How to make a band saw with your own hands?

Various tools are always useful in the household, especially when it comes to living in your own home. One of the irreplaceable products is the band saw. In this article, you will learn how to make such a tool yourself, what are the features of this process. You will also familiarize yourself with the safety precautions that must be followed during the manufacture of the saw.
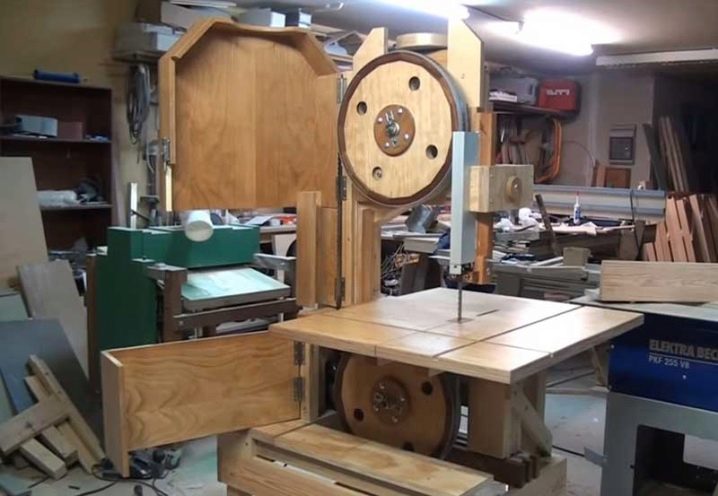
Necessary equipment
Such a tool is sometimes needed if there is a need to work with a tree. Although some models of band saws also allow you to work with synthetics, metal, stone. The high density of the materials described requires the use of devices in which there are components made of steel of the reinforced group. A standard analogue will not work due to the fact that when processing metal or any of the other materials mentioned, a disc with teeth very quickly becomes unusable.
If we talk about the equipment that will be needed to make a band saw, these are:
- welding machine;
- welding machine (it is better if it is a semiautomatic device);
- Bulgarian;
- sharpening machine;
- electric jigsaw;
- Sander;
- screwdriver.




By the way, electric tools can be easily replaced with manual counterparts. However, it should be borne in mind that this will significantly increase the time of the assembly process and will require a lot of labor.
Tools and materials
To create the type of saw in question, you will need the following tools and materials:
- a piece of plywood about 1.5 centimeters thick;
- timber made of solid wood;
- tapes or attachments that will be used for a screwdriver or grinder;
- a pair of bearings for the driving axle;
- studs, washers, self-tapping screws, nuts, shoe;
- a pair of shafts;
- bolts that will be used to adjust the vertical and horizontal types;
- a pair of internally threaded brass bushings;
- PVA glue;
- bearings under the axle of the upper type;
- lamb for adjusting screws;
- insulating tape.
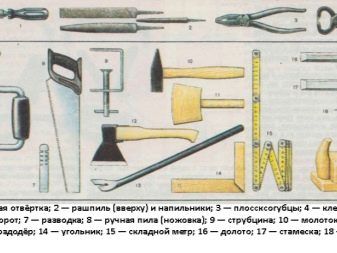



Separately, it should be noted that for the correct creation of certain parts of the saw, it is necessary to have drawings. Also for work you will need the following components:
- pulleys;
- sawing table;
- base;
- saw blade;
- the mechanism responsible for tightening the tape.



Choice of tape
It is extremely difficult to make such a canvas for wood or metal carving at home. For such purposes, tool steel of the U8 or U10 type is suitable. A log saw should be as flexible as possible. Its thickness for soft wood should be approximately 0.3 mm, and for harder wood - 0.5-0.7 mm. The length of the saw blade itself will be about 170 centimeters.
You also need to make the teeth yourself, correctly set and sharpen them. To weld the tape into a solid ring, you need to use solder and a gas torch. The seam of the joint itself should then be sanded.




It is more convenient to purchase a finished product in a store. Typically, the width of such canvases is from 1.8 to 8.8 centimeters. It is better to choose a model for such a saw based on what material you plan to cut. Manufacturers usually offer the following categories of saws:
- from hard alloys (they make it possible to process high strength alloys);
- on the basis of diamonds (their use allows you to saw materials such as marble, quartz, granite);
- made of strips of steel of the instrumental type (they are used for sawing wood);
- bimetallic (they are necessary for working with metals).

