Fiber concrete: what is it and where is it used?
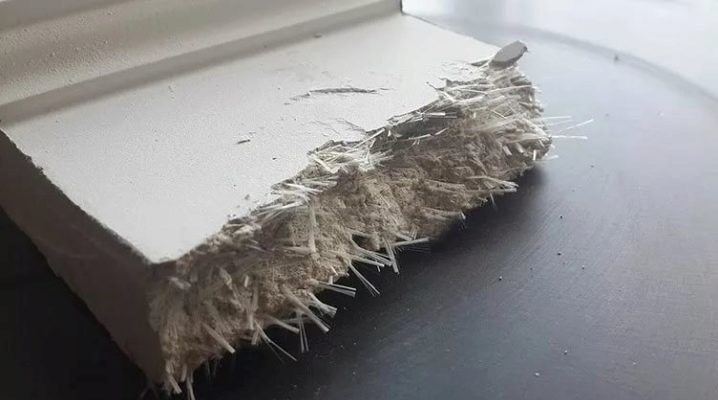
Technological progress abundantly supplies people with more and more new materials for construction work. Among the relatively recent developments of this kind, it is worth noting fiber concrete. It is useful to know the features of this material even for those who are not going to use it - just for general development.
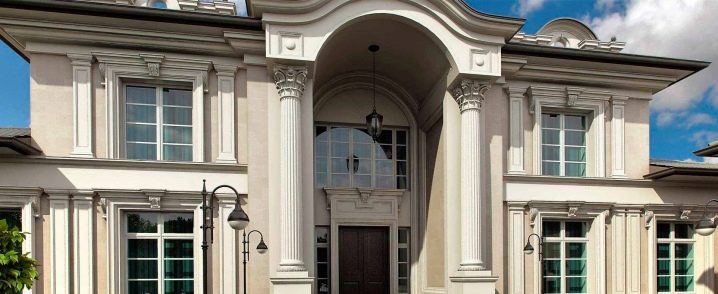
Description
Fiber-reinforced concrete is a subtype of concrete that is reinforced over the entire area using metallic and non-metallic inclusions. To strengthen the material, steel wire and fibers of carbon, polyamide, glass, acrylic, polyester, viscose, nylon, and basalt are actively used. The strongest fiber made of steel turned out to be more in demand than others, which is obtained by cutting wire with a cross section of 0.1–0.5 mm into sections from 10 to 50 mm. Fiberglass is only slightly inferior to it, which is popular due to its significant technical qualities. The use of other synthetic materials helps to make the technological process more economical and give the material a variety of characteristics.
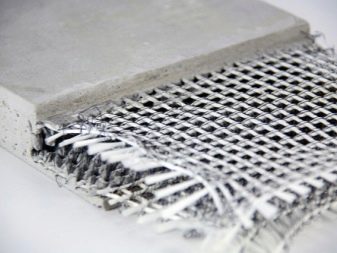
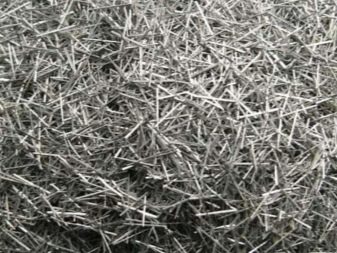
Fiber-reinforced concrete compared to conventional concrete:
- better resistance to stretching and tearing;
- has a higher elasticity;
- does not sit down;
- more resistant to cracking;
- resistant to cold;
- immune to toxins and atmospheric elements;
- little abrasion.
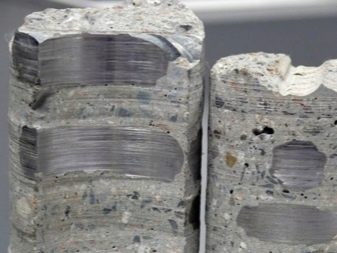
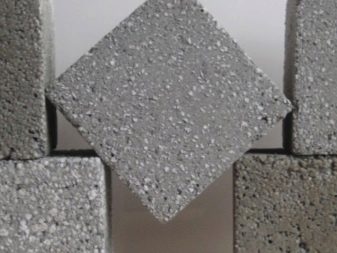
At the same time, the strength and plasticity of the material are also at a decent level. If the solidified layer is cut, a homogeneous structure will be visible, which is penetrated throughout its thickness by thin threads going in an arbitrary direction.
