How to make a rack jack with your own hands?

The jack is an indispensable tool for both installers and ordinary motorists. Rack jacks are considered the most convenient to use. Such a tool should be in everyone's trunk, especially when you consider that it can be easily made with your own hands.

Peculiarities
Without exception, all rack jacks work according to the same principle. When the ratchet mechanism interacts with the rail, the jack body begins to rise, and with it the pushed object rises.
Wherein rack jacks are of two types: mechanical and electronic. It is clear that electronic models are much more convenient, since the direct participation of the owner is minimized. However, at the same time, they are also quite expensive, and assembling such a device at home is a very difficult task that requires you to know not only mechanics, but also electronics.


Mechanical rack jacks, in turn, are divided into two more subspecies: gear and lever... The housing in the lever jack is lifted by pressing the lever, and in the gear jack - thanks to the handle with gears.
Even the simplest rack and pinion jack models can lift up to 8 tons, which is enough for a car. And there are also more advanced models (for construction work) that can lift weights from 10 to 20 tons.
The main disadvantage of rack and pinion jacks is considered their dimensions... All the same simple models weigh about 40 kilograms, and the weight of construction models can reach up to a centner.


Those who decide to make a rack jack with their own hands should take into account several important nuances.
- One of the main parts of a rack and pinion jack is its support platform. It is she who affects the stability of the entire structure, which is very important, given that we are talking about lifting loads weighing several tons.
- Another necessary element is bracket. When making and using it, it is imperative to take into account the lifting height.
- The lower the grab goes, the better. Low-lift systems can lift loads even from the ground.
In fact, making a jack with your own hands is not so difficult. With at least minimal experience, you can probably do it without outside help.
At the same time, making a jack with your own hands always comes out cheaper than buying it.



Preparation
Before you start building your own jack, you need to prepare a little. It's better to start with the theoretical part and decide what kind of jack you need: what load capacity is needed (to raise the car, or a simpler option is suitable), what type of mechanism do you prefer and, in general, think over all the nuances.
After that, you will need a suitable circuit. And you also need to prepare materials and tools. For some models, additional details may be needed, but the unchanged ingredients for creating a rack and pinion jack are:
- channel (a small piece of size 200);
- square shaped tube with a minimum wall thickness of 2 millimeters;
- 8mm steel strip;
- various nuts, bolts, springs and other small parts.
The list of required tools is also small:
- drill;
- wrench;
- Bulgarian;
- welding machine.
After all preparations are completed, you can start working.
All dimensions indicated for details, by the way, are only approximate... You can easily take both more and less reliable options.
But remember that the load capacity of your jack will depend on the thickness and size of the parts.


Manufacturing instruction
On the net you can find many different instructions for the manufacture of rack and pinion jacks: there are both simple explanations, where everything is shown "on the fingers", and detailed analyzes with drawings and dimensions.
The same wide choice is offered in terms of execution. Here you can find mechanical jacks, and electronic, and three-stage and, in general, whatever. Of course, we will not be able to disassemble them all.
But still, let's try to create the simplest homemade jack with a lever mechanism. This process looks like this:
- for a start, a piece of a channel with a width of 60 millimeters and a profile pipe are taken;
- on the channel on the sides, 2 holes are marked, and then 2 holes are made, the width of which should be a couple of millimeters larger than the width of the profile pipe;
- then we take a pipe (for example, a water pipe) and cut a piece from it slightly longer than the width of the channel;
- weld the pipe to the channel approximately in the middle (this is not so important);


- now we take a steel strip and mark it so that we get 3 segments - 2 along the edges of about 200 millimeters, and between them one with a width of 65-70 millimeters;
- slightly cut the marked places with a grinder, and then bend it 90 degrees along the cut line and weld the fold line - the result will be a beech "P";
- at the ends of the resulting part, we make 2 holes with a diameter slightly larger than a piece of pipe;
- we take an axis with a diameter slightly less than the hole in the pipe, and a length of 65-70 millimeters, connect all 3 parts and weld;
- make 2 holes with a diameter of 12 millimeters on the sides of the channel, take a bar with the corresponding diameter, insert and weld;


- we make 2 clamps - small rectangles with holes for a profile pipe;
- take 4 nuts and weld 2 of them to the retainer, and 2 from the inside to the channel, insert the retainer into the structure, and connect the nuts with springs;
- make an oval hole in the second retainer;
- we make a stop for the retainer and weld it to the channel from the bottom, and from above we weld the bolt on the same side where the nuts were welded;
- we put a spring on the bolt, connect all the parts, and fix the second retainer with a nut;
- it remains only to weld the lever and the support platform - the jack is ready.


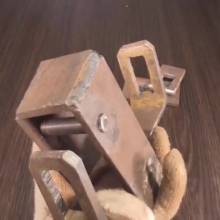
The instruction may seem a little difficult however, in practice, everything comes out much easier. Before starting work, it is best to re-read it a couple of times, think over the entire procedure from start to finish in your head and clarify incomprehensible points.
The resulting device will be able to satisfy the needs of an ordinary consumer and will lift any passenger car up.
If you suddenly want to increase the lifting capacity of the jack, you just need to choose more durable parts.
For information on how to make a rack jack with your own hands, see the next video.
The comment was sent successfully.