Refractory bricks: characteristics and varieties
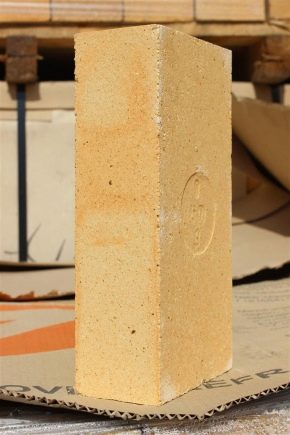
Ordinary brick is not suitable for the construction of all structures and structures. So, for the manufacture of stoves or fireplaces, as well as industrial facilities, it is customary to use not standard, but special refractory material, which is not afraid of high temperatures.
Today we will take a closer look at these building materials and find out what characteristics they have.
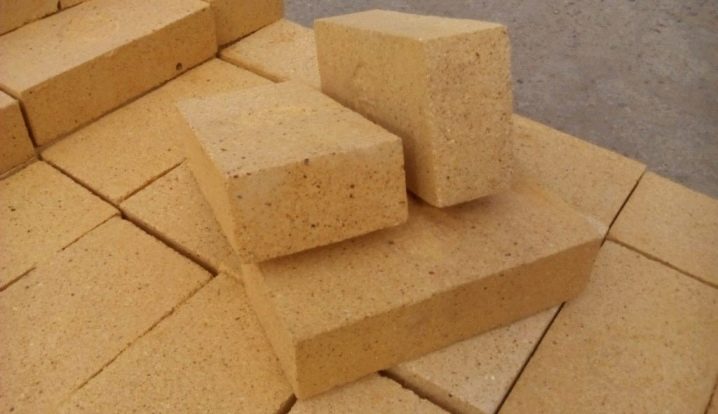
Features and composition
Brick is one of the most popular and common building materials with many positive qualities. Pretty brick houses are found on almost every street, so the demand for such products is beyond doubt.
It is important to keep in mind that standard types of bricks are not suitable for all jobs.
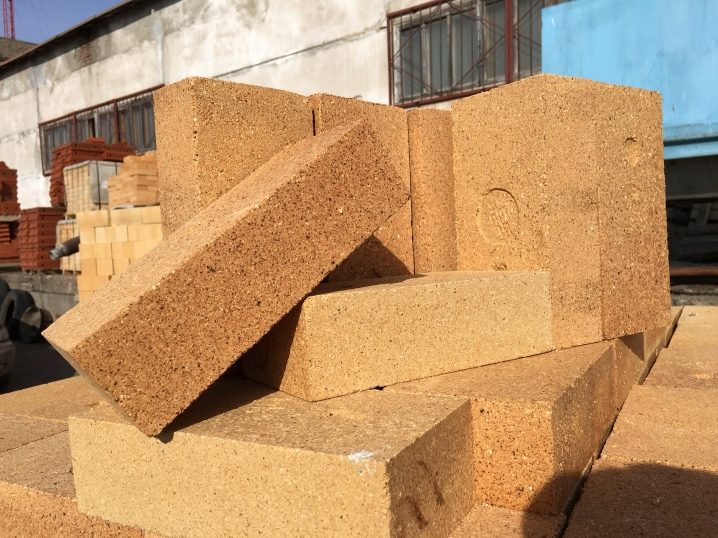
Under high temperature conditions, traditional brick can quickly deteriorate and deform / collapse. Here it is customary to turn to a more practical and wear-resistant refractory material, which in such circumstances will not lose its positive properties. Fortunately, nowadays you can find such products in many retail outlets.
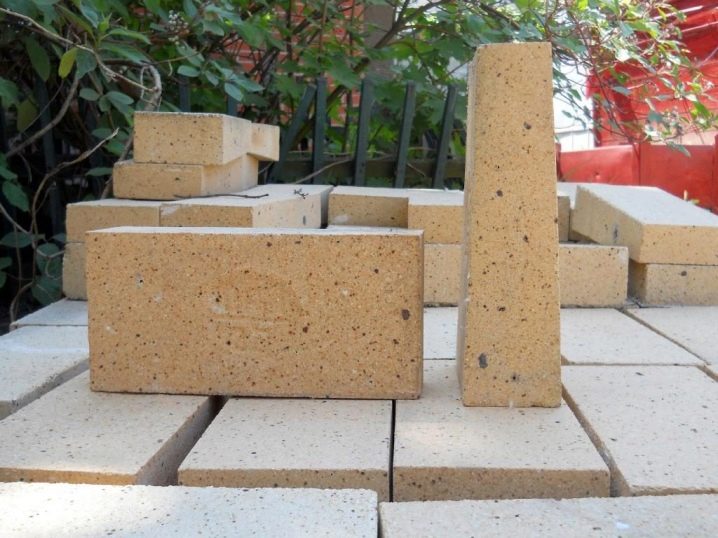
Heat-resistant brick is an ideal solution for the design of bases that insulate an open flame. In addition, these resistant materials are used when it is required to finish the inner walls of household stoves, channels of chimneys, fireplaces or pipes. The work of laying this brick (lining) is usually done by experienced craftsmen.
