Description and creation of foam boats
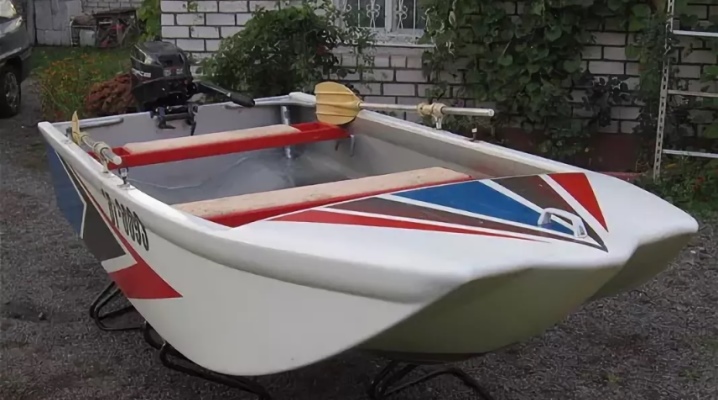
Describing Styrofoam boats and building them is very important. Many people are keenly interested in how to make them with their own hands from foam and fiberglass. In addition to getting acquainted with the drawings of a homemade foam boat, it is important to find out everything about its manufacture without fiberglass.
Features of a homemade boat
Don't think that the foam boat is just a demonstration model. In fact, it can demonstrate very good performance. The lightness of foam structures is undeniable. This material will remain on the surface for a long time.
Homemade craft can be used for fishing, and for trips along lakes, rivers, canals.
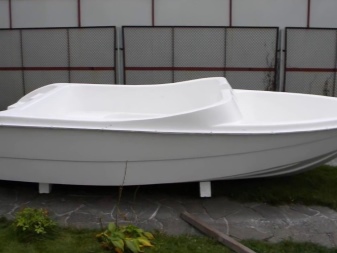
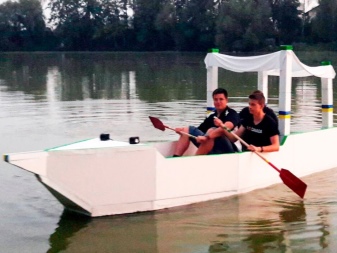
Styrofoam is easy to handle. It manages to give it almost any shape, which expands the flexibility in the use of designs. The inertness of the known insulation material is large enough to interact well with wood and fiberglass. It is also neutral in relation to epoxy resin. Subject to correct, competent calculation and intelligent manufacturing, operational problems should not arise.
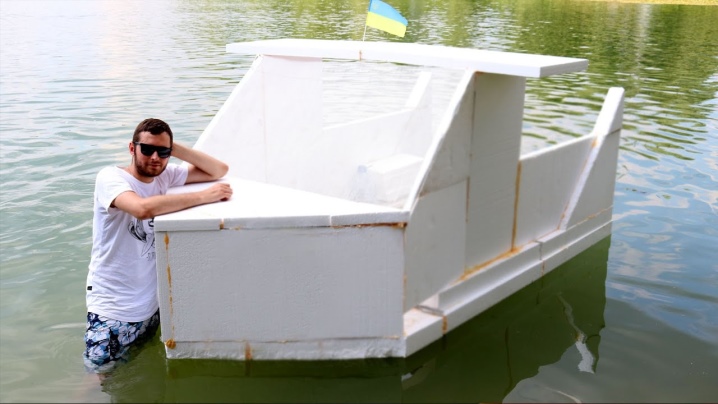
Project preparation
Drawing up a diagram is a very important step. All parts of the structure and their dimensions are thought out in advance. They take into account how many people will travel, how large the cargo planned for transportation is. It is necessary to determine in advance whether the boat will be equipped with a motor or not. Equipping with an engine is possible only with structural reinforcement of some parts.
The drawing should reflect:
- nose and rear transoms;
- rear segments of sides and bottoms;
- main boards;
- main bottom;
- the bow of the boat edge;
- sheet for the cheekbone.
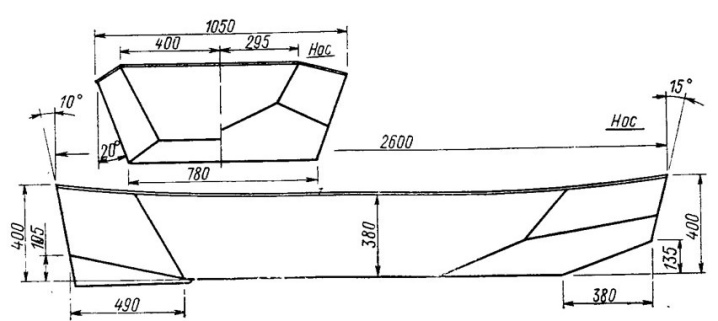
Drawing is advisable to carry out in close to real dimensions. This will reduce the likelihood of miscalculations. It is also useful that the body parts with this approach can be marked directly. The scheme is transferred to plywood (this workpiece is called plaza). The plaza includes an indication of all the parts that form the skeleton of the ship being created.
