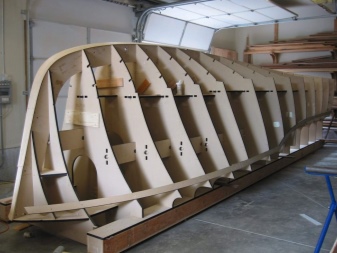
A proof test is carried out on 10% of the boards from any press-fit batch. You need to find out:
- the degree of resistance to longitudinal tension and compression;
- the portability of folding in a plane parallel to the structure of the workpiece;
- resistance to dynamic bending;
- compliance with regulatory requirements for humidity and bulk density.
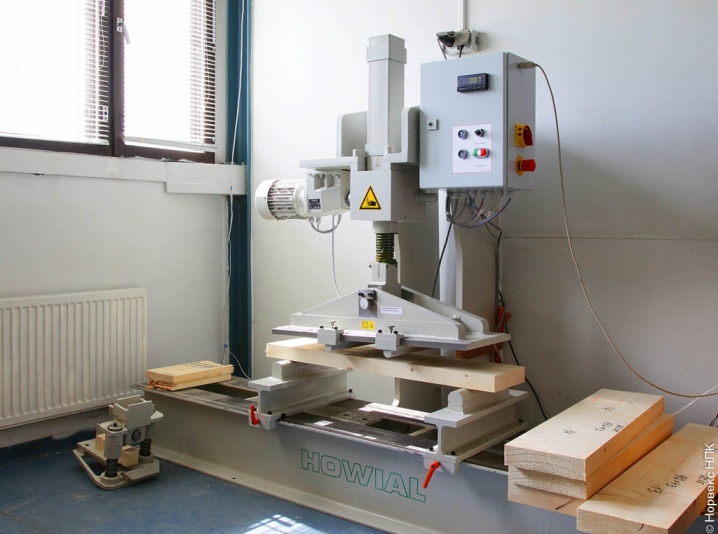
The moisture content of the delta wood is determined after a compression test. This indicator is determined on samples of 150x150x150 mm. They are crushed and placed in containers with an open lid. Exposure in a drying oven at 100-105 degrees is 12 hours, and control measurements should be carried out on a balance with an error of no more than 0.01 grams. The accuracy calculation should be carried out with an error of 0.1%.
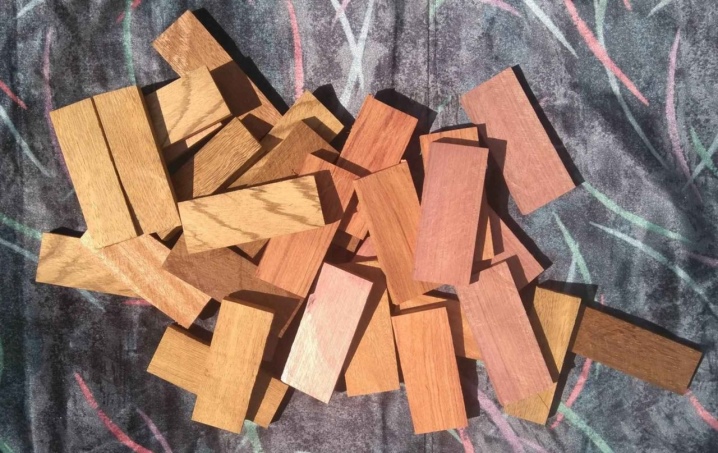
Everything is perfectly described, short, detailed, professional!
The comment was sent successfully.