If the saw is homemade and small, as in the case under consideration, then it is best to buy a product made of strips of instrumental steel. This option is affordable and practical. If the work will be carried out with materials of a hard type, then it is better to buy an expensive saw that is highly durable, which will be resistant to wear.
If such a tabletop horizontal mini-saw will be used for a curly type cut, then the width of the panel should be selected taking into account the radius of curvature. Another important criterion is the quality of the sharpening of the teeth. The cutting edge should be as straight and sharp as possible.


How to do it yourself?
After carrying out the calculations and adjusting the dimensions of all elements, you can begin the independent installation of the band saw. The main element of a carpentry machine is a work table, where wood, metal, stone or synthetics are processed. This design involves a circular movement of the cutting element, which affects the workpiece. Fastening is carried out with a pair of pulleys. It should be said that the entire structure takes up a lot of space, therefore, when creating drawings, the dimensions of the room should be taken into account.
The frame of the bed is a supporting part that holds the entire mechanism of the device in question. It is made exclusively of metal profiles, which need to be welded due to the fact that due to vibration during operation, the load increases significantly. If the machines are small in size, and there are no metal profiles, then analogs made of wood will do. But it should be a solid board with a width of 2-3 centimeters, and not plywood sheets or material such as chipboard.
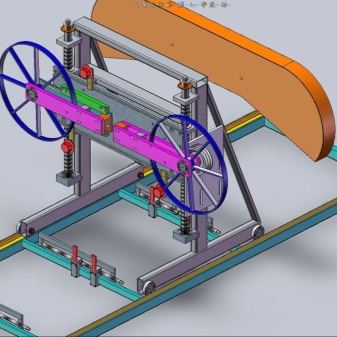

The boards should be joined so that the layers converge at the intersection of the fibers. An extremely important detail will be the pulley block, which is responsible for the tension of the blades. The wheel shaft is fixed in an insert, which is located inside the frame. The axis is adjusted with 2 threaded rods. Now let's go directly to the features of the assembly process.
From the bike
Let's consider the process using the example of a variant made of bicycle wheels. First, a frame is created, which will be the base. It can be made from an inch of pine, planed on a thickness gauge to a thickness of two millimeters. The frame can be glued from a series of overlapping plank layers. It is made in the shape of the letter C. Above, a base for a tensioning guide with a wheel is installed, and two supports are mounted on the bottom, which are connected to the base. When gluing gradually, you should carefully monitor the perpendicularity of the parts so that the frame is flat.
The next part is the assembly and installation of the movable block for securing the wheel from above. Such a block should move in a vertical direction and tension the saw blade. On the previously made frame horns, an oak profile is fixed, forming a guide-type groove. The block itself is a rectangular frame with a holder for the shaft of the upper wheel inserted into it, which is moving.
The next aspect will be the manufacture of saw wheels. They should be 40 centimeters in diameter. It is best to make them either from MDF or plywood. The easiest way will be to glue them from three plywood circles.
It is important to pay special attention to the central part. Wheels can be made using a milling machine. A hole is made in the circle in the center, where a milling-type compass is inserted. This hole is used for aligning the workpieces and subsequent gluing.



Then plywood flanges should be made and placed on the wheels.The flange itself is made of two elements. The outer one and a half millimeters thick holds the bearing. The one inside is 1 centimeter thick and forms the space between the wheel and the bearing. In the outer part of the flange, make a hole for the bearing, press in using a mallet. The flanges are glued to the wheel, after which a wheel shaft holder is made, which will be located at the bottom.
Also, 4 technological holes are made in the wheels so that clamps can be installed during gluing. When the wheel is glued together, it should be immediately mounted on the shaft. If everything is fine, then you can carry out wheel fixing.

