Grinding machines: types and their characteristics

Buying a grinder is a responsible business, so you need to prepare for it in advance. Before buying, you need to figure out what kind of machines there are in general, how these or those models relate to the processed material, which manufacturers are most trusted among professionals or amateur craftsmen. But first you need to understand what a grinding machine is in principle.

Peculiarities
The sander is designed for processing various surfaces made of wood, metal, plastic and even glass. Depending on what type of machine your machine belongs to, you can make rough, finishing or finishing.
When it comes to rough processing, they mean getting rid of the surface of large holes and twigs. As a rule, this type of work is primarily carried out with wooden products, since by nature a tree cannot be perfectly smooth.
During rough processing, a large layer of wood is mercilessly removed, while the surface becomes only slightly smoother. Depressions, scratches, roughness remain on it, which require further procedures. For such processing, special machines with coarse abrasive discs or belts are used. The speed of such processing is usually high, so the grinder must be powerful.
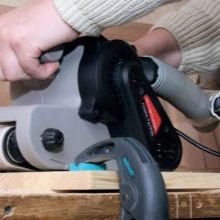


Medium processing allows you to remove irregularities visible to the naked eye, bringing the appearance of materials closer to ideal. Again, this type of work is more often done with wood, but sometimes metal work also requires similar measures.
In this case, they try to ensure that the surface is flat, and not perfectly smooth. Particular attention is paid to indentations and protrusions, which can disturb the flatness of the plane.
In this case, grinders are used with a large number of revolutions, but with an average power. Medium depth cuts take longer than coarse ones, so it is important that the machine is able to run for a sufficiently long period.
It is worth noting that units with such characteristics are practically not represented on the market of household construction equipment, so either you have to buy a grinder for professional use, or prepare for the fact that the average processing will take several days, or even weeks.

Finishing or finishing is the most delicate moment in the whole work. It takes the most time and effort and requires extraordinary skill. Indeed, at this stage it is possible to nullify all the results of past works. Finishing is carried out immediately before painting, varnishing or other decorative work, before which the surface must be perfectly smooth. In the case of wood, it can also be pickling. At this stage, all roughness and irregularities are removed.
For the last work on processing, special polishing attachments are used, which bring the surface "to mind". Among other things, they are used for glass, renovation of paintwork on a car body.
Metal polishing is needed when it is necessary for the iron part to shine.The grinder here works at the highest speed, and such a jewelry work does not tolerate the use of unnecessarily powerful machines - it is too easy to make a mistake.

Device and principle of operation
In terms of the set of accessories and their device, all grinders are similar to each other. As a rule, they consist of several elements.
- Frame... Most of the time it is made of plastic, but don't let that confuse you. In production, specially developed polymers are used, which are distinguished by high indicators of wear resistance and strength, but at the same time they are light. These qualities make them ideal for making all body parts, from power on / off buttons to handles.
- Lever... Each grinder needs to be held in a certain position somehow. For this, the handle serves. It is distinguished by an ergonomic shape, and it must also have a thread, so that even a heavy machine is comfortable to hold. The important point is that the handle "dampens" vibrations from the grinder, so that with its help it will be possible to direct the machine as needed, while not giving all the strength to hold it.
- Electric motor... All but the oldest grinders use an electric motor. It can be powered from various sources: directly from the electrical network or from a battery. Electric grinders are more convenient. They have good performance due to the fact that they are powered from the mains and do not require constant recharging. Roughly speaking, they work for themselves and work until they overheat. Cordless sanders are another matter. They cannot work for too long and are mainly used when working with hard-to-reach places, when it is not possible to connect the machine to an outlet.
- Compressor motor... This is just an exceptional case when the motor does not run on electricity. The engine works by supplying compressed air, which drives the mechanisms.
- Reducer... Helps convert the energy produced by the motor into useful work. It is necessary in order to increase the torque and speed of the device, while reducing the load on the motor. It can give the ability to switch from 1 to 5 speeds.
- Spindle... This part serves to impart a rotational movement to the nozzle. One of its ends is a threaded shaft to which the attachment is attached, and the other is attached to the grinder itself. The spindle can be attached both parallel to the device body and perpendicular to it.
- Protective cover... Protects the master from sparks, bouncing particles and small debris that inevitably forms as a result of working with a grinder. If such small particles bounce off the work surface, they can cause serious injury to a person, for example, if metal shavings enter the eyes.