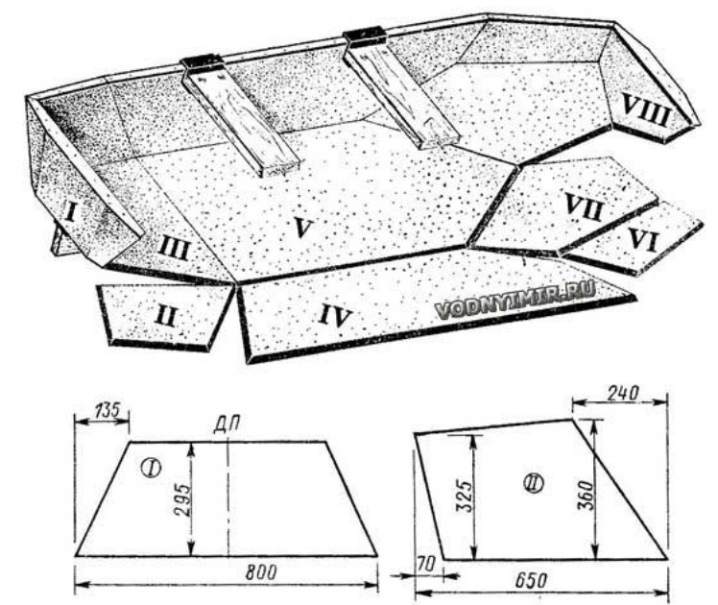
There is rarely enough space on the plazas, and this problem is constantly faced by all shipbuilders. It helps to save it by drawing projections of the sides and half-latitudes on top of each other. In order not to confuse anything, lines of different colors are used. Each mentioned projection should show the sections of the frame of the two sides, connected in the assembly behind and in front. It is very important to follow the correct placement of theoretical lines, such as:
- the front surface of the case;
- material laid on the deck;
- frame perimeters;
- edges of stringers and carlengs.
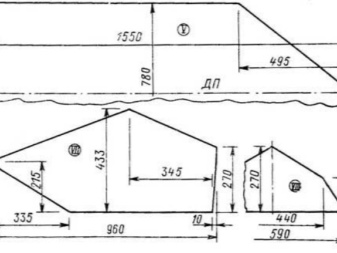
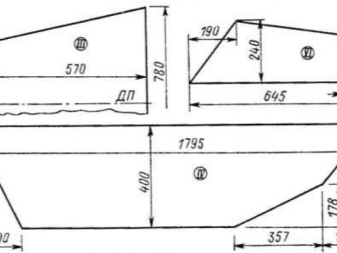
Manufacturing methods
There are several options for how to make a quality watercraft.
Classical
It is quite possible to make a simple collapsible boat from foam plastic for construction purposes with your own hands. When the drawing is ready and all the materials are prepared, you can immediately get down to work. They start with the formation of the frame. The cladding is attached to it. They try to make the main body as strong as possible, because the characteristics of a home-made craft and its reliability on the water in various situations depend on it. The parts of the sheathing must be adjusted and glued as tightly as possible.
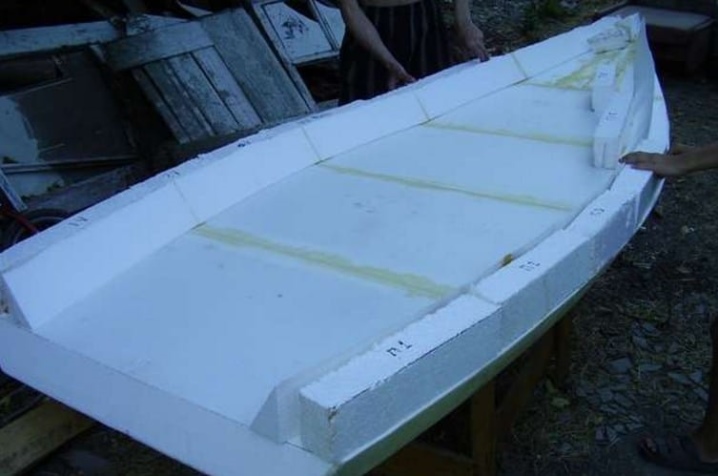
The cladding is formed both from the inside and from the outside. In both cases, mechanical strength is important for her, which guarantees the safety of the boat. The skeleton of a boat is created from wooden blocks. It is made in parts, connected with nails or screws.Additional reinforcement of the skeleton is made by attaching plates and corners, and the ribs of the frame part are best made of plywood.
