Spray gun for a vacuum cleaner: types and production

A spray gun is a pneumatic tool. It is used for spraying synthetic, mineral and water-based paints and varnishes for the purpose of painting or impregnating surfaces. Paint sprayers are electric, compressor, manual.
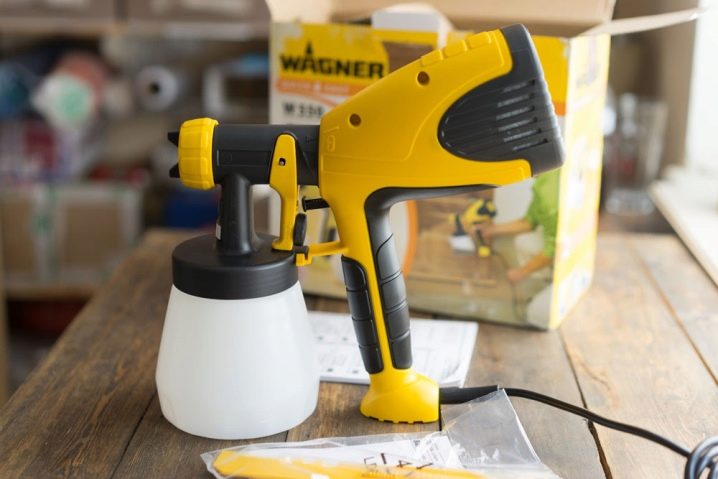
Varieties
The division of the paint-spraying tool into subspecies is determined by the method of supplying the working material to the spray chamber. The liquid can be supplied by gravity, under pressure or by suction. The injected pressure is a factor influencing the shape, length and structure of the "flame" - a jet of paint and varnish material. The stable operation of the apparatus can be ensured by both a high pressure coefficient and a low one.

High pressure spray guns are technically complex devices. Making them at home is not recommended. Self-assembly can result in damage to the structural integrity of the spray mechanism itself and uncontrolled release of working fluid.
Low pressure sprayers are less demanding in the area of housing resistance to internal impact. They can be used in combination with devices equipped with low-torque suction-blowing units. One of these devices is a vacuum cleaner.

This device is equipped with an electric motor that drives a turbine. The latter creates the effect of suction of the air flow. Some modifications of vacuum cleaners provide for the outlet of the air stream from the opposite side from the point of its intake. It is these models that are used in conjunction with sprayers. Vacuum cleaners of old models are mainly used as a suitable "compressor" for the spray gun: "Whirlwind", "Raketa", "Ural", "Pioneer".
Vacuum spray guns are simple in their device. They can be assembled with your own hands from scrap materials.
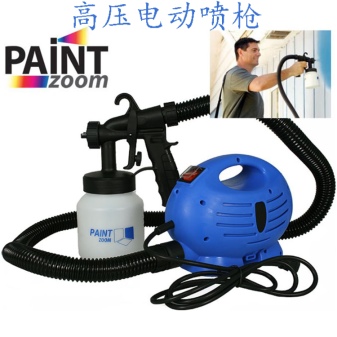

Principle of operation
A low pressure spray gun works on the principle of pressurizing a container with a working fluid. Under the influence of pressure, it enters the only outlet leading to the spray assembly.
The tightness of the joints of the structure is important. The slightest air leakage excludes the possibility of full operation of the device.
The diameter of the hole through which the air enters the pressure chamber and the duct for the discharge of the pressurized air must correspond to the capacity of the vacuum cleaner. Too large a diameter value reduces the efficiency from the pressure that the unit creates. A small value of this parameter increases the likelihood of exceeding the permissible load on the engine of an improvised "compressor".
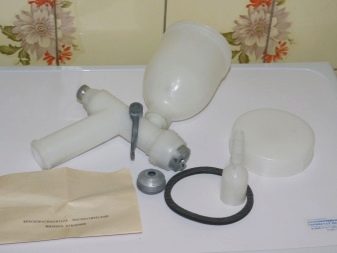

How to make?
The easiest way to achieve the goal is to select a special nozzle that was supplied with Soviet vacuum cleaners. It fits over the neck of a 1 liter glass jar.
In this case, it is necessary to adjust the outlet of the nozzle to meet the target parameters. Then you need to fit the edge of the vacuum cleaner hose to the point where the air flow enters the sprayer. If their diameters do not match, it is worth using an adapter with a hermetic seal (for example, rewind with electrical tape).A common model of the described nozzle is shown in the photo.