The principle of operation for each machine is different. It depends on what type your device belongs to. Basically, all machines grind and polish the surface due to the frictional force, however, the desired effect is achieved in different ways.
Types and their characteristics
There are a huge number of grinders, each of which is based on its own special method of grinding, has an unusual shape, allows you to work in a horizontal or vertical position, and so on.
First of all, it should be said that the greatest demand among all types is for machines for work:
- for metal;
- on plastic (can also be used for glass);
- stone (used for marble, granite and other durable materials of natural origin);
- on wood.
When choosing a suitable unit, you need to take into account their power, the speed of rotation of the disk, as well as the principle of operation on which they are based.The level of processing at which you plan to stop is also important.
Machines that quickly get rid of rough scars are unlikely to be suitable for jewelry finishing, as you simply cannot control them sufficiently.


The size of the units also plays a role. A mini-machine, with the help of which manual processing is carried out, cannot be compared with a large professional construct designed for polishing parquet. It is necessary to soberly assess the state of affairs, leaving professional equipment to professionals. An elementary argument in favor of such a decision is that in everyday conditions it will not pay off.
By the way, another classification of grinders logically follows from this thought - according to the level of use.
- Professional. Designed to perform a large volume of work almost continuously for a long time - an average of 8-12 hours without interruption. They cope with their duties faster, however, when using them, they require skill. They are made of materials of increased strength so that they can be operated for a long time without damage and negative consequences for the motor. It is possible to customize the machine in almost all parameters that are necessary in the work. They weigh a lot, are expensive.



- Household. Models of this class are produced for home use. Also, the emphasis is on the price, and therefore it is not always possible to adjust even the most primitive settings. They cannot work longer than 20-30 minutes without interruption and often more than 3 hours a day. The car must be given a break of at least 15 minutes from time to time so that it will serve the number of years indicated in the instructions and so that it does not have to resort to replacing parts, repairing the motor and so on. The price is affordable, but the performance is poor. As a rule, they are more mobile than professional units.
- Semi-professional. The car belonging to this class combines some features of the professional and household models. For example, it can be high-performance, but quickly "get tired", or it can have many settings, but be inferior in performance, and so on - there are a lot of combination options. The price for such models is above average, but if you plan to often do grinding work at home, then it is better to give preference to just such a design.



By the type of structure, many types of grinders are distinguished.
Tape
Tape models are ideal for rough finishing of wood surfaces. They perfectly and quickly remove all visible irregularities, roughness and other unpleasant things. Their difference lies in their structure: the part responsible for grinding is not round, but rectangular. It is a tape stretched between two rollers and looped. It turns out, as it were, an endless abrasive belt that constantly moves and grinds the right place.
Also tape machines are used to polish car paintwork... There are even special models designed for car maintenance.
The negative point from using such models is that if you keep the machine in one place for too long, change the degree of pressure or lead it across the grain of the tree - you can get unattractive indentationswhich are extremely difficult to get rid of in the future. To do this, you will have to carry out the entire cycle of work from the beginning, gradually reducing the abrasiveness of the nozzles.
Another point is that there is no way to process the surface in the corners. It would seem that a rectangular surface should cope with this without problems, but everything is different. The machine grinds only with the central side, and the sides are lifted. So this option is ideal if you need to quickly rough out a large surface without hard-to-reach corners.



Vibration grinders
Vibratory orbital sanders have a wider variety of attachment shapes than the previous belt model. The standard set includes flat rectangular and triangular nozzles. The principle of operation is that the nozzle moves back and forth within 5-11 mm, due to which the surface is polished.
Such a mechanism of work is good at the final stages of processing, when you need to take your time to bring the detail "to mind". Vibration grinding models are characterized by low power, which does not change much depending on whether the unit is professional in front of you or not.
Be that as it may, finishing or medium processing with the help of such models can be carried out, and work with a rectangular nozzle with large areas, but not in corners and hard-to-reach places, but triangular on the contrary... This is due to the fact that, due to vibrations, the rectangular sole constantly collides with an obstacle, due to which damage is done to the grinder and to the parts adjacent to the workpiece. The triangular is more maneuverable, but it is difficult for it to quickly process a large surface.
The pitfall of processing with a vibration machine is the possible appearance of deep scratches, which are then extremely difficult to get rid of. They are popularly called "lambs".
Scratches appear when a tiny particle gets under the sole of the car. Even with a grain of sand, it is capable of severely scratching the surface, which is processed just so that there is not a single blemish.