Many technical characteristics of refractory bricks are very different from those of ceramic or silicate stones. The main ingredient in these building materials is clay. The remaining components in the composition of such products are various impurities and specialized additives. However, all additions to the composition of these materials are characterized by the fact that they retain their positive qualities even under the regular action of high temperature values.
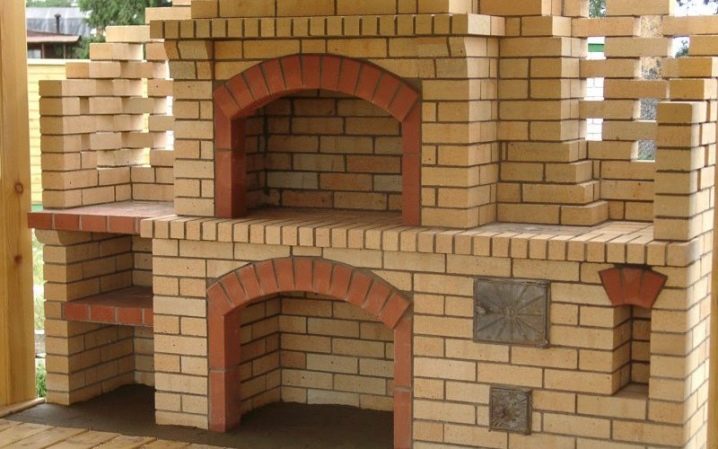
High-quality refractory bricks are very often used in industrial production. For this reason, this building material must necessarily meet a number of relevant requirements for its quality.
When choosing a suitable refractory brick, it is very important to ensure that there are not even the slightest defects or damage on its surface. Such shortcomings can lead to bad consequences, for example, to a malfunction of a particular design. Usually, this fact provokes unnecessary spending.
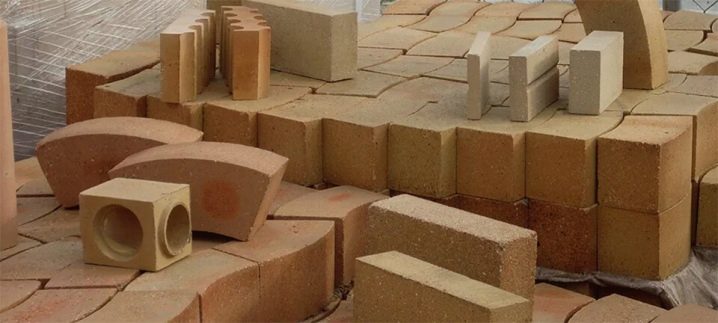
The main features and properties that these reliable materials have are the following parameters.
- These products are characterized by low thermal conductivity. Due to this quality, the required temperature regime is always maintained inside the heating equipment.
- Such a brick is not afraid of contact with high temperatures. Even under the influence of intense heat, such materials do not lose their positive qualities and do not fail.
- Also, these bricks are distinguished by the presence of thermal inertia. It heats up in the shortest possible time, and cools down rather slowly.
- Refractory bricks are characterized by optimal heat capacity, which is sufficient for the accumulation of heat energy and its further transfer.
- Heat-resistant brick is not afraid of hot gas, metals or slags. Not every building material can boast of such properties.
- The volumetric parameters of such products remain unchanged. They are not subject to shrinkage or additional growth.