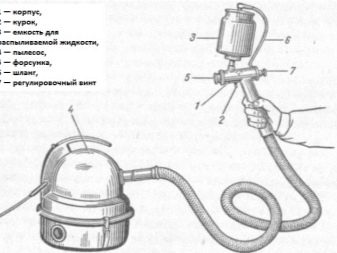
If it is not possible to install a paint spray nozzle, you can assemble your own spray arm. The following instructions will help you get things done.
Preparing the vacuum cleaner
At this stage, it is worth minimizing the load on the engine of the dust collection unit. To do this, remove the waste bag, if any. Then remove all filter elements that are not involved in protecting the electric motor from dust. It will be easier for air to pass through the vacuum cleaner's suction system. It will be ejected with more force.
If the vacuum cleaner has only a suction function, and the air outlet is not equipped with a corrugated hose connection mechanism, a partial modernization of the device will be required. It is necessary to redirect the air flow so that it starts to come out of the pipe through which it was previously sucked. This can be achieved in two ways:
- changing the polarity of the motor contacts;
- by redirecting the turbine blades.


The first method is suitable for vacuum cleaners of earlier years of production. Their motor design allows the direction of rotation of the shaft to be reversed. It is enough to swap the contacts through which power is supplied, and the engine will start to rotate in the other direction. Modern models of vacuum cleaners are equipped with a new generation of motors - inverter. In this case, changing the positions of the contacts will not give the desired result.
The problem is solved by changing the position of the turbine blades relative to their rotation. Usually these "wings" are set at a certain angle. If you change it ("reflect" the opposite), then the air flow will be directed in the other direction. However, this method is not applicable to all models of vacuum cleaners.

It is important to consider that any intervention in the design of the vacuum cleaner automatically removes it from the warranty (if any), and can also lead to irreversible consequences. Therefore, it is recommended to use only a used vacuum cleaner for spraying paint and varnish liquids, which is no longer suitable for the intended use.
Required parts and tools
You can use a hand-held spray gun, upgrading it to fit your needs. A suitable model of this device is shown in the photo below.
The advantage of this manufacturing method is that the sprinkler is already equipped with key components:
- spray tip;
- pressure chamber;
- air intake and manual content release systems.


For the conversion, you will need the main parts:
- a plastic tube (its diameter should allow the hose of the vacuum cleaner to freely dock with it);
- sealing agents (cold welding, hot melt or others);
- pressure relief valve.



Instruments:
- marker;
- stationery knife;
- glue gun (if hot melt glue is used);
- a drill with a circular saw attachment with a diameter equal to the diameter of the plastic tube;
- nut with a diameter equal to the base of the pressure relief valve;
- rubber gaskets and washers.
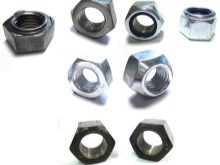


Each specific situation may determine a different set of accessories and tools.
Manufacturing process
Using a drill with a circular nozzle, you need to cut a hole in the wall of the tank of the hand sprayer. The location of the hole is determined individually based on the convenience factor that is relevant for a particular user.
A plastic tube is inserted into the hole. There should be no more than 30% of the tube inside the container. The rest of it remains outside and serves as the connection point for the vacuum hose. The place of contact of the tube with the tank wall is sealed using cold welding or hot glue. The likelihood of "fistula" should be excluded.
It is allowed to install a non-return valve at the point of contact between the hose and the tube.Its presence will provide protection against the ingress of liquid into the suction hose and other systems of the vacuum cleaner.


