Repair of hydraulic jacks
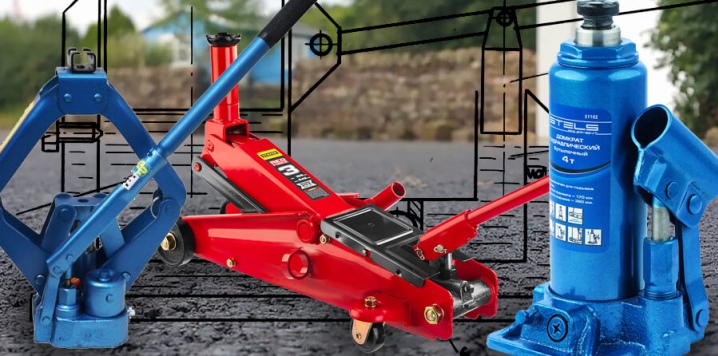
Devices designed to lift various loads to a relatively low height have long been widely used in many areas. For example, even in ancient times they were used to break open gates during the siege of fortresses. However, even the most reliable modern models fail sooner or later. Taking into account all the nuances, you should consider how the features have a repair hydraulic jacks and is it possible to perform all the necessary work yourself.
Causes of major malfunctions
Even taking into account the fact that hydraulic jacks are considered to be the most durable, they are not insured against breakdowns. This applies to devices like bottleand rolling type.
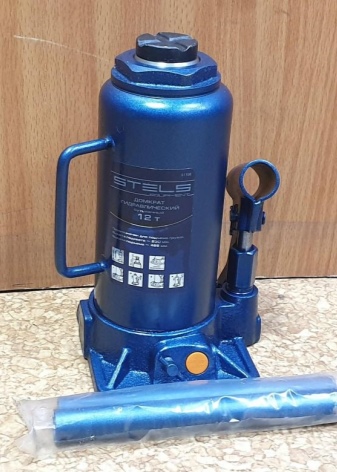

By the way, now quite often you can find models of still Soviet production.

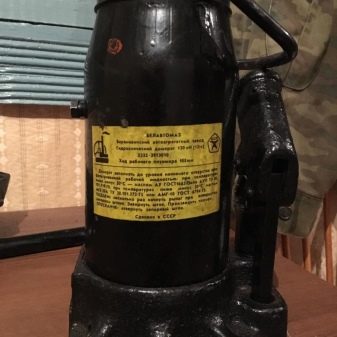
The reasons that the jack does not work may be wear of old parts, as well as improper operation... As practice shows, most often the failure of oil equipment occurs due to the lifting of loads, the weight of which exceeds the maximum permissible. Malfunctions of hydraulic jacks of automobile and other types are associated with different problems. When analyzing them, it is necessary to take into account the following important points:
- Often you have to deal with the failure of the hydraulic cylinder, which is the main element of the entire structure, as well as damage to the plunger mirror. As a result, the working part of the device does not maintain the required pressure, and oil, in turn, enters the space above the piston.
- Typically, the mirror is damaged due to improper use of the equipment. It is about transporting a bottle-type device in a horizontal position, if this is not provided by the manufacturer.
- Due to serious damage to the mirrors, leaks of working fluid and air penetration occur, leading to active corrosion. It causes accelerated wear of sealing elements made of rubber, which is susceptible to mechanical stress.
- Damage to the seals leads to the ingress of foreign particles into the oil, clogging the valves and channels.
- When the jack falls from a great height, significant damage to its elements (both internal and superficial) is possible.
- Frequent excessive loads can lead to failure of the mechanism and its serious breakdowns. One of the most common problems is stem curvature, which causes oil to flow through the chamber. It is important to remember that each specific model is designed for a certain load, exceeding which inevitably leads to damage to the lifting equipment. All relevant parameters are indicated in the instructions for use of the jacks.
- Among other things, it is possible to find yourself in a situation where the hydraulic mechanism leaks when it is used for other purposes. In this case, it is again about ignoring the manufacturer's recommendations regarding the operation of devices.
Naturally, this is an incomplete list of reasons why the jack may require repair.

Particular attention is strongly recommended to be paid to periodic maintenance. It means that at a set frequency, it is required to sort out the mechanism to detect faulty spare parts and replace the working fluid.

Disassembly
Taking into account the simplicity of the design, in the overwhelming majority of cases, with the knowledge, skills and tools it is quite possible to repair a faulty hydraulic jack with your own hands. Difficulties arise most often when it is necessary to bulkhead and renovation non-separable structures. However, now on the network you can easily find a sufficient amount of materials.