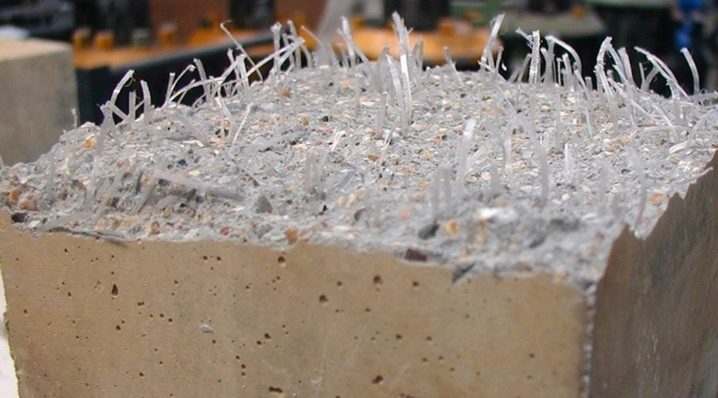
Experts can confidently say, seeing the features of inclusions, what are the properties of the sample and how exactly it was obtained.
In addition to technological nuances, there are generally accepted conditions, such as:
- the compatibility of the original concrete with the fiber used;
- strictly specified proportion between them;
- uniform dispersion of fibers in the mass.
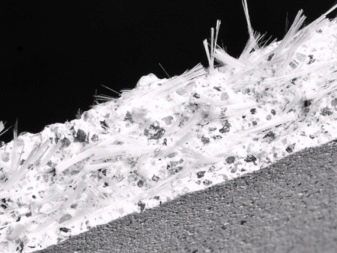
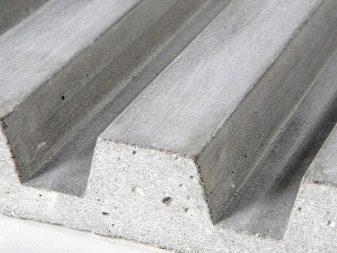
Appointment
Fiber-reinforced concrete products are used in a wide variety of areas. It finds application in the foundations of skyscrapers, and in road construction, and in the construction of hydraulic structures. If fiberglass is added, the material can be used for noise control, water purification and facade decoration.
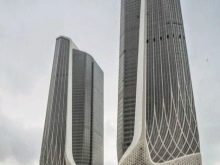

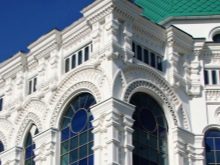
Even the most mechanically loaded structures using fiber-reinforced concrete will work 10–20 times longer than ordinary cast stone.
Cornices occupy an important place among the architectural decorative elements made of the material under consideration.
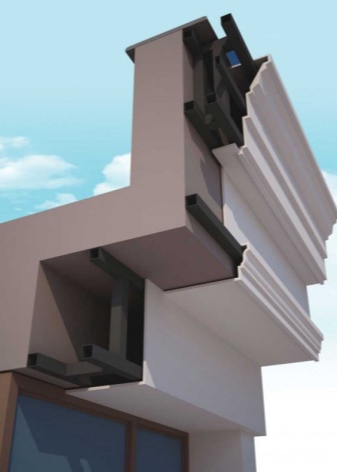
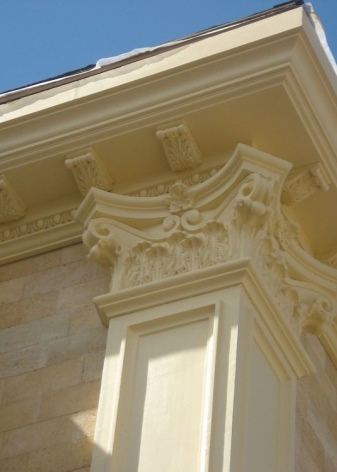
To obtain them, a variety based on fiberglass is used. Experts select the technology and determine the nuances, taking into account the height of the structure and its distance from the wall. Sometimes the cornice is divided into several blocks with different heights, if the removal is large, the installation is carried out on a subsystem of metal elements. The walls are made from 2 to 4 cm in thickness, and the length of a single element can be 70–100 cm. For the installation of cornices, parts made of ferrous metals, galvanized or stainless steel are often used.