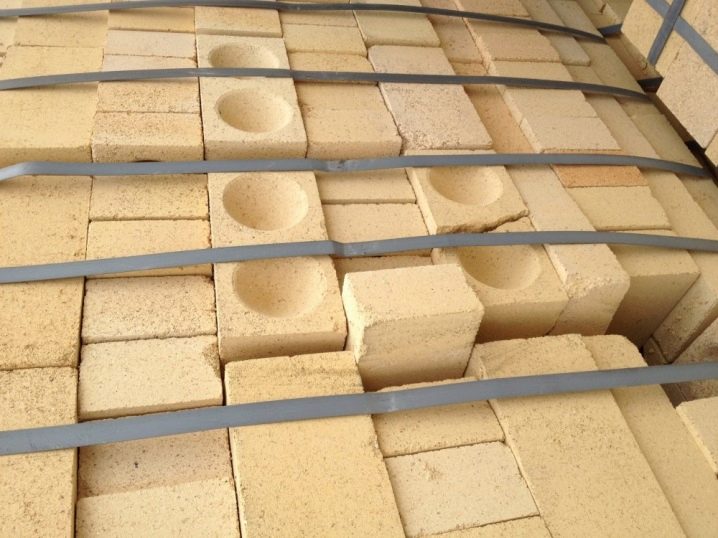
Similar materials are made in accordance with GOST and regulatory documents. As mentioned earlier, the composition of these products is based on a special kind of refractory clay. It usually takes up about 70% of the total brick volume.
In order to obtain blocks with different technical characteristics in the molding mass, some types of additives are used, such as:
- fine coke;
- graphite;
- coarse quartz powder.
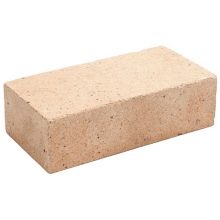
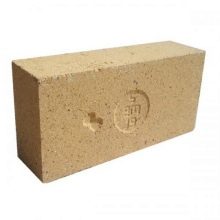
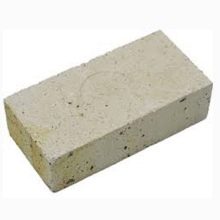
Refractory bricks are produced using the semi-dry pressing method. At the same time, the necessary raw materials are first prepared, the clay is thoroughly crushed and kneaded. Next, the charge is introduced. The composition is brought to a homogeneous consistency. At this time, water is added to it (no more than 10%). This component is necessary for the solution to acquire the proper moisture level.
The harvested mass is transferred to a special hopper. After that, the composition is sent to the dispenser moving back and forth. When the parts are formed, they usually go straight to the bottom punch of the mold, which goes down with the workpiece. After that, the upper half of the press is lowered onto the bricks. The pressure is applied to the food to make it denser.
The lower punch, at the end of production work, squeezes the brick out of the mold. At this time, the carriage with the dispenser moves for firing at a temperature of 1000 degrees. If the bricks are produced in accordance with this technology, then they do not need to be dried, so they take less time to prepare them. In addition, the described method is much cheaper than plastic molding.
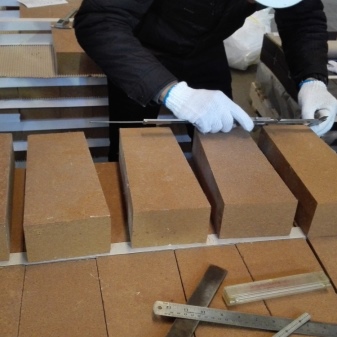
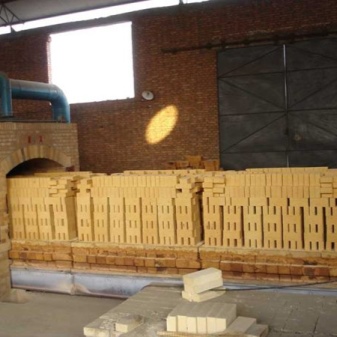
Advantages and disadvantages
Refractory bricks, like other building materials, have both positive and negative sides.
First, you should familiarize yourself with the positive:
- in most cases, such products are lightweight, so it is convenient to work with them;
- are highly durable - they are very difficult to damage or break;
- able to withstand very high temperatures;
- differ in heat capacity and thermal inertia;
- can have different shapes and sizes;
- tolerate temperature changes without consequences;
- are not afraid of negative external factors;
- have an attractive appearance and different colors, for example, white or red (the most popular options).
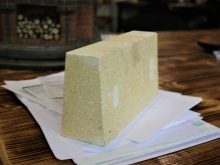
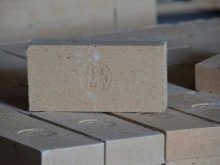
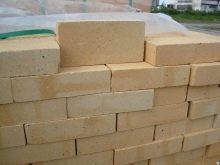
Now it's worth familiarizing yourself with the disadvantages of these products:
- they are rather difficult to cut and sawn, because they are characterized by increased strength;
- have a higher cost than standard products.
