Description of fireclay clay and its scope

In the manufacture of bricks with refractory properties, as well as stoves, fireplaces or decorative items, fireclay is used - fire-resistant clay. Fireclay consists of white kaolin, which, when processed under high-temperature conditions, acquires a high degree of fire resistance. After passing through hardening at high temperatures, fireclay has a special strength that can be compared with a stone rock.
The crushed chamotte is called "chamotte clay". It has a high degree of plasticity, resistance to high temperatures, and also has a decorative appearance, which is used in the process of plastering furnace surfaces.
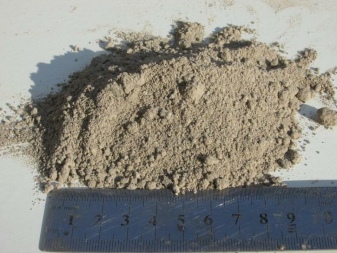
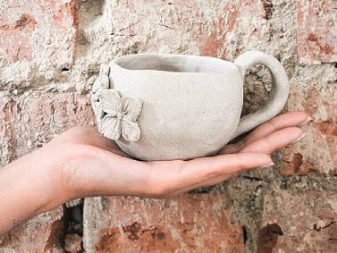
What it is?
Refractory chamotte clay includes high dispersion hydroaluminosilicates. This material is classified as a natural fossil and is subdivided into clays of marine type and continental origin. Sea clay is mined from the bottom of the sea, while continental deposits are found in river and lake sediments. In Russia, chamotte clay is mined at deposits, the largest of which are Astafyevskoe, Kyshtymskoe and Palevskoe.
The color of the rock looks depending on its constituent components of organic impurities. Pure clay has a light gray color, but red, blue, and yellow varieties are also common.
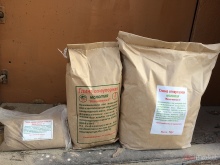
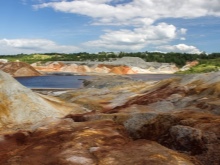
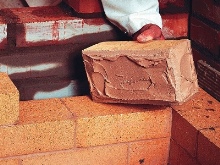
The composition of refractory chamotte clay is as follows:
- quartz sand elements;
- potassium oxide;
- aluminum oxide;
- calcium oxide;
- magnesium oxide;
- sodium oxide;
- iron oxide.
The demand and popularity of chamotte is quite high, and this is due to the fact that the composition of the product is completely natural and has a high degree of resistance to high temperature conditions. In addition, the chamotte mixture does not shrink when it dries and therefore does not crack. The duration of clay drying depends on the ambient temperature; on average, this period is 10-12 days.
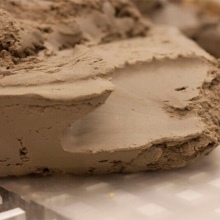
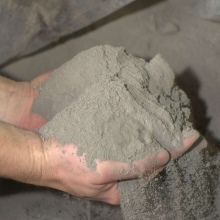
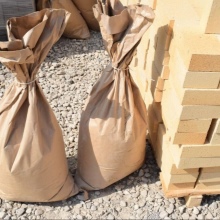
Technical parameters and properties
The characteristics of chamotte clay for each manufacturer must comply with the standards of GOST 6137-8, which determines the main parameters of the product:
- the color of the dry chamotte mixture is gray, the product is free-flowing in structure, without lumps and large conglomerates;
- grain size fraction by diameter - approximately 2 mm;
- high-burnt chamotte has a moisture absorption coefficient of 2 to 10%;
- low-burnt chamotte has a moisture coefficient within 25%;
- the total moisture content of the product should not exceed 5%;
- the melting point ranges from 1550 to 1850 ° C.
The shelf life of dry chamotte composition does not exceed 3 years, when stored in dry and tightly closed packaging. Fireclay clay mixtures are used for laying stoves, fireplaces, chimneys.