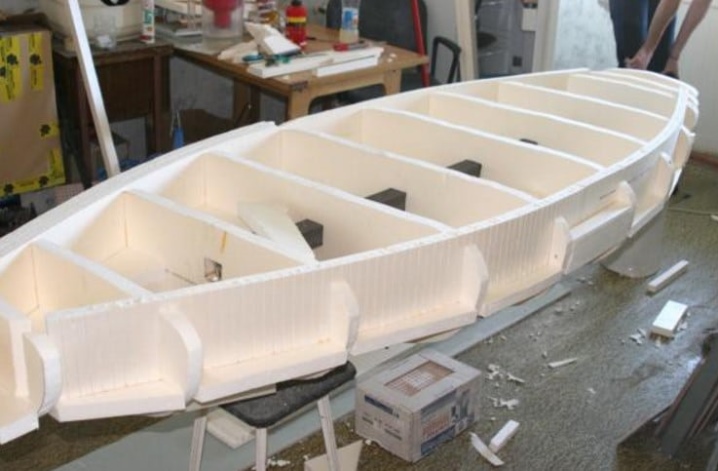
The next stage of construction is the formation of the main skin. It is created with the expectation of maintaining buoyancy. The cladding is made of foam sheets 5-10 cm thick. Additionally, you will need epoxy glue. Since Styrofoam sheets cannot be bent, each corner is created from 3 pieces. Diagrams and measurement lines are transferred to the panel.
The structures are glued to the frame. Instead of glue, you can use nails with wide flat heads. Internal cladding is usually made of plywood. They are mounted in the same way one after the other in order to do everything right. It is imperative to ensure that the plywood blocks do not bend, because they can damage the base material.
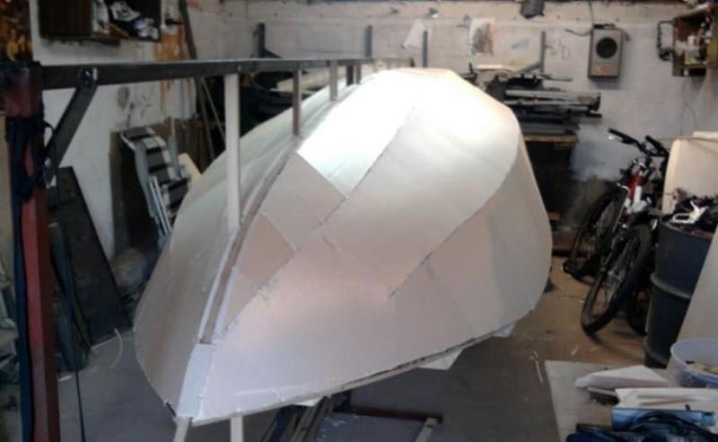
Using fiberglass
The technology of using fiberglass is attractive in that it allows you to equip the boat with a motor. The material reinforcing the structure must be cut into canvases. They must be the same length as the body. Any joints are categorically unacceptable. To make a fiberglass structure, it sometimes has to be stitched together.
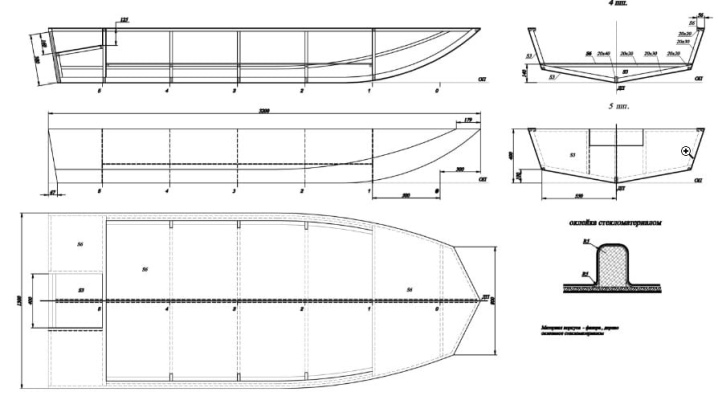
In this case, fiberglass threads are used, pulled out from the waste generated from it. An alternative is ordinary linen thread, but it will have to be impregnated with linseed oil in advance. Fibrous material should be thoroughly treated with polymer resin. Stitching rollers are best suited for this purpose. Everything should be done so that even minor air bubbles do not remain.