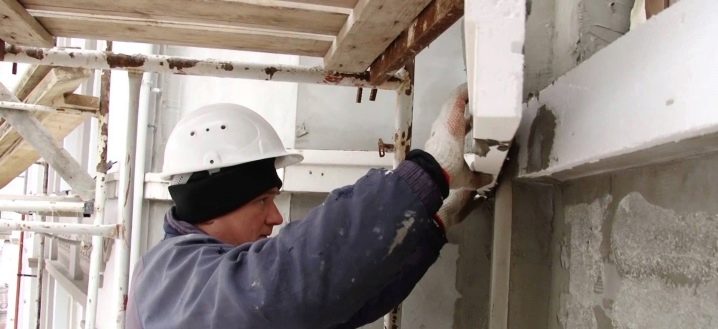
For fastening the cornices, a through, hidden or mixed method is used. Fiber-reinforced concrete columns are an excellent solution for those who want to take care not only of the appearance of the facade, but also of the interior of the room. The main part of the columns takes a noticeable share of the load, reducing the pressure exerted on other elements of the buildings.Therefore, in addition to purely design advantages, these details allow the construction of massive buildings. They also indirectly affect the perception of facades, reducing the likelihood of cracking.
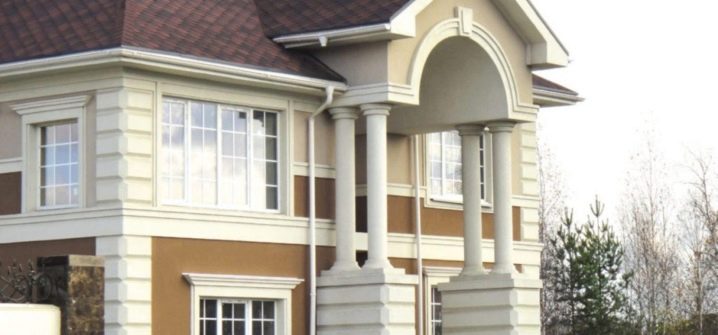
Views
To correctly apply fiber-reinforced concrete, you need to thoroughly understand the features of its individual types. The earliest examples of this material were obtained before the First World War. At that time, there was still no special variety of synthetic materials, and therefore the experiments of materials scientists took place with cut wire. Fiber today is standardized by the requirements of the state standard. The steel filling is divided into anchor and wave groups, the ends of the segments in these two cases must be bent.

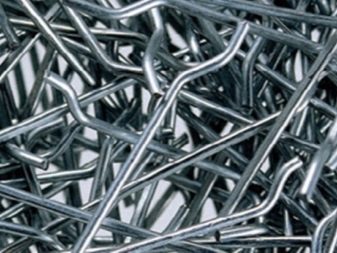
To obtain metal fiber for the frame, the raw material is most often processed purely mechanically, on drawing machines, rolling mills or cutting equipment. The technology is chosen depending on the fiber diameter to be obtained. Extremely fine filaments are made by passing steel through holes in diamond parts.
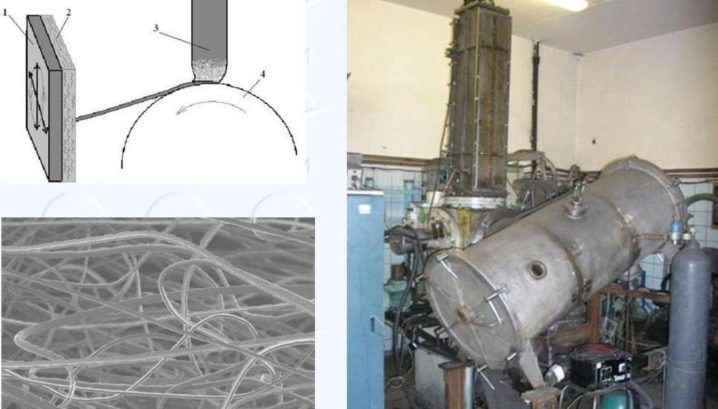
Steel fiber is good in strength, but it is heavy. Due to its high tendency to corrosion, such a material is almost unsuitable for the facade.