After that, a standard drive pulley is attached to one wheel. It remains only to carry out wheel balancing. You can use the bearings as support for the panel, where the sawing will be carried out. After fixing the time axis horizontally and putting on the bearings, the wheel is placed in such a way that it simply rotates, and its heaviest part is lowered. Then they make small indentations in the lower part of the wheel from the rear, which will be the last balancing step. After that, you should put on the cut cameras from the wheels from the children's bike.
It remains to attach the wheels to the saw frame. Put the top wheel first. A washer is put on the shaft, and then secured with a bolt. The same is done with the wheel underneath. Using a ruler, set the wheels in a plane. Fix both wheels and test. The band saw is ready.


From a jigsaw
Consider how to make a tool from a jigsaw. To make such a saw, you need to do the following:
- form a frame from the boards, similar to a curbstone with dimensions according to certain drawings, inside which to mount an electric motor;
- make a bar from a bar;
- attach supports for plywood pulleys so that you can cut various workpieces;
- attach the frame to the cabinet;
- in the support from below, make a hole for the pulley, where a bushing with 2 bearings is inserted;
- lay a tabletop made of plywood on top;
- sheathe the sidewalls.


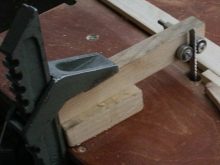
After that, it is necessary to connect the pulleys from the motor and the belt, which performs cutting. They are mounted on a shaft made from a steel bar. The pulleys themselves are made of plywood circles that are glued together to make a part 3 centimeters thick. There should be three of them. One is needed for the belt wire, two more for the web of the tape.
The first is installed inside the pedestal, and the rest - from the bottom and top, as they will activate the saw. A hole is made in the center of what is on top. The bearing is inserted into the bushing and then locked. This pulley is then fitted with a bicycle tube.
The upper pulley is attached movably to allow the cutting belt to be tensioned. The lower pulleys must be attached to the shaft. The one that will be the leader is put on a strap. When the elements are mounted, align them. They must be in the plane of the vertical type. Washers can be used for this. The cutting tape is attached to the pulleys, and the machine itself is equipped with a guide part.


Simple plywood model
Let's describe another option for creating a saw - from plywood. To create a base, it is better to take stronger wood. It is also necessary to resolve the issue with the drawings.
It is necessary to make a frame in the shape of the letter C, which has already been described above, after which the table should be assembled. Its height should be optimal for work. In addition, the bottom pulley, wire pulley and motor must fit into it. The shape of the table can be any.
The table top is installed directly on the support from below, after which the pulleys are cut. They can have an arbitrary diameter, but the larger they are, the longer and better the saw will work.
You should choose the right canvases. The best blade to pulley diameter ratio is one to a thousand.




To secure the pulley from above, a special movable block will be needed, which must move in a horizontal direction. This is necessary in order for the tape to stretch. You will need a special lifting type mechanism. The simplest option is a block mounted under the block and connected to a lever with an extremely tight spring. Also, self-aligning bearings should be provided in the pulley mount from above, so that you can quickly put on and dismantle the wheels. They must be attached as tightly as possible, otherwise the structure will soon become loose.
Along the blunt end of the saw, it is necessary to mount the guides on a small block. If you want to make everything simple, then you can screw three roller-type bearings to it. Part of the canvas will rest on the first (it will be flat). The other two will hold the tape from the sides.
Align the guides well at the anchor point. Even a small deviation can cause problems. It is better to mark the beam position with the canvas stretched as much as possible and the guides already set. Instead of two bearings on the sides, it is possible to form the restraints from wood. The design as a whole resembles the solutions described above.



Safety engineering
Before you start making a band saw yourself, you should learn about some aspects of the work. It is important to strictly adhere to all safety standards. In some cases, the blade may not be able to withstand, so you should check its attachment before using the machine. It is also worth considering the following points:
- the larger the workpiece you have to work with, the larger the teeth the saw should have;
- it is better to use tapes for cutting of a universal type (then the blade does not need to be changed every time you have to work with a different material);
- before the creation of the device, it is imperative to choose the place where it will be located in order to take into account its future dimensions;
- before starting work, it is necessary to tighten the cutting tape as much as possible, otherwise the machine will not perform its work normally;
- the device should be active for no more than 120 minutes in a row, after which it should not be touched for 24 hours.
After long-term operation, the device must be lubricated.



For information on how to make a band saw with your own hands, see the next video.
The comment was sent successfully.