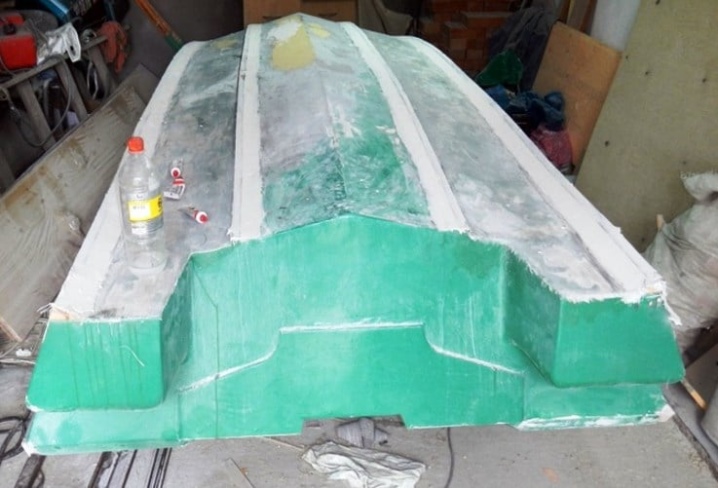
By themselves, they are not harmful, but this is a sign of the presence of voids. And each void weakens the structure very significantly. Each layer of fabric is installed in the same way. It is allowed to use 1-5 layers of fiberglass.
It is recommended to use 300 grade fiberglass. It is applied in 2 layers.
The amount of fabric is selected in advance. Before gluing it, the base of the boat is prepared very carefully. This preparation is done by fixing a steel angle similar to that used in putty work. As a result, the corners will be stronger and their shape will be better preserved. Temporary fixation of corners (including for fitting) can be made with small screws.
The fiberglass must be fired before gluing. Appropriate processing is often carried out over a fire by being pulled through a flame with the aid of a companion. A blowtorch and even a gas torch can also be used. In the last two cases, the fabric is suspended and carefully handled. The fabric improved in this way is placed on the frame along the boat.
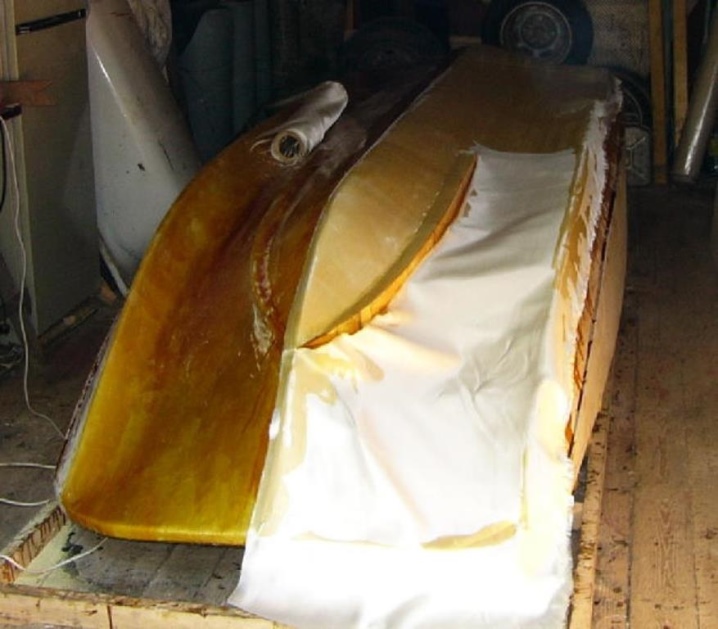
Each next section is laid with an overlap of the previous one by 15 cm. All of them must be carefully smoothed and pressed to the surface. The layers are laid mutually perpendicular to weave the fibers and form a strong coating. You need to smooth out any layer, no matter how it goes. After preparing the boat, you should leave it alone to begin the resin polymerization process.
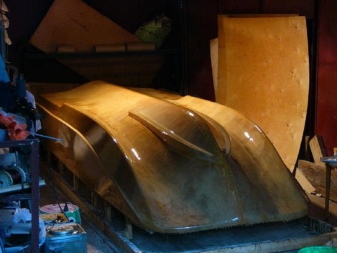
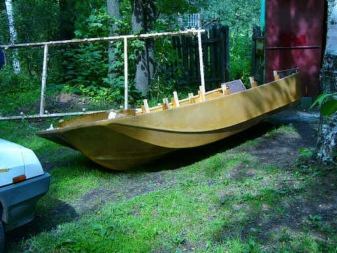
For information on how to make a foam boat, see the next video.
The comment was sent successfully.