Bricks are made of clay, they, like mortar, have fire resistance and thermal conductivity with the same parameters.
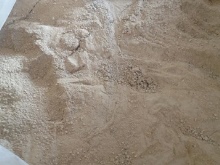
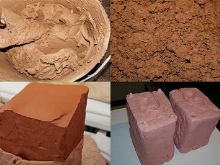

Annealed kaolin has the following beneficial properties:
- a high degree of resistance to high temperature conditions makes it possible to use the product for arranging fireplaces, stoves, and chimneys;
- clay is able to pass moisture through itself, thereby maintaining a comfortable microclimate in the room;
- when laying, clay is used in the form of a solution that has high adhesive properties;
- the natural composition of clay is an absolutely safe product for human health and the environment;
- the service life of clay is long, and during operation the material does not crack or crumble.
The disadvantages of chamotte clay are that this product has a high cost, and to prepare working solutions, you need to know the intricacies of work and have some skills.
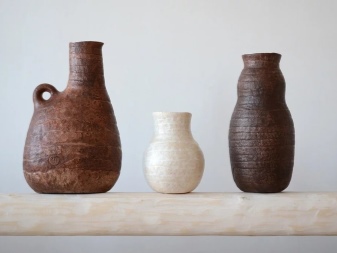
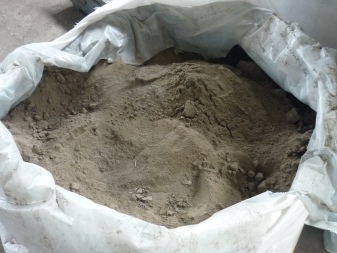
The main physical properties of chamotte clay are its refractoriness, good plasticity, sintering ability and fire shrinkage.
- Plastic - under this term, a moistened chamotte composition means the ability, with the application of small efforts, to modify a given shape, while the mixture remains in its plastic form and does not crack. In clay, plastic properties are manifested only on condition of contact with water, and in small quantities. The plasticity properties depend on the composition of the minerals included in the structure of the clay, as well as on the particle size. When heated to 150 ° C, the plasticity of the mixture is reversible. However, if, after the end of the dehydration process, the chamotte is heated to 500-600 ° C, then the reversibility of plasticity will be lost. If it is required to reduce plasticity, then so-called softeners in the form of quartz, chamotte sand are added to the clay. In addition, excess plasticity can be reduced by adding low-plasticity clays of a different composition.
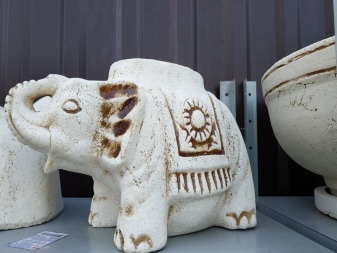

- Binding ability - in chamotte clay, it consists in the ability to bind together finely dispersed particles of sand or chamotte, which in themselves do not have plasticity. When the diluted clay powder dries, a dense and durable formation called "raw" is obtained. By itself, the concept of cohesion implies the force that must be applied to separate the clay particles. The bonding capacity of this material is explained by the small size and lamellar particle shape of the chamotte clay components. The greatest connectivity is inherent in those types of chamotte clay, which contain the largest number of such clay components.
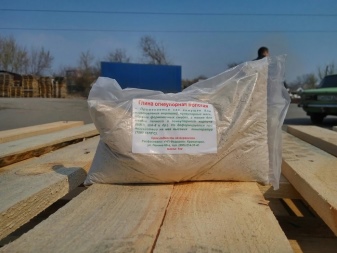
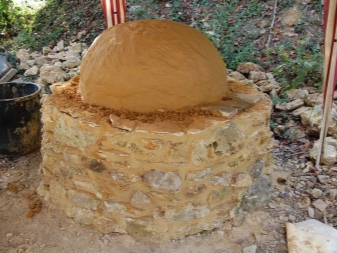
- Air shrinkage - this parameter is manifested by a change in the dimensions of the original workpiece made from a plastic mixture and dried, downward. This value is expressed as a percentage relative to the original size of the unfinished workpiece. The change in the air shrinkage index for chamotte clay is no more than 5-11%. The highest percentage of shrinkage is shown by clays with a high degree of plasticity, they are also called "fatty", and the least degree of shrinkage is shown by the so-called skinny, low-plastic grades of clay. If you use chamotte clay with a high degree of shrinkage, then during firing the product will change its original parameters, which will cause difficulties in the manufacture of products with the specified parameters. To change the situation, chamotte is added to the clay composition, and its amount depends on the binding characteristics of the clay fractions.