They are devoted to the described work, as well as the materials used in their implementation, including repair kits. To disassemble almost any hydraulic jack, you will need:
- hammer and chisel;

- screwdriwer set;
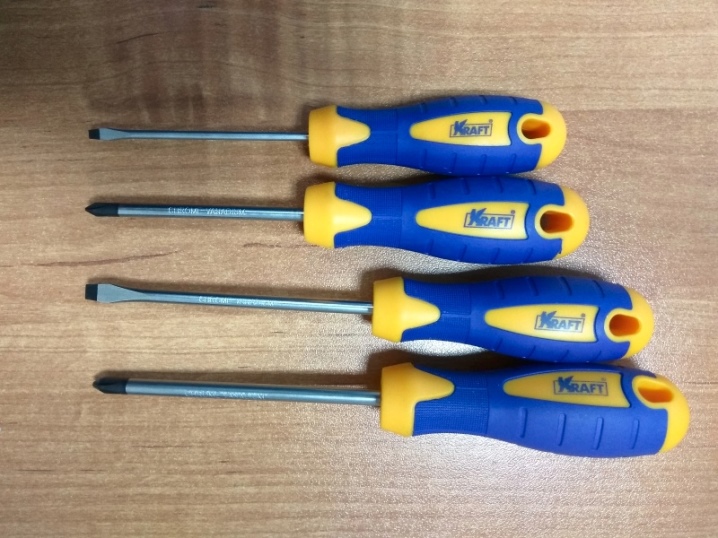
- pliers;

- hacksaw for metal;
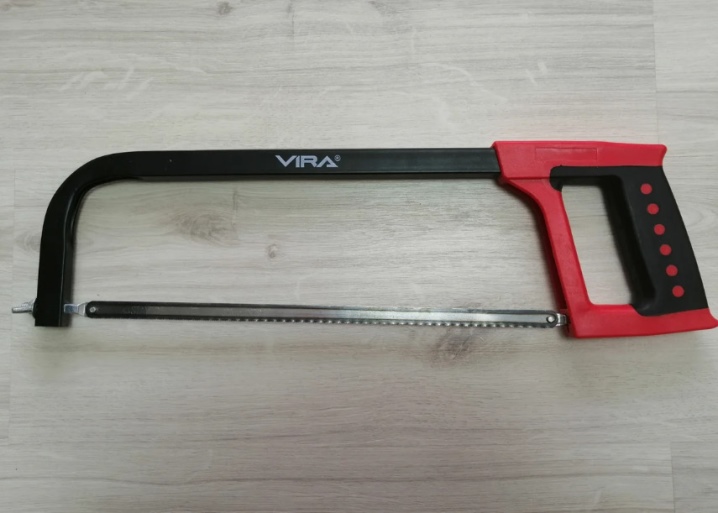
- set of wrenches;

- universal adjustable wrench.

This list in each case will depend on the model of the jack and its design features. This means that in some situations it is very easy to get to the "insides" of the lifting mechanism. However, disassembly of the device will often require a certain amount of time and effort. The process of disassembling the hydraulic jack can be considered on the example of the classic bottle-type model.
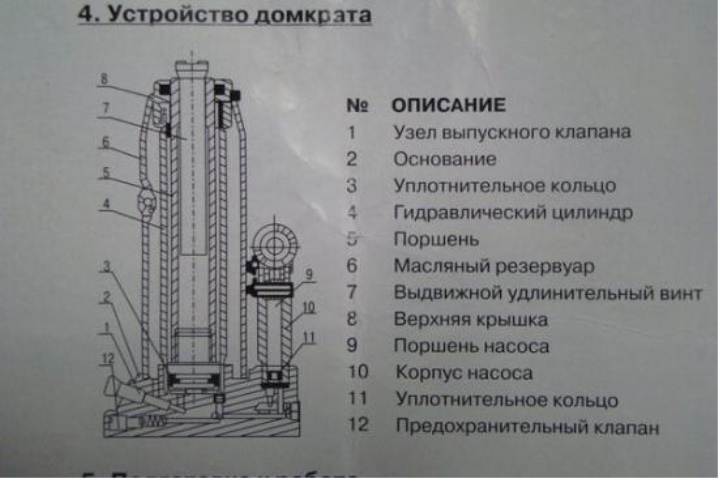
In a simplified form, the sequence of actions will look like this:
- First of all, you will need to completely drain the working fluid (oil). To do this, use a special drain hole or a permeate valve. You will need to unscrew the upper nut (hex), as well as the lower valve.
- The next step is to remove the case. At this stage, an inspection is carried out in order to detect malfunctions and damage. We are talking about the tightness of the housing and the condition of the lower O-ring. It is important to remember that these structural elements are not subject to stress and act as a reservoir.
- Then you need to unscrew the working cylinder itself and dismantle the piston.
After all the listed manipulations are completed, unscrew plunger.