Mineral fiber is obtained from molten volcanic rocks, usually basalt. The properties of the raw material affect the characteristics of the material; it is resistant to mechanical stress, to contact with alkalis and acids. Basalt fiber does not catch fire and makes the concrete in which it is added three times stronger than conventional mortar.
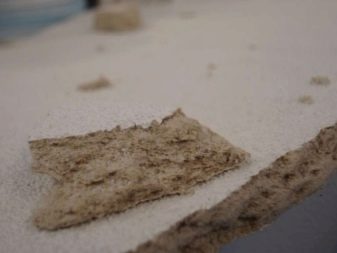
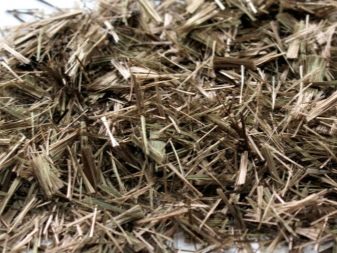
Additives made on the basis of such a mixture are used for a variety of purposes:
- fixed formwork;
- wall panels;
- small architectural forms;
- preparation of fountains;
- production of parts for the reconstruction of houses;
- stucco moldings in the cornices;
- slabs in road construction.
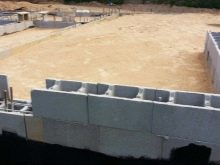
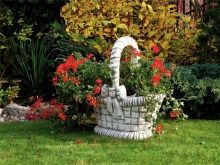
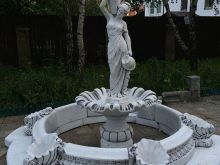
Fiberglass concrete is produced by pulling the molten mass of glass using special equipment. Since glass is quite different in composition and can be flexibly varied, designers can achieve impressive mechanical performance. Dispersed reinforcement is assembled into bundles of a given diameter. Carbon fiber is made by processing raw materials with significant heating. Such material has a number of excellent characteristics:
- resistance to mechanical stress;
- immunity to aggressive chemical factors;
- low elongation when heated;
- no risk of corrosion and amazing adhesion;
- incombustibility.
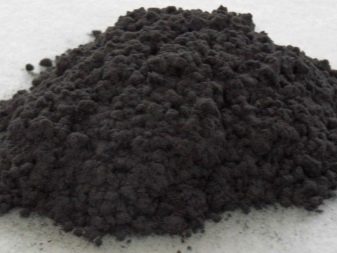
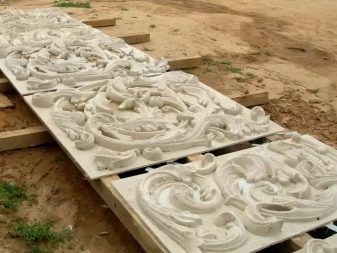
The problem with carbon filament is only related to its high price. Polypropylene fiber concrete exceeds any sample without reinforcement in terms of shock resistance. But at the same time stretching and compression is tolerated much worse. Also, polypropylene is not resistant enough at high temperatures, and there is a great risk of purchasing frankly low-quality raw materials. The fact is that the range of characteristics of the material is huge, and a professional cannot distinguish a standard product from waste by eye.
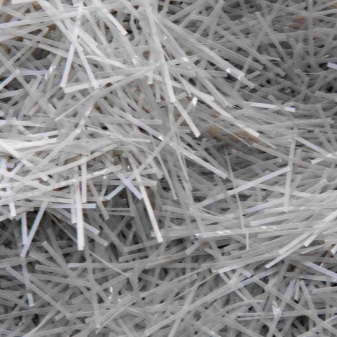
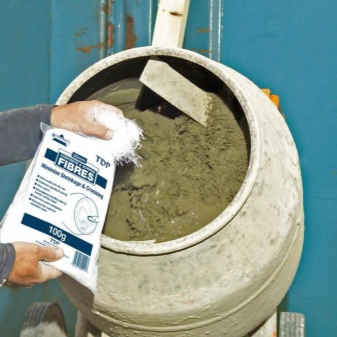
Specifications
Russian GOST provides for the production of various types of fiber-reinforced concrete. The chemical and fractional composition of the mixture directly affects its practical parameters. Thus, the addition of fiberglass provides:
- specific gravity from 1700 to 2250 kg per 1 cu. m;
- thermal conductivity not lower than 0.52 and not higher than 0.75 W / cm2 x ° С;
- bending tensile strength - 210-320 kg per 1 sq. cm.