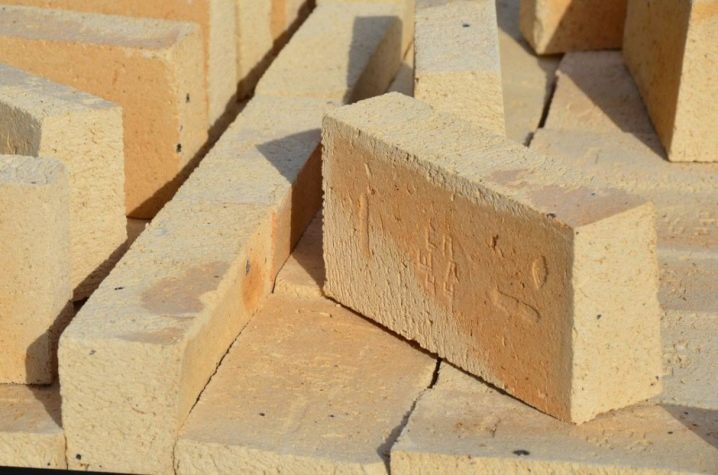
Specifications
Modern heat-resistant brick has its own technical characteristics, which you must definitely familiarize yourself with if you are going to work with this building material.
Consider a list of the main characteristics inherent in such bricks.
- Low level of thermal conductivity - thanks to this type of brick, it will be possible to maintain the required temperature in the interior of the heating units.
- Heat resistance is the main technical characteristic and distinctive feature of this building material. Heat-resistant bricks are able to withstand temperatures exceeding 1500 degrees.
- Modern refractory bricks are not afraid of aggressive chemicals.
- Similar products leave factories with the following dimensions: 23 x 6.5 x 6.5 cm, 230 x 114 x 75 mm, 230 x 114 x 40 mm, 250 x 124 x 65 mm and 345 x 150 x 75 mm. Deviations from the listed dimensional parameters are permissible, but very small. For example, the thickness of a brick may differ by no more than 2 mm, length - up to 5 mm, width - up to 3 mm.
- The thermal conductivity of such building materials is quite low.

Views
Do not think that heat-resistant brick has no subspecies. Today, you can find several types of similar products on sale.Let's take a closer look at the most popular and demanded products and their properties.
The basic varieties of this material include the following options.
- Main brick... Materials with this name are used in tandem with a lime-magnesia solution. Used in steel production.
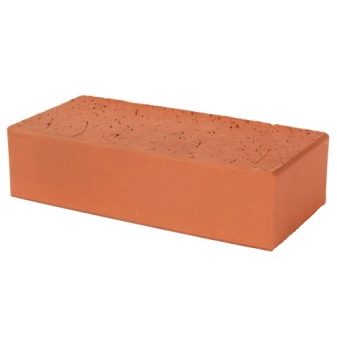
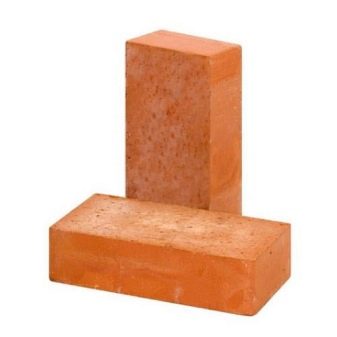
- Carbonaceous... Material of this type most often acts as the base of domain structures.
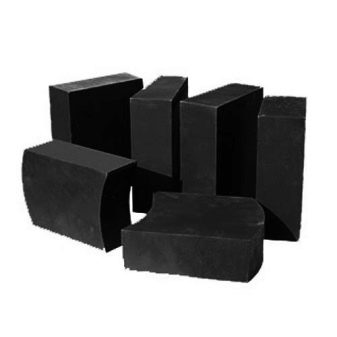
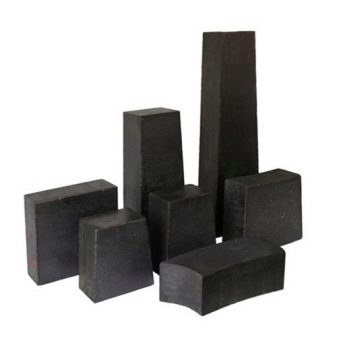
- Quartz... These options contain components such as quartz and sandstone. The specified stone is not designed to be adjacent to other building materials. Exceptions to this rule are metal, fire. Any alkali has an extremely negative effect on quartz brick.
