Electric vibratory rammers: description and tips for choosing

Before the erection of various buildings, laying of road or garden surfaces, landscaping, soil compaction is required. If this type of work is neglected, the risks of destruction of the flooring or structure are great. Special rammers are used to compact the soil. In everyday life, electric vibro-legs are most often used. They are distinguished by their compact size and low weight, which makes them easy to use.

Characteristic
Regardless of the model, all electric rammers have a similar design. They include:
- electric motor for 220 or 380 V;
- protective frame for the motor;
- reducer;
- prefabricated vibration device;
- tamping sole.

Depending on the modification, vibratory rammers with an electric motor differ in power, shock amplitude, advance speed, jump height and vibration force... In addition, they come in a variety of outsole dimensions and sizes. The performance of the equipment is more influenced by the impact force and vibration frequency.
The more these indicators are, the larger the soil area can be processed within a certain time period.

Electric rammers, unlike gasoline and diesel ones, they have less performance. However, they are more economical and do not require complex maintenance. Also, electrically driven equipment is quieter. All such modifications are equipped with a residual current device that protects the rammer from premature failure in the event of sudden voltage surges.

The main disadvantages of electric vibratory rammers - inadmissibility of operation in rainy weather and poor mobility. The equipment can only work near a source of electrical energy, and the range of its action is limited by the cable.

Principle of operation
Electric vibratory rammer - equipment that converts electrical energy into mechanical energy. When the unit is in operation, the engine transmits rotational movements to the crank unit. Its piston reciprocates, which is transmitted to the rammer leg. Due to the high frequency of impacts on bulk building materials and soil, there is a shock-force effect, as a result of which they are compacted.

Selection rules
When choosing a vibratory rammer, you should pay attention to several important parameters. It is necessary to do the following.
- Read the instructions and technical characteristics of the installation. Technical parameters must correspond to the planned types of work.
- Give preference to fully equipped solutions: they must be supplied with a tamping sole and various attachments.
- Decide on the scale and conditions of work... For work in narrow areas or confined spaces, choose rammers with the smallest working shoe size.
- Decide on the number of strokes. The higher the value, the faster the technique will cope with the compaction of the material.
- Choose the optimal dimensions for the device.

Experts advise buying vibration rammers with anti-vibration system for the handle (not available on all models). It helps to reduce vibration loads on the operator's hands during operation.

Application
Electric vibratory rammers widely used in the construction industry. During operation, they do not emit harmful emissions, which makes them suitable for indoor use. Vibratory plates used for compacting sand, soil or gravel with a layer of up to 30 cm. Vibroleg, which has a smaller work sole, is used for compaction of deeper layers.
With its help, you can compact materials laid in a layer of 50-70 cm.
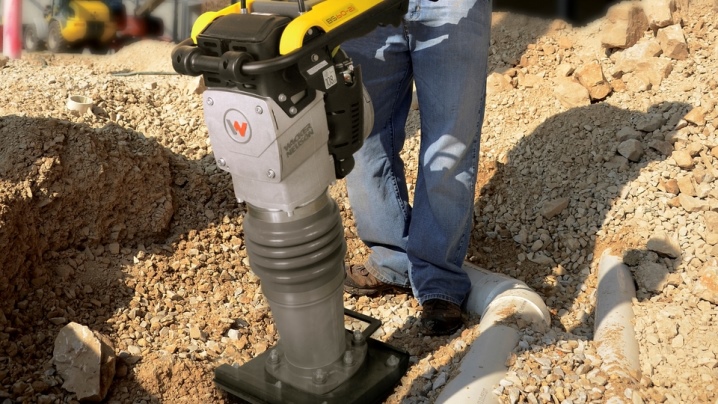
Equipment is often used for the arrangement of the local area, if necessary, laying paths on the personal plot, ramming the foot of the support structures. The technique is applied when laying tiles, and when erecting a pile-strip foundation foundation in the construction of private structures.

In the following video, you can watch an overview and test of the Weber MT SRV vibratory rammer.
The comment was sent successfully.