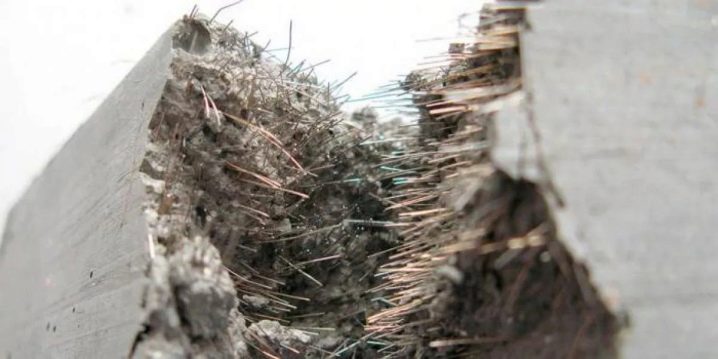
These properties make it possible to reduce the thickness of the manufactured structures and significantly reduce its weight. And the combination of reduced load and environmental friendliness significantly expands the application area of the products. Fiber concrete is most popular where a minimum risk of cracking and excellent impact resistance is required. It is difficult to find a better solution for flooring. The light weight of fiber-reinforced concrete blocks simplifies their use for finishing buildings with decorative elements of various types.
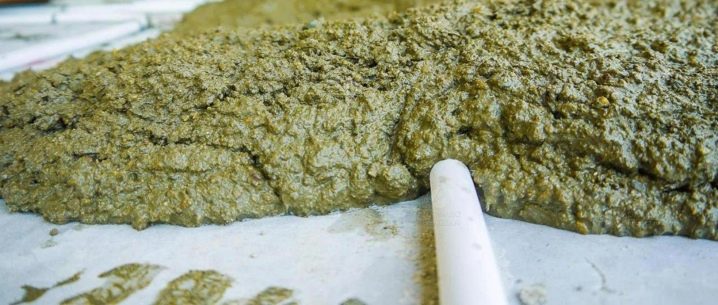
The proportions of the polystyrene-based mixture depend on the required density. So, if it is 200 kg per 1 cu. m, you will need 100 liters, 200 kg of the cement itself and 0.84 cubic meters. m of crumbled polystyrene. The amount of crumb will not change with increasing density, only additional water and a binder are added. The resulting mixture is perfect for pouring the floor, and for use inside the formwork.
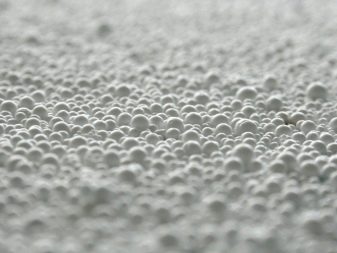
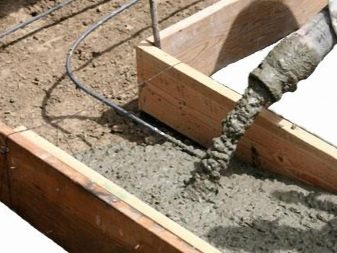
You can learn more about the production process of fiber-reinforced concrete products by watching the following video.
Manufacturers overview
The production of fiber-reinforced concrete is established in Russia at a fairly high level. There is no compelling reason to prefer imported products. An excellent result is brought by the use of mixtures of the brand "3DBeton", also experts recommend focusing on brands ROSPAN and LTM. Thanks to modern equipment and the latest technological methods, it is possible to meet the bar that Japanese concerns set in the world market. The choice between manufacturers can be made based on just logistics, because no practical difference can be found between their products.