It is worth noting that at all stages of disassembling the jack, it is necessary to immediately diagnose the state of its structural elements.

How to repair
Repair of the hydraulic jack is required in situations where it will not raise or hold the load, or if the stem will not drop. In principle, such a process is simple, however, there are a number of important nuances to consider. So, the presence of traces of corrosion can significantly complicate the task. That is why it is recommended before dismantling the jack. take care of the availability of a special liquid for removing rust.
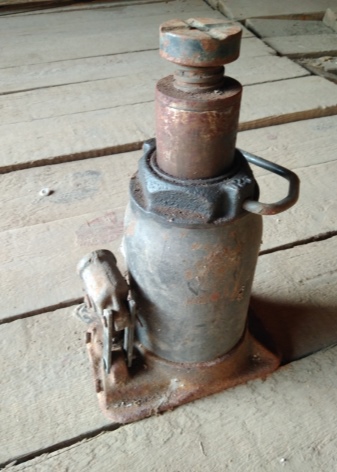
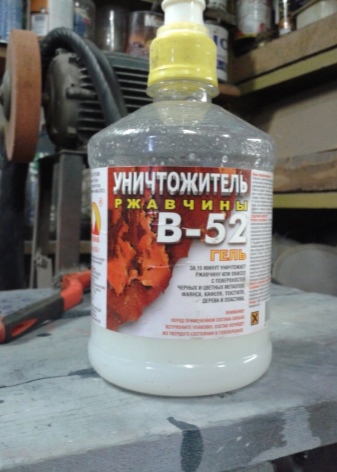
The whole process of repairing the described lifting equipment can be divided into the following stages:
- Determination of the nature and causes of the problem. In the absence of pressure in the system, it is most likely that the sealing elements are worn or damaged. If there are difficulties when lifting loads, then there is a high probability of curvature of the rod.
- Taking into account the scale of the malfunction, partial or complete disassembly of the device. It is important to perform all actions with the utmost care and accuracy so as not to damage the fasteners. Even minor defects can cause fluid leakage and, consequently, pressure drop in the system.
- Inspection of all units in order to diagnose them.
- Replacement or restoration of damaged and worn out structural elements.
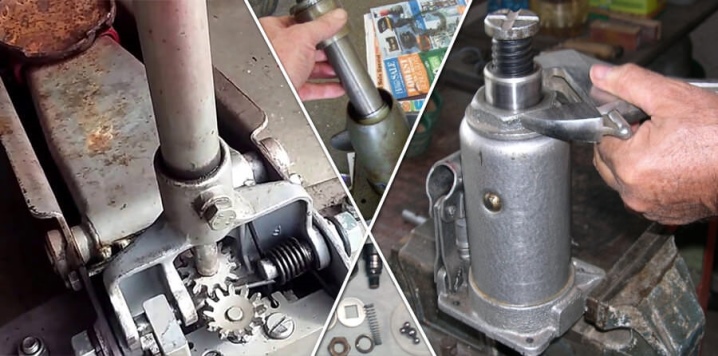
In practice, most often, repair work and manipulations provided for by the implementation of maintenance are reduced to the following actions:
- After dismantling the jack, the inner surface of the working chamber is thoroughly cleaned.
- For a complete inspection of the sealing cuffs, they must be removed. As a rule, these structural elements are fixed using special devices. In the process of disassembling and replacing rubber rings, the sequence of their location should be taken into account.
- An integral part of the described operations is the replacement of the working fluid.