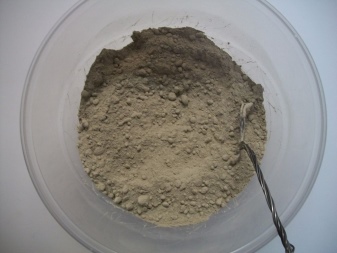
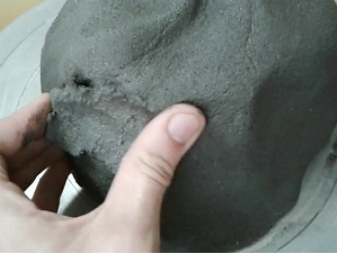
- Fire shrinkage - manifests itself by changes in the volumes and dimensional indicators of the original workpiece in the firing process. The shrinkage of the material is explained by the fact that clay compounds, which are easily melted at high temperature conditions, turn into a liquid state. The resulting liquid substance completely envelops all clay particles that cannot be melted, and also clogs all the voids between these particles. Such a partial remelting of the components of the clay mixture, in combination with the action of the surface tension force of the liquids, causes the maximum approximation of all the components of the mixture to each other, while the volume of the workpiece decreases, which is called the shrinkage of the fire type.If the chamotte composition contains a large amount of a quartz component in the form of fine fractions, then there may be no shrinkage, or expansion of the particles of the composition is carried out, since when heated, the quartz particles will form a new type of crystal lattice of particles with an increase in their volume. Fire-type shrinkage of chamotte clay, as a rule, does not exceed 3-6%. There is also the concept of complete shrinkage, which consists of the interaction of fire and air shrinkage in total, this indicator is in the range of 6-18%.
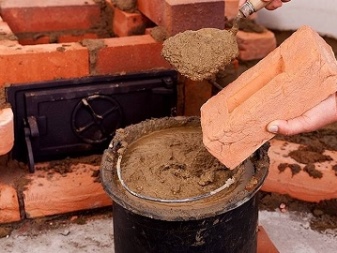
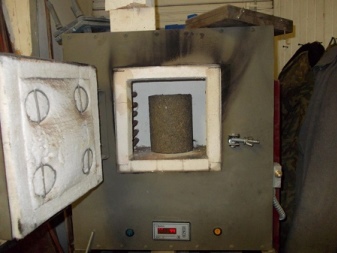
To obtain a product according to the specified dimensional and volumetric parameters, during molding, it is necessary to take into account the percentage of shrinkage and increase the parameters of the blank. The shrinkage process in fireclay clay begins to occur already at a temperature of 600 ° C, it takes a rather long time. This uniform process takes place until the temperature does not rise to 1000 ° C. After this milestone, shrinkage is most intense and continues up to a temperature of 1300-1400 ° C, after reaching this mark, shrinkage stops.
- Sintering temperature - this is an indicator of the temperature regime, under the action of which the clay mixture loses its ability to absorb moisture, that is, it cakes. Refractory chamotte composition and all products made from it are sintered without melting and deformation, without losing the ability to refractoriness.
- Refractoriness - this term is understood as the property of a clay mixture not to melt under the influence of temperature conditions within 1580 ° C. Such fire resistance in clay is achieved due to the small percentage of impurities contained in it. This type of clay is used in the manufacture of refractory products, including earthenware or porcelain.