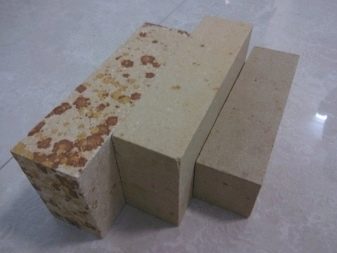
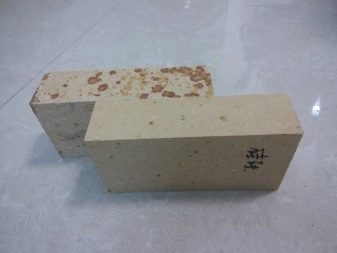
- Alumina... This brick is considered the most common. It can withstand temperatures from 1000 to 1300 degrees. Alumina blocks are renowned for their ability to withstand the effects of temperature fluctuations without problems. Often, these raw materials are used in the manufacture of stoves (both domestic and industrial) and combustion chambers.
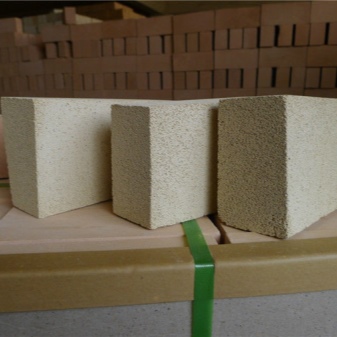
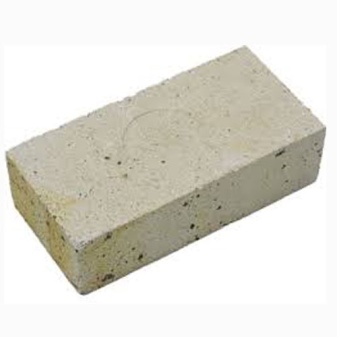
- Klinovoy... The specified brick is usually produced with dimensions of 300x300x300 mm. Often this building material is used in the manufacture of industrial structures. It bears the ShTsU marking.
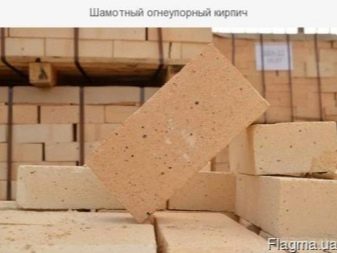
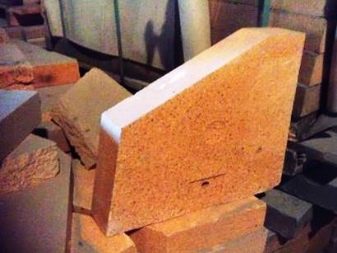
- Semi-acidic... The specified brick is produced with PB marking. Its fire resistance is limited to 1670 degrees Celsius. As for the porosity of the semi-acidic material, it is 24%. The content of additional components in these products varies from 14 to 28%.
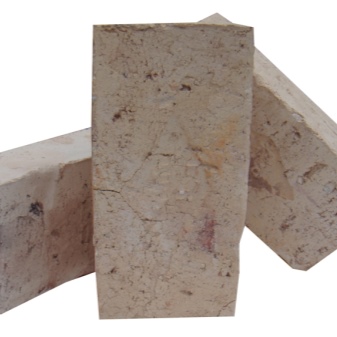
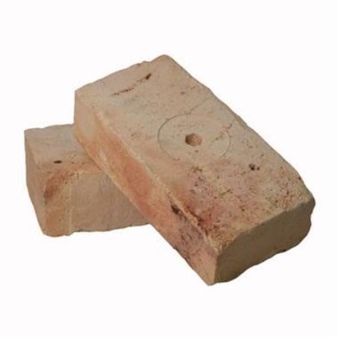
- Magnesite... Magnesite bricks boast excellent refractory properties. During their production, such a component as magnesite is fired at high temperatures (1500-1600 degrees). As a result of such processing, very strong and heat-resistant products are obtained, which are permissible to be used in the industry.
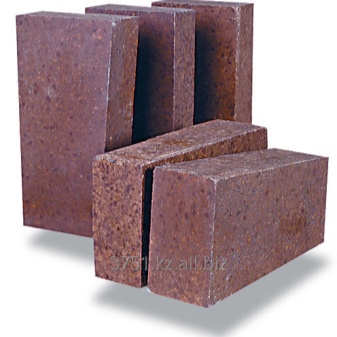
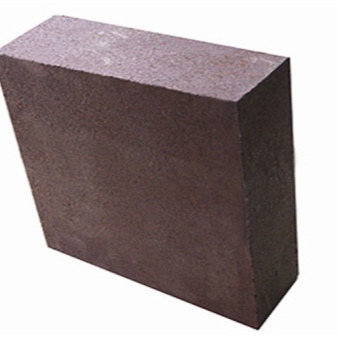
- Lightweight... Lightweight brick is no less popular nowadays. This wear-resistant and durable material easily transfers the effects of aggressive chemicals and is lightweight. Basically, such light raw materials are used for the manufacture of evaporators, steam vents, boilers and other devices. It is easy and convenient to work with it, because it weighs very little, especially in comparison with analogues.