In addition to these situations, you have to deal with serious damage. mirror surfaces and deformation of the rods. As a rule, it will be extremely difficult to cope with such problems on your own. It should be noted that bottle-type hydraulic jacks differ from their rolling "counterparts" in maximum simplicity of design. Due to the lack of adjustments, after the completion of the repair, you can immediately start testing and operating the serviced or restored mechanism. Most manufacturers complete their products with rather detailed instructions, which describe the algorithms for disassembling and assembling lifts.
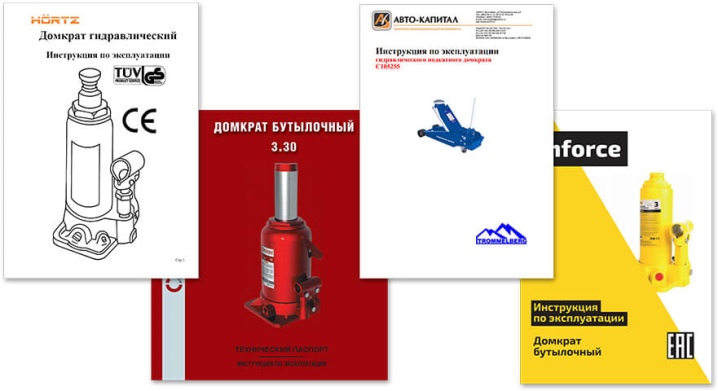
Regardless of which category the equipment belongs to, after maintenance and repair, it is required check its performance in test mode... It is important to take into account that the full operation of the mechanism with incorrectly installed seals and the admission of other errors will lead to its failure.
It is also strongly recommended to use stops for safety when lifting a car and other loads.
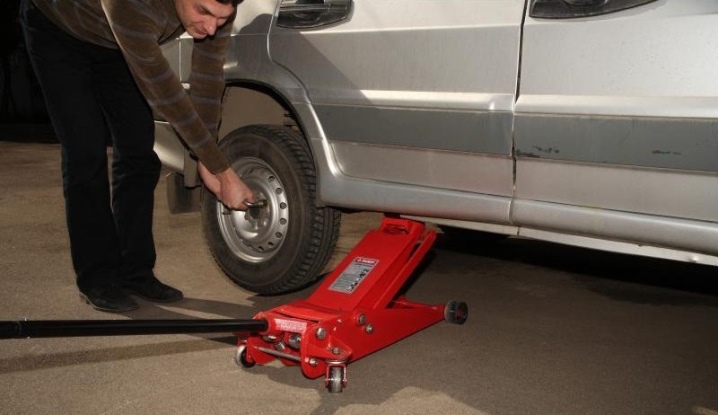
Broken valves
There are situations when, in the presence of working fluid in full, the jack does not lift the load or does not hold it. To restore its operability, it is necessary to pay attention to the valves, namely, their adherence to the seats.

It is important to consider the following points:
- In the absence of good contact, the springs are checked, which, most likely, have lost their rigidity.
- The cause of the malfunction may be clogging of the valves, which should be thoroughly cleaned and flushed with gasoline or kerosene. Then you will need to dry these elements of the mechanism with compressed air.

If the springs are very weak and there is no point in increasing their elasticity due to washers, then their will have to be replaced with new ones... The situation is similar with deformed valves.
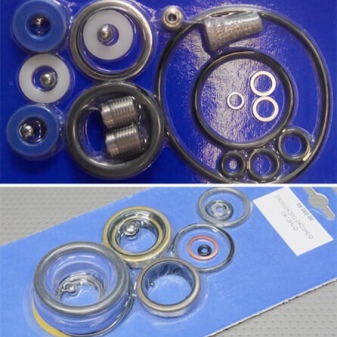

Fluid leak
These troubles are usually caused by mechanical damage to hydraulic jack structural elements... Before starting to repair the equipment, it will need to be disassembled. In parallel, all metal parts are inspected for the presence of foci of corrosion. Found damaged elements are usually subject to replacement.

Experienced users and specialists recommend draining all oil and thoroughly flushing the mechanism during the work. It is also worth replacing all cuffs with new ones.

Removing air or dirt
Continuous use of lifts inevitably leads to accumulation of air. In parallel with it, small foreign particles can also get into the working cavity. As a result, it becomes dirty, which affects the performance of the device. It should be noted that the hydraulic jack functions on the principle of communicating vessels. When the working fluid leaves, the pressure is maintained. But the air is not removed under pressure, but creates a kind of pillow that interferes with the lifting of the load. Air from the system is removed when changing the oil, and dirt is removed using special solutions.

Recommendations for use
Compliance with the rules for using any tool allows you to maximize its service life. Naturally, hydraulic jacks are no exception. So, in particular, it is highly recommended after completion of work, release the equipment from the load... In addition, the guarantee of the lift's durability will be its correct storage taking into account the negative effects of moisture and low temperatures.
Once again, it is worth recalling that periodic overloads become one of the most common causes of breakdowns.


You can learn about the features of the hydraulic jack in the following video.
In parallel follows pay attention to the condition of the working fluid... By the way, the so-called mining is often poured into the cylinders of jacks.This in itself has an extremely negative effect on the functional performance of the jacks.