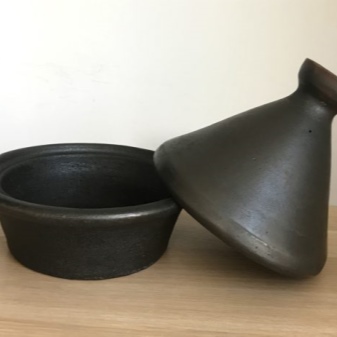
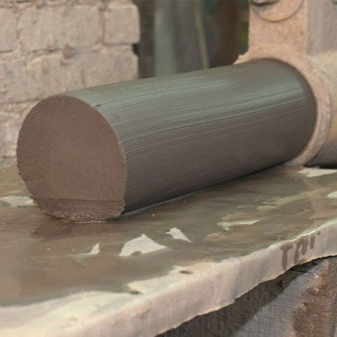
Due to its refractory qualities, clay is most often in demand for laying furnaces. In addition, refractory bricks are made from this material, which is necessary for laying out the furnace from the inside, that is, for forming a firebox. The same clay is also used as a masonry mortar, as it has a good adhesive ability to surfaces. In addition to the use of chamotte clay in the furnace business, it is also used for coating in the form of refractory masses and mortars. For these purposes, the brands PHB or PHA are used.
Today, refractory clay is used to produce ceramic facing tiles, tiles for finishing furnaces, crucibles for melting precious metals, porcelain products, and faience.
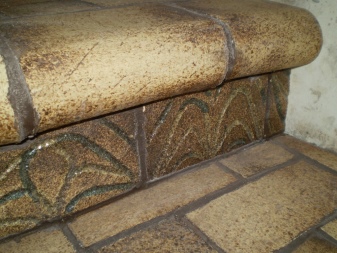
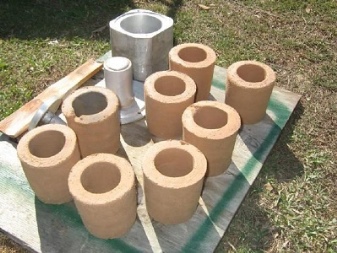
Description of species
Refractory chamotte is a component on the basis of which solutions can be prepared for various purposes. Clay is subdivided into lumpy and ground. The lumpy variety is used for the manufacture of clinker, ceramic and heat-resistant products, and chamotte powder is used for the preparation of working solutions used for coating or plastering surfaces. In addition, rammed and molded mixtures are prepared from the powder.
Kaolin clay is also subdivided according to its composition, depending on the proportion of chamotte sand. For the preparation of solutions use:
- binder type of clay with a content of 55% sand;
- smooth type, where the sand can be from 20 to 48%;
- depleted type with a sand content of not more than 21%.
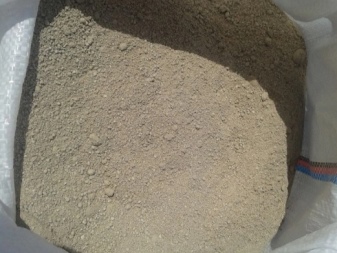
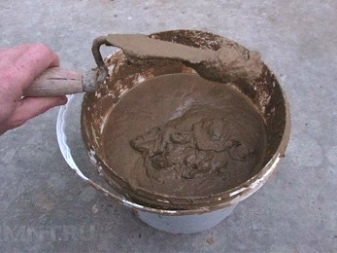
Depending on the content of aluminum oxides, the chamotte composition is subdivided into the following types:
- highly basic - no more than 40%;
- the main one - from 25 to 37%;
- semi-sour - no more than 27%.
In addition, chamotte clay powder is also subdivided into grades. There are 4 grades in total, depending on the composition of impurities and the degree of fire resistance:
- special;
- I grade;
- II grade;
- III grade.