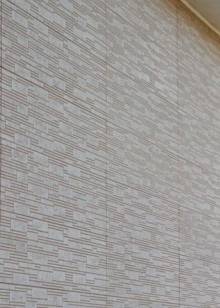
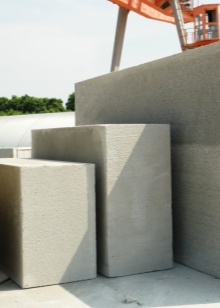
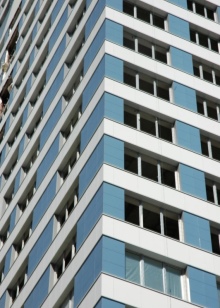
How to choose?
The species composition and concentration of the added fiber will be much more important than the inscriptions on the label. So, if you want to achieve the highest strength, it is recommended to buy concrete, where a metal fiber was introduced in a mixture with fiberglass. Then it will be possible to restrict ourselves to the minimum possible thickness of the walls, which means that the foundation work can be facilitated and the cost reduced. The described recipe also allows fiber-reinforced concrete:
- stay strong under breaking load;
- preserve their valuable qualities under the influence of various substances and weather conditions;
- not to lose usefulness at high air temperatures and with strong heating of the stone itself;
- repeatedly survive freezing and defrosting without sacrificing performance.
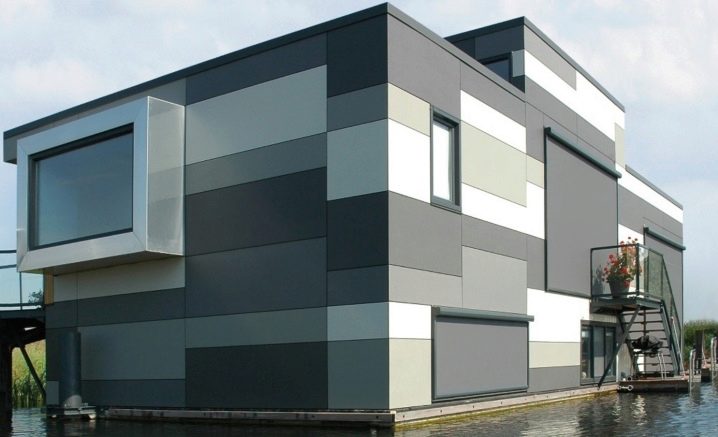
Such a composite is able to withstand even the load arising from the movement of railway transport, during takeoff and landing of aircraft. Glass fiber allows the use of a concrete mixture for covering facades, for finishing industrial buildings, which is unable to absorb dirt and is easily washed off when clogged. Steel filling is used if you need to decorate the floors of indoor and outdoor parking lots, road surface, reinforced foundation. Such fiber-reinforced concrete can also be used to build secondary hydrotechnical complexes and concrete tanks.
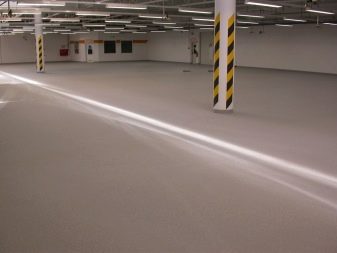
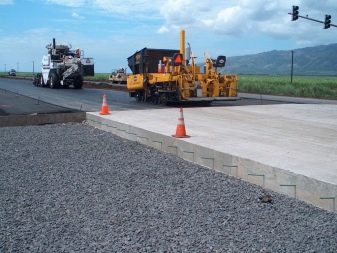
Mixtures based on polypropylene are recommended for use in the production of foam blocks, porous composite and buildings of small area. Due to the varied color spectrum of fiber-reinforced concrete, consumers can choose any appearance they want - even the perfect imitation of natural stone. If you need to make textile concrete, sometimes viscose and cotton are used.
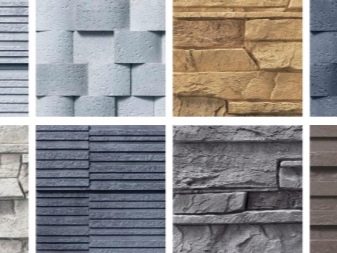
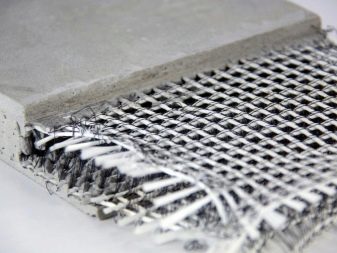
Important: fiber-reinforced concrete is more expensive than a simple mortar, therefore you will have to calculate the need for it as carefully as possible and very accurately choose the appropriate type of mixture. Information about the quality characteristics of raw materials is no less significant: experienced buyers always require the provision of laboratory test documents.