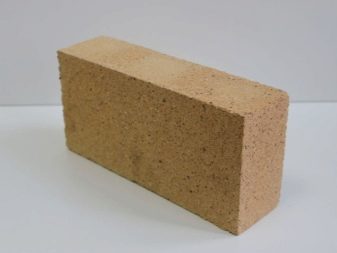
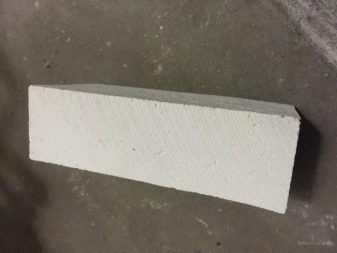
In addition to those listed, there are other subspecies of wear-resistant refractory bricks, for example:
- siliceous;
- aluminum silicate;
- mullite;
- dinas;
- corundum and others.
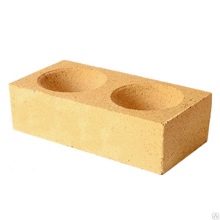
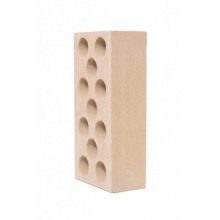
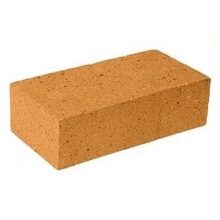
Popular brands
All refractory bricks are marked according to their properties and composition. So, the first letter in the brand designates the name and a certain type of product. If this is the letter "Ш", then the stone is chamotte, if "D" - dinas, and if "M" - mullite.
As for the second letter in the marking of heat-resistant building materials, it is designed to demonstrate the highest temperature for which the stone is designed. For example, the most popular are the following products:
- SHA, SHAK 1400;
- SB 1350;
- SHUS, SHV 1250;
- PB (semi-sour species) 1250;
- PV 1250.
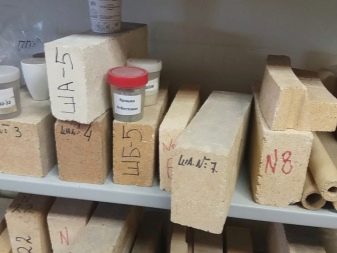
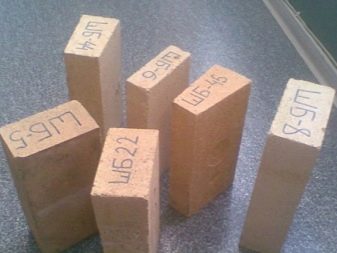
The dimensional parameters of heat-resistant bricks are recognized by a digital designation that precedes the first two letter designations of the product brand. For example, the product SHA 5 is produced with dimensions of 230x114x65 mm, and products marked with SHA 8 have dimensions of 250x124x65 mm.
There are also products marked ШБ 22, which have a trapezoidal shape. Their dimensional parameters reach 230x114x65x55 mm. After the numerical designations in the marking, there are letter designations that represent the abbreviation of the plant that manufactured the product.
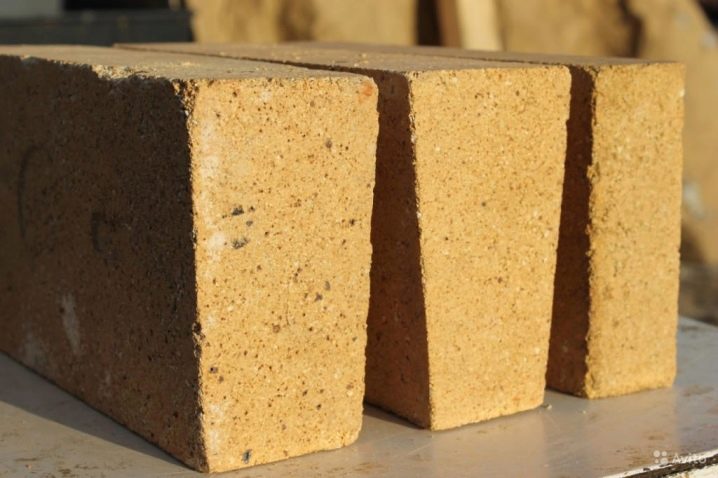
How to choose?
The choice of refractory bricks should be approached especially responsibly, because very important tasks are assigned to it. This building material must coexist seamlessly side by side with high temperatures and sometimes open flames.