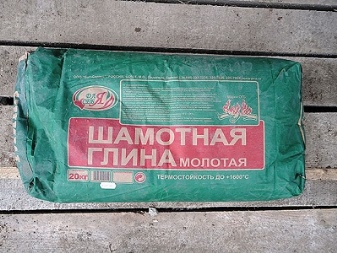
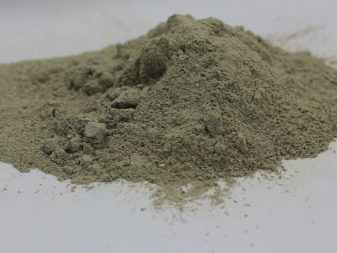
What is chamotte used for?
In the form of a dry mixture, fireclay clay is used for the preparation of working masonry or plaster mortars, and also refractory bricks are made from it. Chamotte clay is an indispensable product in cases where the garden needs a fire bowl, a stove for heating a house, a tandoor for cooking, a crucible for burning materials.
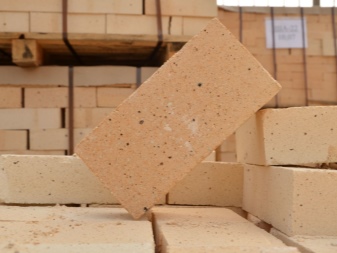
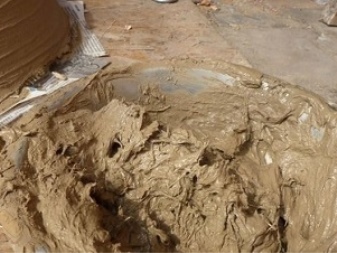
Masonry ovens
To perform furnace work, when prefabricated elements are installed when laying a stove, barbecue or fireplace, not only special refractory bricks are used, but also a fireclay mixture obtained from clay. For work, you will need to purchase dry clay marked "Ш", which means "fireclay".
Since refractory bricks are expensive, they are mainly used for arranging the inner furnace of the furnace, and the outer part of the furnace structure is assembled from red clay bricks. In order to reliably connect all elements of the masonry with each other, bricks must be laid on fire-resistant fireclay clay, which has an expansion coefficient equal to that of bricks when heated.
As a rule, on average, for laying 100-110 bricks, you will need to prepare at least 3 buckets of fireclay mortar.
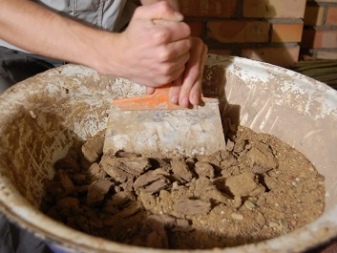
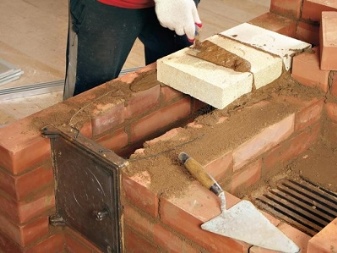
Plaster
In addition to mixtures for making brickwork, plaster compositions for finishing wall surfaces or as an adhesive for facing with a finishing material are also made from chamotte. Fireclay plaster is an excellent option for adding reliability to the masonry when arranging stoves. Such a composition is used to treat those parts of the furnace that have access to other rooms. This approach reduces the heating of the wall surfaces and creates a barrier for heated air. The thickness of such a plaster finish should not exceed 1.2 cm.
All types of work with fireclay mixtures are performed using a spatula. Simplifies the process of using serpyanka tape. After completing the masonry or plastering process, you will need to wait for the solution to set and dry.