Use cases
The production of fiber-reinforced concrete for hydraulic structures is justified because a higher modulus of elasticity, compressive and tensile strength can reduce stresses in the cladding layer.
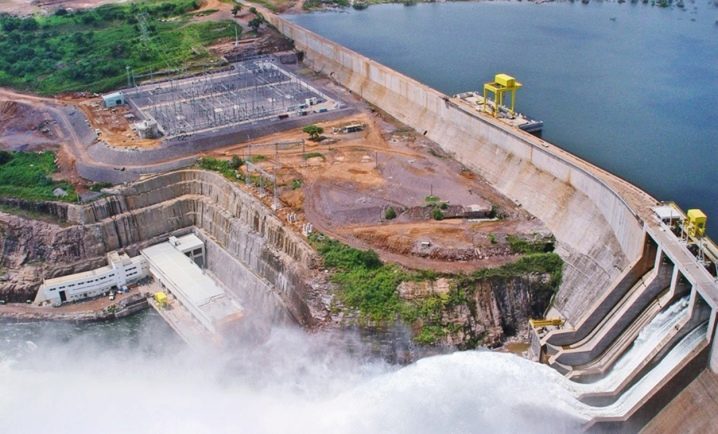
According to laboratory testing, practical properties are influenced not only by the type of fiber used, but also by the length of the fibers and their diameter. Dispersed reinforcement helps to maximize the mechanical properties.
Getting fiber concrete with your own hands requires the use of both a concrete mixer and a crushing device. The addition of sand and cement immediately after grinding (rather than stirring) helps to achieve maximum homogeneity of the mixture.
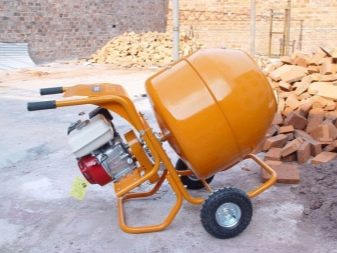
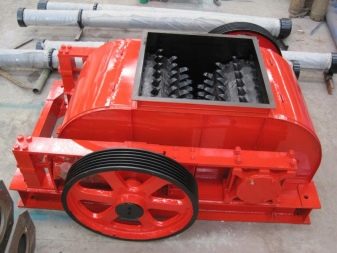
The manual production of fiber-reinforced concrete means that it is necessary to carefully control that there is no excessive concentration of fiber in certain places. This itself delays the process by at least 30% in comparison with the mechanized process. But if you follow all technological standards, you can guarantee compliance with the same characteristics as in serial production. Even furniture is made of fiber-reinforced concrete - stone countertops, sinks and other products. Developers and designers know how to create truly impressive products based on this material.
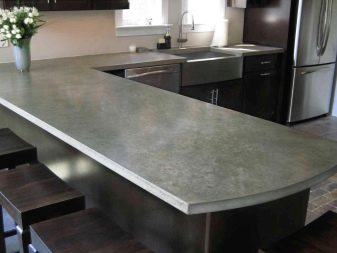
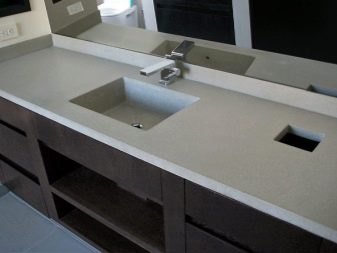
Beautiful examples in interior and exterior
This is how finishing the interior of an apartment with fiber-reinforced concrete might look like. At first it seems gray and inconspicuous, but once you look closely, it becomes clear - this has its own special charm.