Eccentric
Eccentric models are also commonly known as orbital models. This is due to the fact that they combine two principles of work. They rotate and vibrate at the same time. This increases the efficiency of the grinding work.
The sole of the eccentric machine is usually round. Discs with different abrasiveness can be alternately attached to the sole with Velcro, thanks to which such grinders can be used for a wide variety of types of processing: from rough to finishing.
Orbiters are usually equipped with a special dust bag. The particles that form after grinding are collected there. In case of, if you plan to treat a large surface area, models with a vacuum cleaner were invented... So, instead of a bag, a vacuum cleaner is connected. It collects all the particles that form.
Since the capacity of the vacuum cleaner is larger and it does a better job of picking up debris itself, this makes it possible to work without interruption to clean the surface and the bag for a longer period.



Delta grinding
Such grinders got their name because of their shape - they have a triangular base. Delta grinding models are not exactly what you need when it comes to processing large blocks, but they do an excellent job in hard-to-reach places, and are also great for restoring any part.
As with vibratory grinders, delta grinders have a principle of operation based on oscillating movements of the platform, however their range of motion is much smaller - about 2 mm... This allows them to process areas along the walls.
The abrasive disc is attached with Velcro. Due to this, the replacement of emery sheets is quick, but the maintenance of such a machine is more expensive due to the increased cost of consumables.
Delta sanders have a built-in dust collection container... As well as when working with vibratory ones, when working with delta sanders there is a risk of leaving scratches on the surface, so without such a bag the work would become much more difficult and take much longer.
Among other things, some cars have a swivel mechanism for easy handling. The sole on them can be rotated up to 120 degrees.



Corner
The angle grinder, popularly called the grinder, is universal in itself.It is designed not only for grinding, but also for cutting metal, wood, glass. You just need to purchase a suitable attachment. It is called angular because of how the spindle is located relative to the body. It is perpendicular to it.
Angle disc grinder. Discs can be replaced as they wear out, and also depending on what kind of work needs to be done at the moment. There are nozzles with spraying of electrocorundum, silicon carbide, granite. The hardest is diamond spraying.... Among other things, there are special grinding attachments (for example, petals are usually used for grinding wooden surfaces), brush attachments and others.
Although the name may be misleading, work in hard-to-reach places, as well as in corners, with the help of this machine will not work... The round rotating disc is not intended for this: it will not enter the corner so as to grind it completely.
For processing a flat surface at any stage, whether it is removing paintwork or polishing a part, an angle grinder is ideal.



Parquet grinding
An electric parquet sander is commonly purchased by floor laying professionals. There are several types of such devices. For example, a drum sander is suitable for rough processing of parquet, removing old varnish. A drum machine by the type of work resembles a roller with the only difference that sandpaper of the desired abrasiveness is wound on the drum.
Among other things, parquet sanding units also work with discs. When we talk about a parquet disc sander, we usually mean a single disc model.
The abrasiveness of the consumables of these machines can vary greatly. They have great power, which makes it possible to work with concrete floors (for example, to level their surface). As for the finishing, the parquet grinding models are also used for it.
However, it is not only about parquet processing. You can also use the unit to trowel ceramic tiles or ordinary wood floors.
The machine is supplied with a special powerful vacuum cleaner. In addition, it weighs much more than all those listed here, so it is extremely rarely purchased for domestic use. Usually it is bought by professionals, and ordinary owners rent it. Such a device is also much more expensive.


Polishing
Almost each of these options can be used as a model for polishing. You just need to pick up a special attachment. However, there are special machines on the market that are only suitable for polishing work. They are not intended to be used for anything else. Such devices, as a rule, are small, made taking into account the fact that you will have to work with them manually. They don't weigh very much.
The attachments can be completely different. They are made from a variety of materials: faux fur, foam rubber, felt, wool, nylon, felt. Some materials are universal, and some are suitable only for working with certain details. For example, a felt attachment can perfectly polish wooden elements and surfaces, and a foam attachment can perfectly polish metal ones.
Remarkably, belt sanders are rarely used for polishing, as it is not always possible to find a suitable accessory on them. But eccentric, delta grinders and angle grinders are used everywhere.

Brush
Some brush machines are designed as belt-type. Although outwardly they are not similar, the principle of operation is the same there. It is based on the work of rollers. In the process, two brushes are involved at the same time, so such models are more suitable for working with large surfaces. They are more often purchased by professionals, since they are a rather cumbersome mechanism.
The choice of brushes is wide enough. Of greatest interest are nylon brushing brushes used for working with wood. With their help, it is structured and artificially aged.
In the process of polishing with this brush, the softer layers of wood are removed and only the hard ones remain, and the wood acquires a beautiful, pronounced pattern.
Single-brush machines work on a different principle. Outwardly, they look like corner models, since the spindle is also attached here at right angles to the body. Only one brush is involved in the work process. But such models are more mobile and lightweight and are better suited for manual labor. With their help, it is possible to process hard-to-reach places, since the convenient configuration and the presence of additional handles allow this.