When choosing refractory bricks, it is necessary to rely on the following important criteria.
- Size, weight... It is imperative to select quality materials of suitable sizes. It is advisable to calculate the amount of materials you will need before buying. It is better to purchase them with a small margin, so as not to face a shortage of building materials.
- Brand... On the packaging with bricks, the brand to which they belong is always indicated. This mark cannot be ignored, since it will depend on it whether the material is suitable for certain works or not.
- Brick quality... One of the most important positions is occupied by the quality of fire-resistant bricks. In no case should there be any defects on it, otherwise the structure from this building material will not turn out to be the most reliable and strong, which can lead to very sad consequences.
- Number of pores... Refractory bricks should not have too many pores in the structure. This can increase the hygroscopicity of the blocks, which is undesirable for ovens. Due to the impressive hygroscopicity, the stone can undergo crumbling and deformation, and with this the entire structure will collapse.
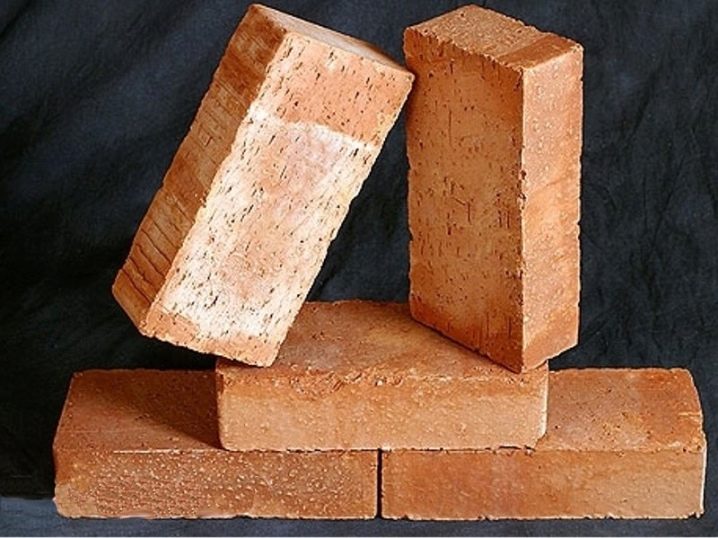
- Surface... Take a closer look at the surface of the fire-resistant brick. There should be no noticeable reflection on it. If one is still visible, then this will indicate that the workpieces were overheated during the manufacturing process.
- Sound... Not every consumer knows that the quality of a brick can be determined by the sound that comes from it when struck. To check the condition of the material, tap it lightly, for example with an iron object. The sound from the brick should come out clear and sonorous. If he is deaf, then it is better to refuse to buy such building material.
- Colour... It is important to take into account the fact that its quality does not depend on the color of the heat-resistant brick. The building material can have almost any shade, for example, beige, yellow, red or beige. All that is required of you is to purchase a batch in which all the bricks will have the same color. If in a laid row at least 1 piece turns out to be of a different color, then it will stand out sharply against the general background.
- Trade point... Experts strongly recommend buying refractory bricks only in trusted retail outlets that have a good reputation in the city of your residence.
It is advisable to ask the seller for quality certificates for the selected products. If you were denied the presentation of documents, then it is better to refuse to buy a brick - it may turn out to be of low quality.
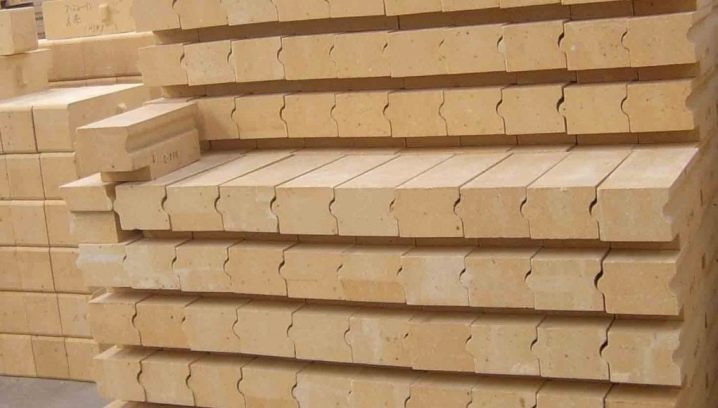
How to cut?
Many users are wondering how it is possible to effectively cut refractory bricks. And this question is very relevant, because this material is highly durable and not the most pliable in cutting.