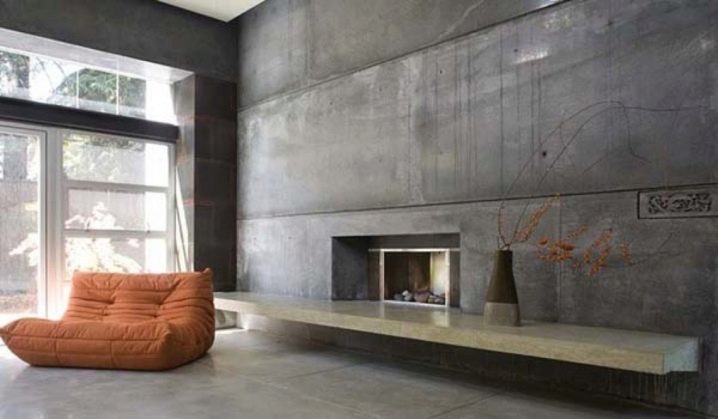
You don't have to choose such a dark plot, textured tiles of light colors with an interesting thoughtful ornament show themselves just as well.
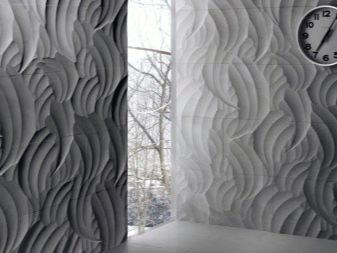
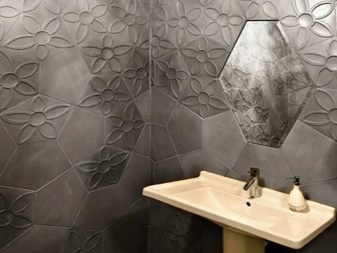
Fiberglass concrete looks great even outside buildings - on this facade it looks exactly like natural stucco molding of the classical model.
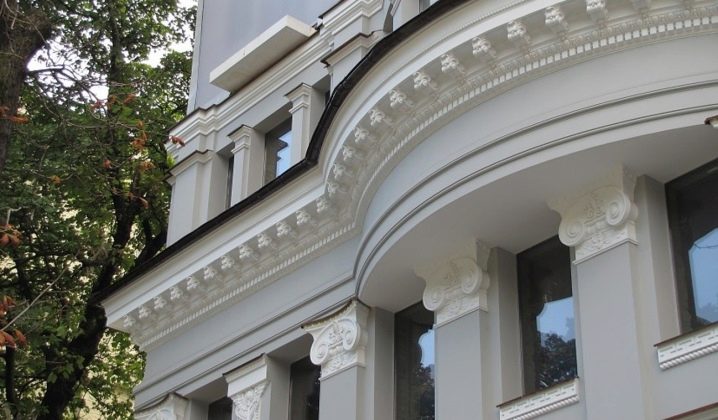
If you wish, you can also order a one-color wall, the decoration of which is provided only due to the surface relief.
Arches and columns found in the design of building facades are the most complex types of decor. But fiber-reinforced concrete not only simplifies their creation, it also guarantees strength and long-term service. By the way, reliable decorative railings are made from the same material. On the basis of fiber-reinforced concrete mixtures, it is possible to create abundant plant decor corresponding to the Rococo style. Resistance to moisture and mechanical destruction will allow you to enjoy design achievements for a long time.
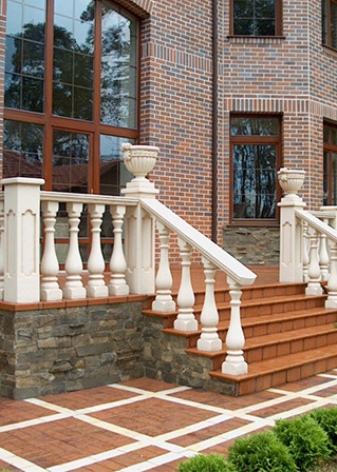
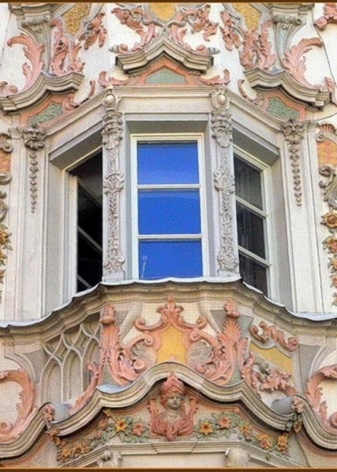
The comment was sent successfully.