Multifunctional
In general, there is no such thing as a multifunctional grinder. But there are multifunctional tools designed for grinding and polishing products from various materials. They come with a variety of attachments of different shapes and properties, for example, triangular for medium processing, round for polishing, etc. Also included are emery materials with different abrasiveness.
Such devices are necessarily equipped with a dust removal system, sometimes it is possible to connect a vacuum cleaner to them... For home use, multifunctional tools work well, however it is not recommended to choose them for professionals... Despite the huge number of settings, they do not have the required power. Also, they often cannot be used for a long period of time: they quickly heat up.
Multifunctional tools include a grinder, with which you can perform not only grinding and polishing work, but also cut almost any building material.



Special cases
Despite the huge variety of models, not all needs were met. For example, none of them allows you to sand the ceiling and still not get very tired. To fix this, engineers came up with a telescopic machine. It looks a bit like a regular mop, as it has a sliding long handle. But this makes it possible to reach the ceiling without any problems, while not keeping your hands above your head all the time.



The vertical grinder is designed for sharpening metal tools such as drills. There are also models with which concrete surfaces are polished. For example, you can grind walls with such a machine.


A bench grinder is essentially a grinder.
She can sharpen knives, scissors, skates, manicure supplies and more.


Flexible Shaft Sanders are essential when you need to machine a hard-to-reach area that cannot be crawled into with a conventional tool. For example, we can talk about the processing of large depressions or surfaces in a narrow gap. Also, this unit is useful when working with metal: you often have to clean up small spaces, while trying not to bend adjacent parts.
By the way, a mini metal cutting machine will also help in some of these cases. A small manual machine weighs a little, and has the same functionality as a full-fledged model.


The rotary machine is designed primarily for coarse sanding.
It does an excellent job on metal or stone due to its high power.


Model rating
The masters have compiled a rating for different categories of grinders. It includes not only specialized tools intended for professional use, but also household tools.
Among the grinders, such brands as Interskol, Makita, Bosh are especially distinguished. The Russian company "Interskol" the models of tape machines LShM-76/900 and LShM-100 / 1200E are popular. They vary in weight and price. The first one is intended for domestic use and costs half as much as the second one.


Makita offers grinders of good quality and at an average price. Customers most often opt for belt 9911 and 9404, orbital BO5031 and BO5041 and orbital grinders BO3711 and BO3700.



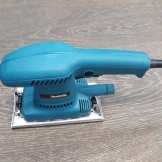
Brand reviews overview Bosh showed that it makes good cars, but their cost is overstated due to the promotion of the brand. Nevertheless, the models of belt sanders PBS 75 AE, eccentric GEX 150 AC and GEX 125-1 AE Box, orbital sanders PSS 200 AC deserve the greatest confidence.



How to choose?
When thinking about choosing a suitable grinder, you need to remember the rules for the selection of both the device itself and the abrasive materials for it.
First of all, focus on the work that you will perform with your grinder. Please note that rough processing and polishing require different tools... Most people choosing such a pair opt for a band model for rough and eccentric model for polishing work. It is advisable that both devices were with speed control - this will greatly simplify your work.
Try how the instrument fits in your hand before buying. A comfortable grip is essential for efficient work. If you keep thinking about how to grip the tool, you will not be able to concentrate on the grinding process itself, which will increase the risk of making a mistake.
Try to get the attachments you need right away. At the same time, only "native" consumables are not always suitable for the tool. In some cases, you can purchase cheaper, but no less quality abrasives. Do not hesitate to try on the sander attachment immediately in the store.



To correctly select the abrasiveness of the emery material, use the following table.

Operating tips
First of all, it is necessary to observe safety measures: use headphones that will prevent injury to the eardrum, wear safety glasses, cover open skin with thick clothing.
Do not use equipment that you are not sure is working properly. Be sure to check the cabinet and cord before connecting the instrument to the mains.
When working with metal, make sure there is no flammable material nearby. Sparks will be emitted during the grinding process, so it is important that nothing can catch fire.
Unplug the power tool before cleaning the dust extraction system.

For an overview of grinders, see below.
The comment was sent successfully.