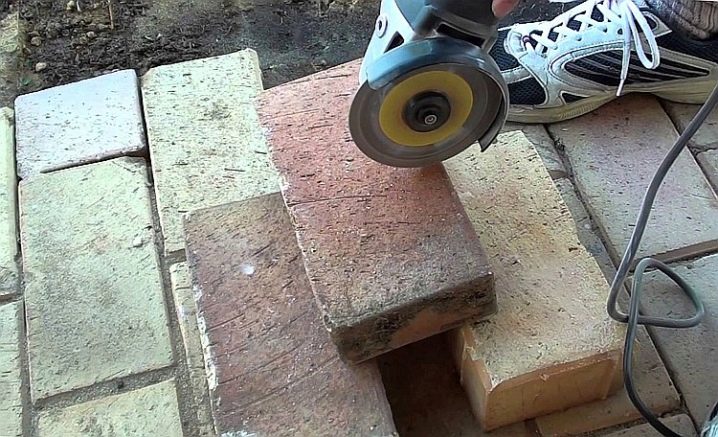
For example, common heat-resistant fireclay bricks are usually cut using a specialized machine.
It is also permissible to turn to a grinder with a segmented diamond disc installed on it. However, this tool does not have a coolant supply function.
The problem can be solved by placing the bricks in a tank filled with water in advance for about 20 minutes. After such a procedure, they will be easy to process, as if a tool with a fluid supply was used.
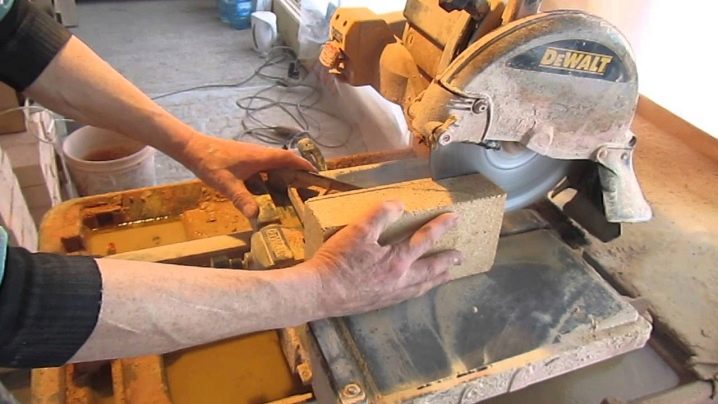
Useful Tips
Use only high quality refractory bricks with ideal dimensions. The accuracy of the shapes and sizes of these products is regulated by GOST 8691-73. Please note that only minimal deviations from the standard are allowed.
Keep in mind that heat-resistant carbon bricks and refractory metal options are not commonly used in conventional domestic stoves, combustion chamber linings, or reinforcement structures. Such varieties are usually used only when it comes to industrial facilities.
If you are facing a fireplace or stove in the house with refractory bricks, then you should pay attention to the condition of the old joints.If they are dry, then they will need to be finalized, otherwise the finish may subsequently move away from the base.
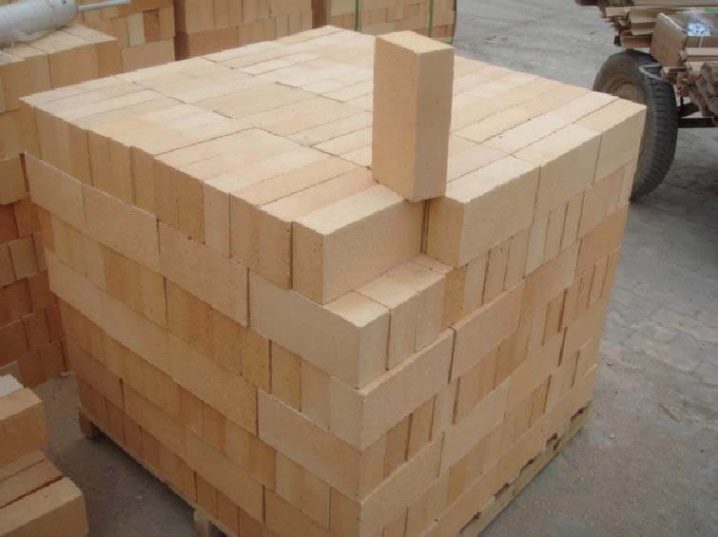
Remember - when falling, high-quality refractory bricks should not crumble. It should break up into fairly large pieces.
It is not recommended to use materials with a white coating on the surface - these are limestone deposits. Materials with such defects should not be used in construction work.
Do not confuse fireclay and oven bricks. Stove options are made from red clay. They are not fireproof.
You will learn more about refractory bricks suitable for laying stoves or fireplaces in the video below.
The comment was sent successfully.