Using a knife or drill of the appropriate diameter, you need to make a hole into which the pressure relief valve will be inserted. In the process of its installation, rubber gaskets and washers are used to seal the place of contact between the valve and the tank. These seals are seated on the sealant.
The hose of the vacuum cleaner is connected to a tube installed in the wall of the container. Their connection is sealed with electrical tape or tape. In case of maintenance of the spray gun, the contact assembly of the hose and the spray gun must be collapsible.
At this point, the paint sprayer is ready for testing. The performance check should be carried out in an open space using clean water as a tank filler.

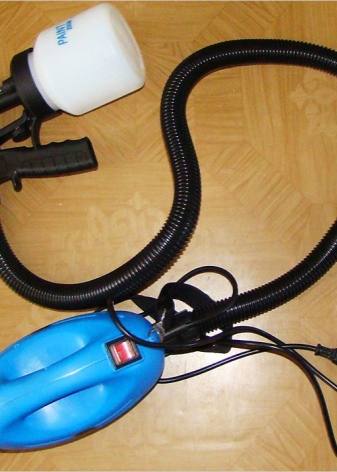
Nuances
The described model of the spray gun has a drawback: the impossibility of starting and turning off by pressing the trigger. In order to use it, you need to activate the vacuum cleaner, and then press the trigger. If this pressing is not made, the pressure in the system will increase. The pressure relief valve is designed to eliminate excess pressure, but this is not a complete solution to the problem. In case of failure or failure, internal pressure can destroy the structure of the atomizer or create an excessive load on the electric motor of the vacuum cleaner.
The problem is solved by installing an additional option - an on / off button. The latter is the "key" of the chain, which will close it at the moment the trigger is pressed. The button should work without fixing in any position.

To implement the automatic on / off function, it is necessary to insert an additional electric wire into the network cable of the vacuum cleaner. The insert separates the zero core of the cord and brings the point of its connection to the button mentioned above.
The button is located under the release lever. At the moment of pressing, he presses on it, the electric circuit is closed, the vacuum cleaner starts to work, the pressure is injected.
Testing and operating rules
In the process of checking a homemade paint sprayer, attention is paid to the tightness of the joints and the quality of the spray of the coloring liquid. The leak must be repaired if necessary. Then it is worth setting the optimal spray level by scrolling the tip in different directions.
Using water, it is possible to evaluate the "flame" characteristics of the spray arm without damaging any finished surface. This data will help you in the future to spray the paintwork with the greatest success.
The function of the pressure relief valve is then checked. Since the hand sprayer works only when the trigger is pressed, the pressure generated by the vacuum cleaner can become excessive when the trigger is not pressed.

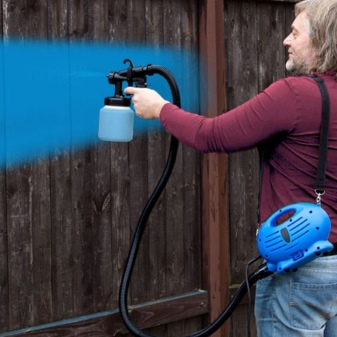
The successful use of a homemade spray gun is ensured by observing certain operating rules:
- the working fluid must be thoroughly filtered;
- flushing of all conductive channels is carried out regularly (before starting work and at the end of it);
- it is important to avoid overturning the spray unit during operation;
- do not abuse the operation of the device "idle", overloading the pressure relief valve.
The advantages of a homemade device
The main advantage of a homemade spray gun is its cheapness. The minimum set of components allows you to assemble an apparatus suitable for painting, impregnation, varnishing and other works related to the spraying of liquids. At the same time, a well-assembled sprinkler has an advantage even over some factory models. Not every spray gun that works without an external compressor is capable of high-quality spraying of water-based and acrylic compositions.
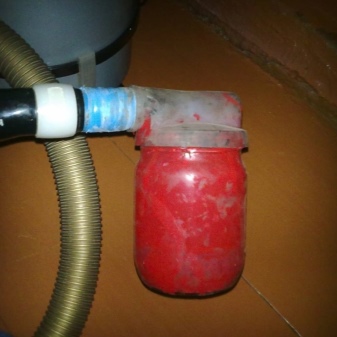

For information on how to make a spray gun from a vacuum cleaner with your own hands, see the video below.
The comment was sent successfully.