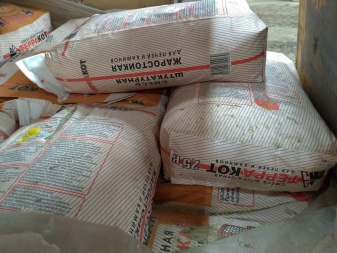
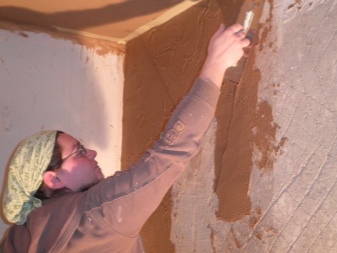
Other uses
Modern designers often use fireclay clay not only for arranging heat-resistant structures, but also for creating aesthetically attractive decorative items. It can be ceramics, tiles, flower pots, flowerpots, dishes, tiles, outdoor flowerpots. Chamotte is used to sculpt figurines, figurines, souvenirs. The versatile applicability of chamotte clay is explained by its attractive texture, as well as its high strength and fire resistance.
Fireclay is a pliable and flexible material that is pleasant to work with. Products made from it always look original and can be harmoniously combined with any design style. In the composition of chamotte, there are no impurities harmful to humans, so you can work with it not only for adults, but also for children. After the product is formed, it is sent to the kiln for firing, during which all geometric proportions remain unchanged for the product.
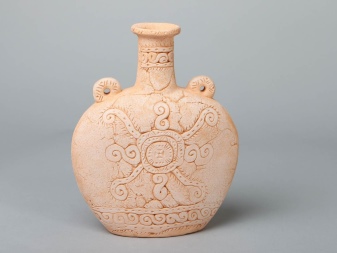

How to work with chamotte clay?
To use chamotte clay powder, you will need to prepare a working solution. Its positive property is that the mixture does not crack when it dries. For example, to make a plaster composition, you should proceed as follows.
- They take chamotte sand, Portland cement and ordinary sand from the quarry in proportions of 7: 1: 2. In order to increase the strength of the finished composition, salt can be added to the mixture at the rate of 100 g per 8 liters of solution.
- Loose fractions must be gradually diluted with water, while stirring so that all components are evenly distributed among themselves. Water is added in small portions so that the consistency of the composition can be controlled. The consistency of thick sour cream is considered the most convenient for work.
- Before starting the plastering work, the surface is cleaned, and then covered with a solution of refractory putty, on which the construction mesh is laid. Further, on top of this layer, another layer of solution is applied. The surface is leveled and allowed to harden completely.
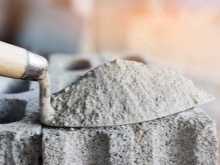
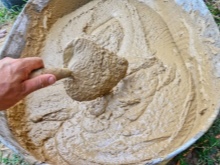
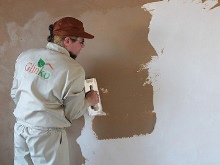
Experts believe that only fireclay sand cannot be used to perform furnace or finishing work, since the working plaster composition will have poor plasticity. Kaolin or clay must be added to the mixture. The ratio of ingredients of sand and clay is taken in a ratio of 2: 1 or 4: 1.
To create a fire-resistant mixture, ordinary river or quarry sand cannot be used, since under the influence of high temperatures it tends to expand, and the masonry or plaster lining in this case will begin to crack and collapse. The addition of Portland cement to the chamotte mixture increases the strength of the mixture, but because of this additive, its refractory properties are reduced - the composition can withstand heating only up to 800 ° C. Sometimes fiberglass is added to chamotte clay, this step also increases the strength of the masonry.
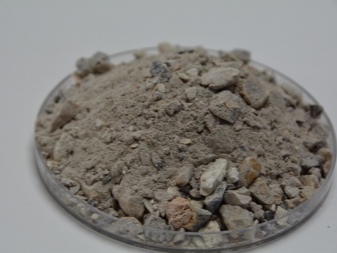
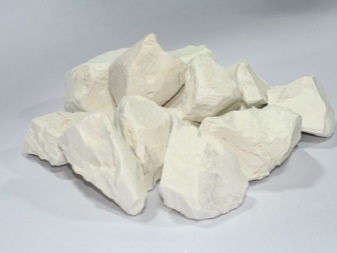
The comment was sent successfully.