With the active use of devices it is recommended to change the oil and bleed the system every 2-3 months. If the hydraulic jack is rarely used, then such procedures can be repeated every six months.
In the process of servicing, it is worth focusing on the following important points:
- volume and quality of oil;
- the presence of air bubbles;
- cleanliness and tightness of valves.
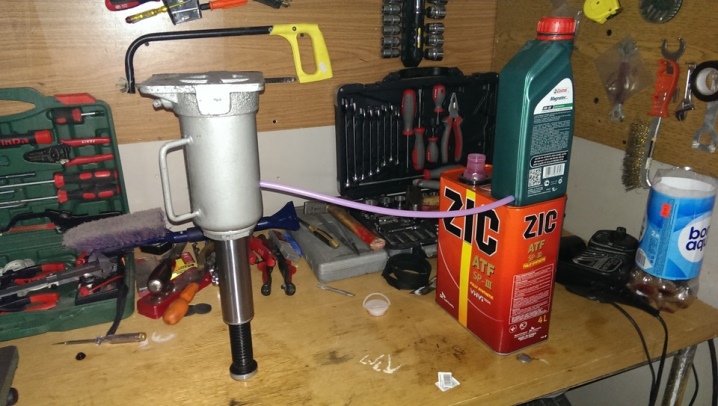
Most often, all problems arise precisely due to lack of working fluid. They are solved by elementary topping up of oil. However, you need to know what exactly needs to be added to the hydraulic jack reservoir. In principle, the equipment is capable of operating, albeit for a short time, on ordinary water. But a good quality fluid will provide adequate performance and durability.

How to properly change the oil in the hydraulic jack is shown in the following video.
When choosing a specific option for a filling material, it is necessary to take into account important features. It is recommended to avoid using brake fluid, because it is able to absorb corrosive moisture. Also, do not make a choice in favor of materials of mineral, oil and glycol origin. The best option would be synthetic oil, which, among other things, is resistant to low temperatures.

Often, lifting mechanisms fail at the most inopportune moments, which can pose a serious danger. Based on this, it is strongly recommended that certain rules for the operation of lifting devices of the category in question.
At the same time, attention is focused on the following key points:
- When installing the jack, make sure that it is firmly positioned on a hard and as flat surface as possible. It is also important that the stop and the load to be lifted are parallel to each other.
- When lifting the car, the support should be as strong as possible structural elements.
- Lifting should be carried out by smooth movements of the lever of the working cylinder. It is important to ensure that the load being lifted remains stationary.
- The use of stands is mandatory in most cases.
- After completion of work, it is necessary to clean the stem from dirt, if any.
- The hydraulic jack should be stored and transported only in the position specified in the instructions developed by the manufacturer and included in the equipment delivery set. Bottle-type and roll-off devices must be in vertical and horizontal position, respectively.
- Store jacks with lowered rods, retractable screws and pump pistons.
- It is recommended to lubricate the listed elements periodically.
- As the working fluid dries up and evaporates, it is required to top up and pump the system.






Compliance with the listed rules will maximize the safety of the process of lifting and fixing heavy loads using hydraulic jacks... It will also help to extend the life of the equipment many times over. It is important to take into account the features of each type of device and specific models.
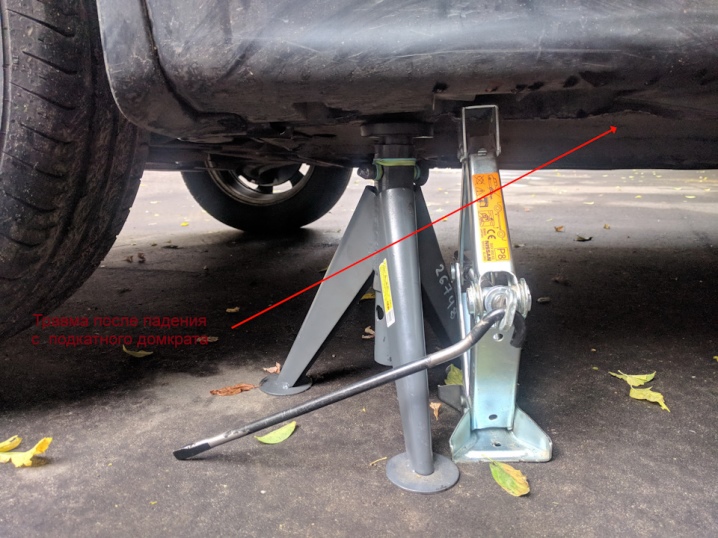
An overview of the disassembly and repair of a hydraulic jack is presented in the following video.
The comment was sent successfully.